Even though it's 9' long, 4x8 sheets would be used for the side panels; there's one small joint near the upper corner of the door. The door is a unit I found on eBay. Side panels could be either plywood, plywood skinned with diamondplate fiberglass sheets like I described the other day, actual 0.042" aluminum diamondplate bonded to the plywood underlayment with contact cement, or perhaps a plywood/FRP panel sandwich using FRP panels from the home center. 4 4x8 sheets are all that's needed to do the skin.
The only modification to the HF frame is that I've moved the axle back 2'. On the stock HF frame it's centered, which gets in the way of having a decent-sized door on the side, but also limits the departure angle for trail use; with the axle moved back the departure angle is a respectable 40 degrees. This one's drawn with 32" tires, to match typical tires on an off-road Jeep or similar vehicle.
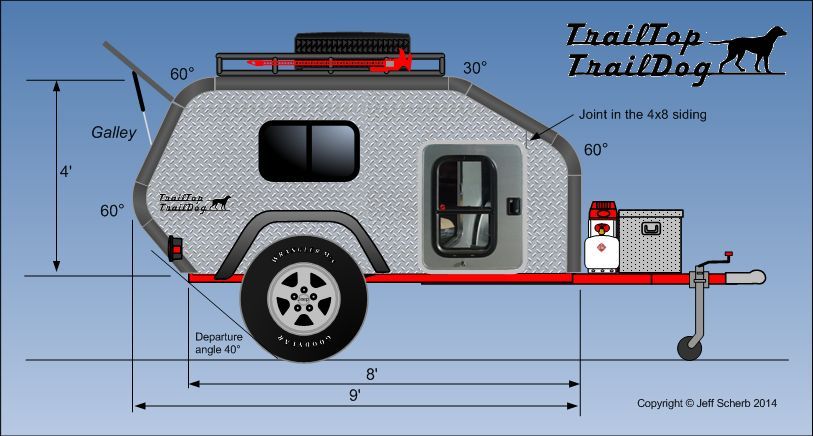
Here's an xray view, it's got space inside typical of a teardrop-style camper. The galley is a teardrop-type, with a hatch in the back. Floor space for the mattress would be about 7 1/2' long x 4' wide, so a little narrower than a standard full sized mattress, but a bit longer.
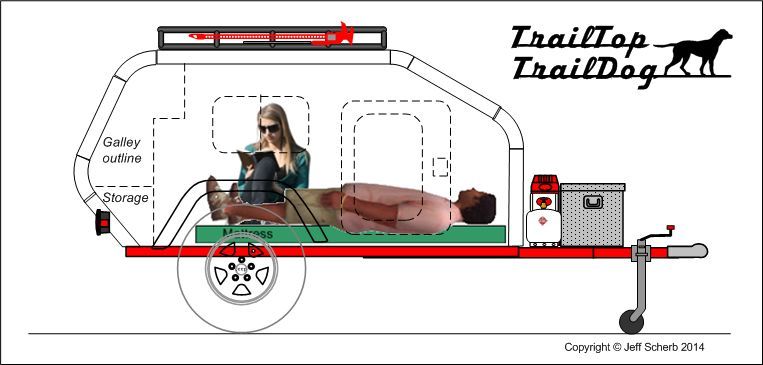