laying glass on a horizontal surface is easy peasy
coat the wood w/ epoxy and allow it to cure
once cured sand the epoxy
lay the cloth out over the entire surface and w/ your hands(in NITRILE gloves) smooth all the wrinkles out
always(when possible) begin coating by pouring the pox in the center of your work and w/ a plastic auto body shop putty spreader squeegie the pox out toward the edges
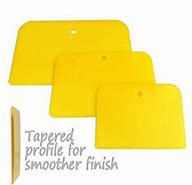
- bondo spreader.jpeg (4.13 KiB) Viewed 1661 times
the first coat on the glass should make the silverish fibers go clear(the silver appearance is only the light reflecting off the fine fibers)
squeegie the cloth down to the wood leaving a weave pattern that you can see and feel butt the cloth will be clear
here is a pic of an old home made oar the grandkids broke and i have glassed over the repair w/ the 1st coat of epoxy
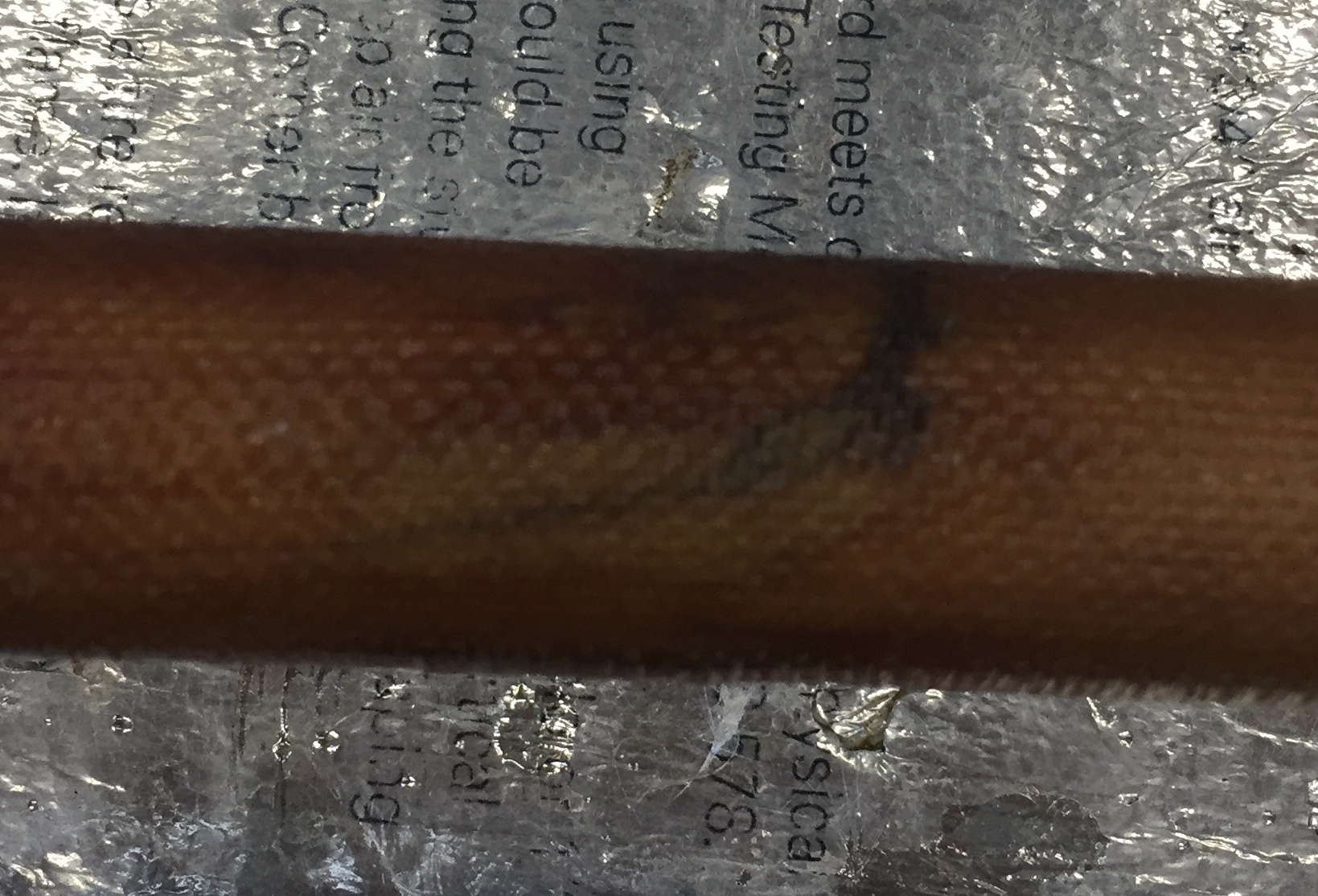
- fullsizeoutput_f7b.jpeg (579.92 KiB) Viewed 1661 times
at this point simply dragging the spreader over the weave will feel like it is dryish
allow this coat to cure slightly (just barely tacky) and apply a second coat again beginning in the middle
this is called HOT COATING and the result is one thicker application instead of several coats that are layered
repete this step until you have a totally slick surface
if you allow these last coats to cure completely it will be necessary to sand between coats
when the pox is almost finger nail scratch cured you can cut any excess cloth away w/ a sharp pair of cheap scissors being careful not to lift the glass cloth away from the wood
once fully cured a rasp will knock the excess cloth off easily
one caution before i sign off is to be sure to use 2 PART EPOXY not FIBERGLASS RESIN which is a polyester product and is hardened w/ drops of catalyst(usually an MEK family member)
ALWAYS WORK IN A WELL VENTILATED AREA AND WEAR BREATHING PROTECTION AND NITRILE GLOVES(many of these chemicals will melt latex and you don't want this stuff on your skin!)
BONNE CHANCE
sw