Okay, so one of the things I think I should start out with since I've got the majority of this project already complete is to give some lessons learned.
1) Building a trailer frame from scratch is not easy, though it can be done. You really need to get things exactly correct and have a big level surface. Also, when you heat steel, it warps. This turned up later on in that the back driver side corner of my trailer is roughly 1/4" warped downwards.
2) If you're building a trailer, have the axle on hand before you start, instead of finding out halfway through that the leadtime on the axle or some necessary part is 10 weeks.
3) Gloves, gloves, gloves. It's not that the glue is toxic really, but nobody is going to want you around them after you've gotten some polyurethane glue on your hands. That and it takes _forever_ to come off your hands.
3b) I don't want to ever see polyurethane / Gorilla glue ever again in my life.
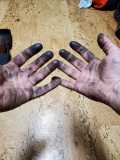
3c) Glues, epoxy, etc will all run and drip when you don't want them to.
4) Fiberglass sucks. No, it doesn't just suck, it *REALLY* sucks. I also don't want to ever see, smell, or use polyester fiberglass resin ever again in my life.
4a) On the same lines, applying resin to a vertical surface cleanly without having drips, runs, wrinkles, or other defects in your final appearance is nigh on impossible
4b) Finishing and smoothing fiberglass resin requires a wet sanding, and it is a lot of effort. And time. And sheets of sandpaper. And your sander isn't probably made to get wet. And then you get to do bondo work. You might as well just cover the entire thing in bondo to get a good smooth surface. Guh.
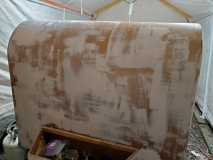
4c) This is why RV makers do plywood -> Foam -> plywood -> Aluminum laminate with simple trim on the corners and glue it together. It is significantly less labor intensive.
5) Tools. Quality tools can make or break a part of a build. A good example, I had a harbor freight oscillating tool. It was loud, unruly, had a godawful method for changing out blades/etc. After needing it a few times, I ditched it and got a real rockwell oscillating tool, with variable speed, came with nice blades, etc. Another godawful tool was a harbor freight wire wheel that I used for cleaning up welds. By the time I was done, there were no wires left on the wheel, my hands hurt, and my jeans were perforated (literally) with steel wires that had been flung at high velocity at me.
6) Be wary of using strong chemicals to stain or varnish the interior of your teardrop. I've had to wait for 80 degree sunny days to boil off the vapors from the Polyurethane clearcoat stain that I used on the interior of the teardrop.
7) Respirator! Get a full face, and use it. At least a half face with organic / VOC filter. The difference my lungs felt between using it and not was worlds of difference when doing epoxy work.
7a) Your house probably doesn't have a respirator. I suggest doing epoxy resin work in an outbuilding not attached to a house. Because the smell *will* get into your house.
8 ) I found on my first outing that a major necessity is a doormat. They're cheap enough off Amazon, and give you a place in the pine needles to step.
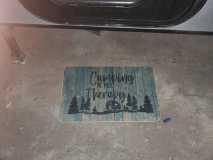
9) The project, or any specific task you think will be 'quick', will take you longer than you think.
9b) Corollary: The project is never finished.
10) Anything you design to have a perfect fit, won't.
11) Read tnttt for a long time before you go into a project. I thought I had read and lurked a bunch of threads, when I only scratched the surface. A good example, I would have done my hatch totally differently knowing what I know now.
Anyway, that's some of my thoughts on lessons learned during this build, so I'll call it that for the night and start editing some videos.