Page 1 of 1
stitch and glue TD

Posted:
Thu Jul 29, 2010 10:23 am
by TD Beej
Has anyone tried building a TD by stitch and glue? I am wondering if it might be the easiest way to achieve the shapes and surfaces I want with my build. I want to have light build so I would then go back and add extra support for stress points such as anchoring locations or around openings. I figure since people use stitch and glue to make boats it should lend itself to making a TD shell quite nicely with good strength and flexibility.
Thanks, Beej

Posted:
Thu Jul 29, 2010 8:08 pm
by GPW
Beej .... seems possible if you can build a boat like that , a TD would be a likely candidate ...

Posted:
Thu Jul 29, 2010 8:32 pm
by afreegreek
yes, it will work just fine especially covered in fibreglass.. you could also use Sikaflex type adhesive to create nice filets at the joints and that will be plenty strong without the glass..
just make a sample corner with Sikaflex with a 1/2" filet and try to rip it apart.. you'll see..

Posted:
Thu Jul 29, 2010 8:35 pm
by caseydog
I thought about it, but didn't try it. I wanted a "tent on wheels," and doing something with canvas would have met that criteria, but wood and nails were more my speed.
I think it would be really cool, but I'd need help, to say the least.
CD

Posted:
Thu Jul 29, 2010 8:41 pm
by kennyrayandersen
I think that’s kind of how the puffin was built, no? I’m thinking of a modified stitch and glue myself – no stitching, but gluing and filleting the corners and laying some tape over that. There is nothing wrong with it structurally, but most want to insulate their tears as well, and if you are going to put in an inch of foam you might as well put an inner skin and turn it into a structural sandwich. In fact, rather than use ¼ inch material to do a stitch and glue, you could use 1/8 inch ply, ¾â€

Posted:
Fri Jul 30, 2010 9:24 am
by TD Beej
Probably no reason you couldn't use a SIP like panel to do the stitch and glue with.

Posted:
Fri Jul 30, 2010 10:46 am
by BigAl
Hi Beej, Having built a stitch n glue sailing dinghy and a 12 foot canoe. The first using copper wire for the stitches and the latter using small cable-ties.
I recommend going for the cable ties. You can trim them flush with a knife, but the copper wire needs ground down.
I agree that a small RV trailer lends itself well to the technique, but most boats are built with this technique around frames that define the shape whilst the glue cures. These frames are either temporary (like a form) or are part of the boat (like a transom or seat fames, etc,).
How do you hope to keep your shape true whilst the glue cures?
Can you share with us a sketch of your shape?
Check out this excellent
SnG boat building Tutorial

Posted:
Fri Jul 30, 2010 11:53 am
by TD Beej
BigAl wrote:I agree that a small RV trailer lends itself well to the technique, but most boats are built with this technique around frames that define the shape whilst the glue cures. These frames are either temporary (like a form) or are part of the boat (like a transom or seat fames, etc,).
How do you hope to keep your shape true whilst the glue cures?
Can you share with us a sketch of your shape?
Check out this excellent
SnG boat building Tutorial
For the shape I am planning to use prestressed panels, two sheets of 1/8th w/ or w/o insulation curved to the correct shape and then fiberglass and epoxied together.
This is still my target though I keep tweaking things and probably will do so right up to and during the build.
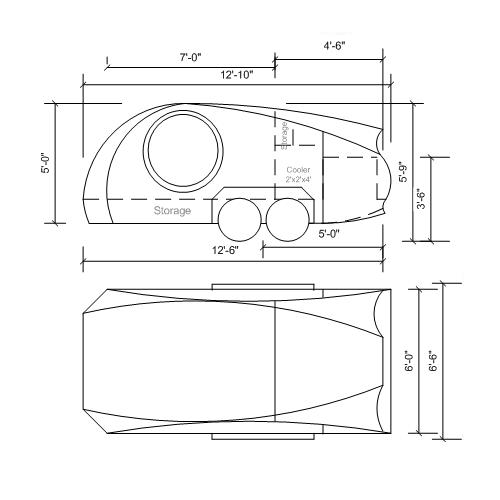

Posted:
Fri Jul 30, 2010 12:21 pm
by BigAl
Lookin groovy Beej!
Couldn't you just build it with glass over sculpted PE foamboard, and forget the ply on the outside?
You could embed ply panels in the foam where you need a mounting for a hinge or a light.

Posted:
Fri Jul 30, 2010 1:57 pm
by NathanL
Once you have your panels worked out you can build a S&G structure as fast or faster than just about any type of structure. Cut your panels, drill your holes, stitch together and it will be together and then you can do the epoxy in the seams.
Can build a S&G boat in a weekend, I see no reason why it wouldn't work for a teardrop "if" it has the right shape to it.
There's programs out there on the net you can layout your panels and stitch them together to make sure it goes together in the exact shape you need, then print them out scaled down and do it paper/card stock for a quick test.

Posted:
Sat Jul 31, 2010 11:03 am
by angib
This sounds like a very workable plan - S&G is an ideal building technique.
The problem is you need to work out the shape of the panels to stitch together. I recommend 'Hull Designer', a piece of shareware that works well:
http://www.carlsondesign.com/#Fun_Shareware
Like any software, it takes some to work out how to use it, but from then on it would be as easy as building a boat from plans.
Andrew

Posted:
Sun Aug 01, 2010 1:17 am
by afreegreek
the best was to come up with your panel shapes is to use a wooden 'wireframe' then use kraft paper to lay on the frame.. then you can just use the side of a pencil lead to rub the pattern on the paper.. remember, you only need half of your shape as the other half is mirror image.. this technique is way faster and more accurate than a computer program..
** what I mean by wireframe is what the sheer, chine, keel, stems, and deck ridge on a wooden S&G kayak would be..

Posted:
Sun Aug 01, 2010 1:34 pm
by TD Beej
Thanks for the links everyone.
afreegreek wrote:the best was to come up with your panel shapes is to use a wooden 'wireframe' then use kraft paper to lay on the frame.. then you can just use the side of a pencil lead to rub the pattern on the paper.. remember, you only need half of your shape as the other half is mirror image.. this technique is way faster and more accurate than a computer program..
** what I mean by wireframe is what the sheer, chine, keel, stems, and deck ridge on a wooden S&G kayak would be..
Using the kraft paper to transfer the mirror images from side to side or to generate the corners may be a useful tool. I will certainly keep it in mind.
Thanks, Beej