Frame Drawing - Feedback Needed

Hello Everyone,
I started a build thread and this is my first question!
Here is a drawing of my frame plan :
Dimensions : 5" x 8"
Main Frame Square tubing : 2" x 2" x 0.125"
Tongue Square tubing : 2" x 2" x 3/16"
Axle : one piece Torsion will "add" a crossbar
Goals :
- Having a frame that is 2" thick all the way
(Tongue not being lower than the frame)
- I also don't want it to be too heavy.
- Floor pine framed + 5.2mm Meranda with 1" foam in the middle (reason for the tongue extending further back)
Questions :
- Should I add angle support for the tongue ?
- Is this "overkill" ?
Thanks of the feedback!
Denis
I started a build thread and this is my first question!
Here is a drawing of my frame plan :
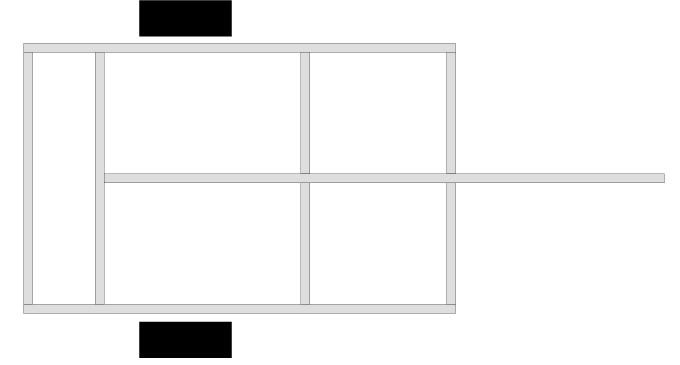
Dimensions : 5" x 8"
Main Frame Square tubing : 2" x 2" x 0.125"
Tongue Square tubing : 2" x 2" x 3/16"
Axle : one piece Torsion will "add" a crossbar
Goals :
- Having a frame that is 2" thick all the way
(Tongue not being lower than the frame)
- I also don't want it to be too heavy.
- Floor pine framed + 5.2mm Meranda with 1" foam in the middle (reason for the tongue extending further back)
Questions :
- Should I add angle support for the tongue ?
- Is this "overkill" ?
Thanks of the feedback!
Denis