That's the plan Capn. Just have to "hide" the mistakes.
Strange, almost unbelievable thing happened at the shop today. A presumably orphaned deer came wandering in asking Karl for help. It seems that it needed something lanky and tall to follow around, and Karl became its surrogate. He fed it apples, made sure it had water and tried to contact a guy recommended by our veterinarian who runs a “foster forest”.
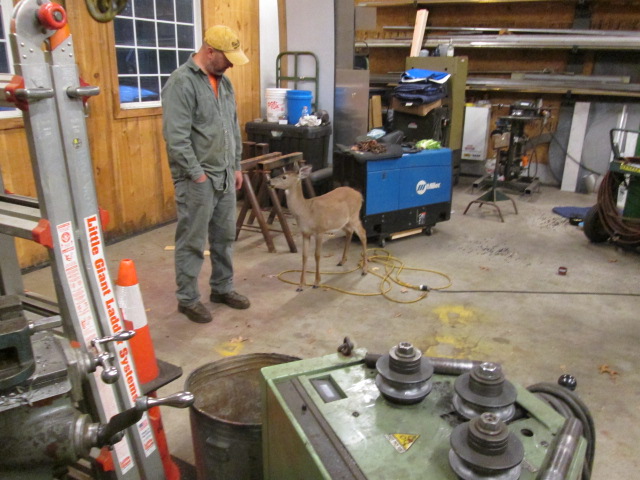
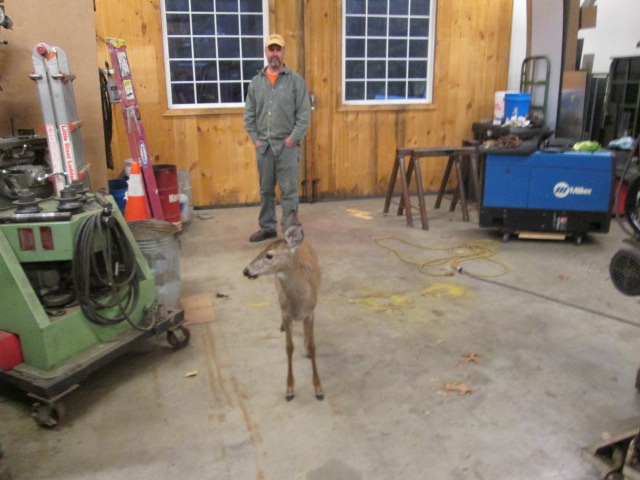
When I came along this evening, Frankie (the name Karl’s wife had given it) had no problem adopting me into the herd, coming right up to me, sniffing my hand and letting me pat it on the head and stroke its ears. A very surreal experience… something that just isn’t supposed to happen. (Blurry pic because it reacted to the noise of the camera.)
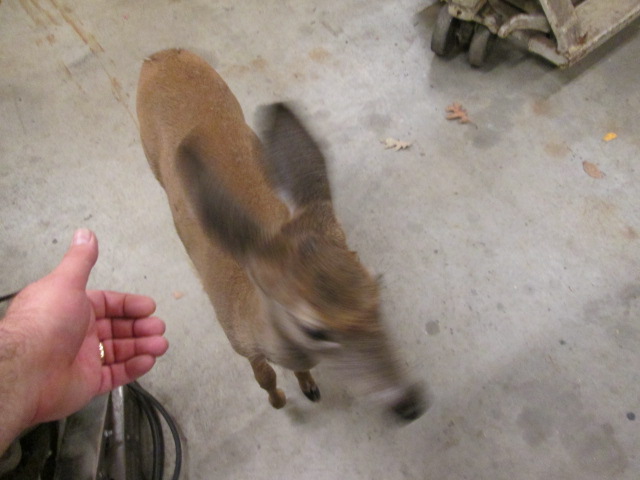
I’m sure the poor little deer was just doing what comes naturally, trying to stick with the herd, to the point where it would climb the stairs to the loft and try to come up past the trap door if we let it (but that was going a bit too far). Fortunately it would follow Karl everywhere he went, so it went back down with him. Torn between letting the thing get eaten by coyotes, having not heard back from the foster guy, and not wanting to set a bad precedent (keeping a wild animal as a pet is probably not a good idea) Karl tried to lead it back into the woods, and it even ran ahead of him as if it was going to take off, but shortly it came right back into the shop again. That was about the time I left for the night, but I’ll get an update tomorrow. Unreal.
Anyway, back to reality. I started by trimming the excess hardened glass from around the inside top of the TB rim. Finally something that the serrated steak knife worked perfectly for. First I made a rough cut to get rid of the porcupine spikes at the top and make things more manageable; then I came back with the knife flush to the rim and sawed the last little bit off.
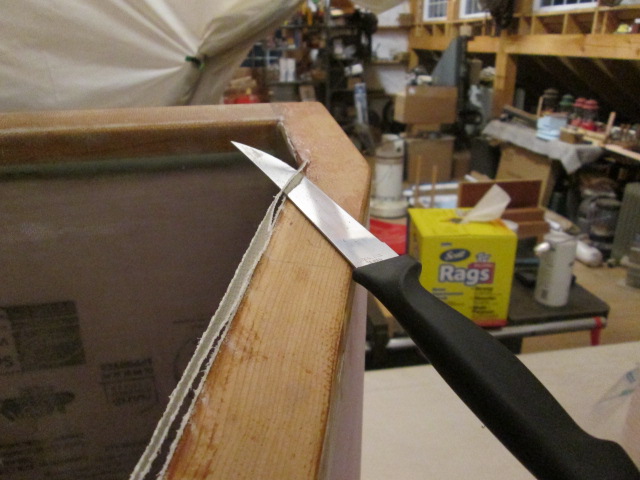
The fine serrations on the knife worked really well getting thru the 2 plies of 6oz weave.
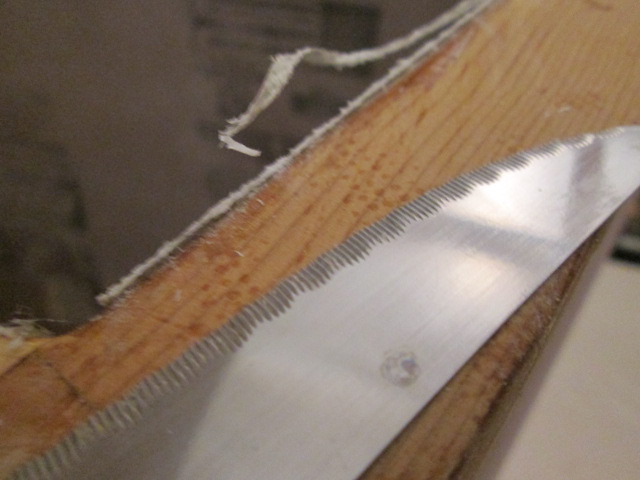
Next I used the small hand block and 100 grit to roll the edge and blend it into the rounded edge of the rim.
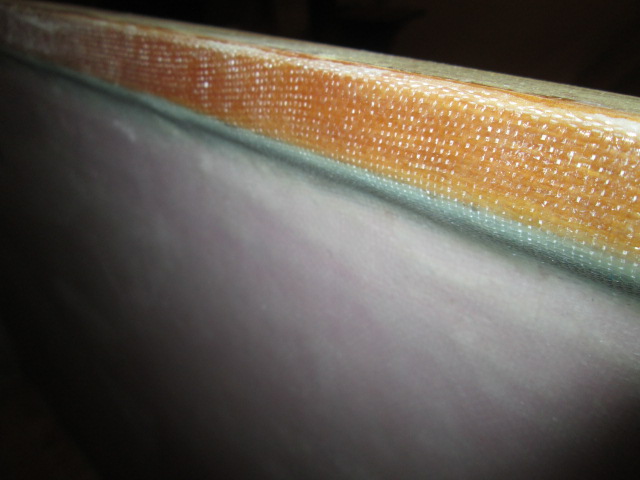
General cleanup of corners, edges and sanded a few barbs.
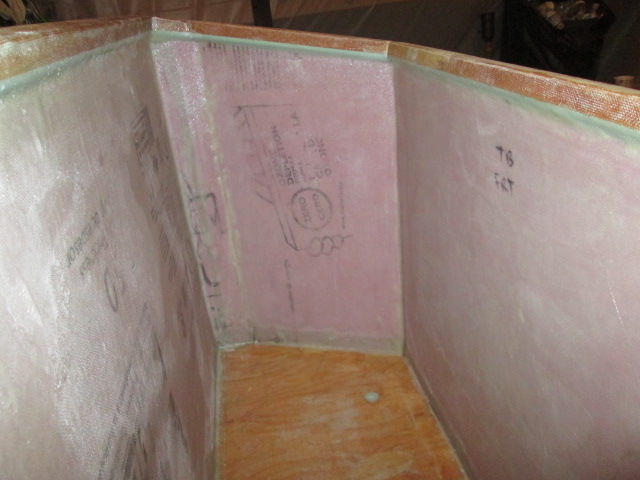
One of the small side corners didn’t bond to the rim well and pulled a sliver of wood off at the top when I sanded on it. Because it is nice and flat I should be able to drizzle some wet down in there and get it to adhere. Also notice the difference between the back rim (on the left) where I tried to wrap the glass all the way (complete with white blisters showing thru) and the sides/front (on right) where I let it run out and just trimmed it off at the inside edge of the rim.
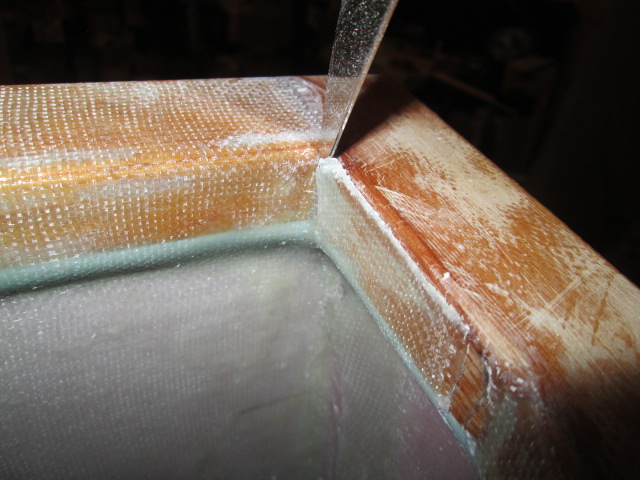
Inside, at the power inlet bulkhead, the serrated knife tip worked to chase out the ports for the shore power and solar connections. The extra fairing I did between the 3/4 inch bulkhead and 1 inch foam worked out well and all laid down nicely. There was a small blister on the electronics shelf just under these ports that got sanded back. I’ll make sure to coat the ID’s of the holes well before I’m done.
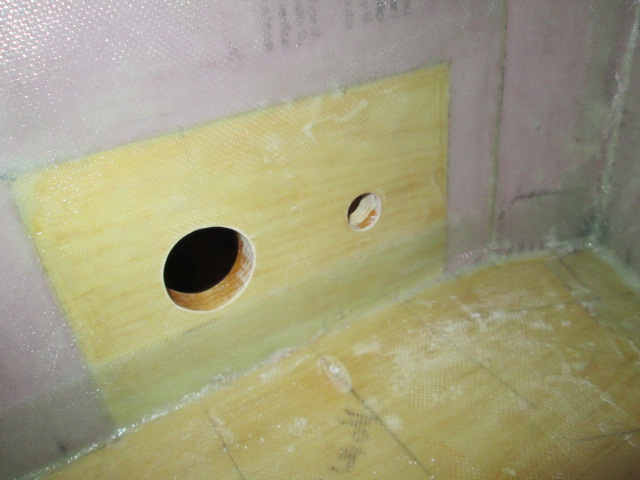
Last night after locating a Mogul base 3-way lamp (300/200/100 watt) I finally have some decent light (should have done this years ago!). Later I clamped the base of the fixture to the bench to guard against accidentally knocking it off the bench. You can also see the template I had started for the glass on the bottom of the box.
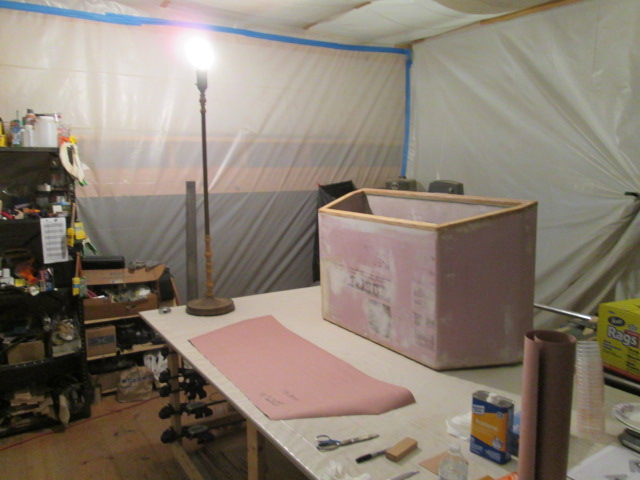
Spent some time noodling over what I had done (seems like ages ago) with the fixed shim where the J-box for the main wire bundle penetration mounts to the underside of the TB. Best I can recall I left one side of the shim open so as not to encroach on the draw bar A-frame, but with the 1 inch rubber isolator mounts that shouldn’t be an issue clearance wise. Needing a dam to fillet up against I fashioned a piece of foam wrapped in packing tape (as a release agent) to fill the notch, then taped over the other side of the hole just in case.
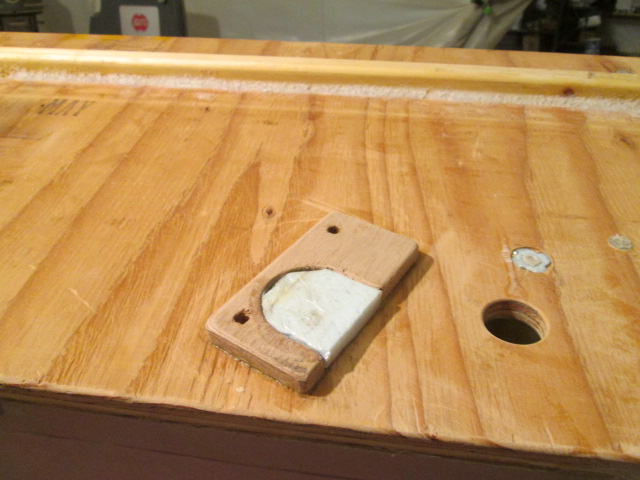
The plan was to fillet around the shim then glass right over all of it. Then I would cut the hole back open and remove the foam filler. The fact that the shim is skewed relative to the weave should help transition over the edges, but I didn’t like the way that the area between the hole and the fillet would be sharp, so I made a new plug, Rev. 2, that fit thru the wire hole and would allow the fillet to wrap around the plug some more. This time wrapped in stretch wrap.
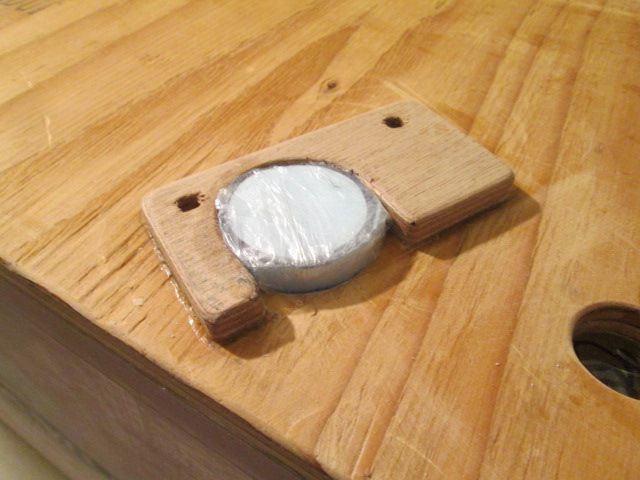
The plan is to cover the stiffening rib under the box with a couple of plies of bias cut, then cover the whole bottom with more cloth. Since I can get more efficient use of the cloth with the weave, the plan is to cut out an overlapping slot in the larger sheet to let the rib poke up thru. You can see that detail here in the template.
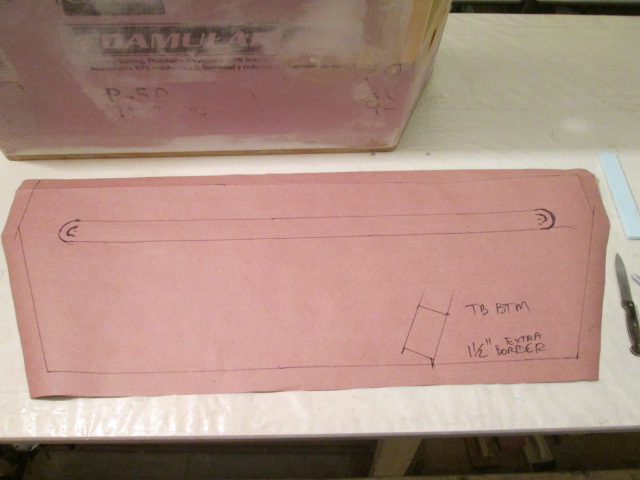
Then I set in sanding the back rim to get rid of all of the blisters and areas that had not bonded properly. Started with the small 100 grit block but quickly switched to the medium board with 36 grit. That got thru the blisters quickly and moved the loose edges back. Then it was back to the 100 grit to do the final feathering. The epoxy and glass will turn to a fine white powder (respirator mandatory), so I would wipe frequently with a damp paper shop towel. This helped keep the dust at bay, but also helped as a guide for the feathering. If there was still a loose lip the white dust would stay visible under the edge. Once there was no white edge the glass was easy to feather. Learning to tell the difference between lack of adhesion, stray clumps of fillet filler or spackle, and the dull haze of sanded glass takes a little getting used to, but that’s why I am going to the trouble on this piece. Here’s the rim of the box after getting all of the spots that bothered me.
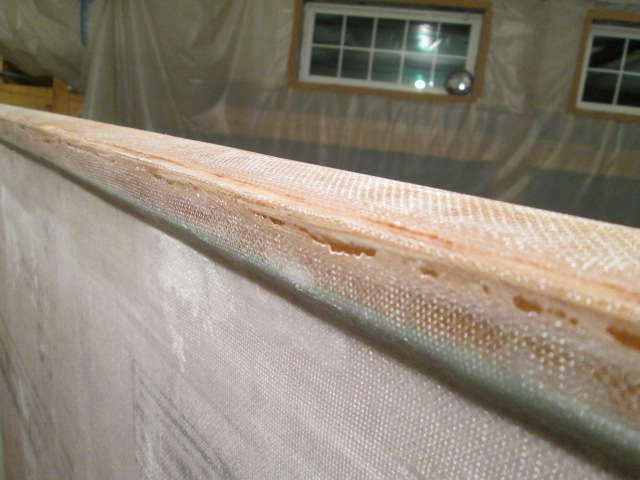
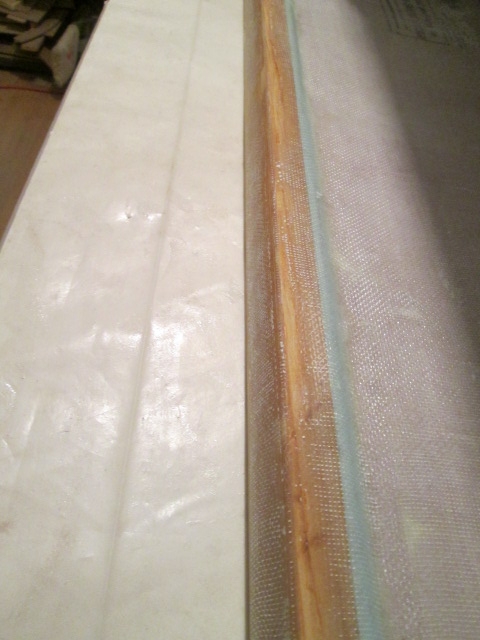
Buoyed by getting to the bottom of that, so to speak, I decided that a couple of the larger blisters on the inside back corner of the box should not be ignored (for the sake of learning to deal with them), so I sanded them out to where I could get the extended razor knife in there and trim back the flaps. Then some 36 grit under my thumb to knock the edges back, but not obsessing too much. The plan is to hit these with some of the filled epoxy the next time I am filleting, that way the foam will have a hard coat and it will be relatively flush, rather than adding overlapping plies and having a more uneven surface. I’m not really worried about panel strength here, just ding and dent protection.
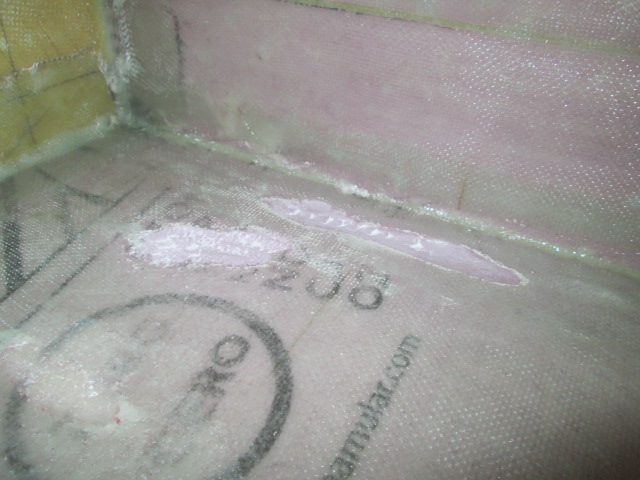
The layup plan now is to:
(a) Finish filleting the bottom rib, lay the bias strips over it, then the bottom panel. Cure.
(b) Trim the bottom layup flush to the sides then increase the bottom edge radius so that the side, front and back panels can wrap under easier.
(c) Add blocking for the draw latches and do any touch-up bodywork on the outside of the box.
(d) Increase the radius around the battery box opening.
(e) Mask a straight line under the rim all around the outside using duct tape as a cut reference/release agent and lay the bias tape over to cap the top rim (consider increasing the edge radii here, too). Try to catch the firm trim stage of the cure and trim to the tape line.
(f) Layup the back panel wrapping under the bottom and running slightly past the top rim (to be trimmed flush after).
(g) Layup the front and sides wrapping under the bottom, on to the back, and running up past the rim (to be trimmed flush after).
(h) Fair the weave and any larger lap seams with fairing filler (but don’t get too sucked into perfect bodywork).
Tonight I worked on making templates for bias strips that will cap the rim and the bottom stiffening rib; and took inventory of the last of the 38 inch wide 6oz. Here are a couple of the templates in progress.

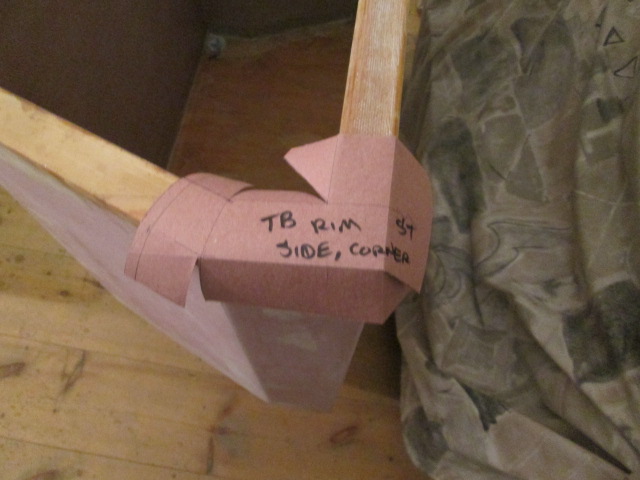
Yeah, and I pet a wild deer. Crazy.