Never really got warm at the shop today. Ran both the turd and the 228E. Karl had not run the woodstove yesterday, and only started it today when I arrived. Went from 31 deg F to 43 or so in the loft.
Also, some news that could affect the rest of the build; Ben has a new place and will be taking his table saw and work table (and, I assume, the miter table) within the next couple weeks. We will have to move TPCE off of the floor hatch in order to lower these down thru, and another piece of Karl’s equipment that is currently stored under the eaves.
I am certainly grateful for having been able to use these for the build to date, so no complaints. I will need to build a new work table. We will see about the table saw. The one at work is… um, pretty inaccurate. Larry generally keeps his portable unit at work (a decent Rigid with folding cart), and that might suit what I have left to do. The biggest thing I can think of right now is the lower edge of the hatch that needs to be ripped at a specific angle, and I’m sure that I will have some more shelf ledgers to rip and groove. I may have to buy a basic “job site” saw to get through the rest of the build.
Anyway, I worked on switch plate details again today. Punched the replacement switch blank out.
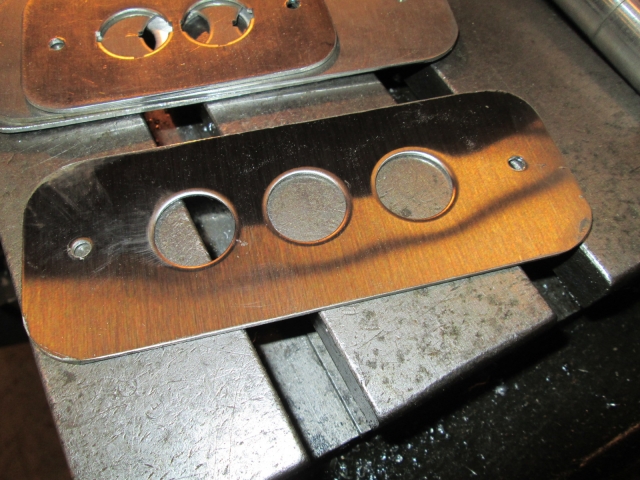
At first I started to drill the screw holes out; had one drift off location a tad (I think it was because I tried to leave the protective film on “the good side” and that let the bit wander some). Then I switched to the 1/8 inch punch in the iron worker, thought I recentered a fresh prick punch mark in the started hole. But we’ll get to that a little later. As you can see in the previous pic, I also punched out the 3/4 inch holes for the switches.
On Karl’s advice (invaluable!) I was able to flatten the warping from the punching operation simply by laying them on a rag on a piece of wood and tapping them with a small soft headed mallet.
Next I set them up in the mill with a counter sinking bit, setting the depth stop to suit the No. 6 flat head screws. You can see the countersunk hole on the right and the screw test fit on the left.
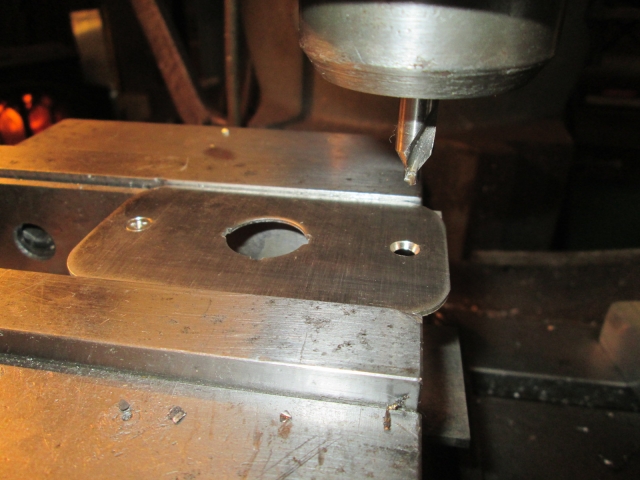
Here is a close up shot of the screw set just below flush.
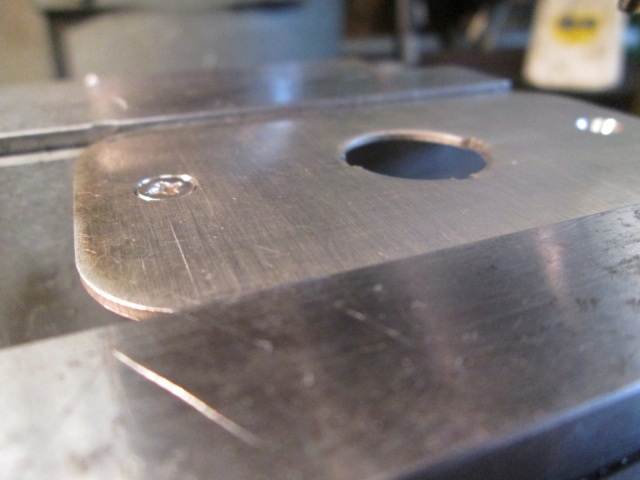
Some deburring, a little buffing of the grain, and a progress pic.
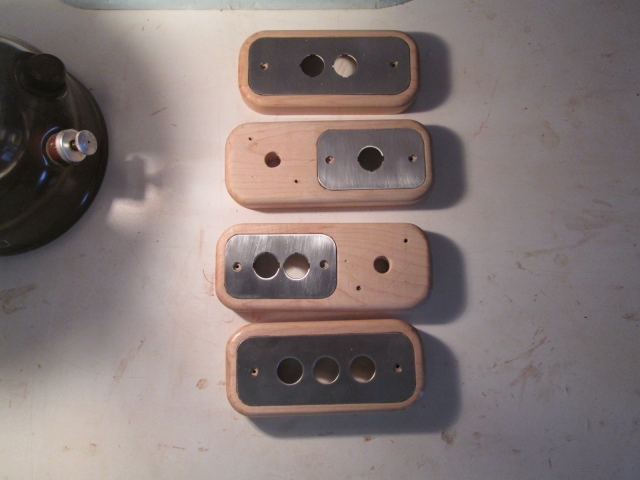
I spent a little time making an adjustment to one of the pillow light blocks because the plate didn’t want to sit down as well as it did before stain. Not sure if I had missed this or if something had changed.
<edit to add> Then I filed the switch key slots in the new switch plate. <end edit>
Next I found that one of the screw holes in the replacement switch plate was not centered on the previously drilled screw holes, shown here on the left after fitting the switches.
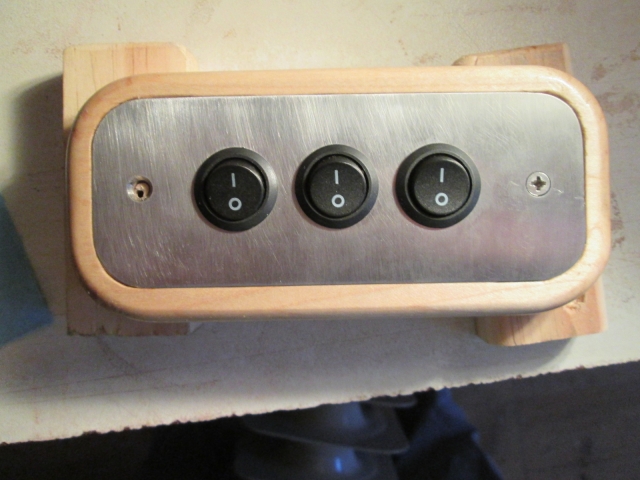
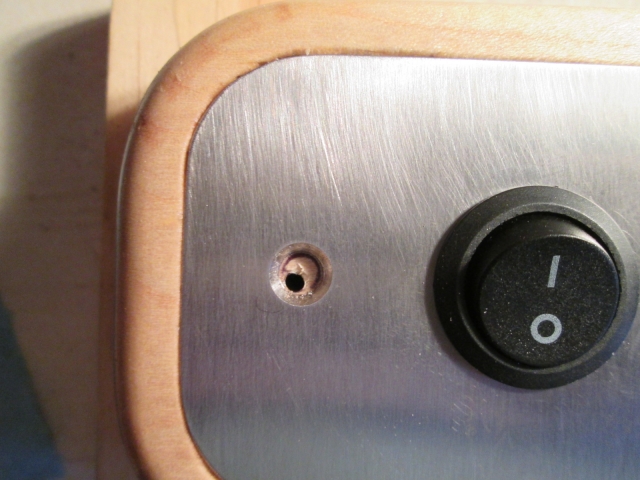
I ran a ball point pen around the inside of the hole as a reference.
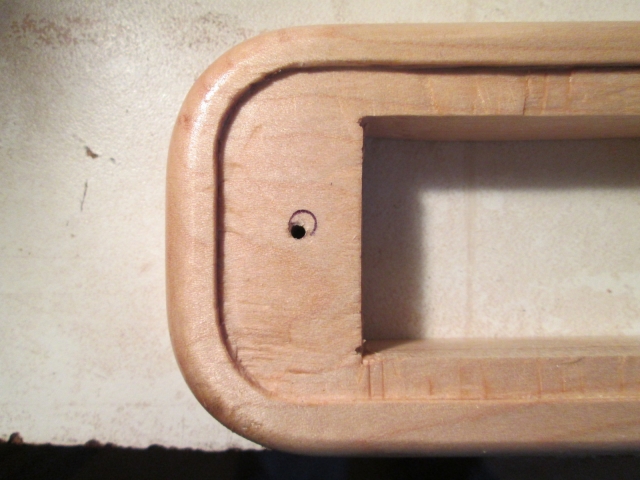
Back to the mill. Because it is very stable and the tools are short and stout, I used a 1/4 inch centering bit to pilot drill the screw hole oversize.
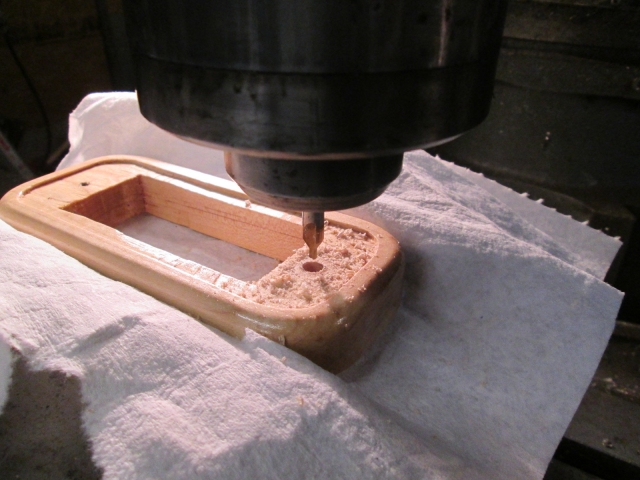
To get the hole a little deeper I switched to a 1/4 inch drill bit.
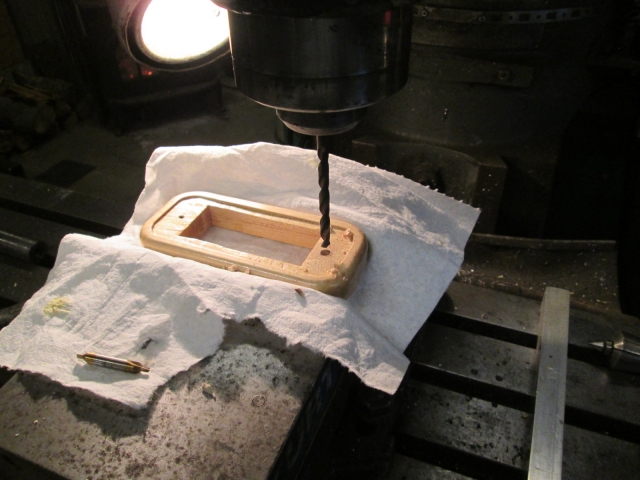
I didn’t drill thru the whole way.
This allowed me to stuff a hardwood dowel into the hole w/o it sticking thru.
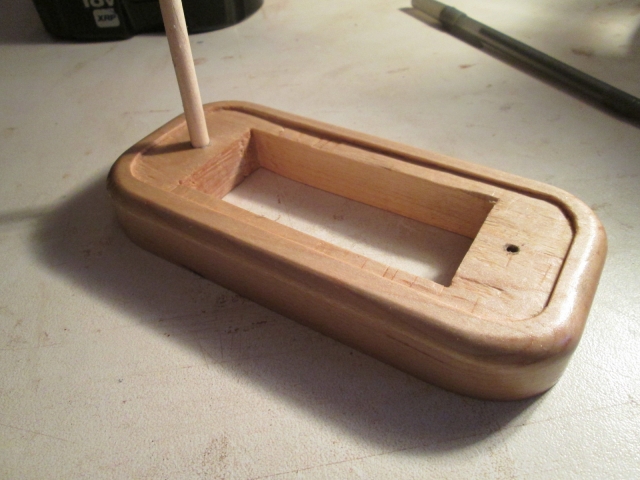
I cut a small piece of the dowel off by just rolling it on the table with the utility knife. Later, at home where it was warm, I glued the dowel into the hole. This will allow me to recenter the screw hole to the new plate so that the flathead screw sits flat.
Next, I went back to the pillow light switch blocks and routed the “hockey stick” wire ways. Note the blue tape with two reference lines.

Here is the starting point.
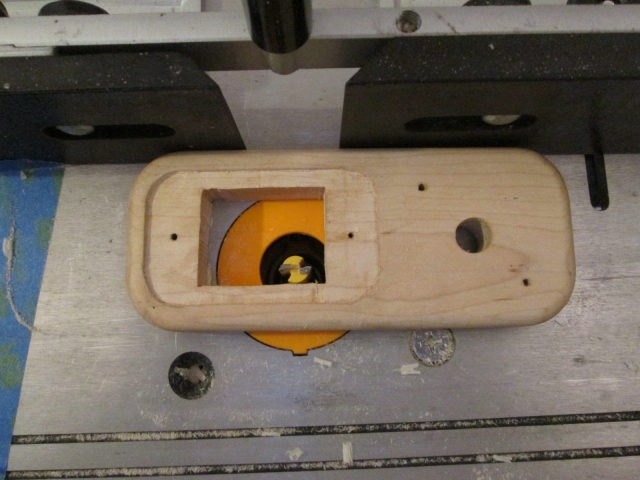
Ran it along the fence until it came to the first line on the tape.
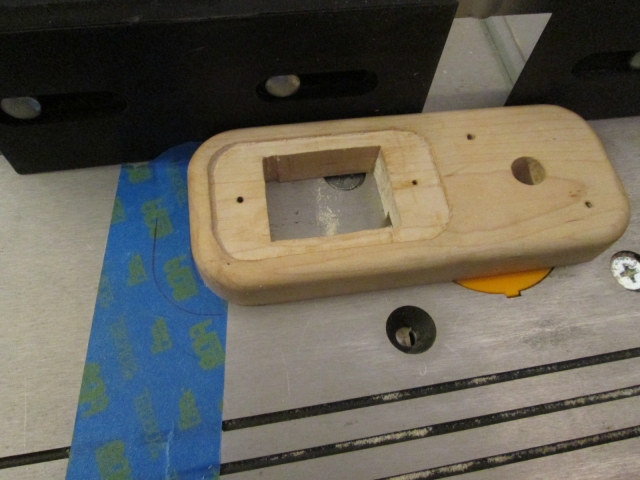
Then eyeballed it while rotating the trailing edge out from the fence until it lined up with the second line (which I had traced onto the tape while eyeballing the block with the hole centered over the bit).
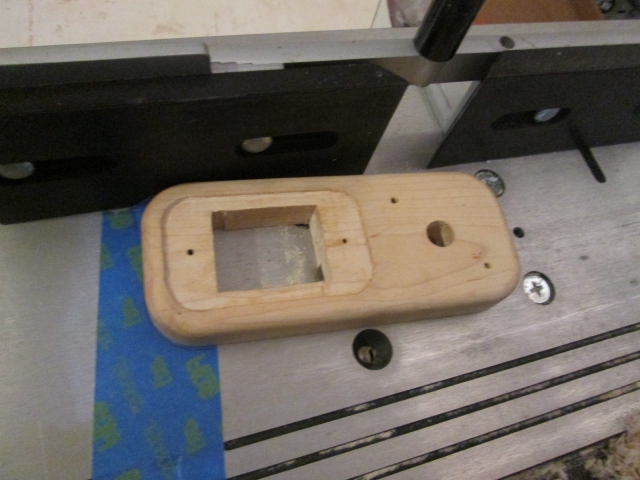
Second piece was done similarly, except opposite hand.
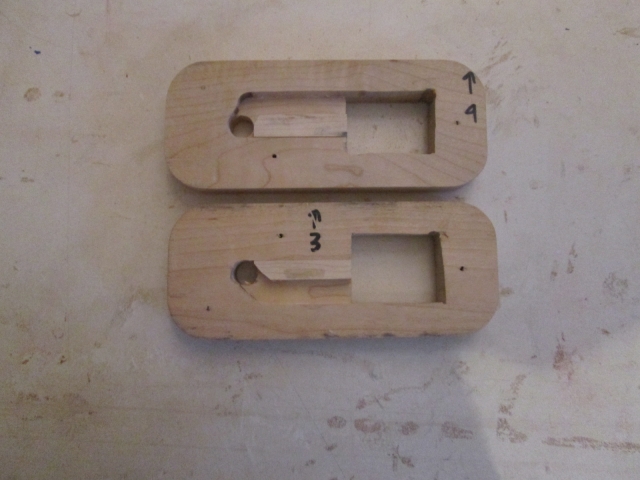
And by this time (about 4 hrs later) the sun (overcast sky) was starting to dwindle, the temps began to drop, and I was cold. Enough for today.