Started out Thursday taking a few pics and comparing my cheap steak knives over on the recent
foamie cutting tools thread.
Karl was fiddling with the coolant setups on the new mill and was using the circle program I mentioned to test, so I took a shot of that.
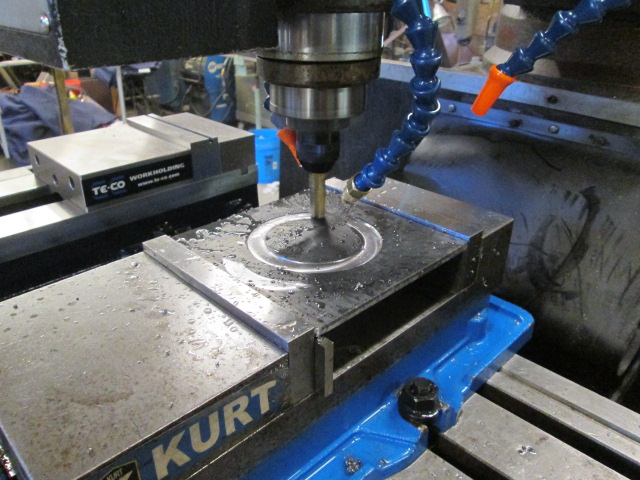
Next I did the primer fog test on a scrap. Forgot to take a pic of the spray can; it was Rustoleum 2X flat gray primer. Said it was good for “wood, metal, plastics and more”. To prep the panel I left the left hand side untouched, sanded the second two thirds with 100 grit on the small block, then hit the right hand third lightly with 220 grit. You can see the sanding scratches from the 100 grit in the middle. This is kind of a heavy application holding the can well back… except for the lower left hand corner where I was holding it and did not want to paint my thumb.
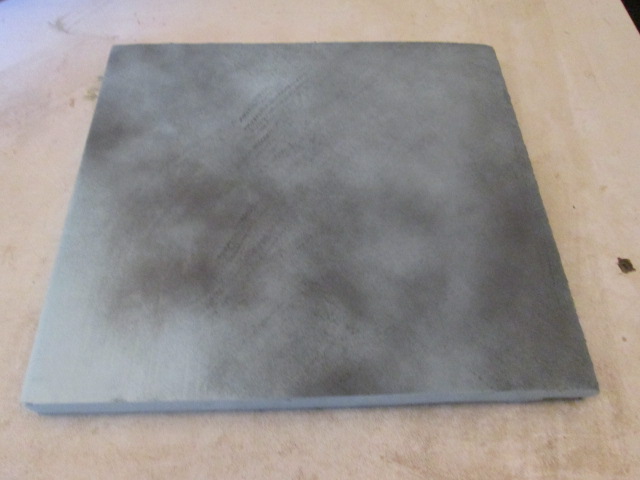
I didn’t see any real indication of melting as the paint seemed to dry very quickly; at least not anything more significant than the pores that are already there from sanding. At some point I found that less coverage is better because the color turns to dust and gets spread evenly as you sand. Unless you wipe it off quickly it defeats the purpose. With just a light coat (less than shown above) there is less tendency for that to happen.
Started on the right sanding with 100 grit on the small block, then, in the second pic worked over to the left. You can see the darkness of the primer down in the original sanding scratches.
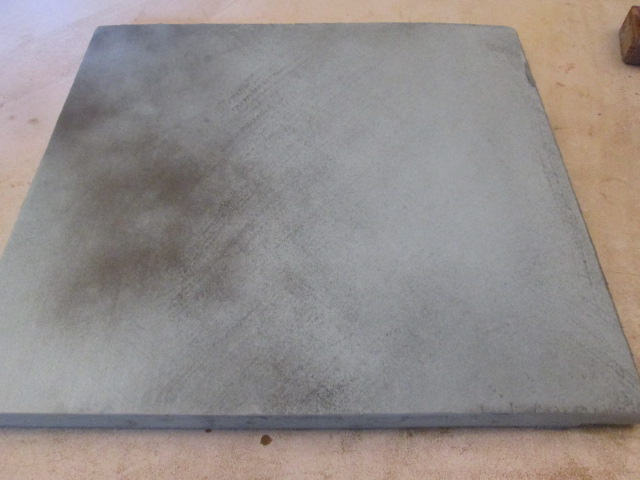
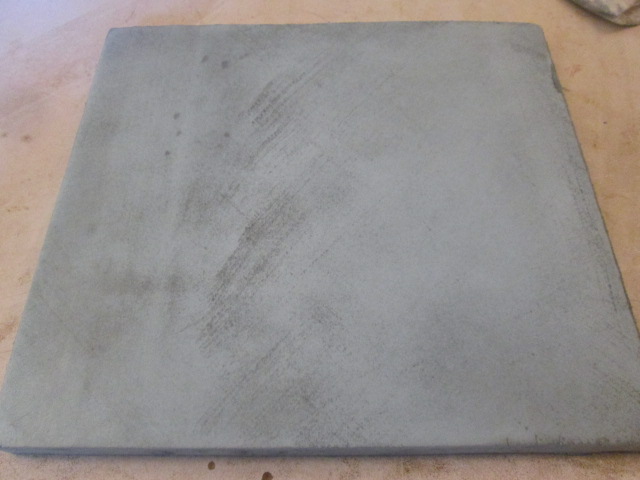
This didn’t really tell me much about getting rid of lumps, since the test panel was flat to begin with, so I sanded a shallow yet distinct valley into it.
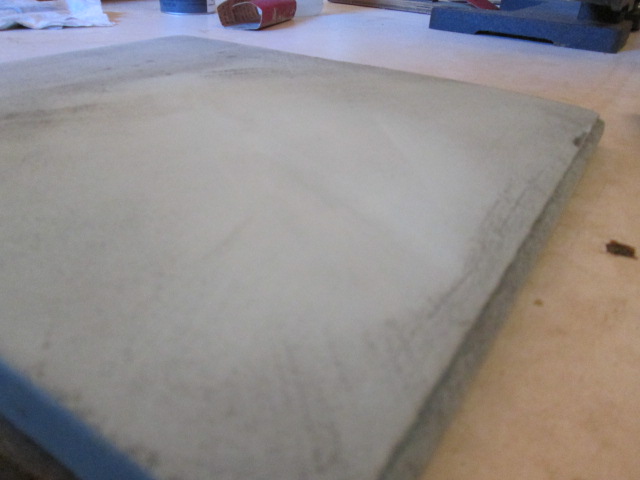
A lighter guide coat this time.
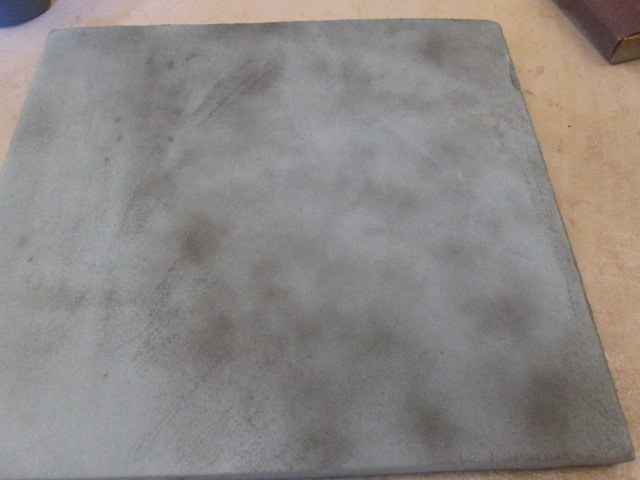
The small block is really too small for the size of this panel test, and wouldn’t span the valley, so I used the medium length board. It had 80 grit on it and given the depth of the valley I just stuck with that grit for this test. Here you can see the difference between the ripped up coarse areas and the more ghostly appearance of the valley.
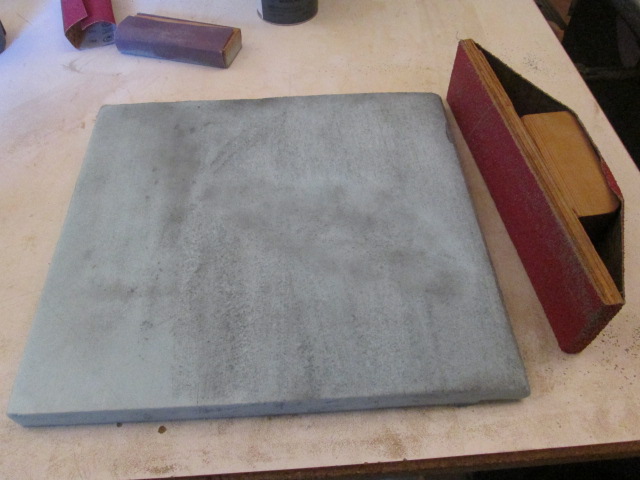
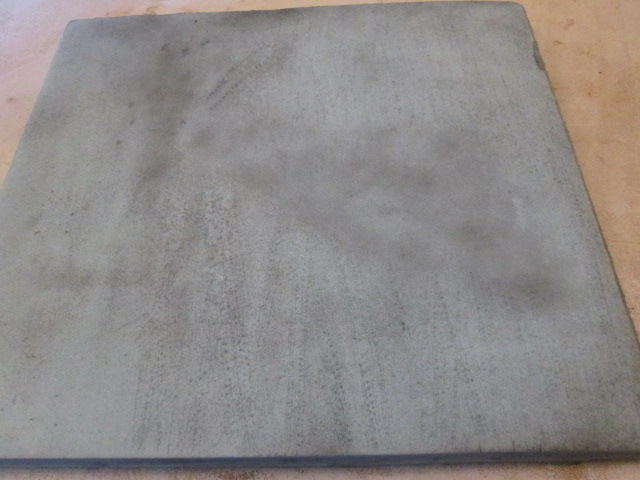
Since I wasn’t worried about taking too much material away on this test piece, I went ahead and sanded some more over the valley.
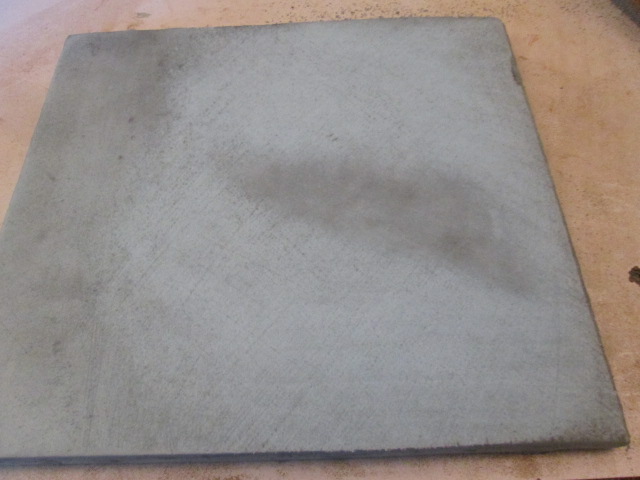
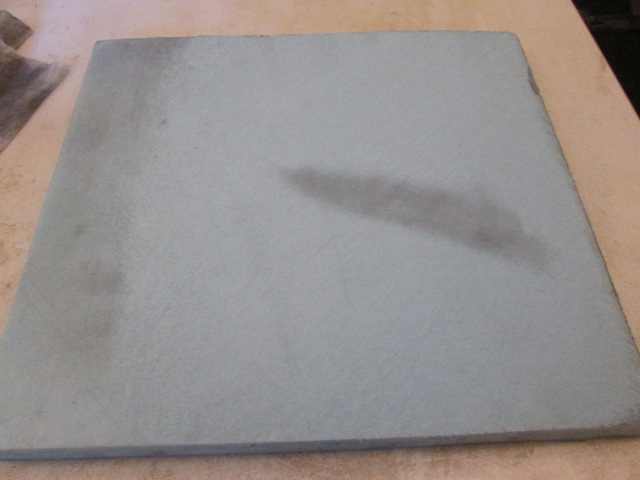
I also picked up a set of proper Bondo spreaders, thinking that the flexibility might work better than the relatively stiff plastic putty knives that I have been using. They did. I laid down some more spackle on the hatch trying to fill the obvious lows before bothering with a guide coat.
Now Friday night, I can’t tell you how much I appreciate Karl’s experience with body work and all of the different suggestions he has made, along with all of you. It may seem obvious to some what the steps should be, but I am learning new techniques as I get thru this, and it is not necessarily the same as working on a hard surface, like a car body. The suggestions have often helped me to decide which way to go to get a better result, and I appreciate all of the support. This is new territory for me.
(On a side note, Karl is a good listener and lets me dump the stress from my day job on him frequently, almost like he is addicted to the nonsense like a soap opera fan!

I was especially animated today, and it felt good to dump all of that stress.)
Anyway, tonight I wanted to switch my medium length flat board over to a finer grit, but was reminded that it is quite a bit narrower than a std 3 inch wide belt. That and the block I have been using to stuff in the back to make the sander belt taut was too narrow and didn’t give an optimum hand hold; so I made another one at the full 3 inch width with an improved (?... yet to be seen) tensioner block set up (forgot to take a pic.). I used that judiciously to take some of the highs on top of the hatch down a little before misting with a guide coat. Not sure why, as I wasn’t planning on doing anymore sanding until I got some more filler into the lows, but it ended up being helpful in a way.
I am sure you have heard of the technique of using a flexible spline or slat to conform to a curve and drag filler along a contour. Well I tried that tonight for the first time and it seemed to work pretty well once I got a little better idea of how the spackle wanted to be treated. The trick was to put a lot more on than would be needed. The spline didn’t seem to want to place, or plow material down into the lows, but it did a good job of dragging the excess off. With only a little excess filler it seemed to want to peel it up off of the surface (says right on the spackle label not to try and skim coat), so the trick was to butter it on, then drag most of it back off again… and don’t over work it. Like making delicately delicious biscuits, as soon as you get the butter and flour roughly combined, stop mixing. You’re done. Same with the spackle; strike it a time or two and you are done. You can get a little more with just a tiny touch of water mist, but the more you try to work it the worse things get. Just walk away.
I can tell that the solution to finishing this up is going to be: get some material on there and rough it in quick (don’t worry if it isn’t perfect, just get it on there close so that it has time to setup for next time); let dry then knock down the really gross stuff; use a guide coat to help decide what is a high and what is a low; knock down the highs and do another round to fill the lows. Repeat until it is good enough.
The slat I used was just the mill edge that had been sawed off of a 2x piece of fir, a scant 1/8 inch thk, maybe even only 3/32 and about 2 ft long (enough to reach from the hinge spar to the point on the hatch where the radius started to drop off more abruptly). I used the new medium length block to make sure the working edge was relatively flat and splinter free, then used the low spot at the back of the hatch hinge spar as a reference guide point. I didn’t bother keeling the cabin over, so I couldn’t quite reach the center, but I figure I can get that area easier from the rear once the outer side areas are set up. With the guide coat under the spackle it was interesting to see where the spline was touching off and leaving a gray spot, vs. where it stayed white indicating areas that had been low; so even tho I didn't sand on the guide coat much at all, it was still providing indications and visual aid.
Now here’s that same camera view as before where I took the lumpy bustle pic from, except things are looking much flatter now.
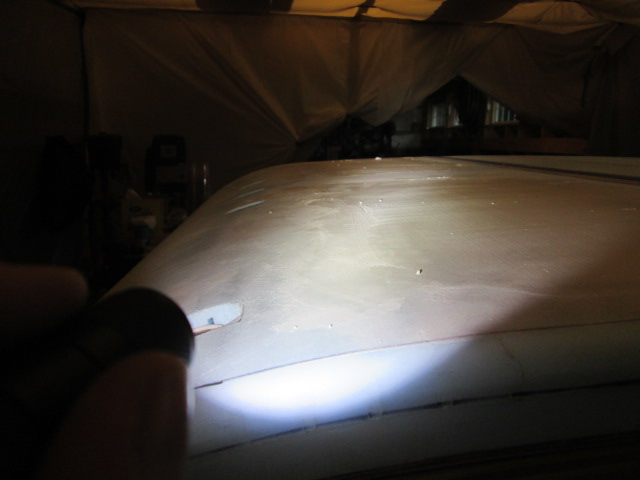
… and another from up higher by the hinge looking more straight across. I can work with this and see a big improvement.
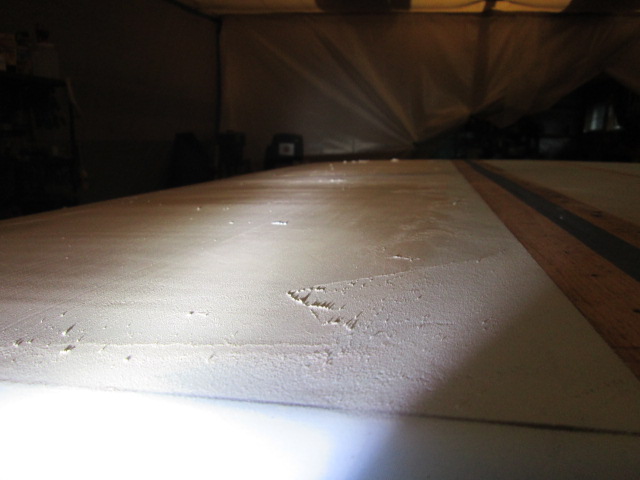
Having a bunch of excess spackle slopping around, I tried to use this technique on the front roof, too, but I think those biscuits may have come out tough from over working. I'll have some more work to do up there tomorrow.
No matter, I think I can get where I “need” to be with the techniques that I am learning here as I go.
I’m happy with where I got tonight. Not for the amount of work that got done, but for the skills that I am developing, and the fact that it seems like I am moving in the direction I want to go, not backwards.
I keep forgetting to bring my line chalk; have to remember to try that, too.