I used flashing on the sides of my tear. It works in keeping the tear dry. I lapped it horizontally two times on each side. Two 2" laps.
Flashing is very thin so a backer is needed for support. I glued the flashing on using Henrys outdoor carpet glue. I had mixed results with this. One side remains attached to the backer while on the other side one run of flashing has come loose. The areas that have come loose are places where I had to pull the aluminum off and then press back on to get pieces of trash out from under the skin. (i was working under a tree). So what little failure there has been has been a result of my working conditions. Th method seems solid.
Total cost was around $50 for the sides. The roof was done with some thicker flashing that I stumbled onto in a hardware store for $8.
End result: It was cheap, light, keeps me dry, looks OK and will last a very long time with very little maintenance. I would not use it again, though. Dings too easy and the end look "hammered glass appearance" was not quite what I was after.
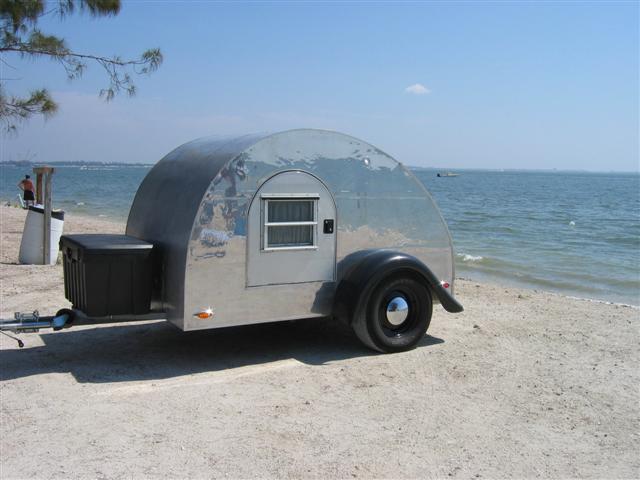