Floor framing red oak, poplar or something else?

Posted:
Sat Sep 04, 2010 11:39 pm
by KenC
For the wood framing that goes between the plywood floor and the steel trailer frame, would red oak or poplar be better to use, I'm looking for the best type of wood to use in an outdoor environment. Red oak and poplar are both available at the big box stores. I've gotten pieces of each to use for mock ups, the poplar is easier to work with (less splitting) but I've heard poplar is susceptable to rotting. Or are ther any other options that you can recommend ?
Thanks,
Ken

Posted:
Sun Sep 05, 2010 6:23 am
by Billy K
I've not built mine yet........Yellow Pine; has been suggested to me over and again.
Good Luck , with yours.

Posted:
Sun Sep 05, 2010 7:09 am
by tk
Red oak also is not great for weather resistance. White oak is. Of what's available at big box stores, cedar or treated yellow pine are probably your best options. The treatment currently in use on yellow pine is, I'm told, much safer for both you and the environment than the old CCA treatment.
Best,
Tom

Posted:
Sun Sep 05, 2010 8:53 am
by bobhenry
Billy K wrote:I've not built mine yet........Yellow Pine; has been suggested to me over and again.
Good Luck , with yours.
Southern Yellow Pine has been the choice species for almost all treated lumber for 5 or 6 decades.
Maybe they know something we don't


Posted:
Sun Sep 05, 2010 1:26 pm
by KenC
Thanks for the info everyone. Can anyone tell me if yellow pine is the same as select pine or if it would be good to use for the floor framing?
Another question regarding the trailer floor, would 3/4 in Arauco ACX be ok to use on the floor ? I would also coat the bootom with the black gooey stuff
Thanks,
Ken

Posted:
Sun Sep 05, 2010 5:22 pm
by Judeyramone
Southern yellow pine is what has been commonly used for treated lumber because it's a very dense durable wood, even untreated... and it's ugly; Unsuitable for decorative uses, primarily because it has too many knots. Wooden ladders are made of it as well, for the same reason. Select pine, or white pine - the 1x4 or 1x6, etc. boards you get at HD and lumber yards (if you're lucky enough to still have one near you), is an entirely different species, much less dense, less strong, fewer & tighter knots, and MUCH softer. I wouldn't use it for much of anything structural that you expose to the elements. I trimmed my garage with it, but not before priming both sides, and many coats of paint on the exterior surface.
IIRC, from my lumber yard days, the coding for plywood indicates ACX would be sanded on both sides (AC), exterior (X)... much like exterior wall sheathing (commonly referred to as CDX - CD=not finished on either side, X=exterior). As far as I can remember, the X rating comes from the fact that the plywood is assembled using an exterior glue, but it really doesn't hold up to the elements at all. It's basically glue that can withstand the elements long enough for your contractor to cover your exterior wall sheathing with siding. There is no plywood that will not delaminate w/o careful prep & maintenance. If you've ever seen an old wood garage door that was falling apart, the first part to go is the plywood panels.
All options you mention are going to rot, especially red oak - don't use that w/o many coats of waterproofing.
I'm gonna throw my hat into the treated lumber circle, but with this caveat:
Treated lumber is milled, bundled, and then dipped into the treating solution in very large bundles, and remains in those bundles until lumber retail workers bust them open & stock the boards on shelves at Home Depot. That's why those boards (especially the ones in the middle of the bundle) are usually wet when you buy them. Unless you let it dry out thoroughly before use, you will experience considerable shrinkage when it does dry out (this is why you are not required to space treated decking boards) - and...
Boards that are dried too quickly, or improperly, bend twist & warp - especially treated southern yellow pine, especially if it's 3/4" thickness. I suggest you find the straightest, truest, driest treated lumber you can, and let it dry in your garage before use, stacked horizontally with 1/4" spacers between each board and cinder blocks on top, every 2 or 3 ft apart.

Posted:
Sun Sep 05, 2010 6:15 pm
by madjack
...I use neither or any...I simply put the ply directly on top of the steel framing...............


Posted:
Sun Sep 05, 2010 8:25 pm
by Wolffarmer
Mad Jack
That is how I am going to build #2. I went way overboard on #1. Like many ( if not most ) of us here.
Randy

Posted:
Sun Sep 05, 2010 8:40 pm
by madjack
Wolffarmer wrote:Mad Jack
That is how I am going to build #2. I went way overboard on #1. Like many ( if not most ) of us here.
Randy
...a caveat...I used a 2x2 piece of red oak for the hinge spar...I guess I could have used 3 pieces of 1/2 ply and turned it, so the line of screws were going into the side, instead of the edge of the plys...I did this for the "overlap" spar, where the joint in the AL is located........
madjack


Posted:
Sun Sep 05, 2010 8:59 pm
by Wolffarmer
Madjack. All of my hinges are screwed to Oak, red or white, not sure what got put where. Probably over kill once again on some of them but not for the galley hinge.
Randy

Posted:
Sun Sep 05, 2010 9:17 pm
by KenC
madjack wrote:...I use neither or any...I simply put the ply directly on top of the steel framing...............

MJ, sounds like a good plan, how do you tie the walls into the ply floor.
Everyone else thats for the input, looks like I'll be searching for some lumber yards to get a better selection of framing material if i go with the subfloor framing
Thanks,
Ken

Posted:
Sun Sep 05, 2010 11:32 pm
by madjack
Ken, my side walls come down over the trailer frame and I use 1x1x1/16 aluminum angle as cleats to join floor/walls together...gorilla glue or epoxy and screws every 4-6"s and it is solid as can be.........
madjack
p.s. I use self tapping trailer deck screws, thru the sidewalls and into the trailer frame to attach all, to the trailer itself...5 per side..........MJ
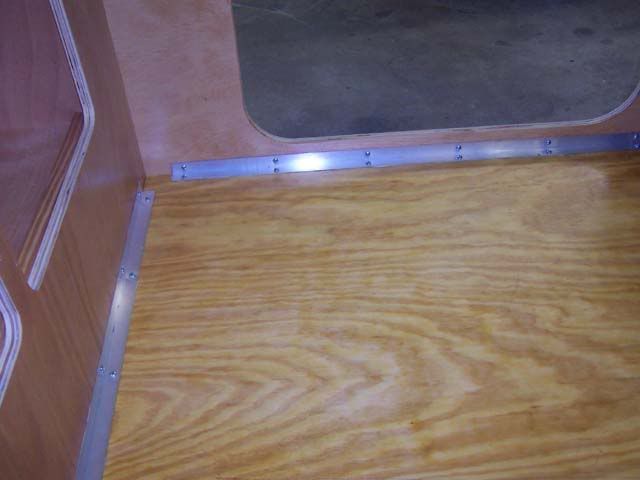

Posted:
Mon Sep 06, 2010 3:33 pm
by KenC
[quote="madjack"]Ken, my side walls come down over the trailer frame and I use 1x1x1/16 aluminum angle as cleats to join floor/walls together...gorilla glue or epoxy and screws every 4-6"s and it is solid as can be.........
madjack
p.s. I use self tapping trailer deck screws, thru the sidewalls and into the trailer frame to attach all, to the trailer itself...5 per side..........MJ quote]
MJ,
Thanks for taking the time to explain the details of how you attached the walls, and the picture is definatley worth a thousand words.
Regards,
Ken