Page 1 of 3
Corrugated Roofing

Posted:
Fri Jul 08, 2011 7:46 am
by Deryk the Pirate
Hi All,
I was wondering any opinions on corrugated roofing
I know they have been putting it on roof's for a long time and they sell screws with special washers to seal it so it doesnt leak. Was wondering any idea how it would handle the 60+ mile per hour wind from driveing?
thanks
deryk

Posted:
Fri Jul 08, 2011 8:05 am
by bobhenry
Pardon the poorly scanned picture but this little barn clocked more than 30,000 miles in the 6 years I was building mini barns.
Lay from rear to front and double the lap over of material and you will need to roll over the front sheet and trap it so the wind won't be able to lift it.

Posted:
Fri Jul 08, 2011 8:19 am
by David S
Deryk,
Back in the day, my family built round top and pole type barns.
I don't ever recall the tin being ripped off a building by wind with out taking the wood sheeting with it.
I would make sure the rafters are fastened with hurricane clips and make sure the metal is screwed down good and there are no loose edges to catch the wind.
My 2 cents, worth exactly what you paid.
David

Posted:
Fri Jul 08, 2011 11:06 am
by dh
They sell a wood strip with a 'wave' cut in it to match the corigations in the metal, might make gettint a good seal on the frontand back easier. I know Lowe's or Home Depot sells it, but not both.

Posted:
Fri Jul 08, 2011 11:13 am
by Deryk the Pirate
I was thinking of putting it on in the same direction as the picture since I could lay a 2nd layer on the ends to increase strength. I like tghe idea that rsin will run off it very well.
Deryk

Posted:
Fri Jul 08, 2011 11:28 am
by David S
dh wrote:They sell a wood strip with a 'wave' cut in it to match the corigations in the metal, might make gettint a good seal on the frontand back easier. I know Lowe's or Home Depot sells it, but not both.
Most mfg's also have a foam gasket to, which seems to seal a little better.

Posted:
Fri Jul 08, 2011 11:28 am
by aggie79
Deryk the Pirate wrote:I was thinking of putting it on in the same direction as the picture since I could lay a 2nd layer on the ends to increase strength. I like tghe idea that rsin will run off it very well.
Deryk
Deryk,
I'm betting that the curve of the roof in the picture was pre-formed. I don't think you can bend "straight" sheets of corrugated steel/aluminum against the (perpindicular to) the corrugations.
When I used to build metal buildings, we used fasteners on the "highs" of the corrugations to tie to the purlins, rather than in the "lows" or "flats". This resulted in a lot less call backs for leaking roofs.
Take care,
Tom

Posted:
Fri Jul 08, 2011 11:39 am
by Deryk the Pirate
Tom, that's an interesting and important point abouut the bending.....hmmm always something lol

Posted:
Fri Jul 08, 2011 11:39 am
by David S
aggie79 wrote:Deryk the Pirate wrote:I was thinking of putting it on in the same direction as the picture since I could lay a 2nd layer on the ends to increase strength. I like tghe idea that rsin will run off it very well.
Deryk
Deryk,
I'm betting that the curve of the roof in the picture was pre-formed. I don't think you can bend "straight" sheets of corrugated steel/aluminum against the (perpindicular to) the corrugations.
When I used to build metal buildings, we used fasteners on the "highs" of the corrugations to tie to the purlins, rather than in the "lows" or "flats". This resulted in a lot less call backs for leaking roofs.
Take care,
Tom
If you use the corrugated barn metal,not the R panels used on metal buildings.it will bend even sharper than the pic.as I said we used to build round top or some call them quansit barns,and they had a lot more curve than what your doing.Here is link to what I was talking about the foam gasket.
http://www.metaldeck.com/foam/78.htm[/url]

Posted:
Fri Jul 08, 2011 11:51 am
by droid_ca
what kind of metal is it made from?

Posted:
Fri Jul 08, 2011 1:39 pm
by forestfrog
You could run the corrugations long ways, like on the Vardo by Tumbleweed...
it would make it easier to form to the curve of the roof.
Either direction will require a sturdy, well sealed underlayment of some sort.
This is the shape I'm leaning towards for my new 5'x8' standy build!
I was thinking of putting it on in the same direction as the picture since I could lay a 2nd layer on the ends to increase strength. I like tghe idea that rsin will run off it very well.
Oops, good point, I hadn't considered rain run off yet, lol!
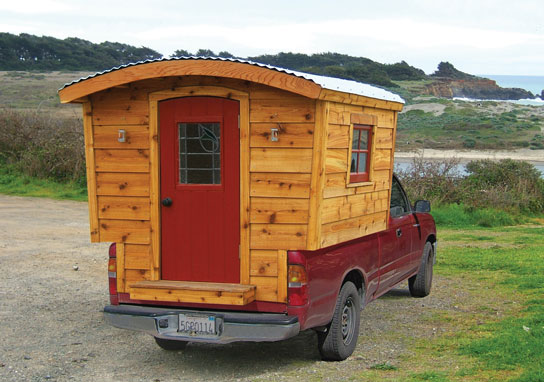

Posted:
Fri Jul 08, 2011 1:49 pm
by droid_ca
couldn't you aneal the metal to tak your shape and then temper it afterwards

Posted:
Sat Jul 09, 2011 10:52 am
by Artificer
Wind: Metal buildings are made to survive 80mph winds. You will have many more fasteners, probably, so it should be secure... just like bobhenry said. Typical post frame building construction has purlins (2x's between the trusses) no more than 24" on center. This is what the metal is screwed down to. I can see your roof having trusses/ribs 24" on center or so, and 2x2's every 6-12". If you still use the typical 9" spacing for screws, you'll still have 2-4 times as many screws holding the metal on. I would make sure that you didn't have more than an inch or two of unsupported metal, and none on the leading edge/front of the trailer.
Bending the metal: depending on the thickness, you shouldn't have a problem putting in the small bend. I agree that the roof will drain better with the corrugations running along the bend.
Metal: the sheets are either galvanized steel, or galvanized and painted. Corrugated metal typically only has a glavanized coating. If you try to aneal the metal, the coatings will be burnt off. The metal is mild steel, so it doesn't harden. Annealing will not do much anyway. There are other corrugated materials (fiberglass, polycarb, Onduro), but I think steel is the best thing to use.
Soffit on the front: If you really want a significant overhang on the front of the trailer, you will have to design in some strength. Extend the 2x2's (if you use that method) all the way to the end of where you want the sheetmetal. cover with a couple layers of 1/4" plywood thats glued together. You get your curved surface, and the plywood will add a lot of support to the metal. I wouldn't go more than 24" out on the front without more support or larger purlins.
Sealing the edge: I wouldn't use the foam material to fill up the corrugations. I've seen too many of those pieces on the ground after big wind storms. May not happen to the vardo, since they'll be on the sides, but why chance it. The wooden pieces with silicone caulk will make a very tight seal, and provide a sturdy backing on the end of the sheets where you need it.
Michael

Posted:
Sun Jul 10, 2011 1:30 am
by dh
You could run the ribs front to back and raise the tongue jack a bit when it rains.

Posted:
Sun Jul 10, 2011 5:39 pm
by Corwin C
I put some of
this on a covered porch last year. When I got it home, I set it down, bridging a couple of 6"x8" railroad ties that were about eight feet apart. It flexed enough to touch the ground in the middle by its own weight. If your curve is slight enough and you're careful, I think that you should be able to pull it off.