Anyone ever use balsa core for an ultralight build

I'm just thinking.....(dangerous)....
I haven't finished my first tear, but of course I'm already thinking ahead to a possible second
If I were to build another one, it would be all about lightweight, for pulling behind my Hyundai. It would be a simple 4x8 so I could go with standard size materials this time. I was wondering, has anyone here attempted to build a sandwich wall tear with balsa core? I know it's very strong, as we've had it in the deck of every boat we've owned, and extremely light. I wonder if one could take just 3/4" balsa core, laminate 1/8" plywood skins on both sides, only use lightweight framing around the door and outline.
Perhaps the floor too, a sandwich construction with 1/4" or 3/8" ply on top, balsa core and 1/8" ply on bottom, lightweight framing around the outside only, fiberglassed with one layer of lightweight cloth on the bottom side to seal out water. Standard foam insulation in the roof. One layer of lightweight fiberglass cloth on the entire outside.
I am not comfortable with the foamie idea because it just seems to fragile and easy to damage.
I know there are a lot of boat builders on this forum and I imagine some of you have worked with balsa. We replaced a balsa deck in one of our boats once and it seemed to me the fiberglass shell covering it was pretty thin. We had some pretty hefty folks running around on the deck and it was solid as a rock, but yet I was amazed at how light the stuff was.
I know it's not cheap. Lets not even have that discussion.
I'm just inquiring as to the feasibility of building that way.
Anyone.....anyone.....


I haven't finished my first tear, but of course I'm already thinking ahead to a possible second

If I were to build another one, it would be all about lightweight, for pulling behind my Hyundai. It would be a simple 4x8 so I could go with standard size materials this time. I was wondering, has anyone here attempted to build a sandwich wall tear with balsa core? I know it's very strong, as we've had it in the deck of every boat we've owned, and extremely light. I wonder if one could take just 3/4" balsa core, laminate 1/8" plywood skins on both sides, only use lightweight framing around the door and outline.
Perhaps the floor too, a sandwich construction with 1/4" or 3/8" ply on top, balsa core and 1/8" ply on bottom, lightweight framing around the outside only, fiberglassed with one layer of lightweight cloth on the bottom side to seal out water. Standard foam insulation in the roof. One layer of lightweight fiberglass cloth on the entire outside.
I am not comfortable with the foamie idea because it just seems to fragile and easy to damage.
I know there are a lot of boat builders on this forum and I imagine some of you have worked with balsa. We replaced a balsa deck in one of our boats once and it seemed to me the fiberglass shell covering it was pretty thin. We had some pretty hefty folks running around on the deck and it was solid as a rock, but yet I was amazed at how light the stuff was.
I know it's not cheap. Lets not even have that discussion.
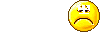
Anyone.....anyone.....


