Page 1 of 4
Making a good joint

Posted:
Tue Jun 23, 2009 6:44 pm
by Forrest747
Today I purchased my baltic birch 11 ply 18 mm thick (3/4) in 4X8 sheets. I need 10 foot lengths so how do i make a good joint is the question.
The plan in my head is getting some pole clamps, glue on the ends of teh joint. then attach the 3/4 inch backing plywood 6 inches wide and screw together and let set for a day.
I will not be able to do a biscuit.

Posted:
Tue Jun 23, 2009 7:46 pm
by WarPony
Forrest, I would NOT use the pole, or bar clamps. I found out that using those will tend to make the piece bow out or in, depending on which side the clamps are placed.
The lap joint (I think that's what it's called), should be plenty strong. Butt the two pieces together and weight/clamp/screw the 1X6, or whatever you will use and let 'er dry.
Jeff

Posted:
Tue Jun 23, 2009 8:26 pm
by tinksdad
The trick with bar clamps is an equal number alternating above and below to keep the pressure equal in both directions. Also the more the better.
A lap joint with weights will work just as well. Just keep everything supported on a straight plane.
Or as madjack does, a 1/4" hardwood spline adequately glued.

Posted:
Tue Jun 23, 2009 9:48 pm
by Miriam C.
I did a butt joint and lapped it on both sides by 6" and put the lap board on the inside. Now I was using 3/8" siding. Use a glue that won't swell too.

Tight bond lll works great.
A rabbet joint will work well too.
http://www.raygirling.com/wwjoints.htm
http://www.youtube.com/watch?v=DhLfb7m9Fug

Posted:
Tue Jun 23, 2009 11:09 pm
by doug hodder
Do you have a router? If so, pick up a 3 wing cutter bit and cut your own slots in both sides of the joint. Stick in a piece of 1/8" ply for a spline. I've done this on 4 tears so far, works great for me. Doug

Posted:
Tue Jun 23, 2009 11:39 pm
by teardrop_focus
All That Is Man
I've done this on 4 tears...
Pics or it didn't happen.


Posted:
Wed Jun 24, 2009 4:01 am
by kennyrayandersen
A 6 inch lap splice is overkill for sure. Scarf joints are really strong, but hard to do cleanly for the novice. The wall isn’t loaded out-of-plane, or in bending, so the joint just has to react shear. If you use either a 1/8 or a ¼ spline as suggested, it will be easy to make a very smooth-looking joint. Just run the router from the same side of both parts being joints and it will even line up exactly without having to worry whether the joint is exactly in the middle or not. Make the slot ¾ inch or so on both sides and make the spline width undersized by a good 1/8 inch. It can’t get much simpler that this kind of joint.

Posted:
Wed Jun 24, 2009 8:16 am
by aggie79
You certainly don't want to do a butt joint (edge of ply to edge of ply.) As others have said, use a lap or spline joint to join the panels. If you have a wood assembly table/work bench and you are not doing a woody, then you can use use drywall screws as clamps. Screw throught the panel down into the assemble table. From experience learned the hard way, use butcher paper or poly under the joint to keep from bonding your panels to the work bench.

Posted:
Wed Jun 24, 2009 9:36 am
by len19070
doug hodder wrote:Do you have a router? If so, pick up a 3 wing cutter bit and cut your own slots in both sides of the joint. Stick in a piece of 1/8" ply for a spline. I've done this on 4 tears so far, works great for me. Doug
I've done it this way several times as well, .
I have made up to 8'X16' pieces of plywood. Staggering all joints.
Happy Trails
Len

Posted:
Wed Jun 24, 2009 10:12 am
by green_eyed_diablito
i recently used a lap joint to get the extra 18" of ply that i needed for my build. it took about three tries on a piece of scrap ply to get the cut perfect...always test cut on scrap lumber.
after gluing, i used brads to to clamp the two pieces together until the glue dried.
the seam will be covered by a trip piece.
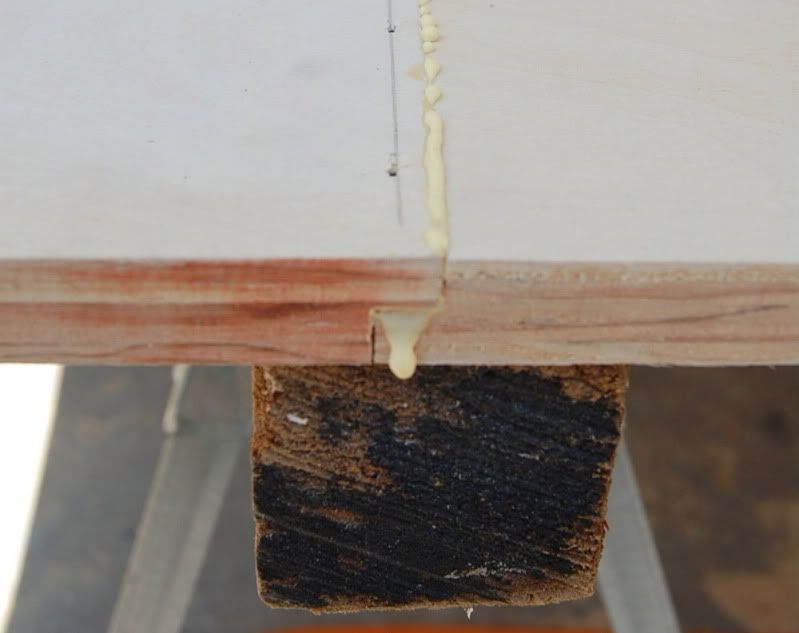
Re: Making a good joint

Posted:
Wed Jun 24, 2009 10:18 am
by planovet
Forrest747 wrote:I will not be able to do a biscuit.
Dang, that's how I did mine and it worked great...
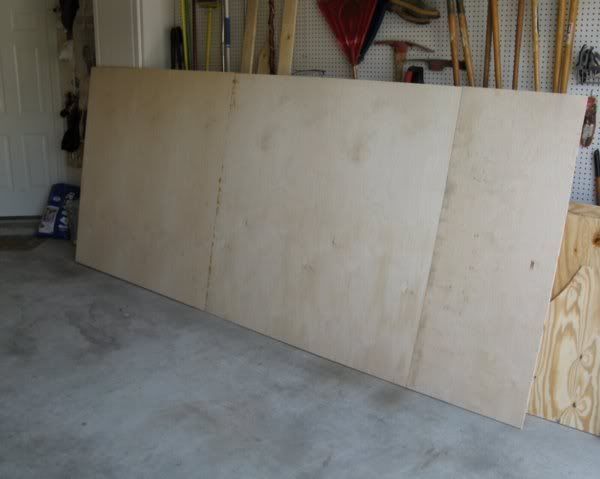

Posted:
Wed Jun 24, 2009 10:28 am
by madjack
nicely done Mark...I use the slot/spline method...works well for me...both of these ways of joining require specific tools...either a bisquit joiner or a router w/slot cutter...a butt joint with backing plate or a half lap joint can work as well but as with ANY of them, attention to proper use of said items will make or break your attempts at making larger ply...unless you are particularly skilled, I would not attempt a true scarf joint as they are greater than 45*s and can be tricky to get shaped properly......
madjack


Posted:
Wed Jun 24, 2009 11:45 am
by chorizon
I used a scarf joint on mine:
Since I'm limited on tools, I used my trusty Ryobi cordless skilsaw to do it and it came out great. I made a temporary fence on the wall pieces, then cut at a 45 degree angle. I glued it with gorilla glue, and made some plates to hold everything flush while it dried. The pic isn't all that great, I wish I would've taken a closer pic of this. Oh yeah, I used wax paper under the parts to keep them from sticking to my floor while drying.

Posted:
Wed Jun 24, 2009 12:10 pm
by ZendoDeb
Hard to beat a good scarf joint, but 45 degs seems a little steep. I might go more 6-to-1 or 8-to-one.
You can do a nice job with a hand plane and some sanding.
here is some info on scarfing and also spline joints
But you don't have to go to all the fuss, especially if the panel will not need to carry a curve - sidewalls are straight on most tears.
You can create an adequate joint with a butt block or even a fiberglass splice.
And I would use a strong laminating epoxy. Mostly because I like epoxy, for a small surface area it creates the most adhesion - especially in wood. (put some waxpaper under the joint, so you don't glue the panels down to your work surface.