Okay, let’s get caught up!
I’ve lost track of which day was which, but here is a photo dump!
The fourth coat on the curb side wall inner and cabin side of the bulkhead came out well enough. I can still find the areas where I broke thru to the gummy stuff while sanding, if I look very critically, but they don’t jump out horribly and should be subdued by the mattress, and shadows from the cabinets.
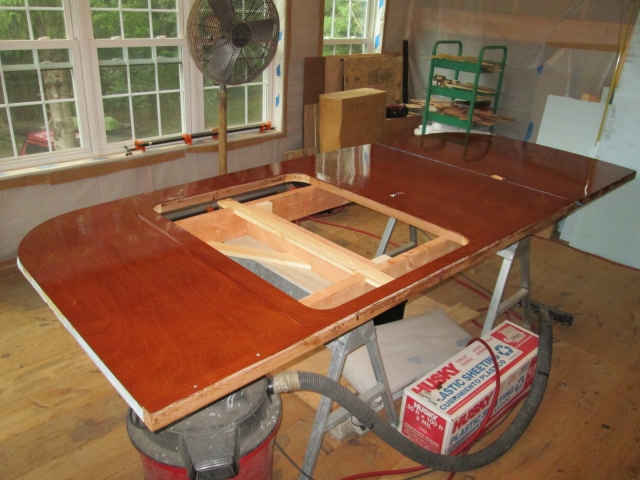
Here is a generally good spot ahead of the door.
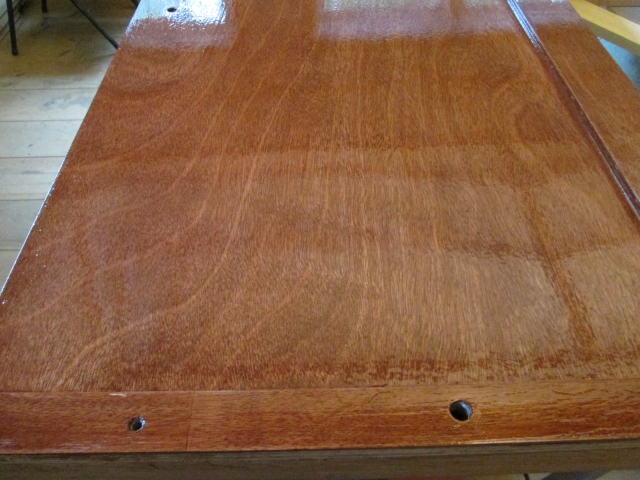
Here you can see some of the typical little pin holes, and the slightly mottled looking area that was depressed after sanding out a gummy area.
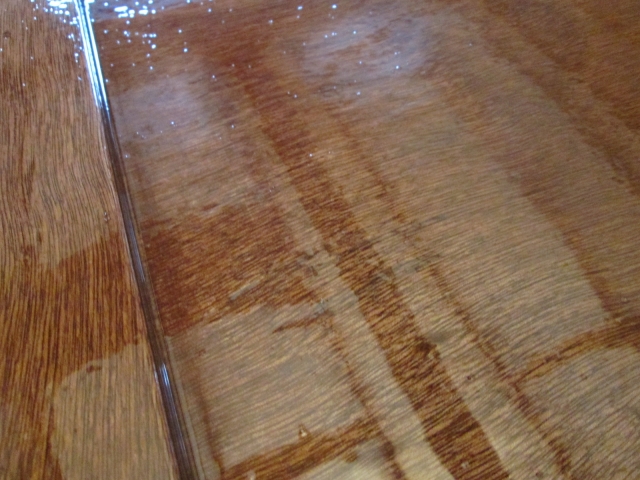
Should be covered by the mattress and linens, but I would like to perfect my skills to avoid such issues in the future. Need to put it on thinner, wait longer and use more coats. Consider using standard build product and/or thinning more.
Here is the bulkhead with some orange peel (visible at this angle) and a few of the sanding gouges in the previous coat of poly just barely visible.
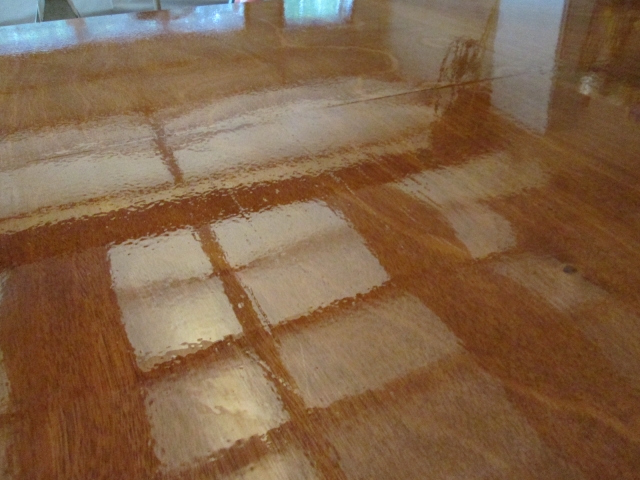
Gouges are much less visible in this shot, and the orange peel isn’t so bad either.
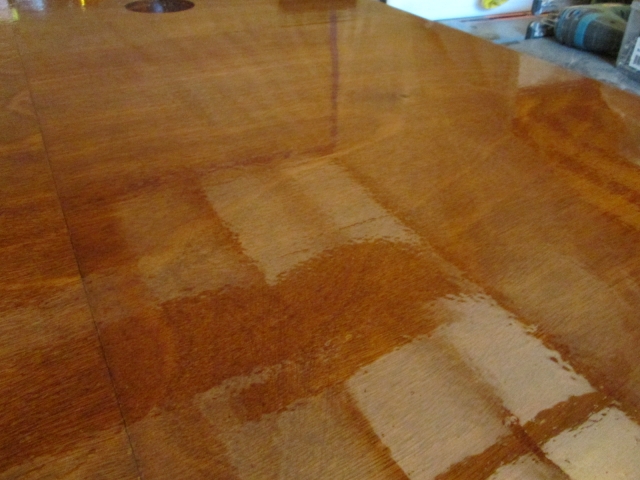
To avoid having the floor and wall finishes resting against each other or something else until they were truly hard, I put a few wedges of scrap maple under the wheels of the panel cart and slid the wall in behind.
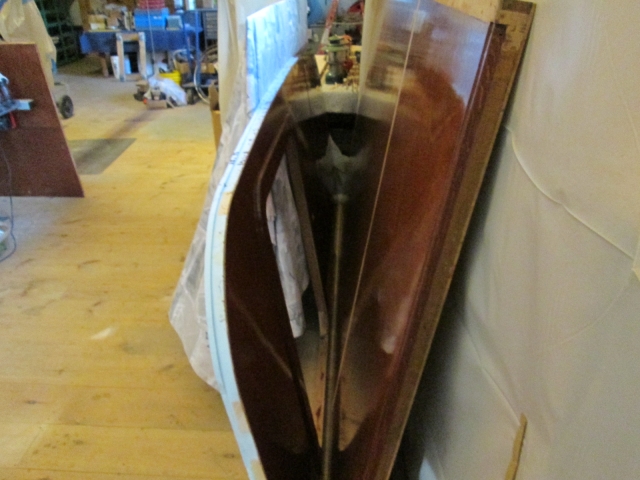
Shuffled parts, and before putting the stained side up, I ran the 1/8 inch radius bit around three sides of the door opening. The sill, being sloped meant that the bottom bearing would not allow the bit to cut the inner edge of the sill, so I just hit that with the small block and some sandpaper (no pic). Anyway, here is the street side inner wall ready for poly.
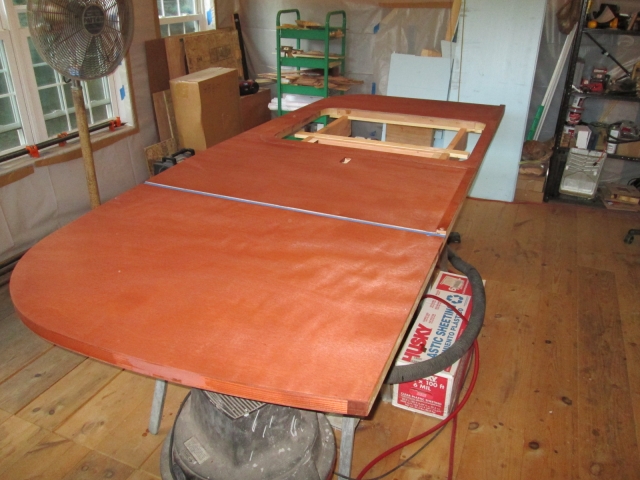
In the meantime I spent a bunch of time scraping excess poly and drips from the unmasked edges and rabbet areas of the bulkhead and curb side wall dado.
I guess that gets us thru to Saturday night when I picked up some rosin paper on the way home.
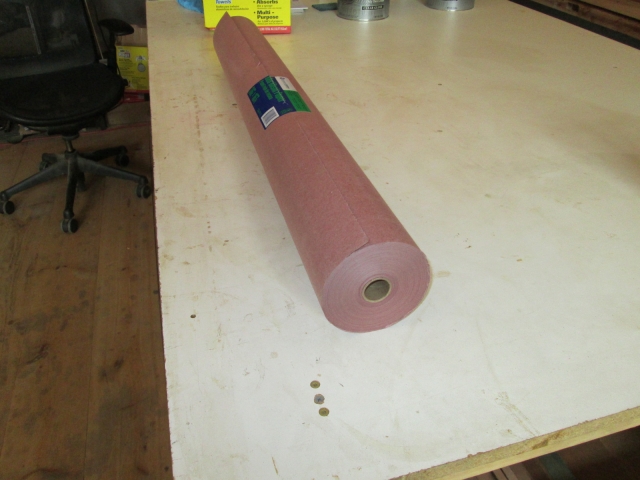
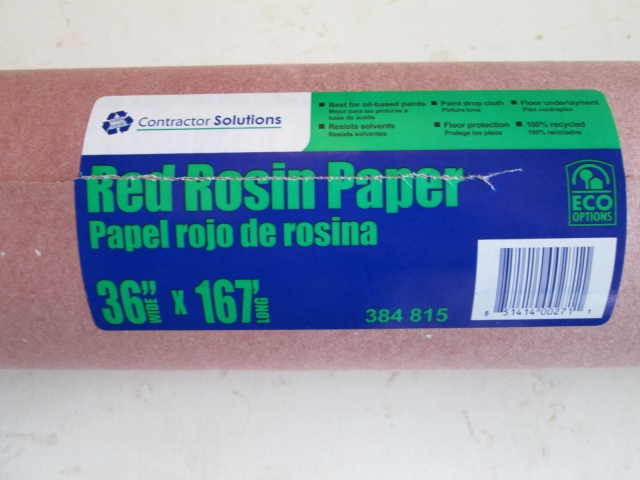
I have plenty of work to do fitting and joining these shiny parts together and I want to minimize the risk of damage to the finish during the following phases, so I will mask with the rosin paper. It is supposed to be good when used with oil based finishes.
Here I have almost completed masking off the door; just the door latch area left to do.
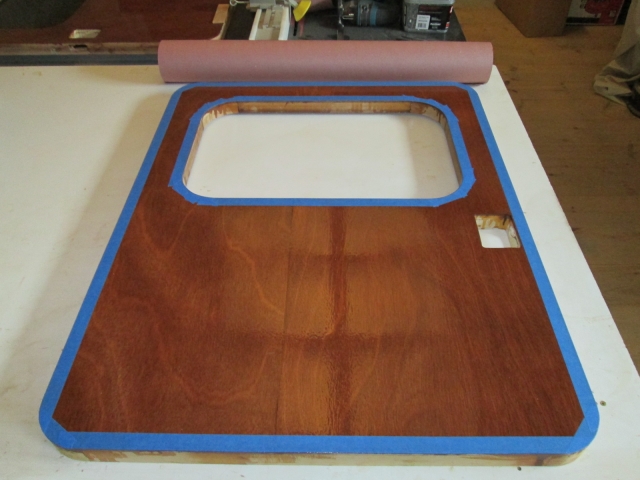
Next I rolled out some of the paper, offset under the door on two sides, and trimmed with the razor knife by following the other two sides. Then traced the window and latch openings, and trimmed those outside the line so that they could be taped to the edge masking as well.
Here is the door with the rosin paper all taped down.

Other door was done the same way.
Bulkhead was done similarly.
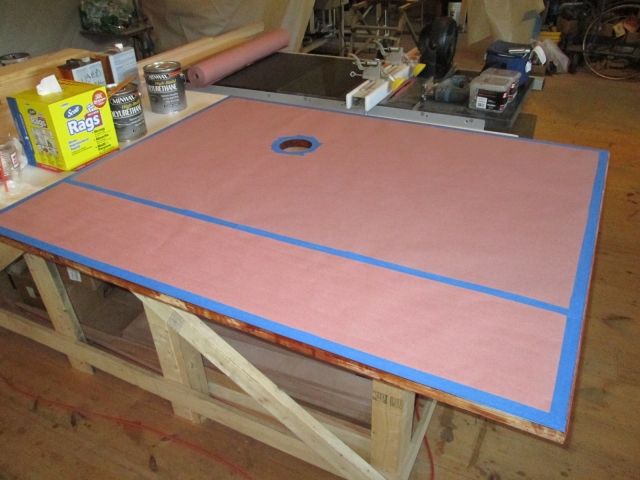
Meanwhile still scraping excess poly from the edges.
My plan from the beginning has been to erect the walls and bulkhead and then hand plane the top of the bulkhead to match the shape of the ceiling (520 inch radius in profile). However, I had second thoughts that it might be better to make an angled pass across the top of the bulkhead on the table saw to get it close.
So I did a trial fit of the bulkhead to wall, with some difficulty positioning it gingerly by myself… didn’t want to drop into the dado slot. Note the quick clamps used as outrigger supports to keep it from flopping down.
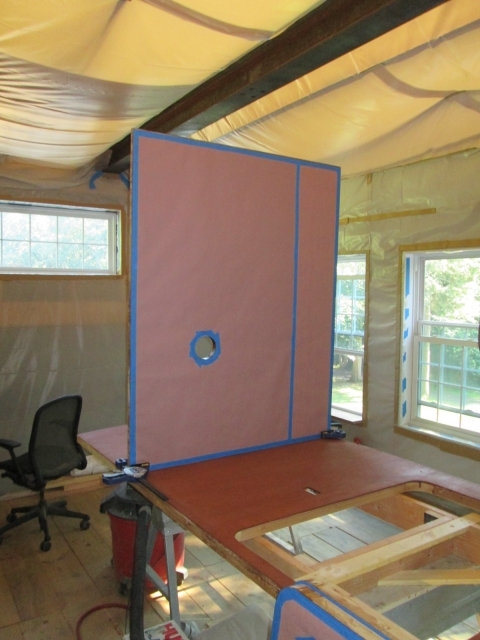
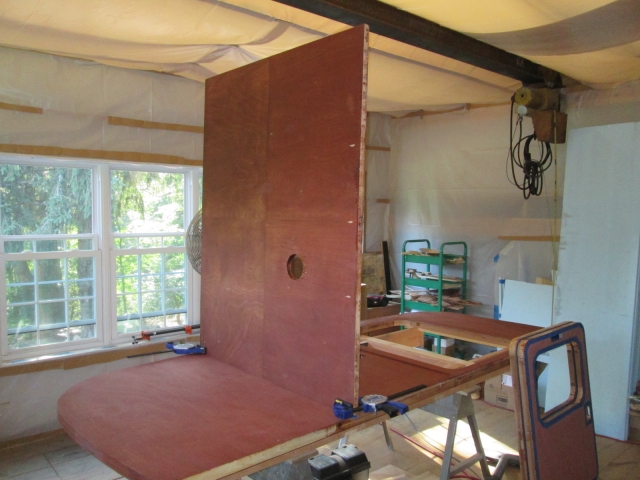
It turns out that the trim job needed is so slight that it’s not worth risking screwing up with the saw. Just a few quick passes with the hand plane once installed and it will be good.
That decided I used the scrapper to lightly remove some poly drips that had worked their way thru the fan hole and along the top and bottom edges, trying to avoid lumps in the galley side finish.
That made a few barely noticeable scratches down thru the stain, so I touched those areas with a dab more stain and set the bulkhead aside.
Next I filled all of the screw holes and minor divots in the door frame wood.

The screw holes were from the clamp method I used during glue up, and from attaching the router jigs for the window recesses and door latches.
Next I rounded over the door outer frame edges to accommodate the canvas wrapping over the corners. Used the same little outrigger shoe to help stabilize the router.
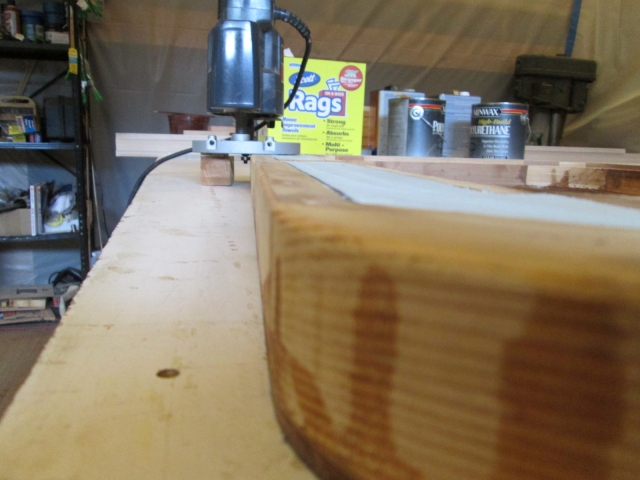
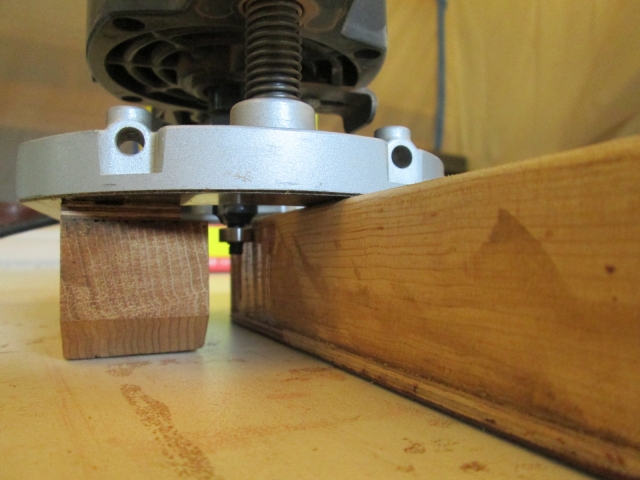
The shoe has one drywall screw that just acts like a locating pin, and the other uses a small scrap of 5 mm ply as a washer. Makes change overs quicker and easier than having two screws with washers.
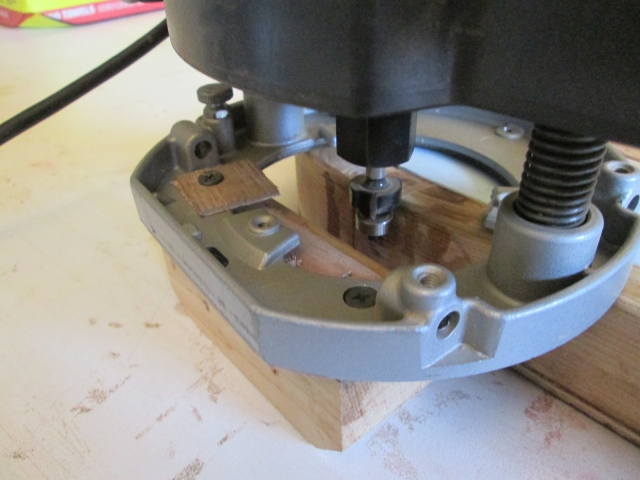
I just touched that gentle with the small block and some sandpaper to remove any tool marks.
That’s about 2 hrs each Wed., Thur. and Fri. and another 5 hrs today before hitting the proverbial wall.
Tomorrow (Sunday) I plan to spackle the outsides of the doors and lay the first coat of poly on the street side wall and galley side of the bulkhead.