Page 1 of 6
UltraLight Body Design

Posted:
Mon Mar 15, 2010 10:17 am
by schaney
How about a 60-70 lb body structure that's not made from cardboard or high tech carbon/honeycomb/epoxy composites?
If you've seen any of my posts in the past, Yes, we are talking about a softsided design. IMHO fabric base structures are a cost effective way to shave pound.
This is a shift to a fixed body design from my normal folding tent units. What I'm thinking is an easy to break down aluminum skeleton that would have a fabric skin. Here is a first pass at the skeleton and basic shape.
What do people think?
Will have a fabric skin on it shortly and am still working on frame approach.

Posted:
Mon Mar 15, 2010 2:07 pm
by Miriam C.

Posted:
Mon Mar 15, 2010 11:43 pm
by TheOtherSean
How about just riveting aluminum skin to it and making a lightweight pseudo-Airstream?


Posted:
Tue Mar 16, 2010 12:01 pm
by dwgriff1
I agree on the soft side idea.
Look at the skin and frame boats. Sturdy and extremely light.
Keep working and keep us up to date, and don't let any one rain on your parade.
dave

Posted:
Tue Mar 16, 2010 12:29 pm
by schaney
Yes a ultra-lightweight softsided, Teardrop like camper would be towable by a Sentra or any compact vehicle.
Sure you could skin it in aluminum but my design criteria of being cost effective would go out the window. What's an Airstream Bambi go for these days, $50,000+.

Posted:
Tue Mar 16, 2010 3:07 pm
by steve smoot
If a Bambi cost $50k, then I have lived in stuff that cost about $47K less...

Posted:
Tue Mar 16, 2010 5:55 pm
by Ageless
2010 Airstream Bambi $$52,601.00
Re: UltraLight Body Design

Posted:
Tue Mar 16, 2010 6:22 pm
by bobhenry
schaney wrote:How about a 60-70 lb body structure that's not made from cardboard or high tech carbon/honeycomb/epoxy composites?
If you've seen any of my posts in the past, Yes, we are talking about a softsided design. IMHO fabric base structures are a cost effective way to shave pound.
This is a shift to a fixed body design from my normal folding tent units. What I'm thinking is an easy to break down aluminum skeleton that would have a fabric skin. Here is a first pass at the skeleton and basic shape.
What do people think?
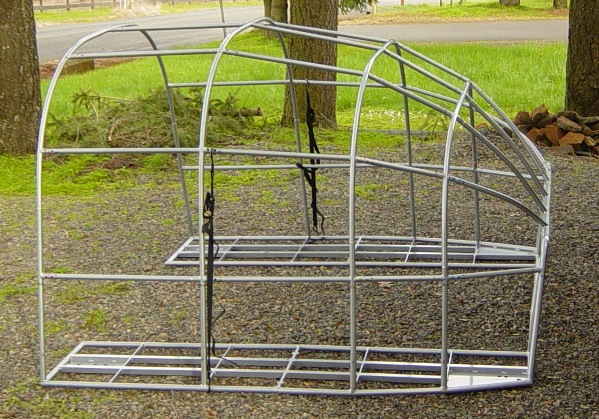
Will have a fabric skin on it shortly and am still working on frame approach.
Screams chicken wire and paper mache to me !
A good fiberglass shell over the paper mache and you are good to go.


Posted:
Tue Mar 16, 2010 6:33 pm
by RAYVILLIAN
How about heat shrunk dacron and epoxy like they do cloth airplane wings.
Gary

Posted:
Wed Mar 17, 2010 12:16 am
by TheOtherSean
Aluminum is expensive, but not that expensive. I figure you can skin a tiny travel trailer for several hundred dollars, maybe a couple thousand tops. It depends on local prices, gauge, etc. The cost of an Airstream isn't primarily the aluminum, its a combination of decent quality and brand name.

Posted:
Wed Mar 17, 2010 9:07 am
by dwgriff1
The problem, as was discussed on another thread, is that lightweight past a point does not really gain any advantage.
You still have friction of wheels and air and such. Weight is only a small part of the equation.
At least that is what the engineers told me.
dave

Posted:
Wed Mar 17, 2010 10:44 am
by schaney
I have thought about heat shruck dacron as a way to cover it. I believe a fabric skin has many more pros than cons. Light weight, easy of adding zippered doors / windows, easy of fabrication and cost effective repair /replacement to name a few.
Dave, for towind on a flat road, a trailer that does not extend past the profile of the tow vehicle, zero wind out and after you have gotten up to cruizing speed, I would agree. Now add acceleration, wind and hills into your equation. This is were you have to consider torque output of the tow vehicle when assessing diminishing return on pounds shaved. Sure a pickup with 300+ ft lb of torque is hardly affect by an extra 1000 lb behind it. But a compact vehicle with 100 ft lbs of torque is notable affected.

Posted:
Wed Mar 17, 2010 2:10 pm
by deepmud
I like it. Subscribed.

I think it would great for off-road, and for unusual shapes/designs.

Posted:
Wed Mar 17, 2010 9:53 pm
by dwgriff1
My rig weighs 580 dry. I pull it with an aging Chevy Cavalier. I get 22 mpg almost all the time pulling it.
I proposed, on another thread, that I could build one that would weigh 300 pounds and the consensus of the engineers was that it would make some difference pulling up a hill, but precious little otherwise.
Should I be enlightened and find an advantage, I'd make one that would be a combination of a piper cub and a Eskimo skin frame boat. Not unlike what you are thinking.
Since it would be so light, I'd use Andrew's Pico Light frame and running gear as well.
This boat inspires my thinking:
http://www.gaboats.com/boats/blackfly8.html
Keep us informed how it works, i am really intrigued by it all.
dave

Posted:
Thu Mar 18, 2010 10:45 am
by schaney
Deepmud, For off-road a narrower and short version would work nice.
Dave, I'm not up on the math but here is a real world way to wrap your mind around it. Take your wheelbarrow and walk around the yard with it, don't take much effort does it? Now push it up on incline, still not to hard to push but does take more effort. Now start adding weight in it, do the same walk around the yard and up an incline, the amount of effort necessary to move it has increased. The basic concept is, the greater the Mass, the great the force necessary to move it. The great the force applied translates into burning more fuel.
When looking at extra weight don't forget to also factor in affects on stopping, handling, or wear and tear.
With shaving pounds a big question is one of trade-offs. How long does it take for the gas mileage improvement (you should also factor in the above items) to offset the additional cost in building? In the case of a fabric on skin structure like this, I'm assuming I could offer a kit that would be more cost effective than building a traditional plywood Teardrop. So with this you would get a mileage and building cost savings. That just leaves the preference question of softsided verses hardsided camping trailers.