My laptop is giving me some trouble, so I will try to keep this concise... as if!
Mostly just catching up on some pics and today's work.
The dismount, folding up the metal saw horse legs and setting the work frame down so the cabin is at a better work height.
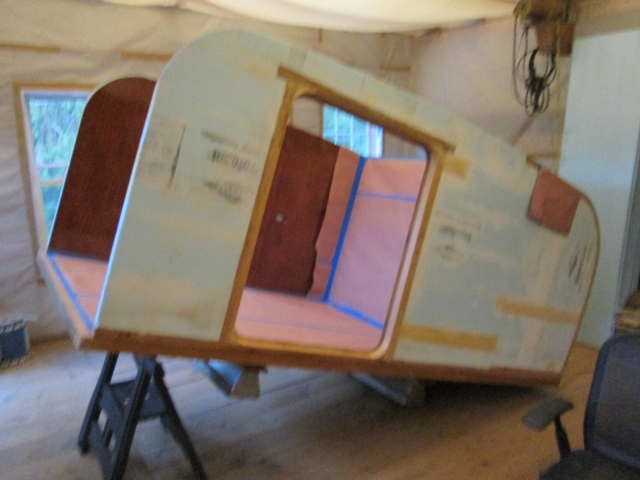

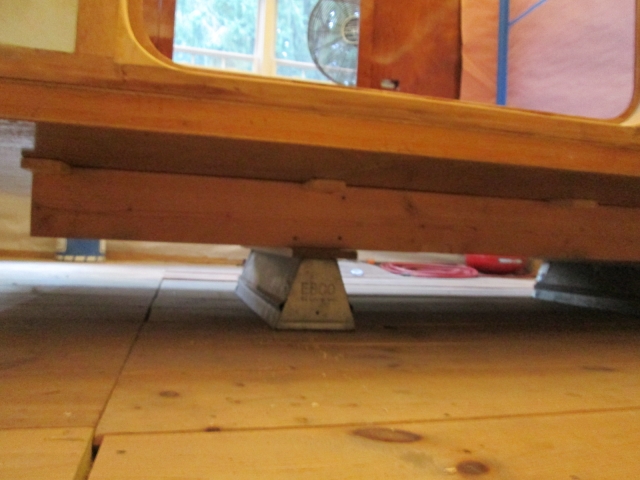
Looking down on the street side bulkhead joint (wall along the bottom, bulkhead in the middle). Note the blue tape pinched in the corner lap on the cabin side (left in pic).
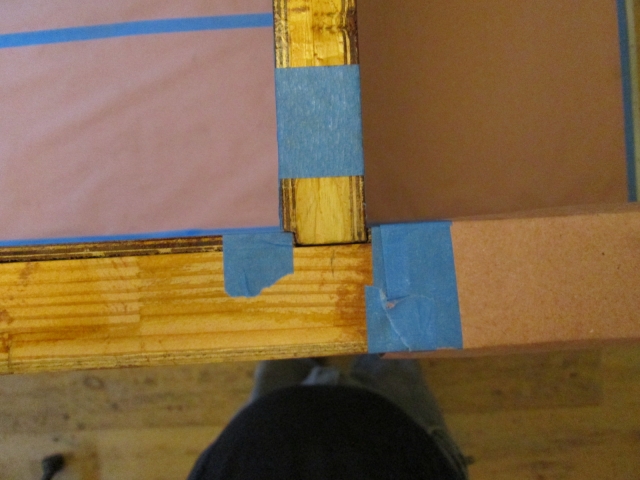
This is standing in the same location looking along the top of the bulkhead with the street side wall in the foreground. You can see how the front of the bulkhead is about 1/16 higher than the wall, and the rear is higher still due to the curve of the roof/ceiling. The front of the bulkhead ran down to flush on the curb side.
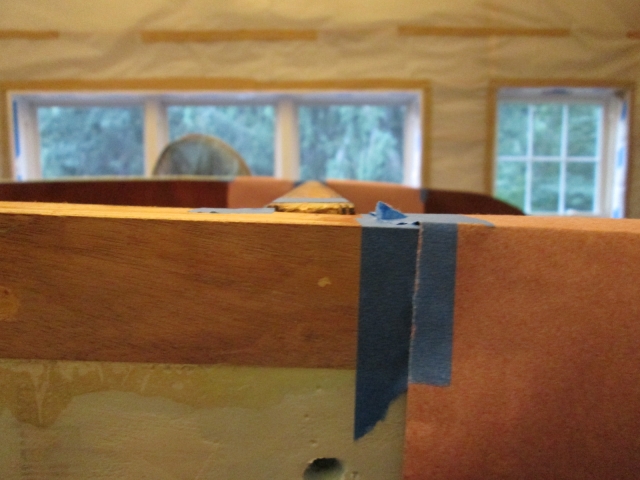
This is looking down on the curb side joint between the bulkhead and wall. Note that I managed to keep the tape out of the front of the joint (right side in pic) on this side.
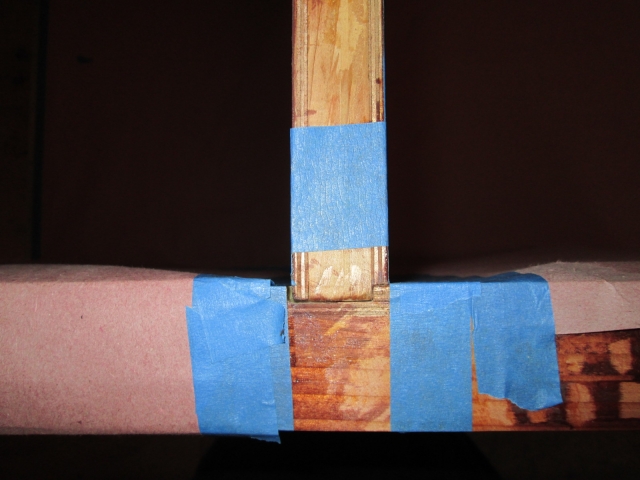
A little edge glue fixing.
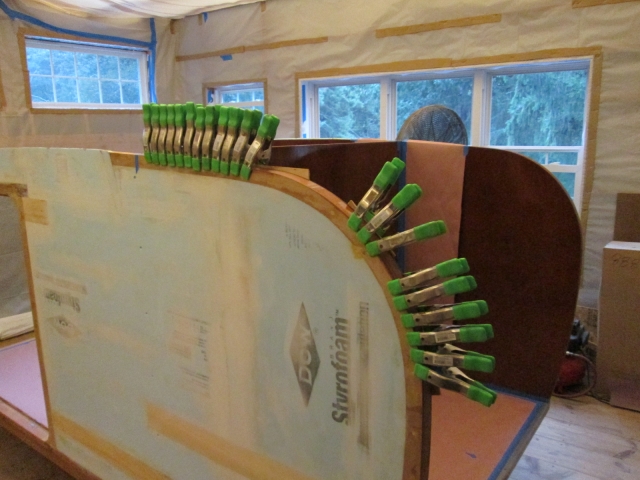
Made some notes on the wiring diagram.
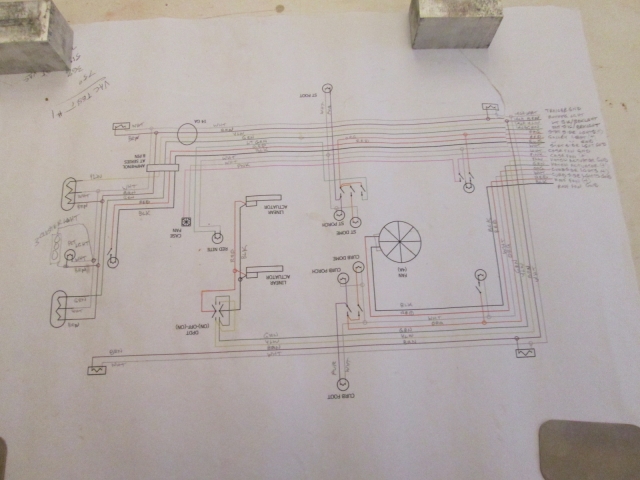
Placed some scrap pieces of plywood on the floor in the cabin and galley so that I can walk around without fear of damaging the relatively thin top skins.
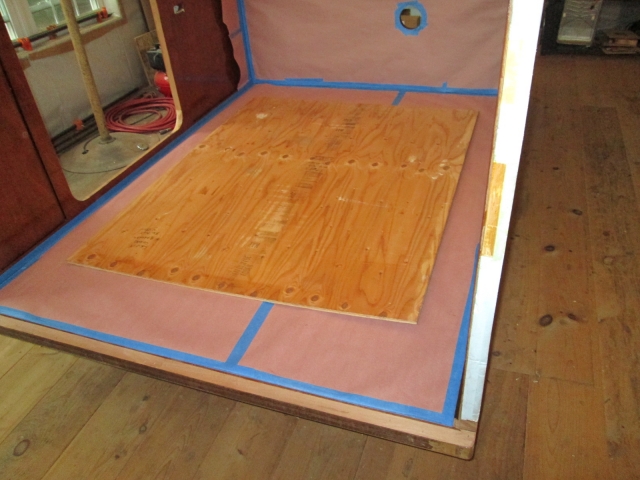
Brought a good step stool from home; a lot easier to maneuver and use than Karl's 6 ft ladder. All that I need for now.
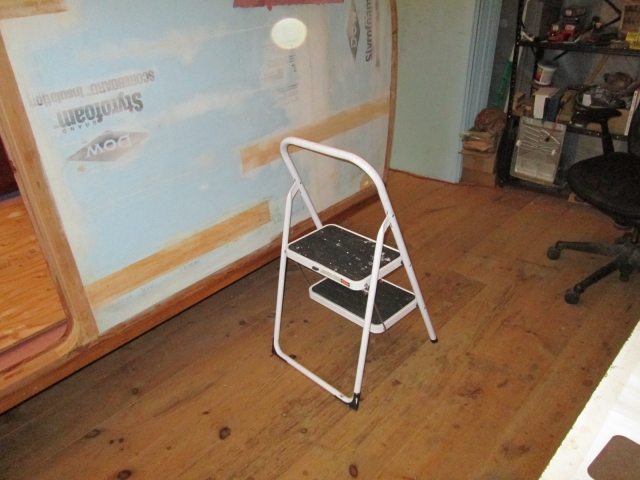
Used the alum. straight edge clamped across the tops of the wall in front of and behind the bulkhead. Cut thru the blue tape and poly with a razor knife then pulled the little whisper of tape off the top.
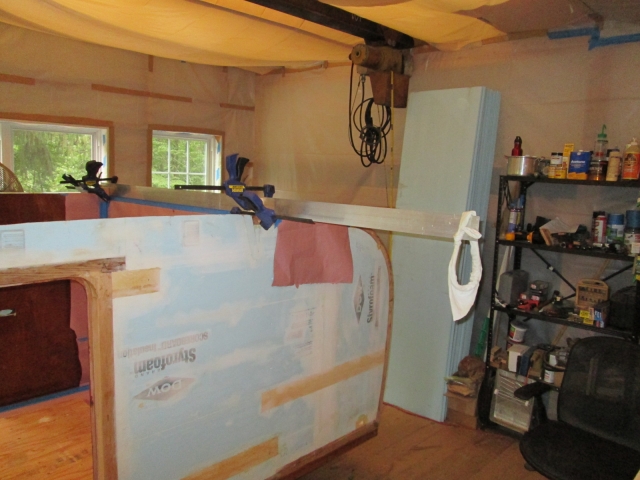
The white rag was to help me remember not to walk face first into the extra part of the straight edge sticking out. Worked most of the time.
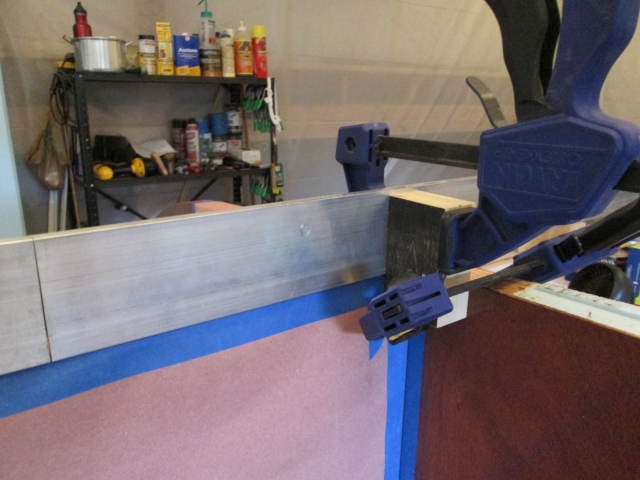
Next I used the bigger Buck plane and worked the top of the bulkhead down to the lines, front and rear. It worked good and easy on the soft cedar until I hit a couple of staples! The blade was only nicked minimally (I caught it pretty quickly), and I shouldn't have much work to hone the blade back.
Here is the result.
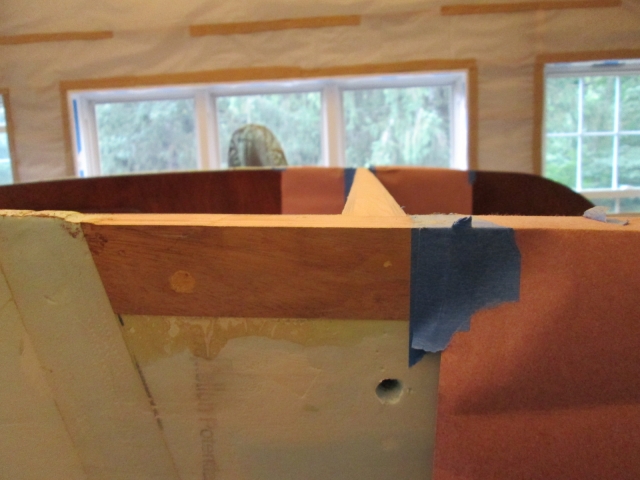
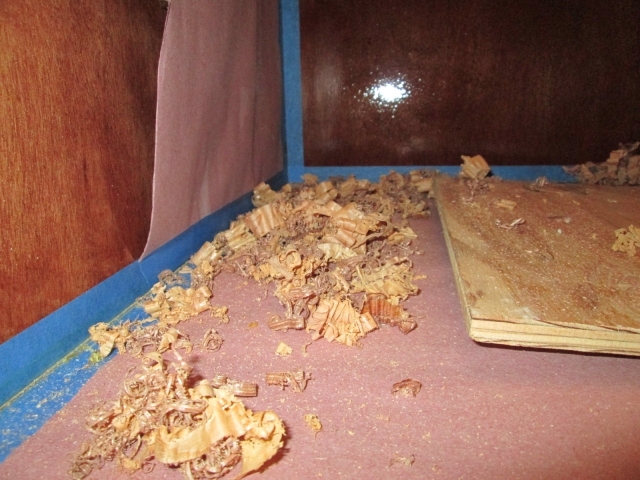
Added another sheet to the drawing showing the exact locations of the ends of the cabinet and shelf frames, the ledgers at the "backs" of the cabinet and shelf floors, as well as the roof spars and butt joints in the ceiling skins.
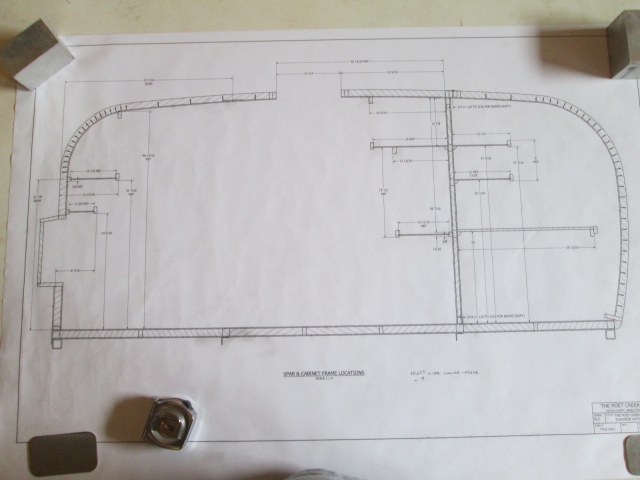
Today I milled up a bunch of maple trim and the ledger stock for the backs of the cabinet and shelf floors. Same technique as before: round over the corners on one of the narrow edges of a 1x2; groove between the rounded corners on the table saw; then rip the two corners off on the table saw. Here's the router set-up.
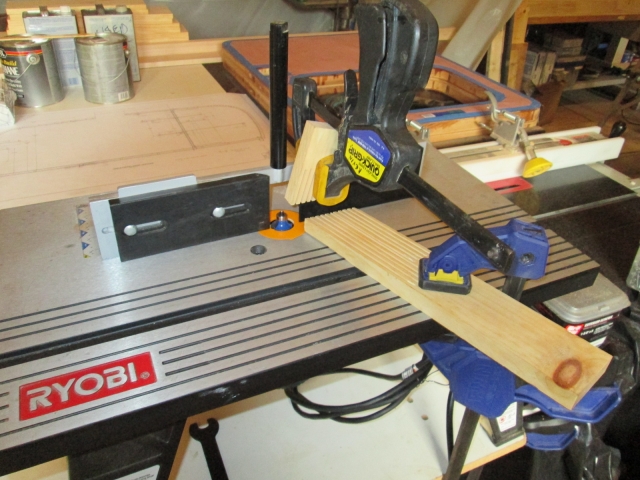
After I clamped the router table to the work/out feed table I had to cock the fence so that it was aiming into the doorway of the camper, else wise the 9 ft stock would run into the foam walls.
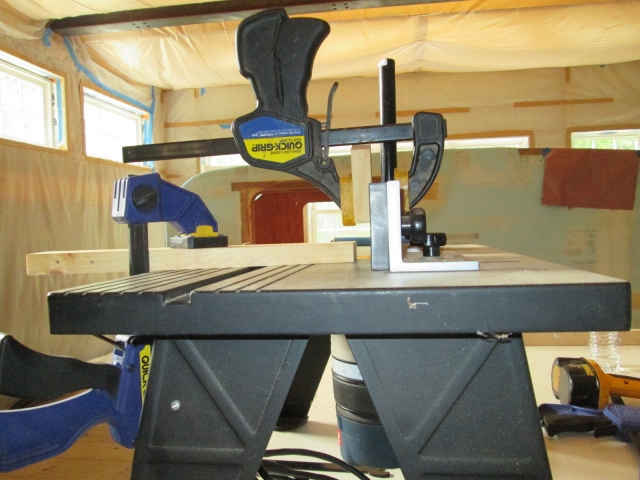
Borrowed this extended roller stand from Karl to match the height of the router table up on the bench. (Although I wiped the shop grime off of the roller, I still covered it with blue tape so that it would not soil the wood.)
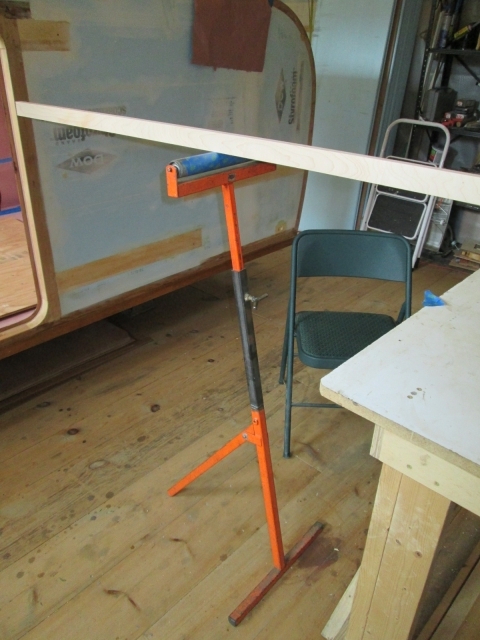
I needed 4 lengths for the grooved ledgers, but probably won't need twice that many piece of the quarter round, especially since I already had 2 lengths from when I made the little front rib blanks. On the other hand, the ledger blanks are only 15/16 tall, so rather than have a bunch of drop strips that would be too small to run thru the saw later, I just made a bunch extra of the qtr rnd. I might want it in the end.
Here's the start of it.
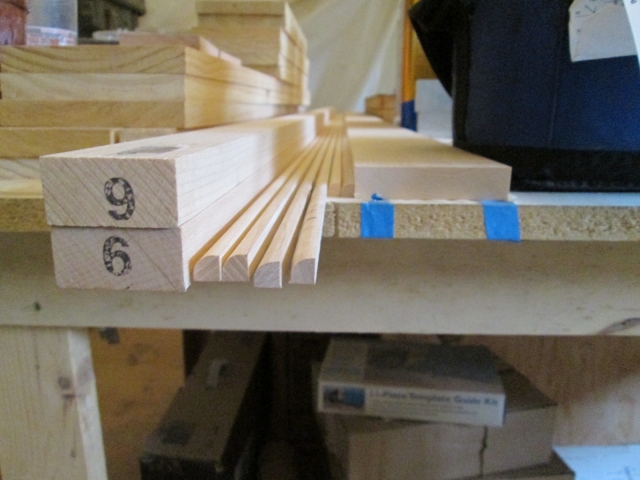
It is actually 5/16 on a side with 1/4 round over.
After ripping off those, one more thin little rip in the table saw yielded the blanks for the ledgers.
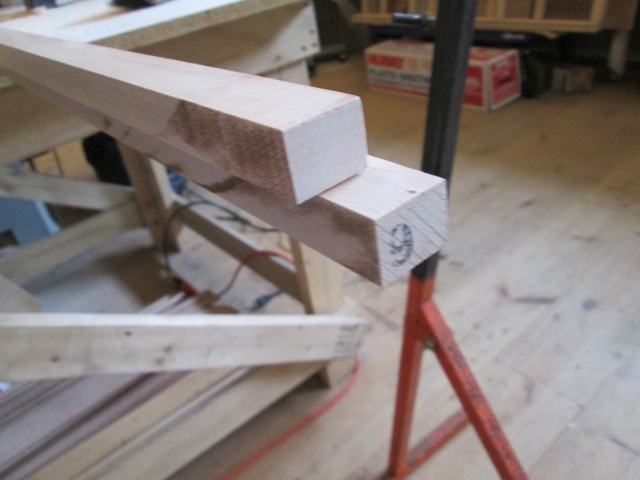
Next I ran the slots for the shelf and floor bottoms.
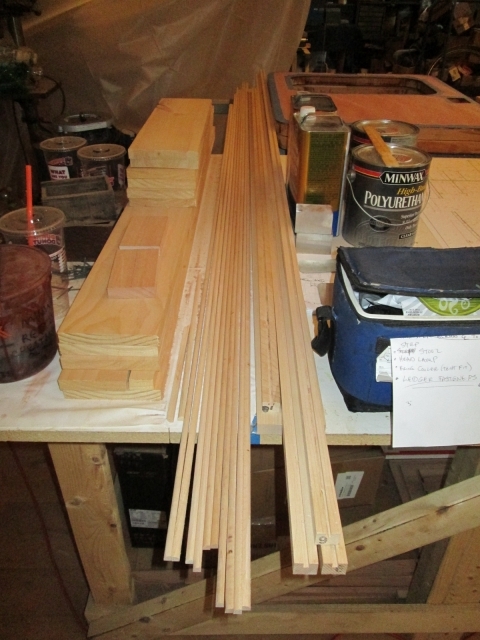
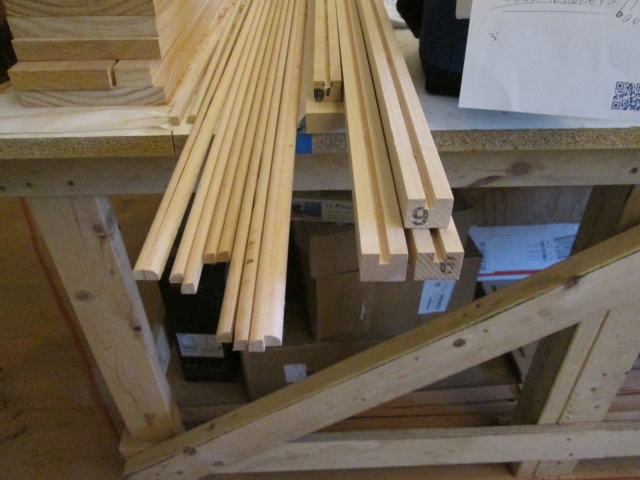
Test fitting the 5mm.
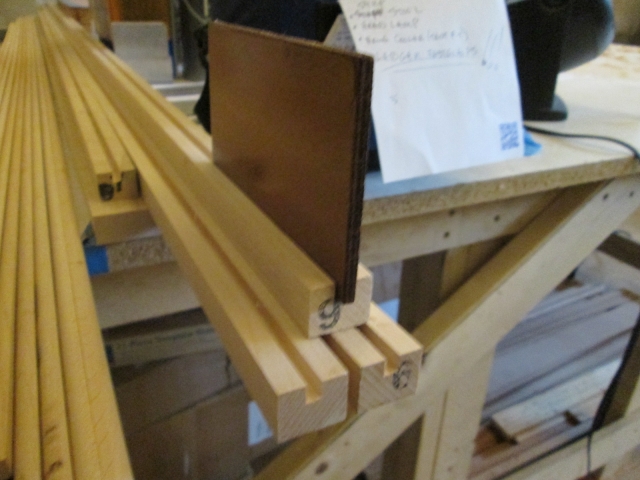
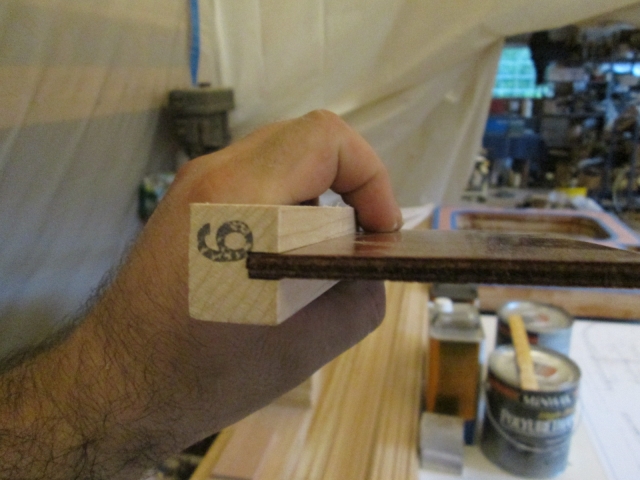
After a pretty full day, it was time for some cleanup, including digging out the bottom of the table saw cabinet.
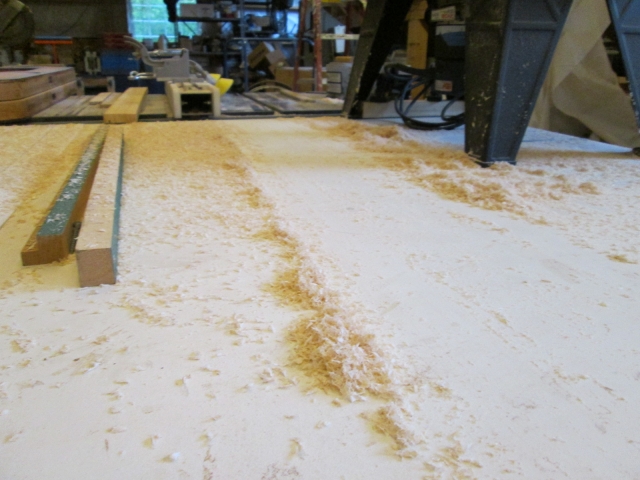
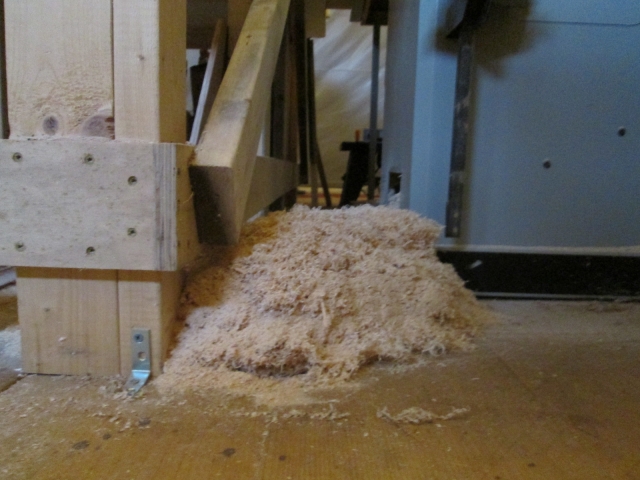
That was only about 1/3 of what I eventually pulled out!!!
And it was time to quit for the day... 80/ct humidity.