Rocketing forward at an astronomical pace...I got both of the sidewall bevels formed and got the next panels glued in.
I beveled the mating edges on the inside of the joint to make room for glue. I didn't touch the outside edge because that's the important surface to align with the adjacent panel (that's the one you'll see).
Here's the wall panel before
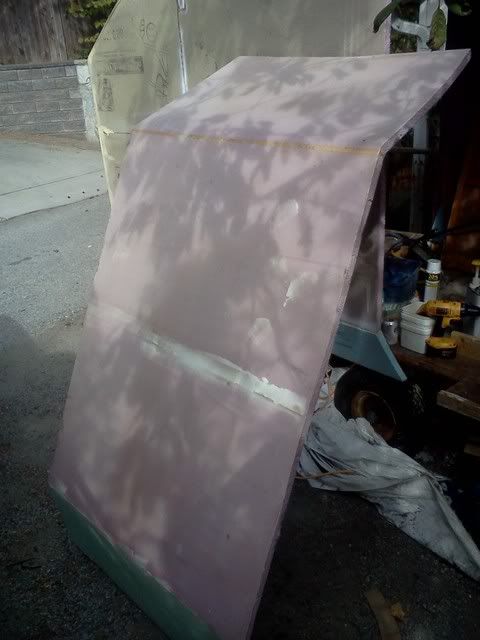
And here's the bevel. One of the things about this method is that, because of the expansion of the canned foam, the amount or depth of bevel isn't critical: the foam will expand to fill it. This went REALLY quick with a 60G disc in an angle grinder !
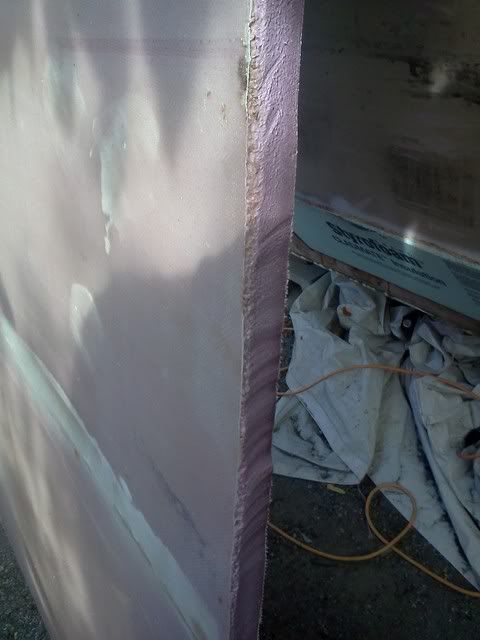
I didn't take a pic, but on the bottom I left a 'leg' at each end and sanded out a generous bevel between them. When I glue in the bottom I'll try and remember to show that.
Then I prepped the floor frame to receive the wall section: a quick sand of the old overexpanded GG runs (more is always better, right ?).
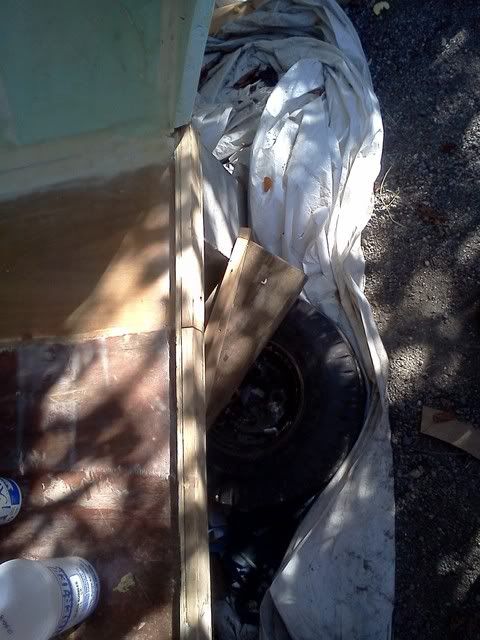
I'd have to go back and check, but I think I built the frame before I decided to cant the walls outward. You can see the 3/4" stock furred with a strip of 1/4" ply to make up the 1" foam thickness of a wall sitting vertically on top of it. To get 100% contact with a 45degree wall, that would need to be 1 1/2" (actually 1.414")....not that it matters at this point. A bit of time with a sanding block solves most problems...well, that and the generous use of high explosives.
This is the left (street) side offered up after beveling. On the outside are the strips of 1/4" ply I've been using to tack sections in place with drywall screws. That keeps the outside of the seam nice and flush and hold the parts against the expansion of the foam. The bevel is uneven but...who are we kidding...that's an angle grinder for you: quick but certainly not a finishing tool (much like the aforementioned explosives)
[img]http://i1202.photobucket.com/albums/bb363/Folder1966/IMG641.jpg?t=1349048986[img]
This is the joint after foaming:
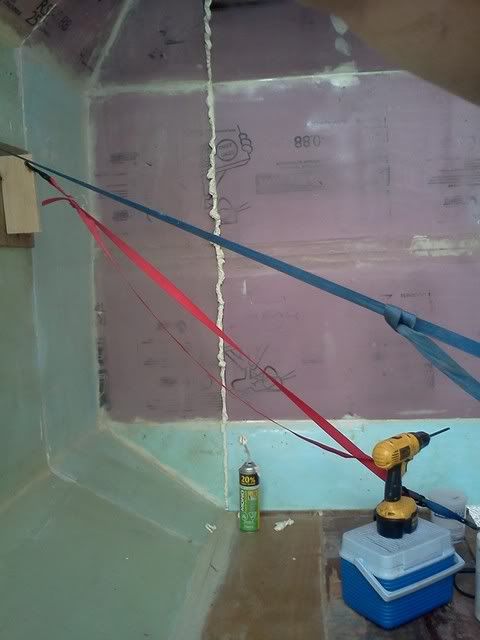
A bevel cut in the end of the applicator and the careful moderation of the trigger allows you to get foam all the way through the joint without voids that would have to be filled before glassing.
This is the left (curb) side after beveling and offered up into place, secured with a couple of the ply straps.
The wall forward of there is unglassed as yet, so it's not as rigid and able to flex inward. It really shows how much rigidity the glass adds. The glassed (aft) seam is perfectly flush - I know that it has to go in because that's where it came out of, but there's something satisfying when you offer up a piece and it fits like a glove...
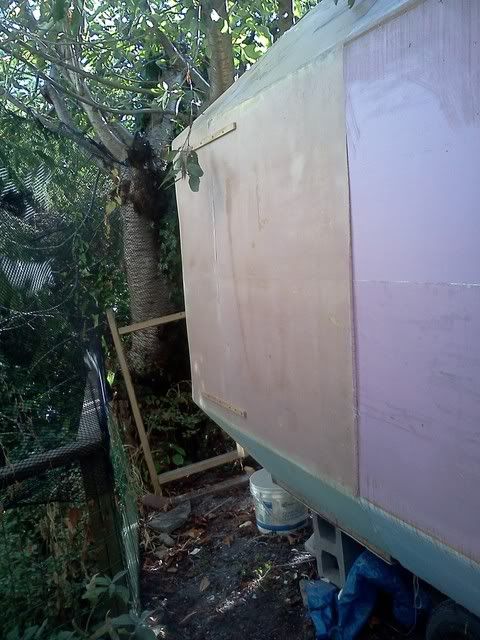
And a shot of the same seam from the inside. I beveled both edges on this one: that's how I'll do the rest of them.
[/img]http://i1202.photobucket.com/albums/bb363/Folder1966/IMG644.jpg?t=1349048953[/img]
A closeup of the bevel:
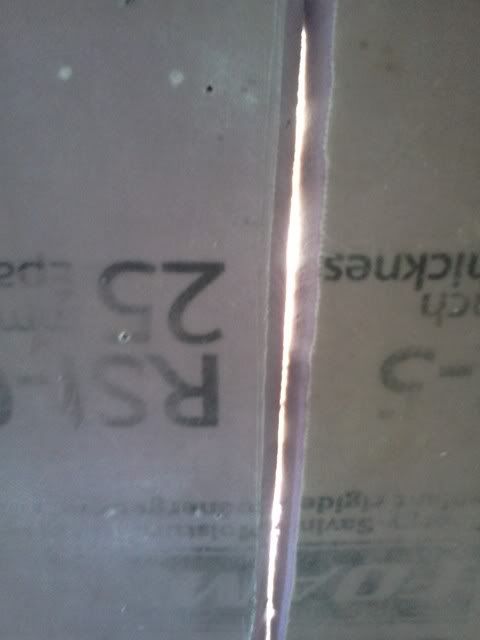
And right after I goobered it up:
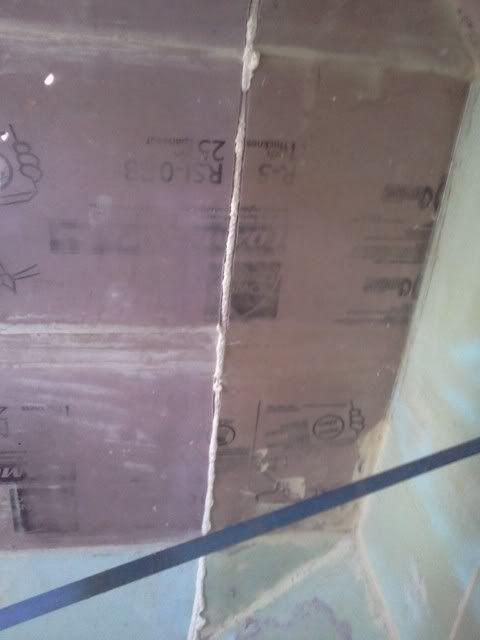
After taking out the rear former, I rigged up a couple straps to hold the back wall plumb. The bottom is fixed, so it acts as a bit of a hinge. Those plates you see have 16 screws each because it was important to have a lot of small pulls over a large area (12"X12") rather than just a few, which would easily pull out of the laminate. This allows me to keep the back face plumb and take out any twist.

And, because I haven't posted one in a while, here's an overall shot...looks the same as it did last winter !
Not inside though...and there's glass that you can't really make out...
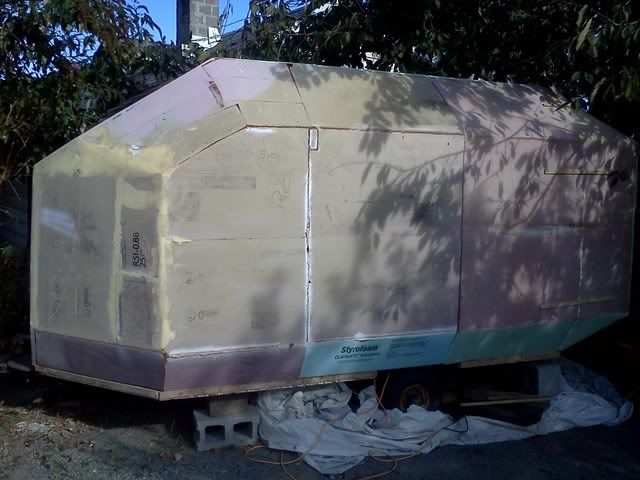
Glen's 'shuttle' comment has been with me all day....light paint and dark windows were already in the plan (thermal)...
I've also been thinking about tongue jacks. I have left myself space to attach one of these to the forward wall with the leg dropping down through the bridle.

Instead, I think I might cut off the coupler altogether and have a tongue extension made up. This coupler is welded on, but I can grind it off and have a local shop make a sleeve to go over it that will allow me to bolt a coupler onto a longer piece of tube. It's not so much for the sake of the jack, but for the fact that I can't really do what I want to with the LPG bottle(s) because there just isn't room: one of the compromises I had to make. The trailer is already small enough for our needs but I can't possibly sacrifice any interior space, and I want room to make up a fairing for the bottle(s) both for fuel economy and (more importantly) to keep them out of the weather and secure since I may be leaving the trailer in the bush somewhere as a hunting camp.