Ya can't build a stripper without sealing it up with a health dose of epoxy...and that is what this final post on this thread is about.
Long before I started construction on the SlumberMAX, I began to look around and try to figure out how I might fiberglass whatever I ended up building. Looking long and hard, there seemed to be two camps...use a lightweight glass under epoxy, or forego the glass and simply give the Tear multiple coats of epoxy under a varnish or auto clear coat for UV protection. I decided for my purposes that I would just give the sides epoxy only, and use a 3.8 oz cloth on the top and bottom for strength and abrasion resistance.
To start your epoxy job, you have to first have some basic tools that include: gloves, mixing pots, small rollers, disposable rolling pan liners, mixing sticks and brushes to tip off the brush marks. In the pic below, you will also see that I have a small can of acetone. On side one of the SlumberMAX, when I hit the purple heart with epoxy, it simply balled up like oil on water...I found that by wiping down the surface of the oily woods like purple heart or teak with acetone about 15 minutes ahead of epoxy time, you draw out those surface oils and the epoxy will lay down fine.
Rollers are pretty important part of getting a good job. I like those West System rollers, cut in half, on a smaller roller. I've found that some of the rollers sold as epoxy rollers, leave bits of lint, others don't carry the proper load of epoxy. You canalso see in this post the sanded, bare cedar. I took it down to 120 grit with a random orbital sander. You don not need to go finer.
Epoxy is the final part of the equation...and I have had good results with West, Raka, and MAS. Other brands like System Three such as US Composites are reported to work well but I haven't tried them. Some thoughts on epoxy:
Epoxy doesn't smell strong (unlike CPES), but you can get sensitive to it over time and that is problematic. Do read the safety lables, minimize your exposure. wear disposable gloves and avoid skin contact.
Hardeners come in variuos speeds, I like the MAS Slow. Reason is, your second and third coats must be applied prior to the previous coat curing. That gives a chemical bond. If you wait too long, you have to sand to re-establish a physical bond. With the MAS slow, I can put on a coat at night, wake up in the morning for coat two, and put the third on that evening...and that just convenient to me.
Always start epoxying with the temps of your wood and workspace warm, and let those temps drop as you start working. That prevents outgassing, and the epoxy is drawn into the wood better.
Finally...I rely on the epoxy pumps to do my measuring....but that may not be your best choice. John Michne in his web article entitled Fiberglassing 101 has some really good information.
Fiberglassing 101
Going without cloth simplifies matters. As you work, apply epoxy to about a two by two foot area with the roller, then lightly drag the brush over the wet epoxy to smoothe it out. Try not to overwork the area to induce excessive bubbles, but...those fine bubbles you do get will dissipate. I try to keep a wet edges as I work.
Finished....now I'll just let this sit overnight with the slow hardener and in the morning it will be hard so as to not be tacky...but soft enough that I can dent it with a fingernail. That's a good time to apply coat two and get that important chemical bond.
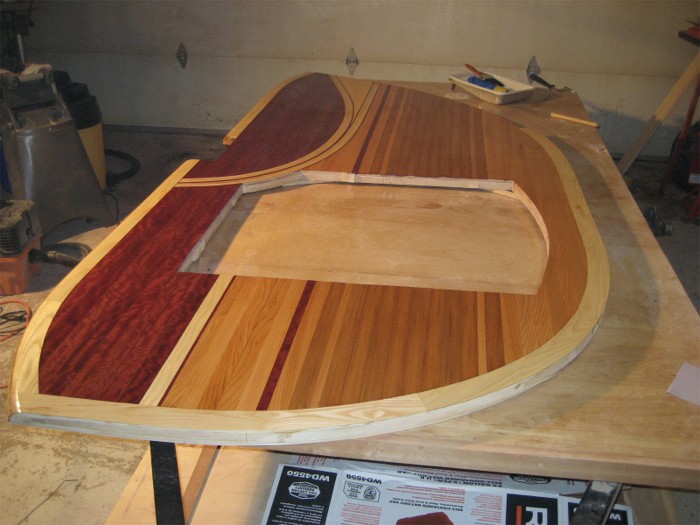