Hardryder56 wrote:Jeff,
What was towing the T&DA trailer? Looks like an old bus or motorhome. How hard would it be to mold the color into the parts from the get go?
Tom
Tom,
I should have gotten pictures of the bus too, I'm guessing it was a late 50's/early 60's bus converted to a motorhome. It was pretty cool looking.
Grant answered the color question, but I'll add a little more "color commentary"...
The outer color of a fiberglass part is the gel coat, and as Grant says, it comes in many colors and can be custom-mixed. Doing parts in a different color involves nothing more than using a different color gel coat as the first step. Sometimes the tint is also mixed in the resin which makes the part the same color all the way through. Tinting the resin would be a good idea for TrailTop parts because you do need to cut some of them to length - if only the gel coat has color then the cut edge won't have the color.
About molding the TrailTop parts commercially in different colors - a lot will depend on the demand for the different colors and the shop that does the molding. All shops have white gel coat on hand, and many have black; they buy that in quantity (55 gallon drums or even larger) because that's what they get the most call for. The typical minimum quantity of a special color gel coat that a shop buys is a 5-gallon drum, which would make a LOT of TrailTop parts, so there would have to be decent demand for that color to make doing the color worthwhile - a shop wouldn't want to buy a 5-gallon drum for one order.
The pricing for TrailTop parts would probably go something like this:
- White or Black non-UV gel coat: cheapest (great choice if they're going to be painted)
- White UV protected gel coat: maybe 10% more expensive due to the price of the gel coat
- Common colors UV protected: could be 15-20% more than the cheapest parts?
- Custom colors UV protected: ? (gel coat by the quart is most expensive, so doing a small quantity in a custom color would cost the most)
Tinting the resin as well as the gel coat would add a little bit more to the cost.
If the fiberglass shop has custom color mixing capabilities in house that should reduce the cost premium somewhat.
If these get to production, the variety of colors will be a business decision that the company can make. Pretty much anything is technically possible, but some options might not make good business sense depending on ow much demand there would be for a particular color and what people are willing to pay for the parts.
BTW fiberglass takes paint very well, so doing colors like the T@B and T@da photos posted earlier is very easy to achieve with paint.
Side story about molding in different colors:
I almost always mold parts in white, because I usually I plan to paint the parts I make. When I started the TrailTop project, I wanted to work in my nice warm workshop over the winter instead of the cold garage, but I can't get a real trailer down into my workshop. I did have an unassembled Dinoot Extended kit here though - the only problem was that my yellow trailer is 11" longer than a Dinoot Extended. So I molded two 11"-long side extension side panels for the Dinoot, and I molded them using black gel coat to match the Dinoot parts. Here they are right after coming out of the mold, before I cleaned them up a bit:
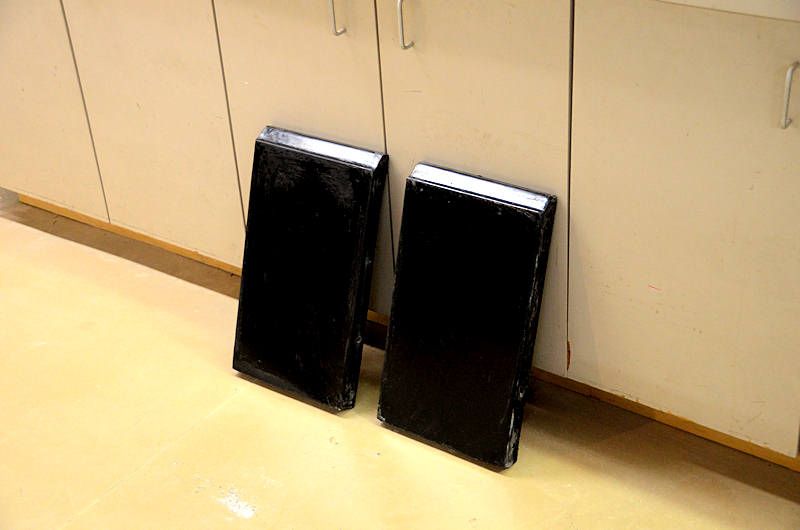
When bolted in place, they made the Dinoot Extended exactly the same length as my yellow trailer, so whatever I build in the workshop on the Dinoot will exactly fit the yellow trailer up in the garage. You can see the panels bolted in at the back of the tub:
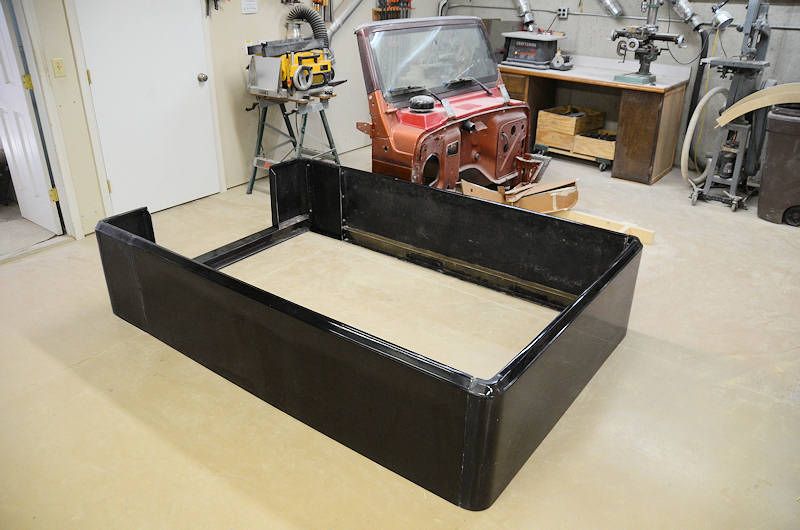