How many ribs in a hatch?

Hi everyone,
Since winter has arrived in Minnesota and I can no longer work on the Lily Pad outside or in the garage, I'm going to start working in the furnace room. I figured I could construct the hatch while I wait for warmer weather.
I've noticed two methods of building the framework. Here's one with six vertical ribs and short horizontal braces in between the ribs:
Here's one that has two outside ribs and full width horizontal crosspieces:
This looks like a 4-wide, but I have seen pics of 5-wide hatches built this way.
Keeping in mind my skill with the jigsaw
, I would MUCH rather cut only TWO curved pieces than SIX. Don't want to burn out the good ol' Craftsman belt sander my husband used in the good ol' days
to make redwood signs. It saved me on the profile and door cuts.
Should I use 3/4" plywood or 1/2" plywood for the ribs? I had a heckuva time cutting the Benroy profile out of 3/4" plywood. I'm assuming it's easier to cut 1/2", so if I cut 4 - 1/2" ribs and glue two together for the outside ribs, then did straight cross braces, would that give me a strong enough hatch? I'll be skinning both sides with 1/8" bending plywood.
Any and all advice gratefully received.
Since winter has arrived in Minnesota and I can no longer work on the Lily Pad outside or in the garage, I'm going to start working in the furnace room. I figured I could construct the hatch while I wait for warmer weather.
I've noticed two methods of building the framework. Here's one with six vertical ribs and short horizontal braces in between the ribs:
Here's one that has two outside ribs and full width horizontal crosspieces:
This looks like a 4-wide, but I have seen pics of 5-wide hatches built this way.
Keeping in mind my skill with the jigsaw

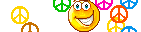
Should I use 3/4" plywood or 1/2" plywood for the ribs? I had a heckuva time cutting the Benroy profile out of 3/4" plywood. I'm assuming it's easier to cut 1/2", so if I cut 4 - 1/2" ribs and glue two together for the outside ribs, then did straight cross braces, would that give me a strong enough hatch? I'll be skinning both sides with 1/8" bending plywood.
Any and all advice gratefully received.