First side looked good-the grease was still red and clean.
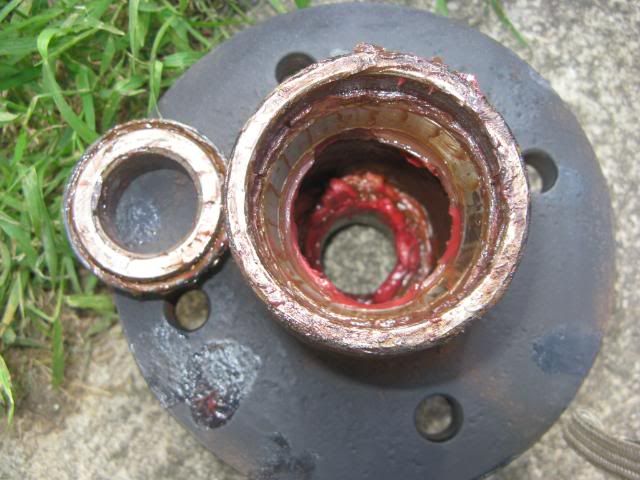
The other side is a different story. As soon as I pulled the dust cap off, I noticed dark brown grease with a muddy consistency. The outer bearing came off ok but when I pulled the hub out with the castle nut attached it came off without the inner bearing. The inner bearing is frozen on the spindle. I have been tapping on it from behind with a screwdriver and hammer but hope there is a better way to do it. Will something like WD-40 help loosen it up?
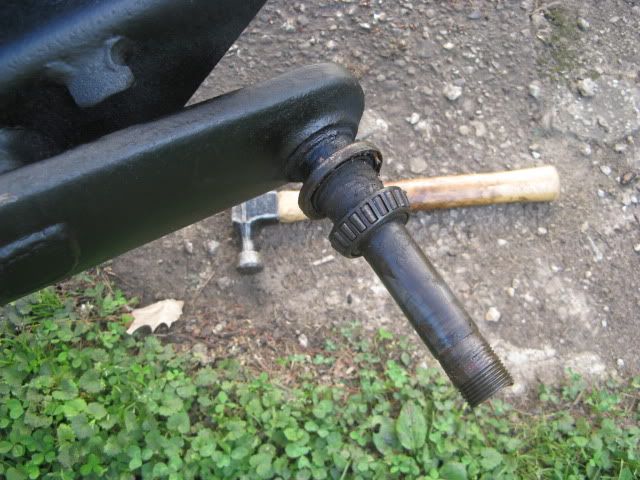
Also, The tutorials I found mention a washer behind the castle nut. I did not have this washer. Is it possible that my hub design doesn't use a washer or are they likely missing and need to be added?