1. I'll start with 5mm underlayment plywood. It's about $15 per 4x8 sheet. I'll attach it to the TrailTop framework with a combination of outdoor-use construction adhesive and flathead machine screws. Once the plywood is in place, I'll seal the joint between the plywood and the TrailTop framework with a marine-grade caulk.
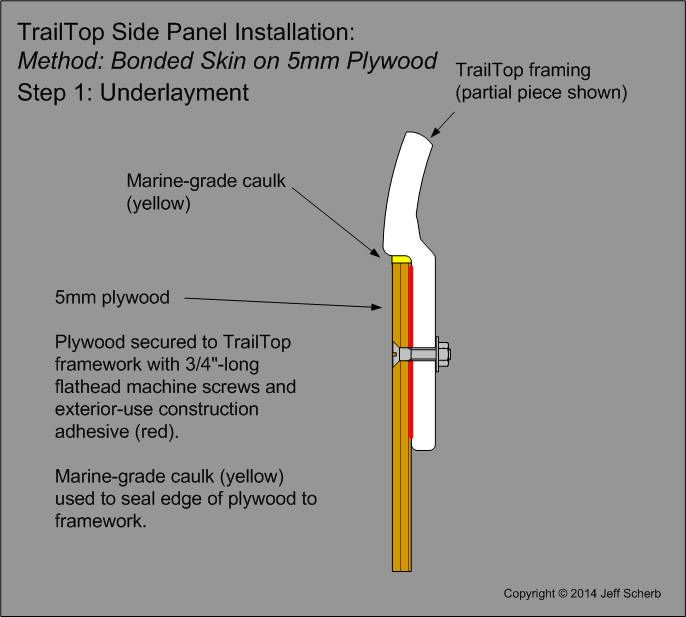
2. I'll probably reinforce the side panels with 1x2 poplar stringers, glued to the back of the plywood and bolted through the framework. The drawing shows the bolt protruding through the stringer on the back side, but I'll probably use shorter bolts that don't come through and drill a hole into which the nut will go, which keeps the bolt/nut below flush on the inside of the stringer. The stringers will be notched at the end near the TrailTop framing so they fit nicely against both the plywood and the framing.
I'll probably set the 1x2 stringers wide-side facing the plywood, which means they'll stick out 3/4" on the inside, which is perfect for insetting 3/4" foam insulation available at a home center.

3. I'll laminate 0.090" FRP sheet to the outside of the plywood using contact cement. FRP is also available at most home centers. Once that's in place, I'll caulk the joint between that and the TrailTop framework as well. The double calking will make a more weathertight joint than if a single application had been done.
Laminating the FRP to the plywood after the plywood has been glued/bolted to the TrailTop framework means that the bolt heads in the plywood will be covered by the FRP - there will be no bolts visible on the outside of the finished camper shell.
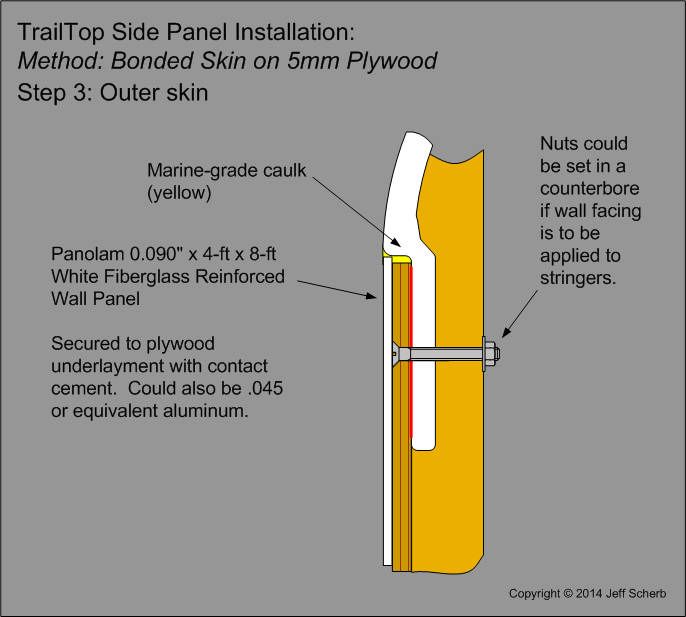
4. I'll inset 3/4" foam insulation between the stringers, and glue it to the plywood. Once that's in place, a 1/8" plywood skin can be added to the interior to finish it off with a nice appearance.
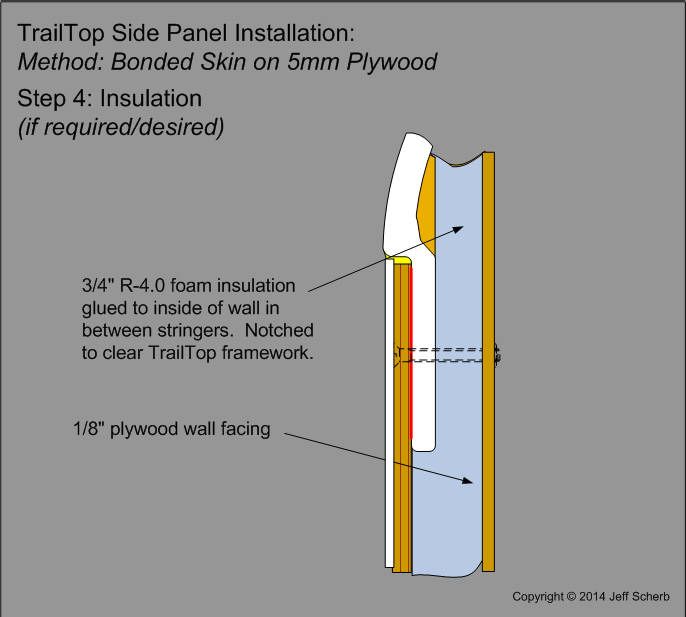
I plan to build the roof so that it will support loads like a cargo basket or a roof-top tent. I'll likely set the 1x2 framing narrow-side towards the plywood, so they provide more strength for loads on the roof. I'll double up two stringers (resulting in 2x2) in two places to support the mounting hole pattern for roof-top tents.
This side panel/roof method will be plenty strong enough for the camper shell to endure off-road abuse, and it will provide a full fiberglass exterior with no visible fasteners.
Photos and more details to come when I get to this stage of the construction.