Numbers:
First we have to establish the design/analysis criteria, and the environment
Typically on-road (we'll hereafter refer to this as over the road (OTR)) vehicles and trailers are designed to 3gs and off-road (OR) vehicles and trailers are designed to 5gs - we will consider those Design Limit loads (DLL) (maximum loads the structure would ever see during it's lifetime). We also generally use an ultimate load factor of 1.5 to arrive at the Design Ultimate Load (DUL). The criteria is no yield at DLL, and no failure at DUL.
Let's also make some assumptions about the teardrop and introduce some dimensions based on the design goals. For now -- let's set the weight at no more than 300 lb (and hopefully we will be under that significantly). The 1963 FIAT 500 is 52 in. wide, but the Smart fortwo is 60 inches wide, so in order to clear the fortwo there should be somewhere in the neighborhood of 30 inches of clearance. so, the distance we need is from the ball (the load to the tongue is introduced at the ball) to where the cabin intersects the trailer. If your cabin curves aft at the front bottom, it's critical to use the intersection of cabin and frame rather than the distance to the from of the cabin. In my cabin design I brought the front straight down for two reasons 1) it makes the front of the cabin stiffer and stronger because there is a large vertical section to react the loads, and 2) it reduces the moment arm in the tongue of the frame, and so reduces the stress in the frame. That might not be a showstopper, but in any case the right dimension needs to be used in the calculations.
First let's pick a material. Since we are shooting for lightweight, let's pick aluminum, and the most readily available and at a decent price is 6061-T6. Furthermore, 6061 is a weldable aluminum alloy. The properties are:
E, Young's Modulus = 9.9E6
Fcy = compression yield = 37 Ksi
Ftu = Ultimate allowable tension stress = 41 Ksi
For weld zones (we'll talk about those later) the material becomes annealed, but 6061 quickly age-hardens over a few weeks and months to the T4 condition. So, for heat affected areas we will use the T4 properties:
E, Young's Modulus = 9.9E6
Fcy = compression yield = 16 Ksi
Ftu = Ultimate allowable tension stress = 26 Ksi
(When we look at the difference in properties between the T6 and T4 conditions, it tells us is that we don't want to do ANY welding in a stress critical area!)
Since we set the weight of the teardrop at 300 lb, we can use a percentage of that weight to apply to the coupler at the ball .I think a fair target would be 15% of the total trailer weight, but lets be on the safe side and use 20%. We use the letter P for load (because we use L for something else!)
P = .20 * 300 lb = 60 lb
Now we calculate the maximum moment in the tongue area which is where the front of the cabin meets the frame
L = 30 inches (tongue length from ball to cabin)
M = L * P = 60 lb * 30 inches = 1800 in-lbs
Inertia is the beams resistance to bending. Inertia for a rectangular section is:
I = 1/12bh^3 -- that is for a solid section where b is the width and h is the height.
For a hollow section we can calculate what it would be for a solid section and then subtract the hole from it. Our equation then becomes:
I = 1/12(b_outer * h_outer^3 - b_inner * h_inner^3)
Alternately sometimes you can find I listed for a particular beam section - the units are in^4
The astute observer will see that the h term is cubed! So, a 1x2 section, for instance, is much stronger standing up than lying down! We'll stand ours up!
Let's start by using a 1x2 aluminum section with a .062 wall, standing vertically!
I = 1/12 ((1)*(2)^3 - (.875)*(1.875)^3) and since we have 2 frame members the equation becomes:
I = 1/6 ((1)*(2)^3 - (.875)*(1.875)^3) = .372 in^4
The bending stress is: F_b = Mc/I where M is the Moment, c is the distance from the section centroid to the outer fiber (for symmetric sections it is just 1/2 the height), and I is the Inertia
The original moment was 1800 in-lb, but that is at 1g. For OTR we'll use 3g, and for OR we'll use 5g
M_OTR = 1800 in-lb *3 - 5400 in-lb
M_OR = 1800 in-lb *3 = 9000 in-lbs
plugging in the numbers into the bending stress equation: fb = M*c/I
fb OTR = (5400 in-lb * 1in)/.372 in^4 = 14.5 Ksi
M.S. = margin of safety = F_allowable/f_actual - 1
M.S yield_OTR = 37 Ksi/14.5 Ksi - 1 = +1.55 (yield criteria is met - anything above +0.00 is OK)
Check for no failure at ultimate load
Ultimate f_bending = f_bending DLL * 1.5 = 14.5 * 1.5 = 21.8 Ksi
M.S. ult otr = 41 Ksi/21.8 Ksi = +.88 (ultimate criteria is met)
(note that for ductile materials that have been heat-treated, the ultimate stress check is usually the critical one, but with annealed 6061 the yield check is critical)
Lets check whether the OR loading is OK
f_b OR = 9000 in lb * 1/.372 = 24.2 Ksi Limit, 36.3 Ultimate
M.S. OR Lim = 37/24.2 - 1 = +.52 (Yield check is satidfied)
M.S OR Ult = 41/36.3 - 1 = +.13 (Ultimate check is satisfied)
So, for static loading, over-the-road or off-road, the strength requirement is met.
We're talking about aluminum here though, right? How about fatigue?
When aluminum is working hard enough there is damage being done with every load cycle. The higher the stress, the more damage is done with every cycle. If the stress is very high, you might only get a few cycles before failure; however, at low stress there is little or no damage being done. The key to a long fatigue life is to limit the operating stress to one low enough that you aren't doing significant damage when it is repeatedly loaded. For 6061-T6 aluminum the endurance limit is 14000 psi, which assumes: 500,000,000 cycles completely reversed stress (this assumes an stress ratio of -1 i.e. fully reversible). Because I g-loading, OTR or OR, is almost exactly in one direction our load does not fully reverse, and that makes a huge different. We can assume that our load gets applied, and then never goes below zero - that gives us a stress ratio of zero (non-reversing load).
Lets look at the fatigue endurance curves
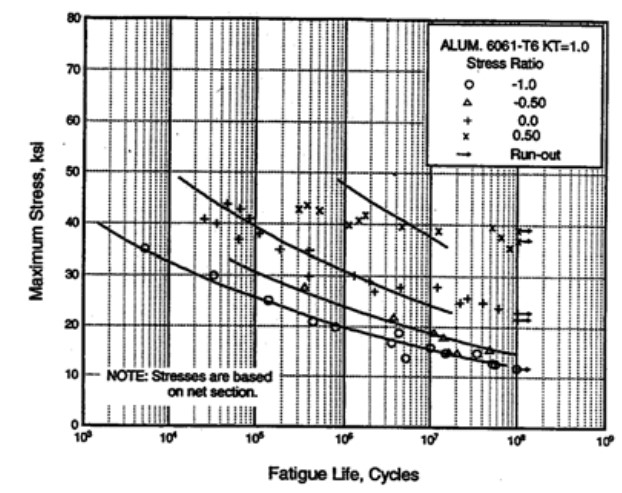
- 6061 s-n curve.jpg (88.15 KiB) Viewed 791 times
The plus symbol is the curve were looking at (stress ratio of zero) and the endurance limit is just a bit above 20 KSI for repeated loading for which stresses below that will result in an infinite life. So, we'll use that as our stress to stay under for Limit loading. This is a bit conservative and we are not realizing limit stress every time the frame is loaded; but, if we set the stress this low at limit load, then we should be way OK for fatigue. Note that this assumes that we haven introduced any holes or welds in a stress critical area.
Let's look at our limit stresses again:
fb OTR = 14.5 Ksi Limit (below 20 Ksi, so it looks like fatigue won't be a problem unless we screw up some design feature!)
fb OR = 24.2 Ksi Limit (this is above 20 KSI, so it doesn't meet the fatigue cut-off for a infinite life)
Therefore, so far, the 1x2x.062 rectangular section should work for the frame (we will do other checks to confirm) in the OTR case, but wouldn't be acceptable for off-roading.
So, what does this tell us? For a OTR design the aluminum .062 wall section should work fine, but for off-road this section wouldn't be recommended. The designer of an off-road version would then have a choice here: 1) use aluminum, but change the wall thickness to .12 in., 2) change the .062 wall aluminum section to 2x2, or 3) use a 1x2 .062 section made from steel, which would carry a smaller weight penalty compared to an aluminum section that now grows to the next size up and doesn't have the same fatigue considerations.
This concludes the initial check. More checks to follow.