mallymal wrote:This just gets better and better....
Thank you very much
mallymal wrote:It's probably a trade secret you aren't prepared to reveal, but I can't imagine how as a "hobbyist" fibreglasser (as you call yourself) you have managed to make such perfect moulds..... The straight sections look tricky enough, but the curves... Wow

I have no "trade secrets", after all I'm not in a trade - this is a hobby for me

.
I'm not sure if I've posted these photos here before, but they show the basic steps involved in making a mold. The quick answer would be "careful woodworking", but here's the long answer...
The first thing is to make "mold masters" - other fiberglass people may call them "plugs" or "models", but basically a master is a perfect original of the part you want to mold. There are many ways to make masters, but in the case of the TrailTop parts, the most effective way for me to do it was by making them out of wood. Depending on the part I'm trying to make, wood may or may not be the right material to make the masters. In the case of the TrailTop parts it was, but I've made masters out of metal and out of fiberglass for other projects. You can use pretty much anything that you can make the required shape out of.
For the curved parts, I used what I guess could be called the "stripwood canoe" method - narrow strips of wood bent over forms to make the basic shape. The photo below shows the master for the 36" radius curve under construction - the strips have been applied over the forms, but not sanded yet:
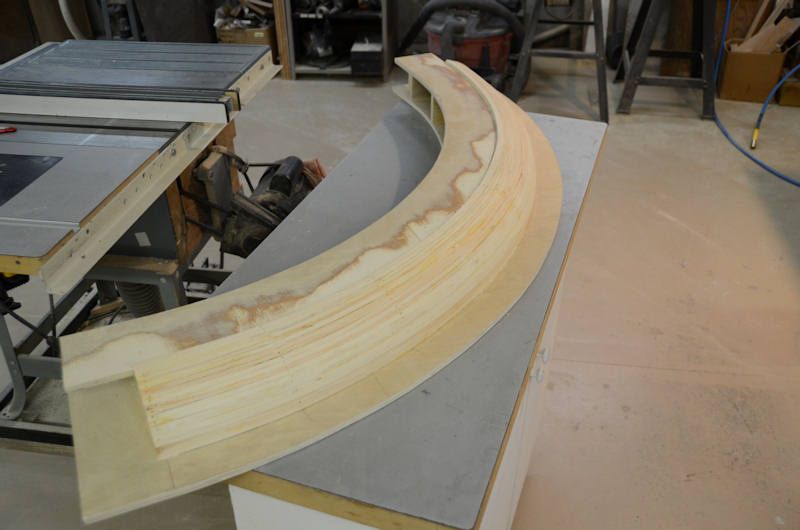
Once that's done, the strips are sanded and filled as necessary with automotive body filler until the surface is smooth, then coats of sanding sealer are applied. This next photo shows all three of the TrailTop framework masters with the sealer applied:
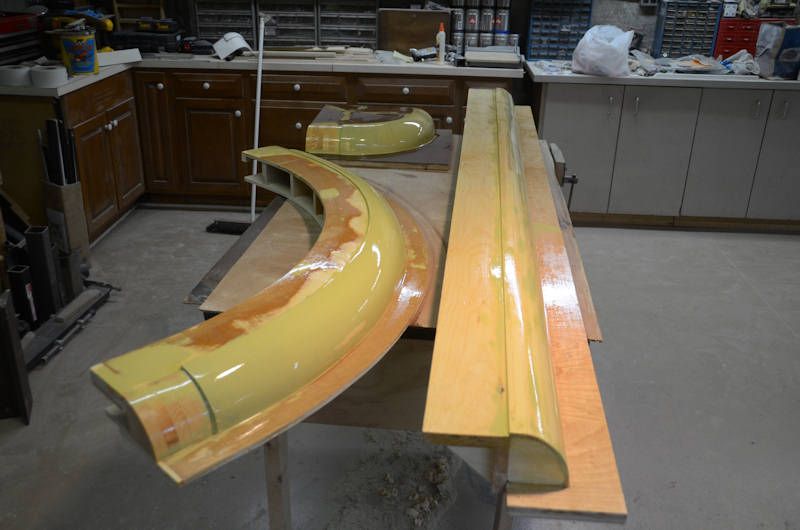
The sanding sealer is then smoothed by more sanding with finer sandpaper, and when they're smooth enough, several coats of epoxy are sprayed on:
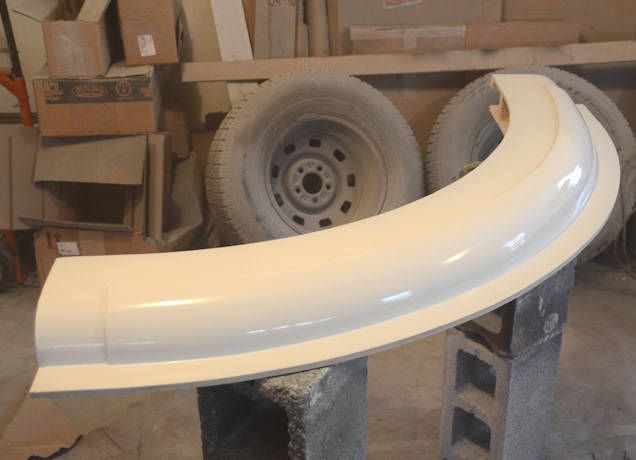
If I were making production molds, there would be more finishing steps to result in a mirror-smooth finish, but since I'm making molds for prototype parts, the epoxy finish is adequate.
After the epoxy has cured a few days, the masters are prepped with mold release wax, followed by a few coats of PVA mold release applied via spray gun. When the PVA has dried (about an hour), polyester gel coat is sprayed on the masters with a gel coat gun. The gel coat is orange, and it's called "tooling gel coat", which is tougher than the ordinary white gel coat that's used to make the actual parts. The gel coat cures for about 2 hours, and then layers of fiberglass mat soaked with polyester resin are built up on top of the gel coat:
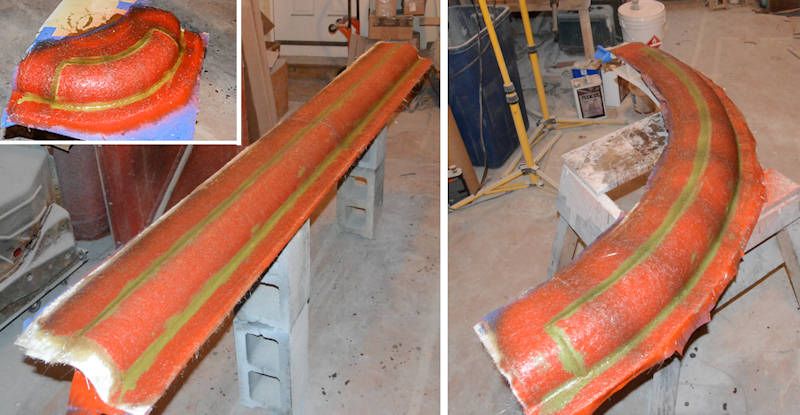
That whole mess cures overnight and then the molds are popped off the masters, they're shown in this next photo immediately off the masters, before the rough edges have been trimmed or the mold release washed off:
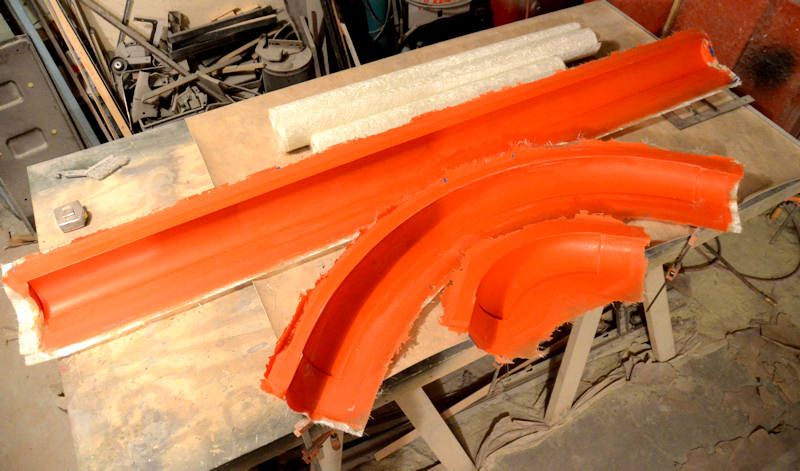
In many cases the molds would then be ready to make final parts, but these molds are two-part molds because of the undercuts in the profile of the parts that would lock them into a single part mold. So these molds have bolt-on forms for the recessed flanges. I made the flange forms out of wood because these aren't production molds and wood will suffice for several dozens of parts, but for production these forms would also be made of fiberglass.
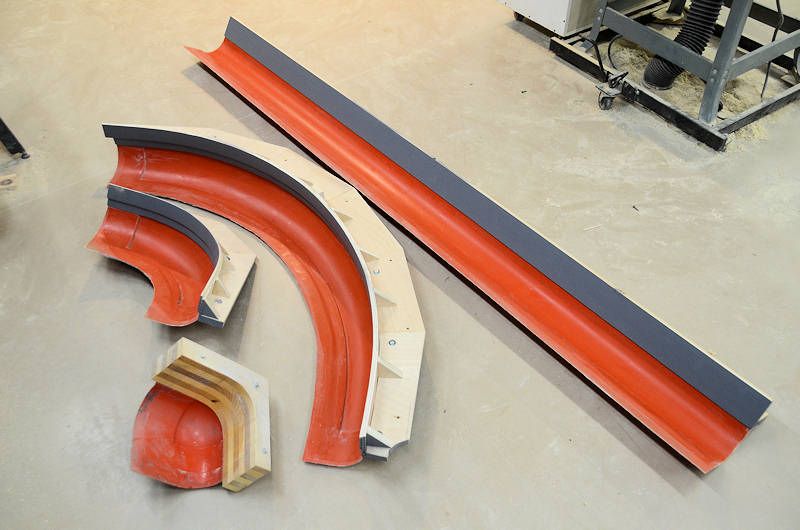
Once the molds get to this stage, they're ready to polish at bit and make as many parts as I need.
There's nothing about it that can't be done in a modest home workshop, and the only special tool that's a good idea to have is the gel coat "dump gun", they're only about $120 and require an air source such as a compressor.
Making parts in the mold is basically the same process as making the molds - prep the molds with wax/mold release, shoot the gel coat (white this time), build up layers of fiberglass soaked in resin, cure overnight, pop the parts out of the molds. This last photo shows the first parts out of the molds, again the photo was taken immediately after the parts were de-molded, before trimming and washing off the mold release:
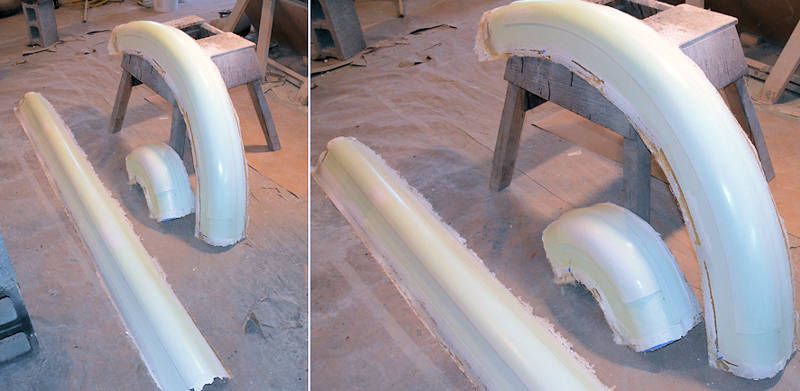
There's a lot of little details I've left out in this summary description, but those are the highlights of getting from a design to a mold and then to a final part. I'm happy to answer an questions anyone has about the process if anyone wants to know more.