12.9.21
I've been working on the galley hatch (at least the design of it). Last March I had roughed it out in CAD but now that I'm getting to building it, I'm working out the finer points... adding taillights, locking mech, hatch underside puck lights, etc. into the CAD so I have a "go by" to work from.
One thing that bothered me and has been causing some headaches along the way is when I first built the floor base layer and installed it, there was a slight crown that developed in the middle. Wasn't much but enough to be annoying. So as things moved along I always had to work around that high point, fitting things to account for the curve. When I installed the rear roll pan I noticed a slight gap in the middle, that crown rearing its ugly head once again......right above the rear receiver hitch. So.... thought I'd document how I fixed it.
When I placed a straight edge along the span of the roll pan there was a high point in the middle (a gap)... wasn't much, maybe .100". I'll be sheathing it with aluminum so I'd not like that gap to transfer to the aluminum. By putting the straight edge up there to span the length of the roll pan I could insert a shim into the gap up to the point where the shim went tight and I could draw a line across the shim. That way I could measure the thickness of the shim and know how much I needed to shim out in the dip. I noticed the gap was larger at the top of the roll pan than the bottom, so moving the straight edge down to the bottom did same shim measuring to get the gap at the bottom.... if I remember correctly the gap went from about .100 at the top and about .060 at about midway down and then to zero (no gap) at the very end edge of the roll pan.
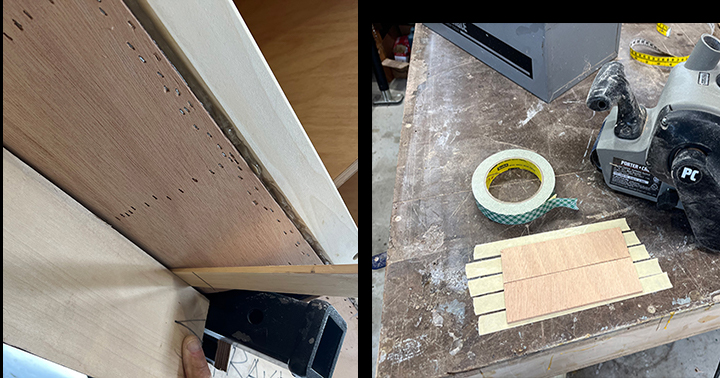
- shim.jpg (250.98 KiB) Viewed 962 times
I double backed 2 thin ply strips on the work table the correct length of the roll pan's curve with double sided tape (the model maker's friend) and using a belt sander, removed enough material to get the strips to taper from .100 to .060 (or there abouts).
I applied these two strips to both sides of the receiver hitch and placed the straight edge back across to check. The two ends of the roll pans and the two strips should all be on the same plane with no rocking from the straight edge.
You can see the two shim pieces on both sides of the hitch receiver and the gap which is what needed to be filled.
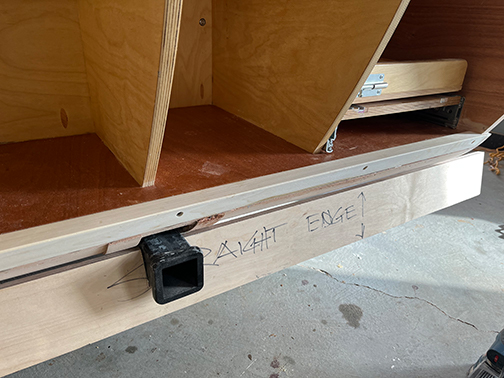
- straight edge.jpg (145.03 KiB) Viewed 962 times
Then applied bondo over the entire surface using the 2 installed shims as reference markers as to how high the bondo filler needed to go. From the strip(s) to the outside edge of the roll pans, the gap spots could be filled in. Of course there was a lot of sanding and refilling.... and kept checking with the straight edge. I also made a curved template using the profile from the side of the trailer to check the curve along the way.
It eventually worked all to being fairly straight and a fairly consistent curve. (unfortunately didn't grab a pict of the bondo surface).
Then installed a second layer of .156 okoume ply over the roll pan shape. I wound up gingerly sanding the bottom edge of the okoume where it wraps around to the bottom kind of tapering it into the curve of the profile so there's no errant edge sticking out..... it just sticks out .156 where it meets the galley floor, which is fine since that needed to build out.
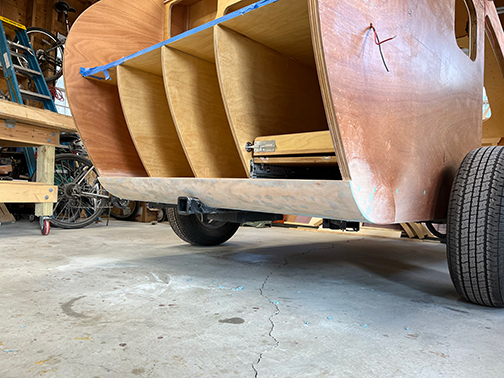
- new layer.jpg (186.4 KiB) Viewed 962 times
So.... a lot of "on the job" revising. "Cut to fit, paint to match" kind of thing.
John