Ideas Stage

Hi all,
We're a couple who has painstakingly rebuilt an old trailer, only to have the aluminum contract enough during the winter to get all the new materials moulded to the point of no return and so now we're looking to build anew. We have the trailer stripped to the bare frame and once it cools down enough will be cleaning it up and painting it.
The design isn't going to be a teardrop, but we're definitely leaning in the general area of a foamie. (XPS, not EPS!)
Initial problems with respect to the outter skin: (We're in Eastern Canada and supplies are limited)
1) TBII is available in gallons only at one supplies reseller for a whopping cost of $40.00/gal which is the same price as polyester resin, here. In fact the resin is cheaper by the 5-gal pale.
2) Glidden Gripper is not sold here, and though there is some speculation that a CIL branded variant is the same product, there is nothing to validate that. Also, I've read that it may not be what it once was, and that the jury is kinda out on that one.
Given these limited options, we could build fibreglass/poly resin skins and somehow try to laminate them onto the foam with GS perhaps, though I can't find any indicators of the possible results. (I'm aware that poly resin eats XPS.) Since the weight and consequent tension would depend on size, a down scale test isn't very practical. Like most we're trying to be very thrifty and building full-scale tests, isn't pragmatic, so we're looking for alternatives. Glass is fairly expensive here as well.
A couple of thoughts have crossed our minds - like the possibility of using a 2-part urethane paint as a 2-in-1 paint / adhesive for canvass. Certainly not cheap at $170/gal, but epoxy is about the same and them to have to prime & paint it makes it significantly more costly. Also, Zinsser has a new product out called BondZ http://www.rustoleum.ca/CBGProduct.asp?pid=291, and then I ran across this: http://www.swingpaints.com/product/3133 Sadly, little information is available about either so I may have some testing to do. Another candidate for testing is this: http://www.homedepot.ca/product/kilz-pro-x-interior-p10-pva-drywall-primer-1896-l/959103. Since it's spec'd as PVA it caught my eye, but it's my understanding that If it's not crosslinked PVA then it wouldn't have the water resilience of TB2, and it's adhesion to foam is also a big question mark at this point. Dollar wise the Kiltz looks VERY attractive, if it works. I have also read VERY promising things about 3M's Super Trim http://www.sailrite.com/3M-08090-Super-Trim-Adhesive, on foam, but that would be quite costly as well, and I'd question how well it would work with canvass..
In terms of the design:
We're not planning to haul this any huge distances, but we want to be able to pull it with an SUV, and so weight and aerodynamics are factors, but not absolutely critical ones. Given this we're not sold completely on a frameless design, but rather trying to limit it's weight as much as possible.
The PVC frame-up builds really caught our attention until we went to try to find some locally. Home Depot up in these parts doesn't carry 3/4" PVC and what they do carry is pricey as hell. I was thinking about embedding some 1X2 into the foam glued in using either GG or GS.
(Hint to those who use spray foam as an adhesive, if after a short time of spraying it, you disrupt it's expansion (remove the pieces being glued and putting them back together) the expansion is greatly limited after the fact. This could also be true of GG urethane glue, but I'm not certain.
Have also thought to try and find some 1.75" steel studs which would decrease weight significantly, and being sandwiched between sheets of foam, be very rigid. Worse case, pop rivot them together back to back for middle-of-the wall studs.
Since steed studs are mandatory for all commercial buildings up here, some myths about their strength can be quashed right out of the gate. Built properly, steel studded walls are plenty strong. Impregnated with XPS and sprayed in (carefully) at both ends, the wall would be as strong as hell.
The design of a full pop-up holds a lot of appeal to us for the reduced drag, but a decent DIY lift system still eludes us. Too bad we sold a junked pop-up last year! The Foamstream & Streamline builds also look great to us so we're still wandering around in terms of where to take the build. Hinged pop-ups on the other hand, don't appeal for us, so much. We may be using this well into the fall and so we might have to abandon the pop up ideal because in the winter, sealing for heat loss would be an issue. That's still up in the cloud of thoughts for the moment.
Size wise, 12/13 ft would do us fine, but see attached (I hope) scale of the trailer on graph paper where 1 square = 1FT. We may narrow the whole thing and cut off some of the rear bumper and loose an axle in the process, as it's much larger than we need. The original camper was 15ft with a footprint-on-frame length of 13.5ft and an overall trailer length of 18 ft. We can go longer if necessary but the 12ft length holds appeal in terms of materials VS waste. 14 would be a viable alternative.
Since we have new(ish) leftover aluminium for the old roof, we were thinking of laying out a 2X2 & 1X2 (on end) framing, filling it with XPS spray foamed in place, covering the bottom with aluminium (rodent deterrence) and going with 1/2" ply for the sub-floor. Also worth noting, I'm thinking hard about making it removable easily, from the trailer chassis, for another use.
Another note:
Last year we had 18 ft of snow fall in just over a month.. crazy year but a good benchmark.. so the roof has to be strong enough for some snow loads. My initial thoughts were using 2X6 as trusses and curving them to 2X2 sized, but over the span we have of width to work with, it's not much of a curve.
So far that's where we stand. Any/all discussions/ideas/input very welcomed. I realize it's early but this is the time to plan
**Edit**
Seems my attempt to post a pic of the trailer failed. Here (I hope) are before and after proposed mods:
Before:
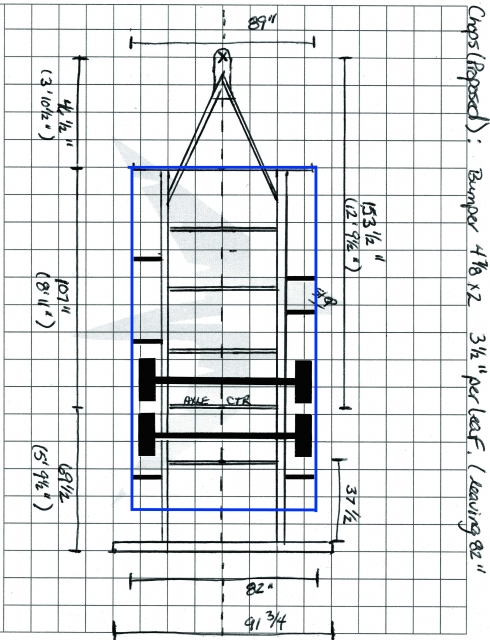
After:

We're a couple who has painstakingly rebuilt an old trailer, only to have the aluminum contract enough during the winter to get all the new materials moulded to the point of no return and so now we're looking to build anew. We have the trailer stripped to the bare frame and once it cools down enough will be cleaning it up and painting it.
The design isn't going to be a teardrop, but we're definitely leaning in the general area of a foamie. (XPS, not EPS!)
Initial problems with respect to the outter skin: (We're in Eastern Canada and supplies are limited)
1) TBII is available in gallons only at one supplies reseller for a whopping cost of $40.00/gal which is the same price as polyester resin, here. In fact the resin is cheaper by the 5-gal pale.
2) Glidden Gripper is not sold here, and though there is some speculation that a CIL branded variant is the same product, there is nothing to validate that. Also, I've read that it may not be what it once was, and that the jury is kinda out on that one.
Given these limited options, we could build fibreglass/poly resin skins and somehow try to laminate them onto the foam with GS perhaps, though I can't find any indicators of the possible results. (I'm aware that poly resin eats XPS.) Since the weight and consequent tension would depend on size, a down scale test isn't very practical. Like most we're trying to be very thrifty and building full-scale tests, isn't pragmatic, so we're looking for alternatives. Glass is fairly expensive here as well.
A couple of thoughts have crossed our minds - like the possibility of using a 2-part urethane paint as a 2-in-1 paint / adhesive for canvass. Certainly not cheap at $170/gal, but epoxy is about the same and them to have to prime & paint it makes it significantly more costly. Also, Zinsser has a new product out called BondZ http://www.rustoleum.ca/CBGProduct.asp?pid=291, and then I ran across this: http://www.swingpaints.com/product/3133 Sadly, little information is available about either so I may have some testing to do. Another candidate for testing is this: http://www.homedepot.ca/product/kilz-pro-x-interior-p10-pva-drywall-primer-1896-l/959103. Since it's spec'd as PVA it caught my eye, but it's my understanding that If it's not crosslinked PVA then it wouldn't have the water resilience of TB2, and it's adhesion to foam is also a big question mark at this point. Dollar wise the Kiltz looks VERY attractive, if it works. I have also read VERY promising things about 3M's Super Trim http://www.sailrite.com/3M-08090-Super-Trim-Adhesive, on foam, but that would be quite costly as well, and I'd question how well it would work with canvass..
In terms of the design:
We're not planning to haul this any huge distances, but we want to be able to pull it with an SUV, and so weight and aerodynamics are factors, but not absolutely critical ones. Given this we're not sold completely on a frameless design, but rather trying to limit it's weight as much as possible.
The PVC frame-up builds really caught our attention until we went to try to find some locally. Home Depot up in these parts doesn't carry 3/4" PVC and what they do carry is pricey as hell. I was thinking about embedding some 1X2 into the foam glued in using either GG or GS.
(Hint to those who use spray foam as an adhesive, if after a short time of spraying it, you disrupt it's expansion (remove the pieces being glued and putting them back together) the expansion is greatly limited after the fact. This could also be true of GG urethane glue, but I'm not certain.
Have also thought to try and find some 1.75" steel studs which would decrease weight significantly, and being sandwiched between sheets of foam, be very rigid. Worse case, pop rivot them together back to back for middle-of-the wall studs.
Since steed studs are mandatory for all commercial buildings up here, some myths about their strength can be quashed right out of the gate. Built properly, steel studded walls are plenty strong. Impregnated with XPS and sprayed in (carefully) at both ends, the wall would be as strong as hell.
The design of a full pop-up holds a lot of appeal to us for the reduced drag, but a decent DIY lift system still eludes us. Too bad we sold a junked pop-up last year! The Foamstream & Streamline builds also look great to us so we're still wandering around in terms of where to take the build. Hinged pop-ups on the other hand, don't appeal for us, so much. We may be using this well into the fall and so we might have to abandon the pop up ideal because in the winter, sealing for heat loss would be an issue. That's still up in the cloud of thoughts for the moment.
Size wise, 12/13 ft would do us fine, but see attached (I hope) scale of the trailer on graph paper where 1 square = 1FT. We may narrow the whole thing and cut off some of the rear bumper and loose an axle in the process, as it's much larger than we need. The original camper was 15ft with a footprint-on-frame length of 13.5ft and an overall trailer length of 18 ft. We can go longer if necessary but the 12ft length holds appeal in terms of materials VS waste. 14 would be a viable alternative.
Since we have new(ish) leftover aluminium for the old roof, we were thinking of laying out a 2X2 & 1X2 (on end) framing, filling it with XPS spray foamed in place, covering the bottom with aluminium (rodent deterrence) and going with 1/2" ply for the sub-floor. Also worth noting, I'm thinking hard about making it removable easily, from the trailer chassis, for another use.
Another note:
Last year we had 18 ft of snow fall in just over a month.. crazy year but a good benchmark.. so the roof has to be strong enough for some snow loads. My initial thoughts were using 2X6 as trusses and curving them to 2X2 sized, but over the span we have of width to work with, it's not much of a curve.
So far that's where we stand. Any/all discussions/ideas/input very welcomed. I realize it's early but this is the time to plan

**Edit**
Seems my attempt to post a pic of the trailer failed. Here (I hope) are before and after proposed mods:
Before:
After: