Thank you guys. You keep me motivated, I really appreciate that. I wanted to share how the access doors completed with skins came out. Naturally due to organic shape of the doors, there was a little bit of twist to the frames. To preserve each individual twist for perfect door match I placed each frame on a solid flat surface (cast iron table saw top in my case) and fixed a little wedge with hot glue under a lifted corner to make all four corners steadily resting on the flat surface, but made sure that I carefully maintained the original, individual twist of every frame shape as they came out of the openings. Then I cut 3mm plywood to rough size, and glued it by pressing down to the frame with light duty staples. That immediately took care of the needed shape, just because it is based on a math of combined curvature of the door skin. Once you put staples, their geometry is individually fixed and due to the skin curvature, those doors are quite rigid. I made round corners by hole saw on a drill press and cut the little segmented shapes out on my table saw with a cross cut sled. Here is the dry fit result of doors before fiber glassing. I got the door build process photos accidentally deleted, but am trying to recover them and put them here if successful. Ordered 3 cam locks with same key, but not sure if I'll get them. If you have any suggestions for locks source I would appreciate you letting me know.
Nodrog, both left and right side compartments are intended to hold batteries and some distribution/fuse boxes. The battery trays have those lowered tabs that fit into these holes. I do not know if I want to completely seal these compartments, the batteries need ventilation. I may seal them only, but leave central compartment not sealed. The center (propane bottle compartment) has an opening in the floor at the bottom anyway so in case of any leaks, the propane will escape downwards.
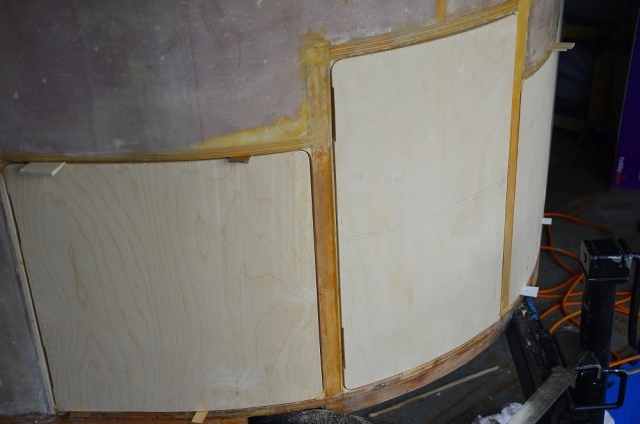