I have continued experimenting with the adhesives to see what holds the aluminum together well. Here is a closer look at the failed samples:
1 - peeled using only my hands. Some of the adhesive is left on both surfaces
2 - could pry somewhat with screwdriver under a free edge but would have had to get more leverage to actually peel it back.
3 - pried off with screwdriver. hardly any adhesive remains on the back of the sample and almost all is stuck to the anodized surface.
4 - could not pry back with a screwdriver. I think the biggest factor is that this is 0.063" thick compared to the rest that were 0.040" but there was also less of an exposed edge to get the screwdriver into.
What I've learned from this is 1) I'm glad I'm using the thicker 0.063" thick aluminum for the door overlay since it will be stiffer and harder to peel, 2) adhering the outer edge will make it more resistant to peel, 3) both the epoxy and Sika Universal work well on the anodized surface but don't work well on the bare aluminum. It seem that better prep of the bare aluminum surface will be important.
With more research I found out the surface needs cleaning, abrading, degreaser then a condition it with acetone or 99% isopropyl alcohol. There are other more complex methods with chemical etching but I would rather not get into the complexity and expense of those. I figured my next step would be to do a thorough prep using easily available materials. Using multiple samples of the same 0.063" thickness and prepared the same way, I figured I'd try to see if what I had available could work. I was out of acetone so I bought some and also saw another affordable high strength polyurethane product to try
http://www.homedepot.com/p/Loctite-PL-Premium-10-fl-oz-Advanced-Polyurethane-Construction-Adhesive-1417170/202192562 I sanded all surfaces with 220 sandpaper, cleaned it with citrus degreaser (normally used on my bike chain) and conditioned them with acetone and let it evaporate off for 6 samples and another scrap of the honeycomb panel.
1 & 2: Loctite 2-part epoxy
3 & 4: Sika Universal polyurethane
5 & 6: Loctite 8X polyurethane
The surface area of each one was similar (although slightly different) and I left an overhang similar to what the door skin will have so I can do a peel test later. Here is the initial setup from Wednesday night:
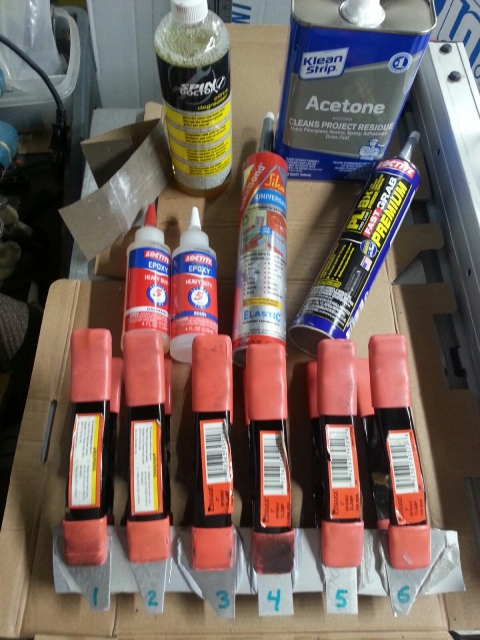
Thursday evening I took off the clamps to check the holding power of each one:
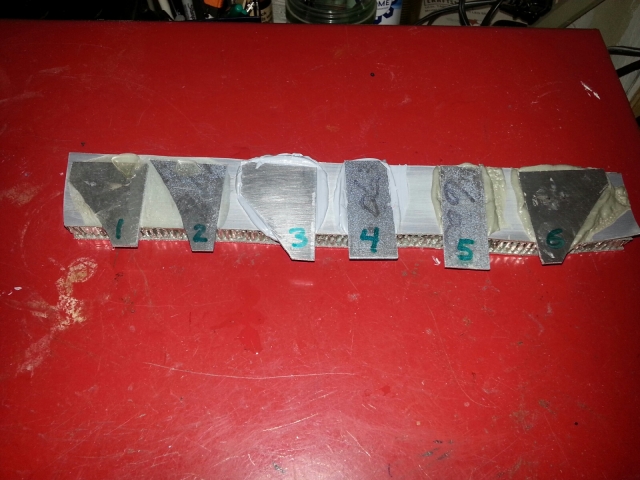
I tried peeling each one by holding the sample set down on a table with my left hand and prying as follows:
Peel test with just right hand: Samples 5 and 6 readily peeled off but samples 1 through 4 held strong. Most adhesive remained on anodized surface but some remained on the bare samples.
Peel test using pliers for better grip and leverage: Samples 1 & 2 popped off with moderately high force. Back of bare aluminum samples were clean with no visible epoxy remaining, all epoxy remained on anodized surface.
Samples 3 & 4 held with pliers test with at least as much force was applied to pop off samples 1 & 2 but I felt a very slight give on sample 4 - it might have started to peel if I were to apply much more force. I stopped there so I could retest them again later since the label on the Sika product says it can take 5-8 days to fully cure so there probably more strength to come.
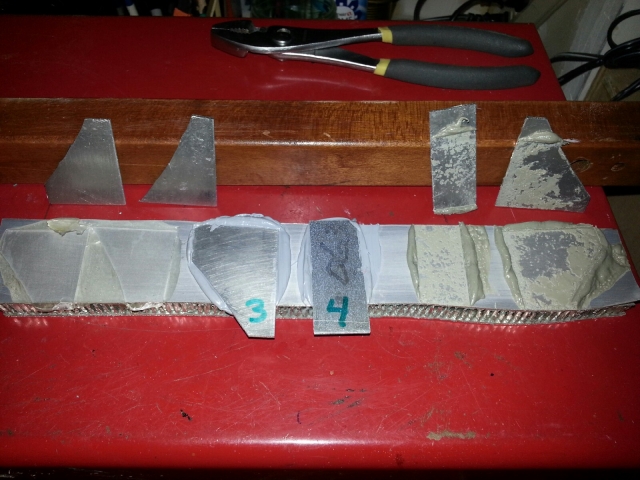
If I had to make a decision right now I think I can make the Sika Universal work with good surface prep and making sure the adhesive flows out to the edge so that it is difficult to get a peel starting. I'll see how samples 3 & 4 are doing this weekend after curing longer. In case the completed door starts to peel in the future my fallback plan can be to include just a few rivets in the door away from other fasteners that will hold the hinges, latches, and trim to the door. I'll think more about it but will want to get back to actual assembly of the trailer soon....
