All week I have been feeling like I have hardly been getting anything done. Late starts due to errands and misc. distractions (not the least of which have included reading long-EZ build blogs on the premise that it is research into composite techniques… but mostly because it is fascinating and probably the ultimate “foamie” homebuilt project I can think of), and with the change in the colors of the leaves on the trees the chunkin’ blood starts to circulate in the veins, so there are some responsibilities to attend to there, too.
Anyway, tonight I finished back filling the tuff spots in the TB with foam strips. I probably should have just filleted everything with epoxy filler, or micro, but the largish step under the TB rim, and the acute angle at the battery box bulkhead would have taken a lot of material. I have plenty of scraps of foam, so it made some sort of sense to try this method.
But before we get into the details of that, let’s get caught up on a few pics that have been sitting in the camera. Here is that pile of cedar 4x4 drops that Karl brought me. Good stuff. In front is the magnetic feather board that Karl got for us.
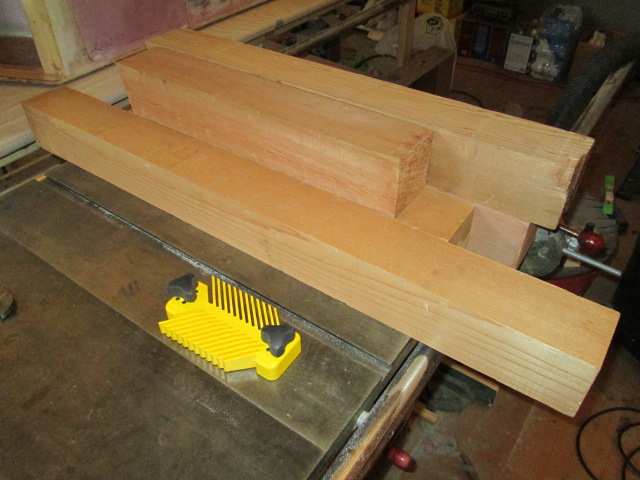
The feather board is pretty nifty. Just a quarter turn on the knobs to release or apply the magnets, and it holds very well on the cast iron top.
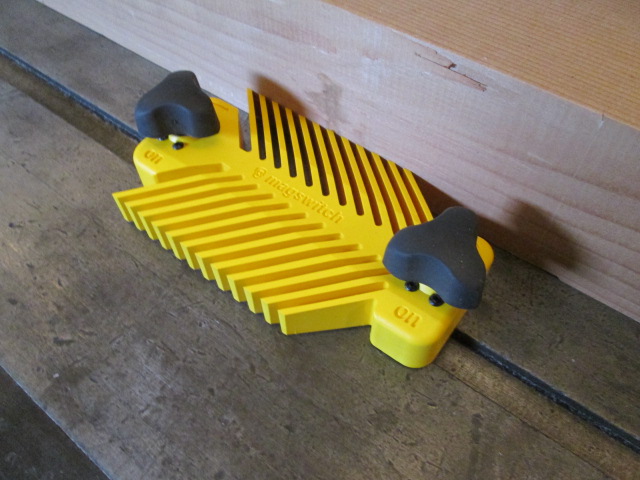
At work they updated all of the first aid kits throughout the plant, so the old ones, including their contents, became obsolete. I took my pick and restocked it from the others that had been removed from service. Nice metal box with draw latches, bail handle and folding hinged tabs for wall mounting if desired. I’ll keep it in the loft for the remainder of the build and then find a place for it in the camper.
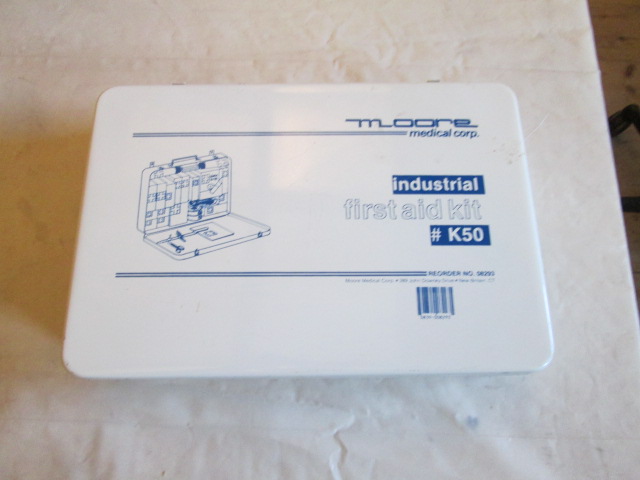
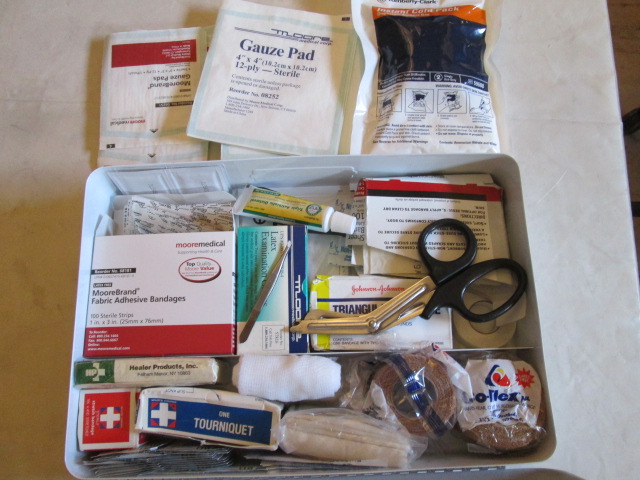
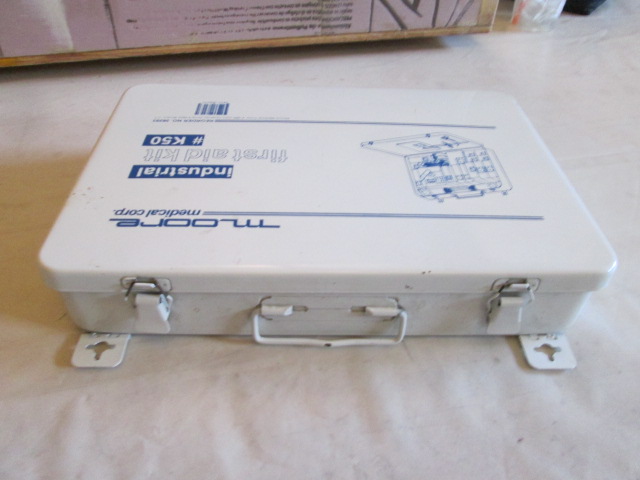
Okay, dry fitting foam corner bits so that the fiberglass can make the turns. I will still use a bead of filled epoxy in the corners of these strips, but it will take a lot less filler to get the job done.
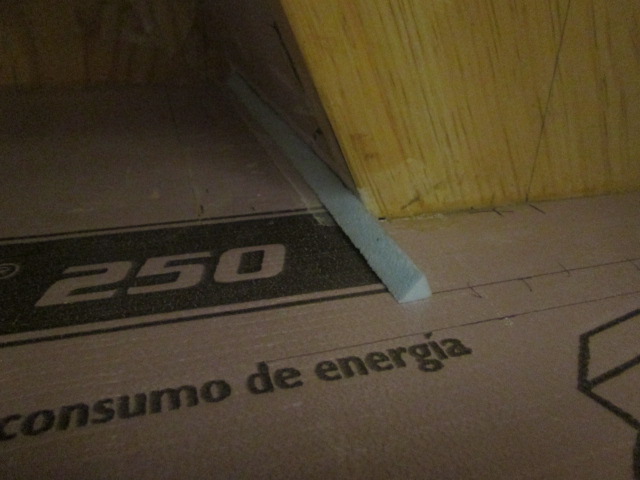
Here it is the next day after trimming to length, gluing in with TB2 and a little touchup sanding.
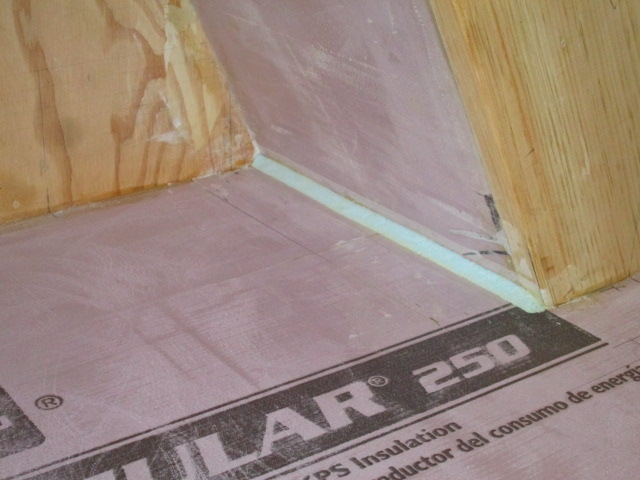
The best way I can figure to do the TB layups is to cover the inside of the main compartment wrapping up at least to the inside edges of the top frame, if not out onto the top flat portion of the top rim frame. Then when I wrap the outside it can overlap onto the frame top, or even wrap down just to the lower inside edge of the top frame.
The top frame overlaps the edges of the TB side panels resulting in a soffit like lip all around the inside edge of the frame. In order to get the glass to “walk” over this inverted lip it will need a pretty good fillet, especially on the back panel where the angle is acute due to the forward pitch of the lid.
After digging out the excess PLP squeeze out from under the rim of the box (all the while thinking that it would be far easier to just sand the back corner of the foam triangle, but not seeming to be able to switch gears… obsessive detail chasing), I used my angle finder tool to set the table saw and cut this triangle piece of foam from the edge of a larger panel. I used TB2 with blue tape clamps to glue it in. This is the top back lip of the TB shown with the TB laying on its back on the bench.
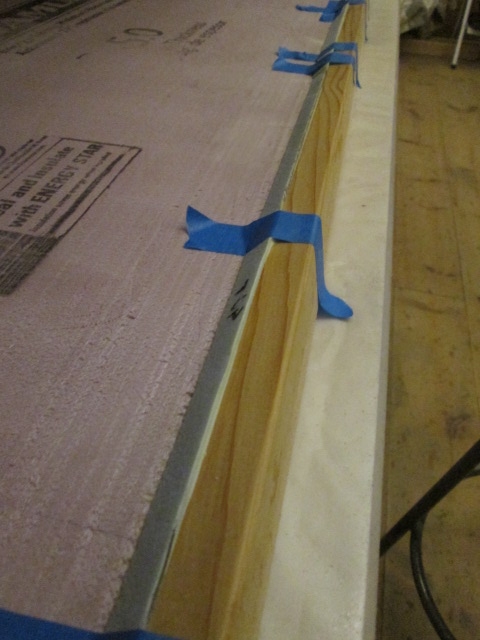
The next night, last night, I pulled the tape and sanded the extra sharp point down flush with a little round over.
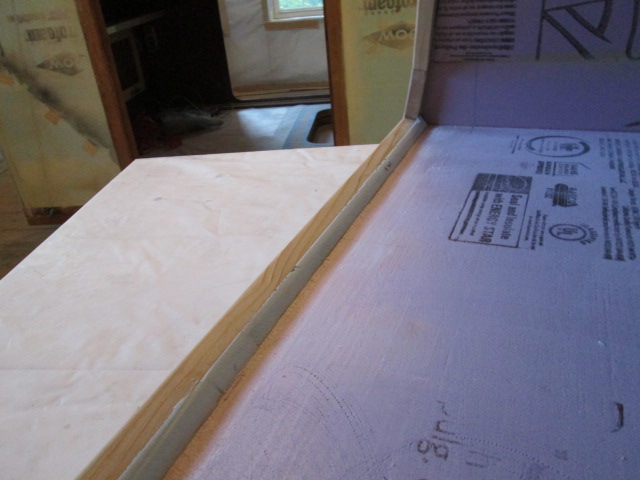
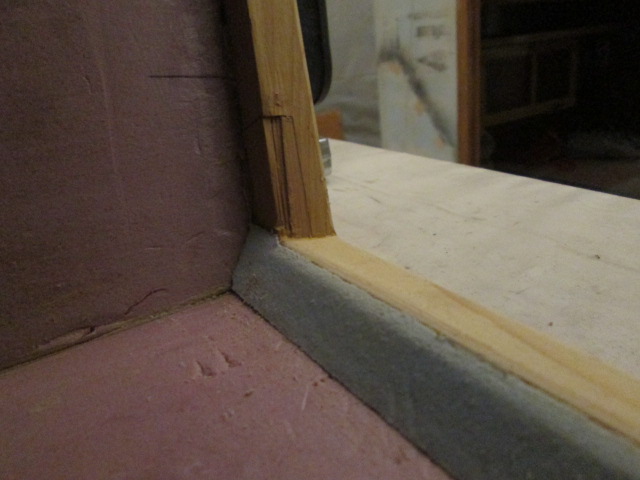
I’ll fill that little chip out of the cedar with epoxy filler later during the layup.
For some reason I had momentarily forgotten about the double fence technique that I had been using with the mini bandsaw; a lot easier to set up and run the slender flexible strips. So, since the front, back and side triangle profiles are all different angles, and I had plenty of slender trimmings that can’t be pushed thru the table saw, it finally dawned on me to use the little bandsaw. Here’s another look at that set-up.

Also, to move things along, I decided to give the hot glue gun a try instead of the TB2.
The hot glue worked fine so long as I kept the hot nozzle away from the foam. Also, if I put too much glue all directly on the foam it would melt it. If I deposited the glue on the edge of the cedar it would cool just enough to still stick, but not be so hot to melt the foam.
That allowed me to bang out the other 3 sides, including mitering the ends so that they blended well.
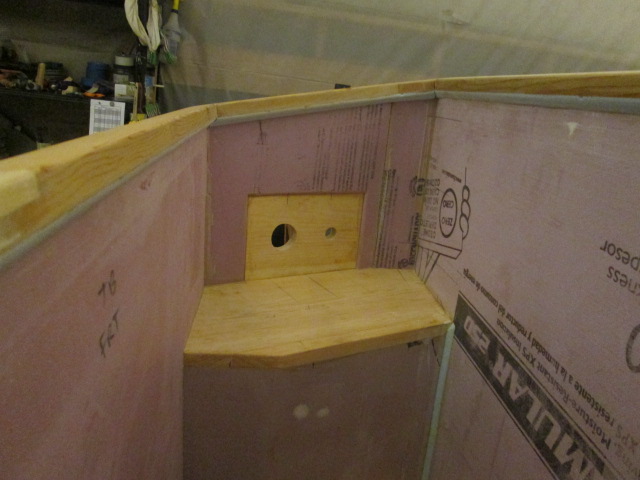
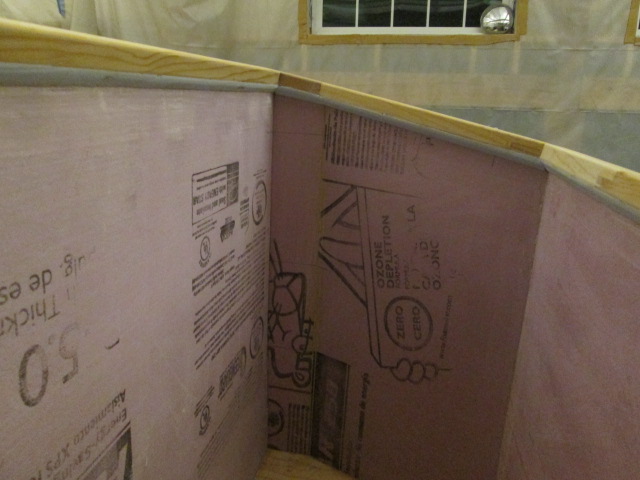
During all of this I also made sure to scuff the gloss off of the foam.
So what’s next? Well, tomorrow Karl and I go north to prep for the hurl. And Sunday morning is supposed to be sub-freezing temps, so I’ll have to watch and either set the TB back up as a hot box, or haul susceptible supplies to warmer locations.
Plugging along here, slowly but surely.