Page 1 of 2
floor framing for 6ft wide campers on 4 ft wide trailers

Posted:
Sun Mar 07, 2010 8:35 pm
by Grid Runner Adventures
is 2x2 what is generally used for framing the floor in 6ft wide teardrops when the trailer is 4ft wide. what do you guys use?

Posted:
Tue Mar 16, 2010 7:56 pm
by brewwagon
Please let me preface this post by saying I havent built a tear yet, but I've worked with wood most of my life.
I think for going 1' over on each side that that would work. But it also depends on what your deck thickness would be and how far apart your spacing your framing.
How long are you making it. Will you be hanging the front and rear off the trailer/frame as well?

Posted:
Tue Mar 16, 2010 8:25 pm
by Grid Runner Adventures
i was thinking of running the 2x2s directly over top of where the trailer cross supports are. havnt measured them to see what the harbor freight trailer cross supports run on center though.
but made sence for mounting etc.
not planning on having it overhang on the back or front just the sides.

Posted:
Tue Mar 16, 2010 8:39 pm
by starleen2

Posted:
Wed Mar 17, 2010 6:37 am
by petertl
Wow. I would never guess one could cantilever 3/4â€

Posted:
Wed Mar 17, 2010 7:46 am
by Noob
[quote="petertl"]Wow. I would never guess one could cantilever 3/4â€

Posted:
Fri Mar 19, 2010 6:51 am
by petertl
I want to do exactly this. (6’ wide tear on a 4’ wide HF trailer.)
I was planning to use 2x2s, 16â€

Posted:
Fri Mar 26, 2010 9:01 am
by brewwagon
my 2 cents. the rule of thumb that I use when canting is that I want to have at least twice as much material on the opposite side of the overhang.
That being said, I dont know about canting just plywood. I think it would be a bit "springy"
Depending on the wood that you use for the frame, I wouldnt go anything less than 1" and anything wider than 16" on center.
I plan on doing a 2x2 and will be 12" on center for my canted pieces and 16 for the rest, with 1/2" plywood over than. If I can get my hands on some decent poplar I may go 1x2.
I'm at this step now in my build. You will see me in the local HD jumping up and down on sticks of lumber to see if I can break things (hopefully not my neck)


Posted:
Fri Mar 26, 2010 1:21 pm
by Corwin C
The whole idea of a torsion box structure is that all sides and corners are tightly fastened (bonded) to each other so that there is no possibility of the individual pieces parting company at any point along the seam short of breaking something (or intentional dis-assembly). Also, a sheet of material (plywood, masonite, beaver board, etc.) will only bend in one direction at a time (anyone who has attempted a compound curve can attest to this) and furthermore, sheet materials will not rack (meaning you can't push a rectangular piece into any type of parallelogram.)
That being said, the floor of a properly assembled torsion structure will not sag at the sides (your front and galley walls won't allow it, they will literally hold the floor UP) and it will not sag between those because the side walls which are bonded to the front wall, galley wall, AND floor won't allow it. What I'm essentially saying here is that you could build your tear out of 1/4" ply and IF the corners and edges are properly bonded, you could stand it up on a single corner fully loaded, and it would not change shape until the stresses on that corner are high enough to literally crush the ply. It could be balanced on a single point in the center of the floor and it will not sag (whatever you're using as that point may push a hole in the floor though.) The trick to this is the BOND between the pieces. If you're not using GLUE of some kind (some work better than others), then you aren't achieving the BOND to have a true torsion box structure. Mosquito bombers from WWII were literally built out of birch plywood and balsa, carried 2000 lbs. of bombs + fuel + crew in battlefield conditions, traveled at 400+ MPH, and the design is simply a properly designed torsion box structure. AND BTW, the majority of the skin surface was 1/4" ply.
Now, I'm not suggesting that everyone start building tears out of 1/4" ply with no framework. The ability of the even a skilled person with hand tools and off the shelf components will have a difficult time bonding 1/4" ply this way. Also, hinges, fixtures, and the like need some thickness (preferably in something other than ply) to attach to. Insulation is always nice (whether from creating a void and filling it or just from thick material.) Openings (doors, windows, vents, holes for wiring & plumbing, etc.) will also affect the strength of the sheet material. Natural materials, like wood, always behave a little bit differently from one piece to another and are somewhat unpredictable, so don't be afraid to overbuild a little. Also, the aging and weathering process can affect the strength of the materials and the quality of the joints. But, the structural design is sound.
Final answer ... if the structural parts are properly bonded, AND you have support somewhere in all three directions (X,Y,Z), AND you have "closed the box" (meaning all corners and edges are supported), you will have no problems with even a rather large cantilever.

Posted:
Fri Mar 26, 2010 2:51 pm
by Arne
If you plan on putting ply on the bottom and the top of the floor, you are in good shape....
ply'ing the bottom adds a lot of 'beam' strength.

Posted:
Fri Mar 26, 2010 9:38 pm
by Bigwoods
I took another approach and widened the trailer. The 4' HF trailer was widened to 5' and just involved a bit of welding. It went well and I felt better than cantilevering the sides. The process is available in the Northwoods build photos.
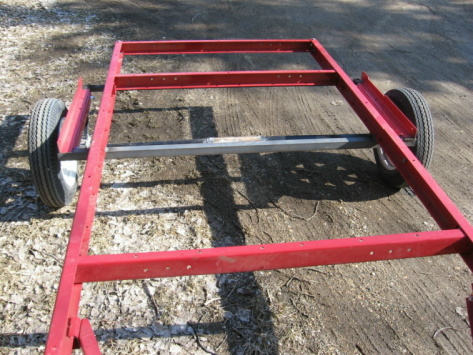

Posted:
Sat Apr 03, 2010 11:55 am
by Grid Runner Adventures
I actually did a bit of work on my harbor freight trailer. went to home depot and bought a nice thick water pipe and cut the spindles out of the stock hf axle and drilled holes through the ends of the water pipe once i cut it to the lenght i needed.
it looked like the barrel of a semi auto gun heh.
inserted the spindles into the ends of the pipe and then used those holes to fill in with welds its a whole ton stronger then the channel iron that they used on the stock axle.
i suggest this upgrade for all the hf trailers. I like having the spindles supported on all sides. if the trailer was overloaded and a weld broke the spindle can just hinge down and break on the stock trailer.
what besides spring weights are trailers rated at for cargo weight. I wonder what my upgrade has raised my trailer too.

Posted:
Sat Apr 03, 2010 2:10 pm
by RAYVILLIAN
I think I would have run the 2x2 out to the edge of the plywood but on the other hand the proof is in the pudding. I looked real close at Starleen2's trailer last weekend and didn't notice any sag. When you think about it all the weight on that 3/4 ply is the walls which give you more support and some cabinets. You won't be standing on that out side 12" . On the 12' warrior I put some 1/8" angle supports outside the frame but that was just because when I stood on it it did sag but when the trailer is done I won't be standing out there either so it is probably over kill.
Gary

Posted:
Sat Apr 03, 2010 2:25 pm
by len19070
I didn't go out quite to 72" but this same thing would have worked.
All I wanted to do was make the inside floor flat w/no wheel wells and to go as wide as the outside edge of the fender, 66".
http://s26.photobucket.com/albums/c106/ ... ?start=all
Happy Trails
Len

Posted:
Sat Apr 03, 2010 4:08 pm
by mikeschn
I'm a fan of only going out as far as the wheels... So in the case of a 4' trailer, that would be 66" wide (like Len's pic up there).
A 5' wide trailer would be 78" wide.
For the in between stuff, I would modify the chassis and the axle.
Mike...