So I'm back at it. Since my last post in early Feb, I've essentially been applying urethane to the interior surfaces of the floor, walls and galley components, and waiting for the weather to warm up enough in MI for epoxy to cure outdoors.
FINAL ASSEMBLYThat time finally came on Apr 13th when I bonded the walls and all galley components to the floor sub-assembly for the final time.
In the week since, then, I've also:
1) Fiberglassed the back wall and galley floor exterior joint
2) Attached the interior ceiling skin
3) Bonded the window frame, and ceiling fan frame
4) Cut out the window and ceiling fan holes
5) Added the final three additional roof spars
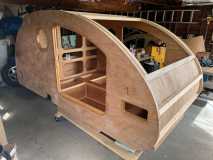
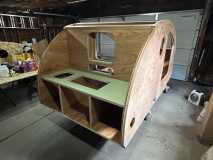
I know people have various treatments for the interior visible seams of all these pieces. I did what I know, and what I thought might add a bit of strength, which was to use thickened epoxy fillets as done in small boat building. I've yet to sand these and touch them up a bit, but am generally pleased with how they turned out. I'll have to take some additional close up photos.
Prior to final assembly, I did a weigh-in of all the components to get a ball-park estimate of where I was at with weight. Here's a tally:
1) Floor subassembly: 116 lbs
2) Driver wall: 59 lbs
3) Passenger wall: 61.6 lbs
4) Driver door: 15.2 lbs
5) Passenger door: 15.2 lbs
6) Cabin back wall: 21 lbs
7) Galley back wall: 14.6 lbs
8 ) Countertop: 24 lbs
9) Galley floor: 22.5 lbs
10) "Cubby" shelf & dividers (5 pcs): 9.8 lbs
11) Galley cabinet dividers and interior wall (4 pcs): 19.6 lbs
This comes to a total of: 378 lbs
This does not include any ceiling items, galley hatch or windows. All in all, I am pretty happy with this progress.
This week I begin the hatch construction.