My results could hardly be called scientific. But they're results. And some of them surprised me.
I made some little 4"x4" 'sample walls' so I could get a gut feel for strength and weight. Of course I can calculate the weights based on the material specs, but there's no substitute for holding something in your hand.
The 1" XPS (pink, Foamular) foam I got was denser than the thinner EPS (beer cooler) foam. There are denser and less-dense versions of both. But the XPS stuff can be cut with tools (whereas the EPS needs a hot knife or wire), and the XPS is nice and rigid. So I think that part of the decision is pretty easy, even if I went with thinner XPS.
The Aluminum Composite Panel I got has a white paint finish on it, to prep it for printing. I like this stuff. But if I can only get it with the white finish on it, I will have to cover it with a vinyl car wrap material that looks like brushed aluminum. On the one hand, this means I can repair scratches by replacing the vinyl. On the other hand, it adds more expense and might mean an additional prep step in adhering the stuff.
I got some beautiful FRP panel samples from Crane Composites, each with a woven wall pattern. They'd be nice for an interior, but I'll have to look at cost and weight as issues. Here you can see the interior finish, the white ACP finish, and the white ACP finish covered with the vinyl wrap that looks like aluminum.
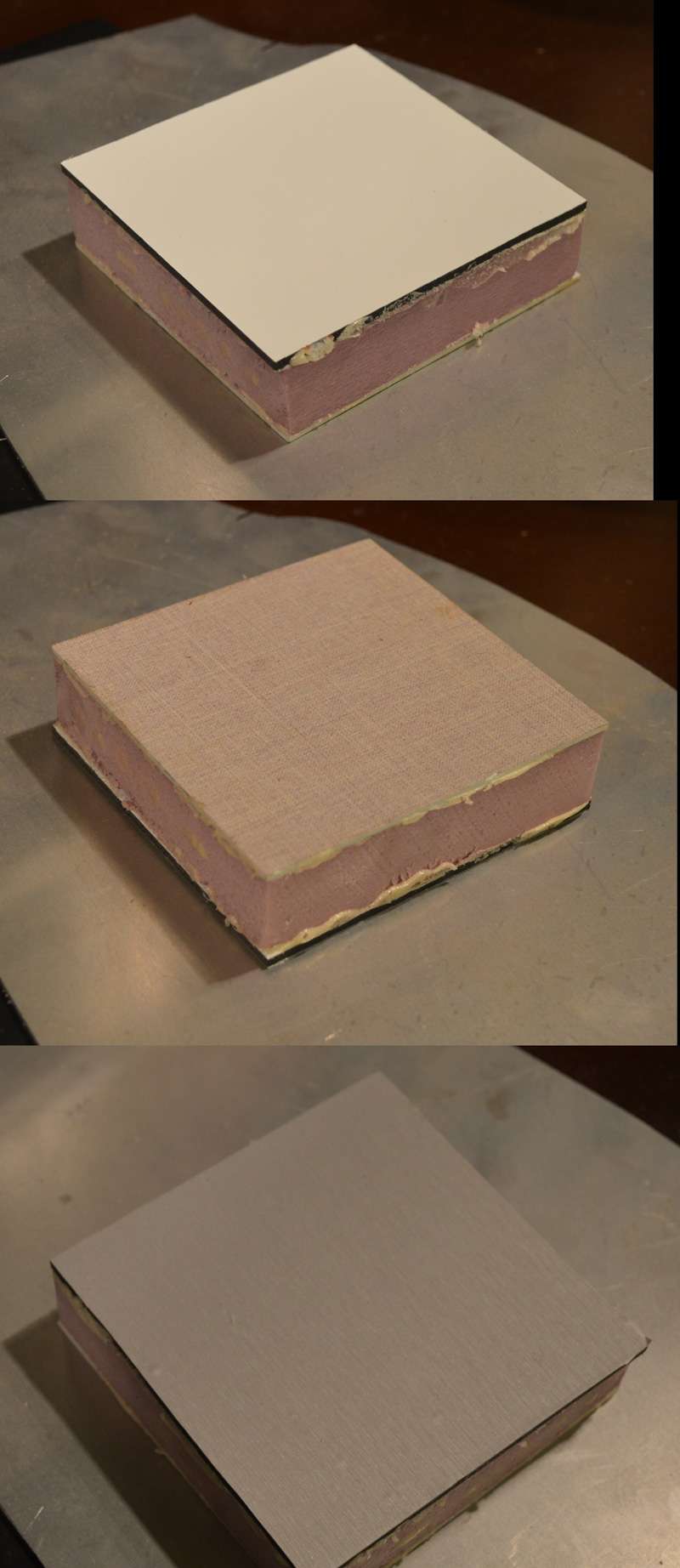
And while you can see how I misaligned one little panel, this picture maybe shows the brushed aluminum pattern better:
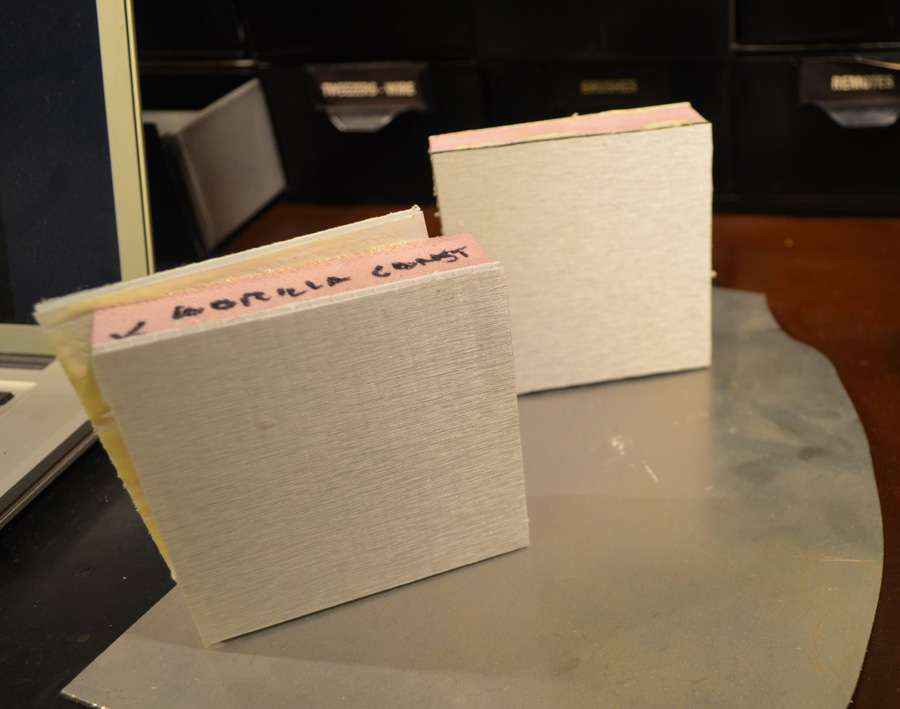
An alternative for the inside is 4mm corrugated plastic. It's light and strong, but the corrugated pattern does show through, even if you cover it with a decorative vinyl. I might try to think of the pattern as a bonus, since it's significantly lighter than the FRP panel, and probably maybe better in terms of rigidity and strength.
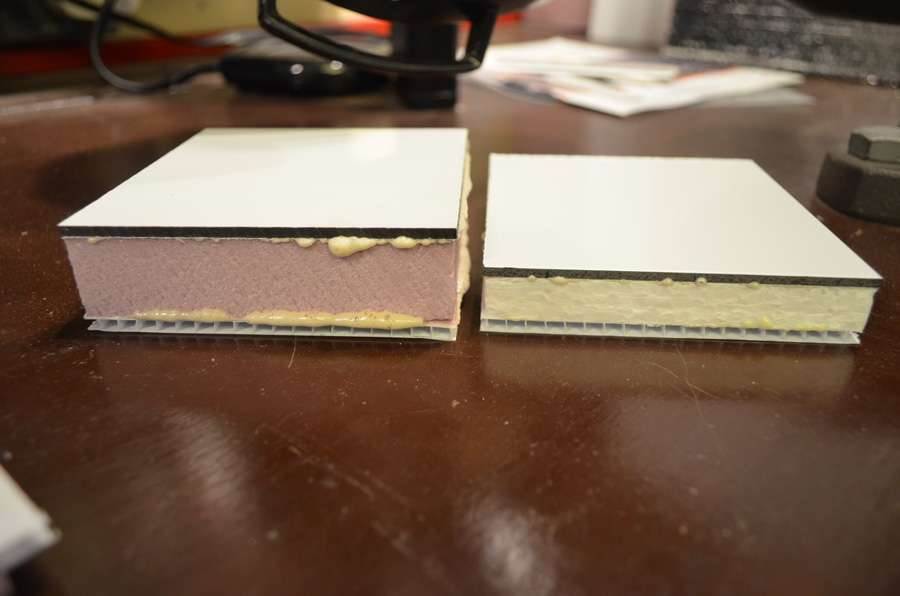
Gorilla Glue (polyurethane based) was the surprise winner for adhering ACP (aluminum composite panels) to foam. It also did surprisingly well adhering ACP to itself. The Gorilla Glue Construction Adhesive (which doesn't foam/swell in the same way as the original glue) also surprised me, although it is not quite as good as the original stuff.
For adhering EPS foam and XPS foams to themselves, the unsurprising failure was Marine Goop, which dissolved the foams. Also surprising was the (relative) weakness of Shelby 277, which is a foam-specific adhesive. It worked, but not as well as either Gorilla original or Gorilla Construction. These are the samples after I did my best to tear them apart.
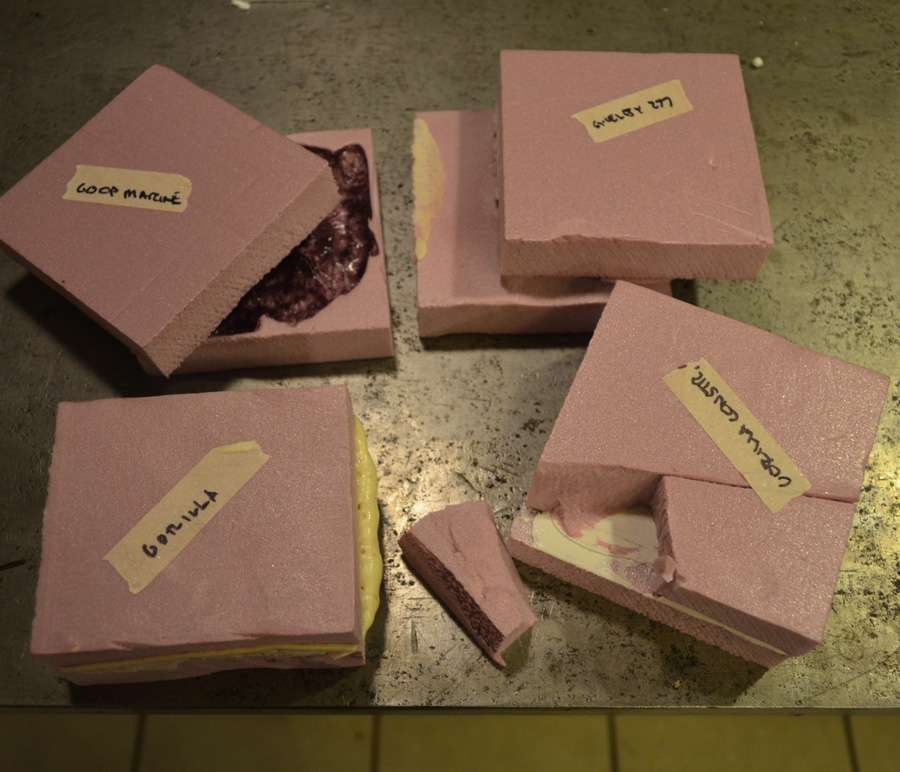
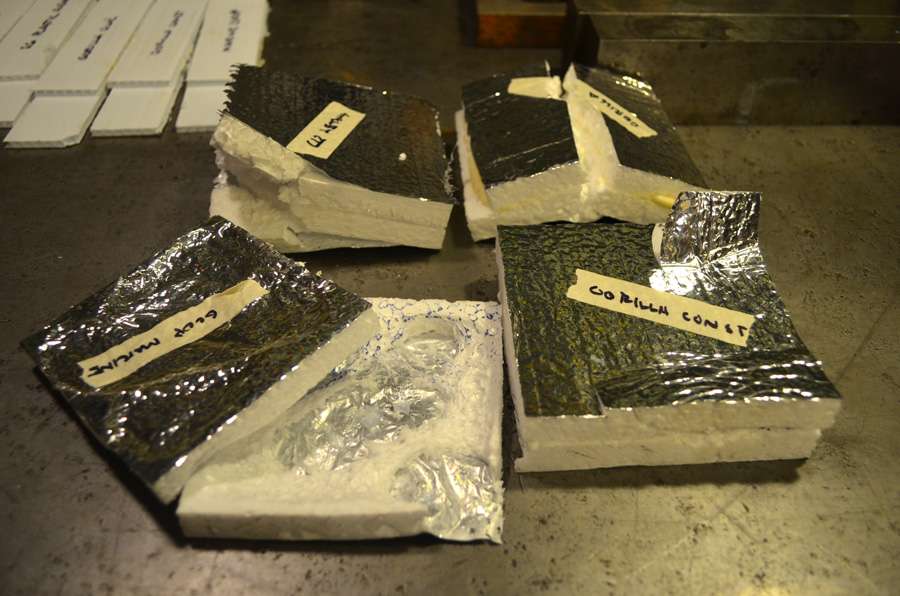
For the strip tests of corrugated plastic (to itself) and aluminum composite panel (to itself), my first thought was to see if each strip could hold a 110# anvil. As it happened, not even an unglued strip of corrugated plastic could support that weight, and I'm lucky I didn't crack a tile. This thing came down pretty hard.
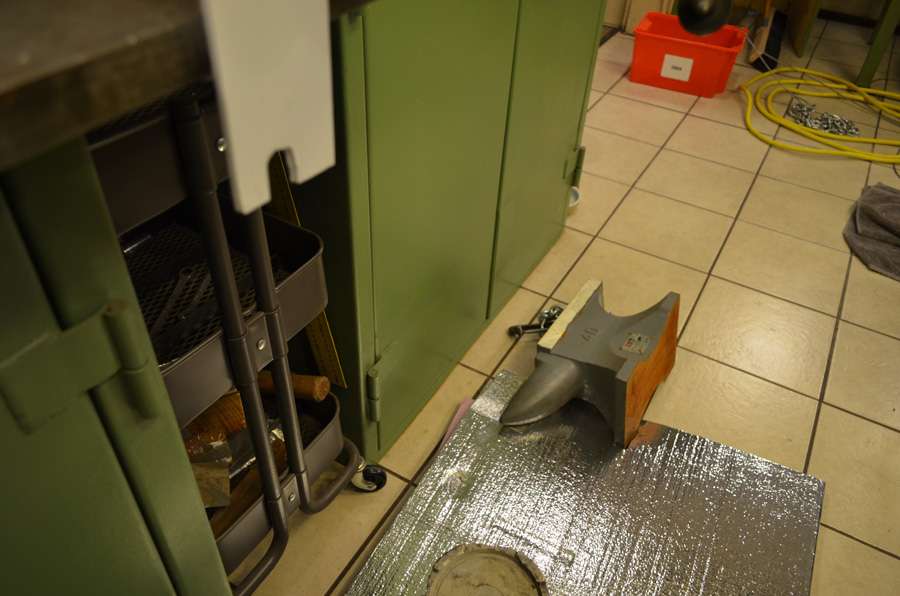
But for the rest, I used a method of adding weight (from 26# to 36# to 46#) to try and get a failure. I took the ones that succeeded and rated them on how easily they peeled apart. For the corrugated plastic, the winner was (again) Gorilla Glue. Marine Goop worked, but revealed some damage to the plastic (and worries me about outgassing). Loctite Pro for Plastics was pretty good, but SuperGlue Plastic Fusion and JB Weld for Plastic both did worse than I expected. Both of them might benefit from woodpeckering holes into the surface, but that is extra work.
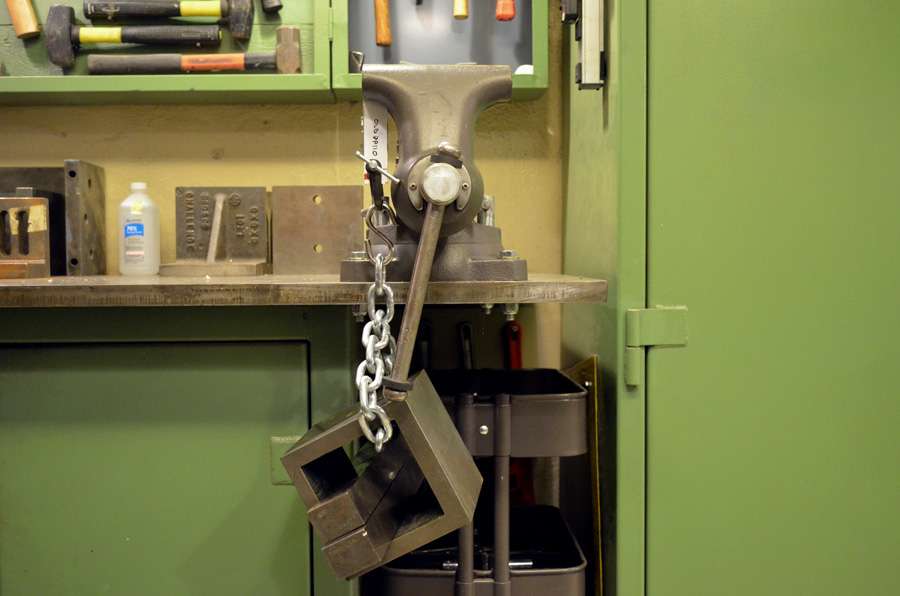
For the Aluminum Composite Panels, I think there might be a strong argument for abrading the surface if I can't get mill-finish sheets. The 3M VHB tape was less successful than I expected, although switching to a thinner (and less elastic) version of the tape will probably help. I also couldn't test my preferred method yet, since the Dow 995 adhesive needs a week to cure. I believe that a combination of (thinner) VHB tape and Dow 995 -- with better surface prep and the same cleaning -- will work for the structural bonds for this thing. But I'll know more in a week.
Gorilla Glue (again) surprised me with its ability to bond the ACP to itself. 3M ScotchWeld DP110 also passed with flying colors, although the peel results also pointed to the benefits of some ScotchBrite or fine sandpaper if I have to stay with the painted ACP.
All of this leads me to wonder a few things about Gorilla Glue. Its expanding properties seem manageable if I hang out and wipe the stuff as it emerges -- and maybe get more skilled at applying the right amount. But does anyone know if the expansion would cause problems over a whole 5x10 sheet? I'm wondering if it will push the panel out so that there is any bowing in the middle and general thickening if the expansion force doesn't have an easy escape route.
And does anyone know about potential health hazards from Gorilla Glue? I'd hate to subject my family to any outgassing hazards if I can avoid it.