Thanks for all the tips, questions, and suggestions.
I'm not skinning the bottom as I want it to be able to dry out if it get's wet. With an offroad trailer, crossing a creek is not out of the question. The plan is to seal the bottom with several layers of undercoating before installing the insulation.
I too do not want holes in my 2x2 steel frame thus the option of the tabs. I may actually bolt through the corner braces. I'm planning on 2x2 for the outside from and tongue with c-channel cross members every 2 feet. I'm also planning on a 2x2 receiver at the back for a bicycle rack. I may put some 1 1/4 receiver at the side by the galley for optional extensions such as tables, etc.
I'm planning on sealing the joint surfaces with epoxy. I may bring them in as well. Still thinking on that one. Thanks for pointing it out.
I've heard of problems with screws working their way out and damaging the skin - thus the idea of screwing from the inside.
Here's a rough sketch of my trailer plans. I just dropped an axle in "about there". I'll get that more accurate later.
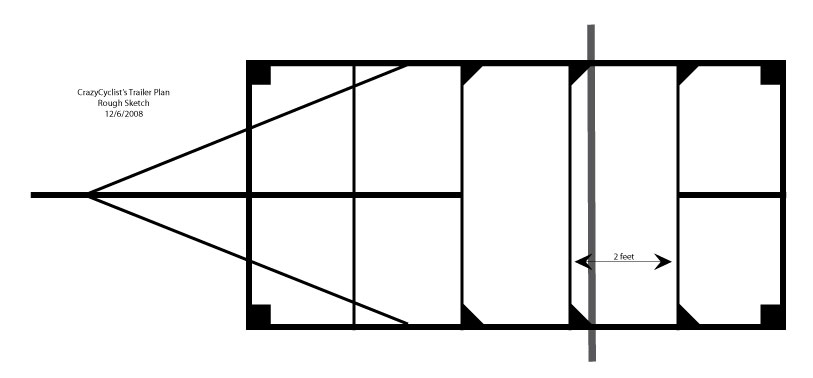