andreuther wrote:I had my axle cut in half and extended it a foot using a sleeve. My axle was 1.5'' solid steel and is now 2'', the sleeve is the full length of the axle. Thanks to my welding friend it all cost me a case of beer.
Did you take any photos to document the process? I've been planning to do the same, after I become semi-skilled at welding. Of course, my first love is the bolt-together process, so it will also be utilized. I did a search on the forum for any sleeved axles, and only found this one, which isn't really a sleeve over the axle, but a solid rod inserted/welded into the tubing,
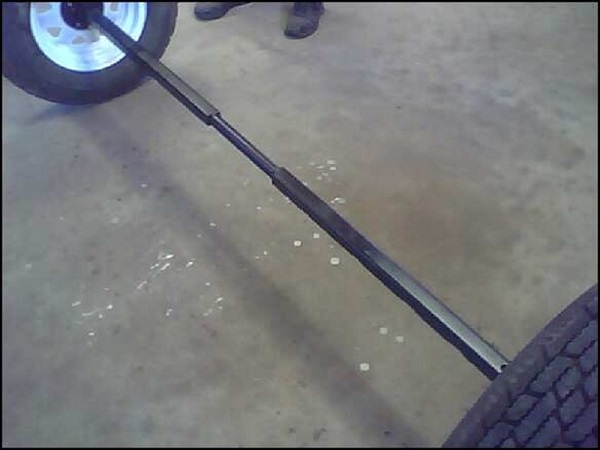
- posted by bbarry ยป Fri Jan 09, 2009 7:17 pm
- axle (sleeved).jpg (54.7 KiB) Viewed 1817 times
My axle is 1.25" or 1.5" square tube (either one?, I don't know- measures @ 1.375"- I don't think they make that size). Either way, even though the axle bearings and hubs have been upgraded to bigger ones, capable of 2000lbs (according to the trailer supply house), I don't trust the probably weakened (sat in a composted area for 18 years) square tube between them. My friend that welded the trailer additions, and has built several trailers before, bought the changeover hub/bearings and checked the stubs for weld quality and trueness. He said the axle would be strong enough for 1000lbs, my goal, at least. Now exceeded at 1475lbs, I'm going to sleeve the tubing, all the way from one stub to the other, and weld/bolt it where needed, and put new spring/axle clamps on it. The springs are fine, the attaching hardware is new, so I will buy a new axle for the next trailer, not this one. Pictures of the proper process would help me on this one, which I'll do in a coupla months. (of course, I've already sourced a new axle for this one, just in case) !