A little background...
I first became interested in teardrop trailers over four years ago when I saw a teardrop thread on a car entusiasts' message board forum...
Since I'm a fan of motorsports high-performance efficiency, simply awestruck by the teamwork and progress made over the years in the incredible world of aerospace and having grown up in the southern California region it is only natural for me to attempt to name my teardrop project along the lines of aviation high performance.
Most of the difficult, dangerous (and often deadly) work of military flight test took place in and above southern California's high Mojave desert, north of Los Angeles in the vicinity of Rogers' Dry Lake near the very small town of Muroc. The name Muroc has become synonymous with not only military flight testing but hotrodding too, as it was on "Muroc" dry lake (Rogers') that the first automotive speed trials occured beginning in the 1920s...
Granted, we're all here on T&TTT because, to put it in the words of the Illustrious and Inimitable Steve Cox, we're "dreaming of little trailers"... and while I do realize that these are ONLY camping trailers... and while I would like to build with traditional materials consisting of mild steel and qualtiy plywood, some of the cabin's interior structural detail will have an aviation flavor and the chassis will be built in an unorthodox fashion in an attempt to minimize weight, retain some strength and be a lttle different than the usual...

The teardrop cabin profile has been influenced mostly by W.A. Harper's Quik-N-Easy teadrop, Grant Whipp's Lil Bears and the Cub/Modernaire. (Thanks go to Dave/DMcCam who very kindly offered the use of his 9' Atma Travelear profile design...)
The chassis design was influenced by Harper's Quik-N-Easy and Andrew/angib's Ultralight chassis designs...

After hacking out a few teardrop profiles with pencil and paper I've come up with an almost-decent profile, and with the help of my friend Rocco, we got the profile drawing into a photoshop'd pic of my tow vehicle... a 2.3-litre-engined, big-braked 2003 Ford Focus ZX3.
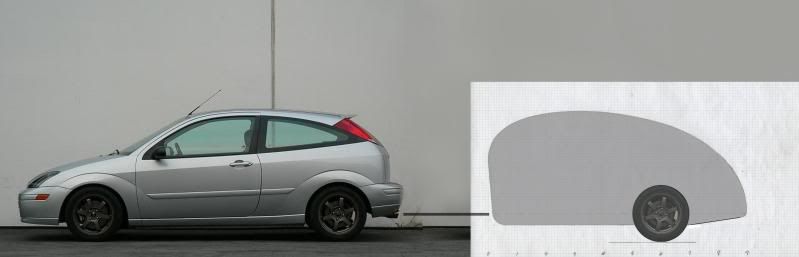
Trailer wheels will be different, and the profile's underside rear angle will be modified...
The car has a (North American market) tow capacity of 1200 lbs creating a fully-loaded trailer projected weight goal of no more than 1100 lbs (preferably 1000)... 1100 lbs to include full-sized steel wheels and 205/50-16 tires, a 71-lb marine AGM 100 ah battery, 50-something-lb 12V refrigerator, some cast iron cookware and a few Coleman lanterns...
We have our work cut out for us to minimize what we might carry in the form of camping luxuries above and beyond what I have posted above...

First thing was to get a hitch onto the car and get most of the material to wire it for trailer lighting...

Next, the trailer chassis' suspension arrived. I'll be using a pair of UFC America Flexiride half axles... together as one axle they are rated for 1400 lbs.
When choosing a rubber torsion axle, it is recommended to consider the maximum load/maximum trailer weight, then multiply by 125%...
In this case the maximum load will be 1100 lbs, 125% of which is 1375 lbs... about as close as we can get w/ the Flexiride offerings.
Although I was reluctant to post pictures of this chassis design until it was actually welded together, it was a recent post in a Trailer and Chassis Secrets thread that has prompted the release of this now de-classified material...

Here's the foundation of the T (Teardrop Camper) - 49 (4' wide x 9' long) Spirit of Muroc...
The Flexiride half axles will be placed as high within the chassis framework as is practical and bolted to these 1/4 inch steel plates... These mounting plates will be welded flush to the top surface of the dual crossmember's 2 X 2-inch 14 guage mild steel tubing. The additional 1 X 2 is also 14 ga mild steel.
I've been told that this is a tricky configuration, welding-wise. I may have to make some brackets to be welded the opposite (bottom) side of the 2 X tubing - but which will clear the torsion half axle boxes - to minimize warp.

A hearty thank you! to Anton and his boss Dan for letting me spend time cutting steel in their shop, and to Chris Considine at CXC Simulations who has also given me some room for the chassis layout but especially for grabbing the pencil drawing of my chassis design and putting it into a CAD printout for dimensions and angles to cut.
Progress will be slow, but I'll post updates as they happen.
Thanks for looking!
