Took a few more bites at the elephant today. I decided that there would still be plenty of flat surface area for the TB lid gasket even with the rim round over increased from the original 1/8 inch radius to 1/4 inch radius both inside and out, so I went ahead and ran the router around the inside edges and along the side edges. The front and back edges aren’t a 90 deg angle, so I had to do those by hand using the matchbox plane and small sanding block.
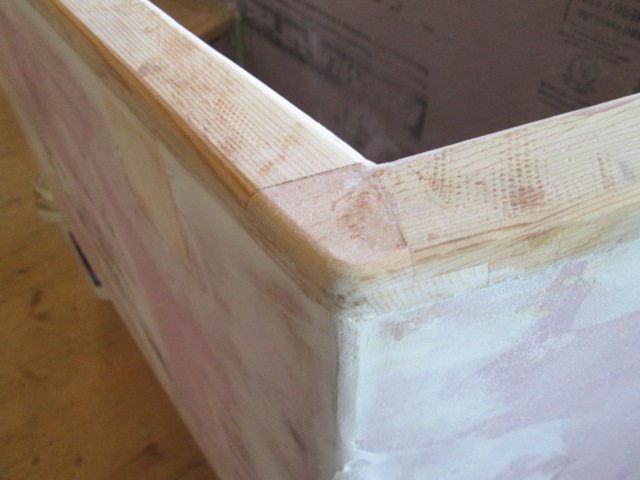
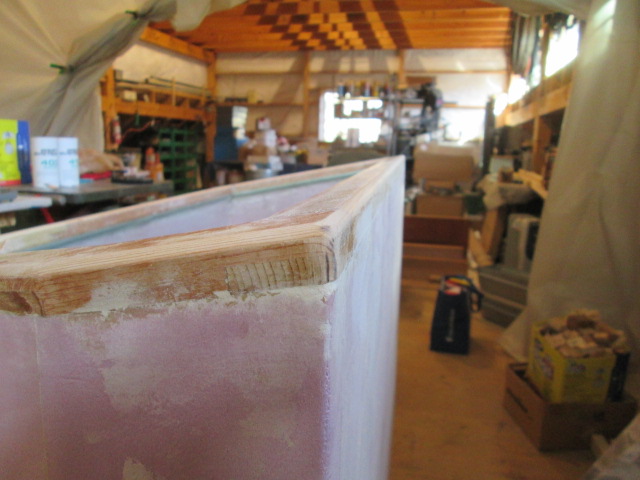
I did some more bodywork on the sides of the box and while that was setting up I cut the glass blanks for the back of the box (2 plies), and for the front and sides (the latter as one section in 2 plies). I considered buying more of the 38 inch cloth, but when I figured out the sizes and yields it turned out that it would cost more and I would have more scrap using the 38 wide than if I split a shorter piece of 60 wide in half lengthwise. I figured it would be just over 3 yards to get 2 plies, so I bought 4 more yards. In the end, because the clerk gave me a little extra to account for the uneven cut edge, I ended up having 35 to 36 inches left over. Since my workbench is not 60 inches wide, I unrolled the glass from front to back on the bench, using the edges of the bench and lines drawn on the plastic to keep things square, and cut up the middle. Since the bench is only about 4ft wide, I did this in 3ft sections and rolled the resulting halves up as I went. First the two plies for the back of the box at about 42-1/2 inches long, then the front and sides pieces at about 74 inches long, total.
From there I turned the longer pieces and again lined them up with the bench. As tempting as it is to continue using the PMPP technique, this piece may be a bit large for that and I figure I need to work more on my dry on dry technique before getting to the hatch. So instead I made some reference lines directly on the glass that I hope will help me lay it on the box accurately.
Here are the two plies for the front/sides laid on the front of the bench.
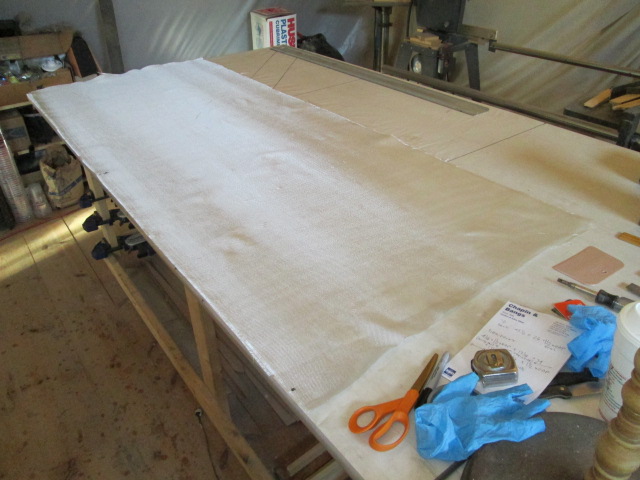
And here they are with the 2 inch allowance for wrapping under the bottom of the box (along the bottom), the locations of the side corners, and the profile of the rim at the top.
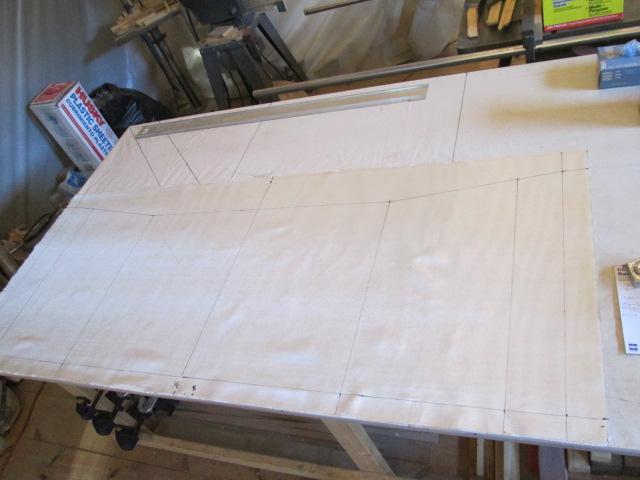
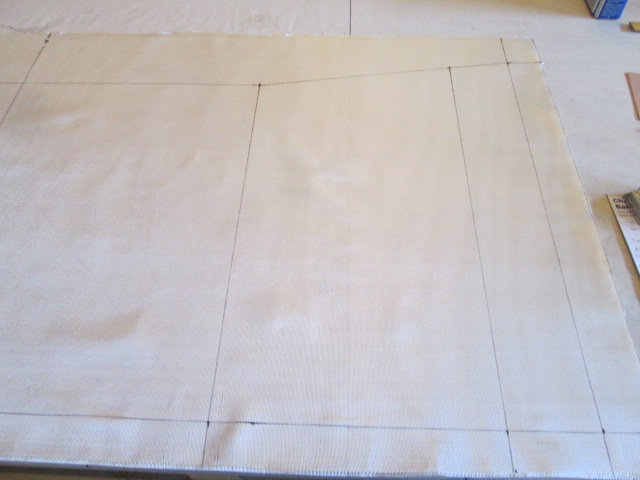
The plan is to wrap the bias cloth over the rim next, then have this piece cap that running up flush to, or just under the rim. I was reluctant to cut the top profile yet, for fear that it would fray before I can get it on the box. Tempted to go back to the PMPP here, but will see what happens as I go.
I used the angle finder to transfer the side angles to the bench, bisected those angles with the compass, and then used the angle finder again to transfer these angles for the darts at the bottom (dart angle equals half miter angle, I think).
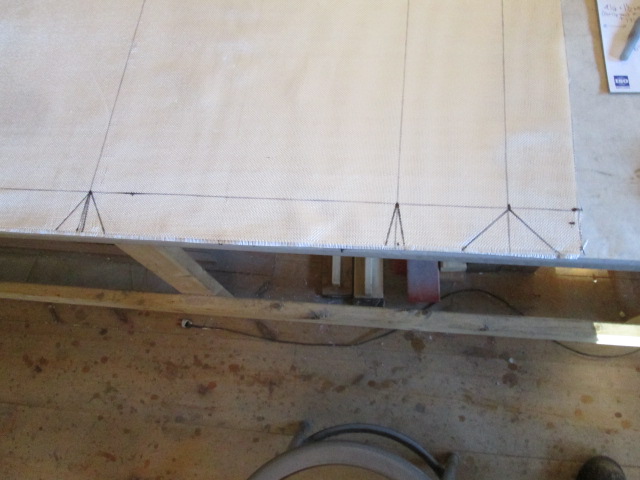
One last task for today was to clean out the t-nuts in the underside of the box for the rubber mounts. I decided to do a tutorial style of documentation here, so step by step. Recall that I wadded up plastic stretch wrap, screwed it into the threaded holes and trimmed it flush before glassing over. Here you can see one of the 5/16-18UNC T-nuts for the battery hold down on the left and the darker circle for one of the 3/8-16UNC mount studs on the right.
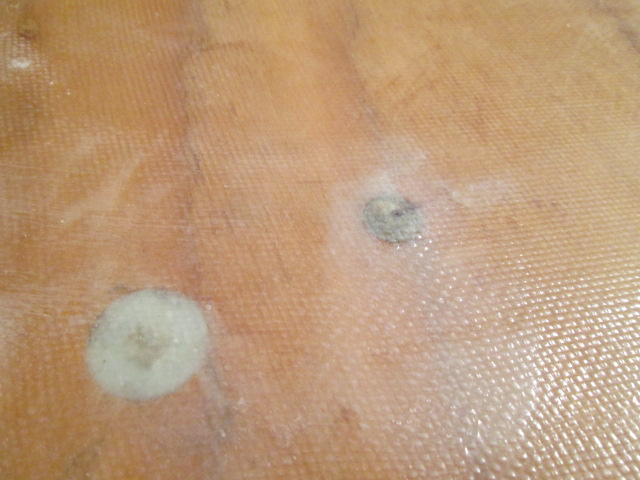
To start I used a small drill bit, eyeballed center from a couple of axes, and just spun the bit by hand to make a center mark. Later I found that I could easily drill a pilot hole by hand if I wanted to.
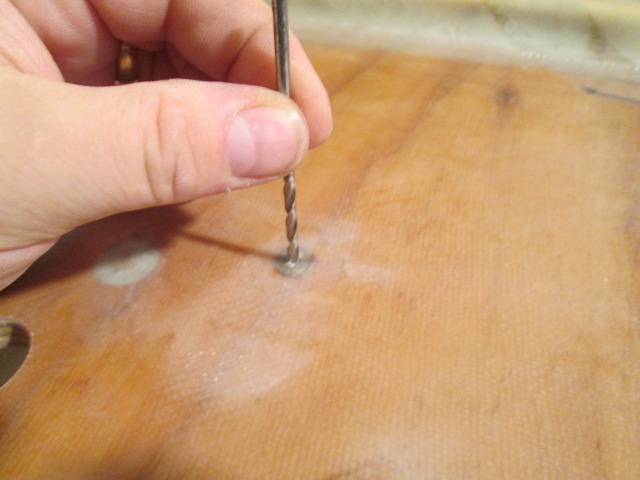
The center mark.
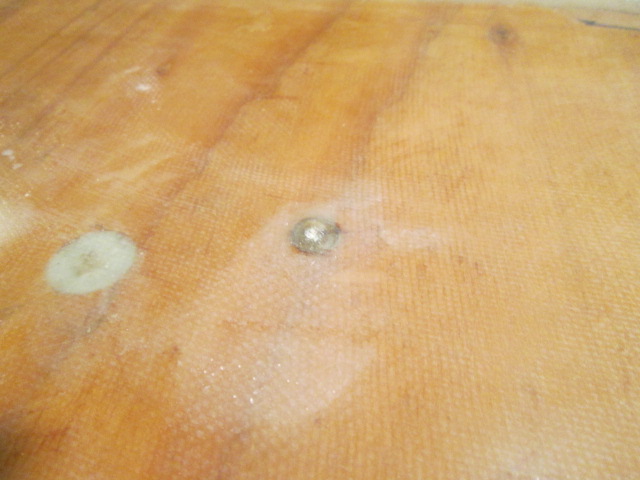
Being that the plywood floor of the box is only 1/2 inch, I didn’t want to accidentally drill thru the inner skin if the drill happened to catch, so I made a stop block for the pilot drill.
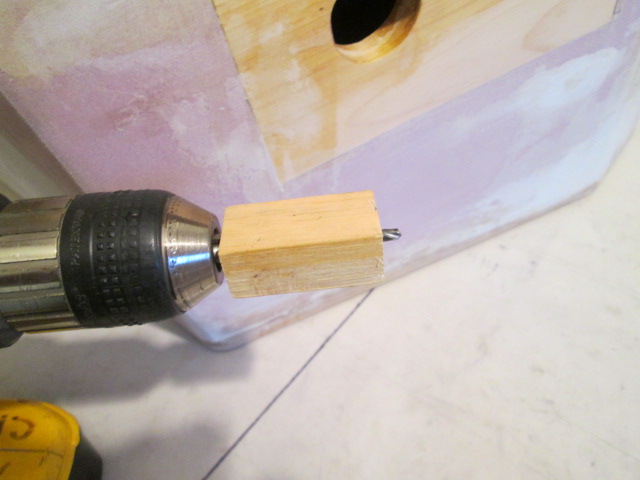
Then drilled out the center mark.
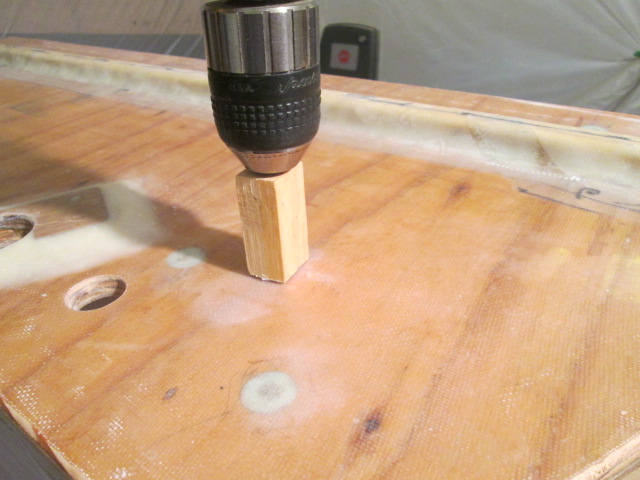
Then I drilled up to 1/4 inch exposing the stretch wrap packing.
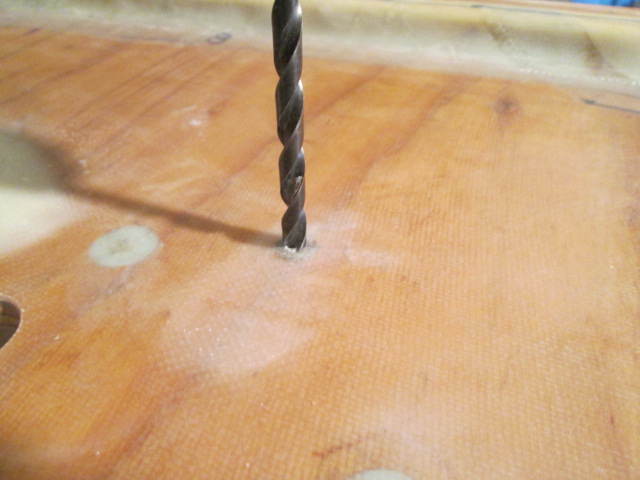
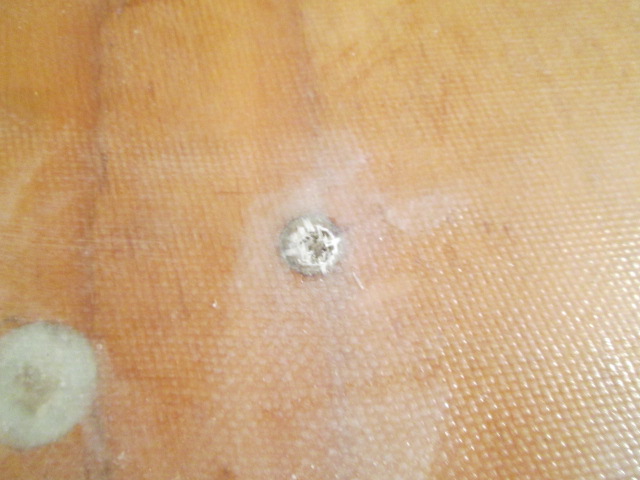
Next I used the spike on the compass and the tweezers to pluck the stretch wrap out of the hole. This took a little bit of doing, but in the end the results were well worth the small effort.
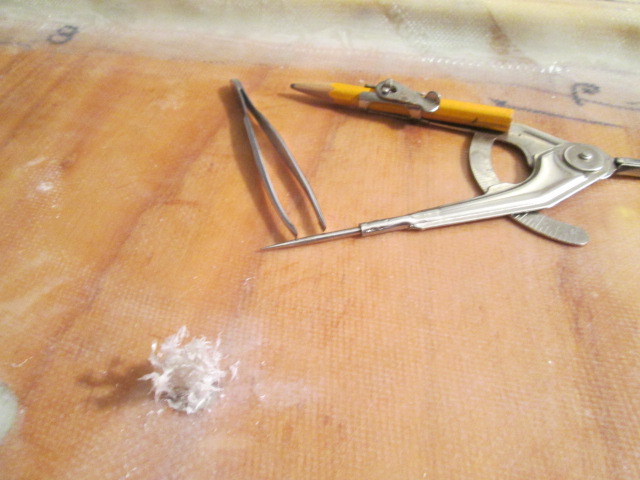
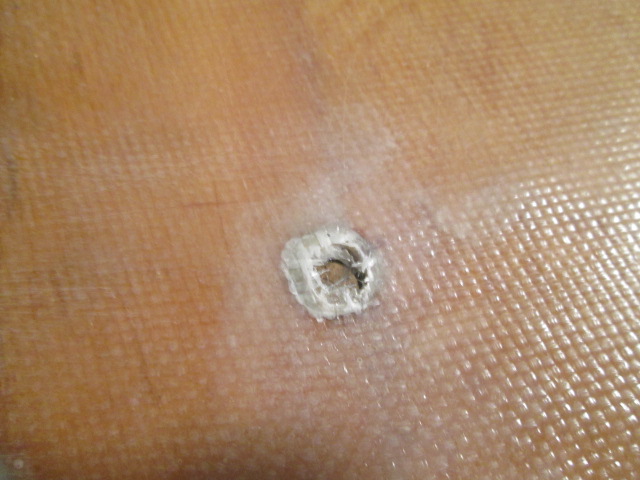
A larger drill bit and a little hand twisting started the deburring process.
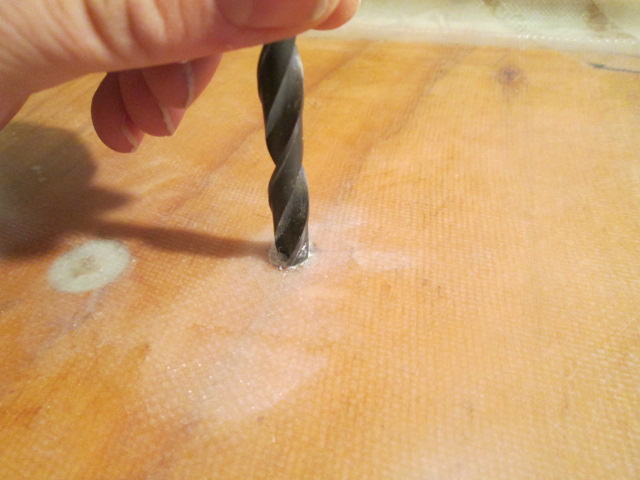
Then I laid the bit over and used a little more twisting going around in a conical orbit to clean up the edge.
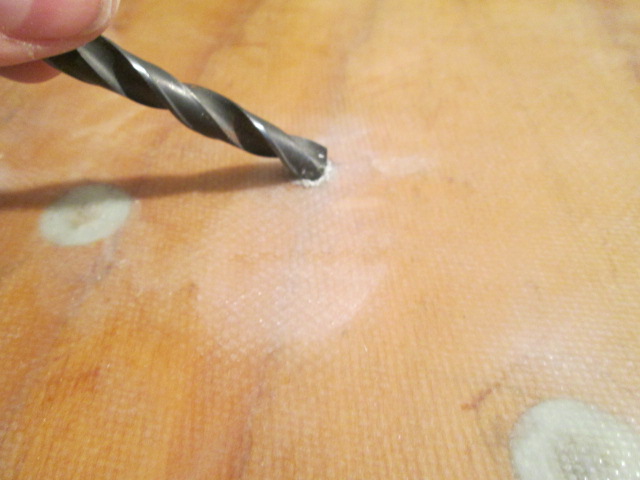
Later I found that a nice sharp blade in the utility knife, used in a downward angular/circular slicing motion worked even better.
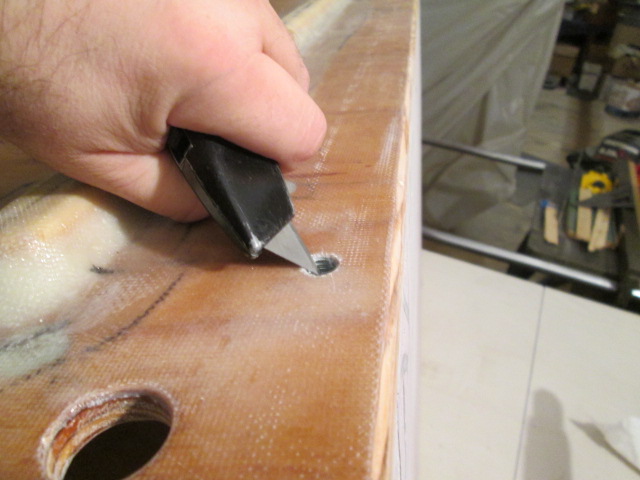
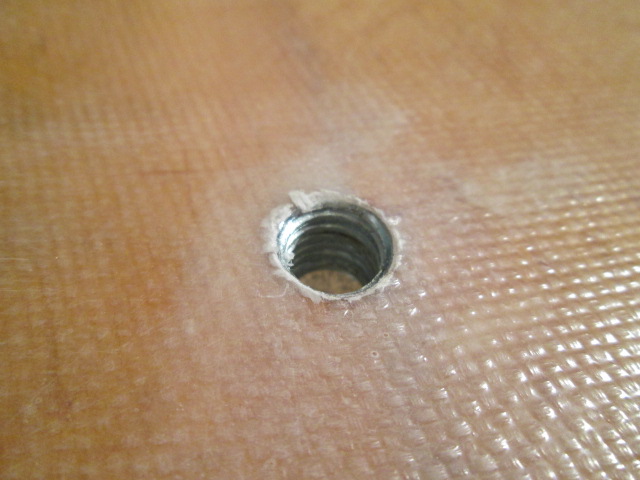
Finally, I used a little scrap of 100 grit sandpaper to finish things off.
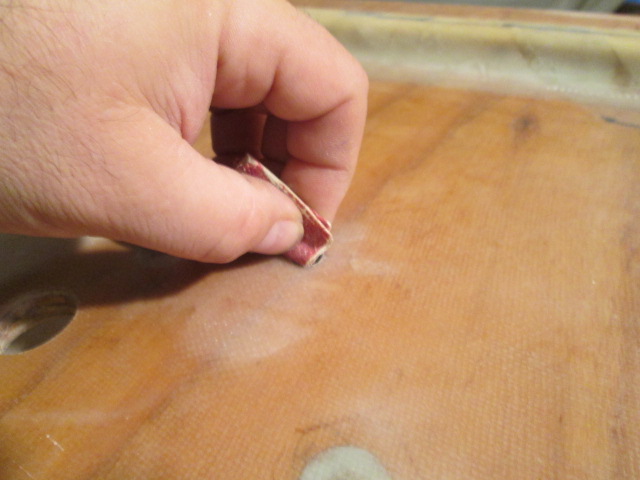
The finished hole turned out as well as could be expected, which was very nice!
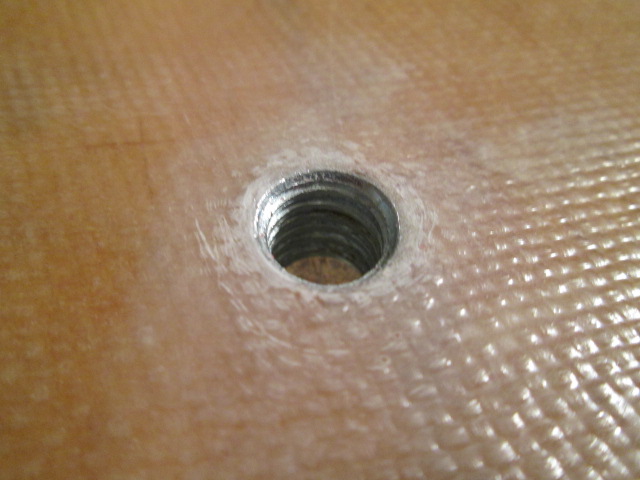
The studs on the rubber mounts were 3/4 inch long; too long for the 1/2 inch ply; so I spun a nut on each and sanded the tip back and re-chamfered using the Bader belt sander. I took care not to overheat during sanding, so as not to disturb the rubber bond.
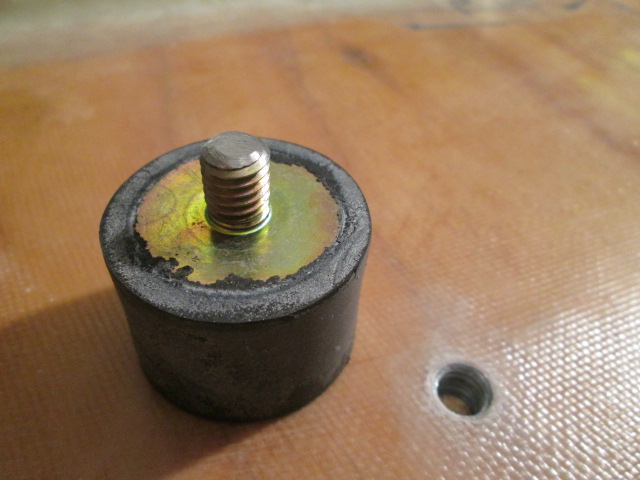
This allowed the mount stud to fully engage the T-nut without poking thru or lifting the glass layer on the other side.
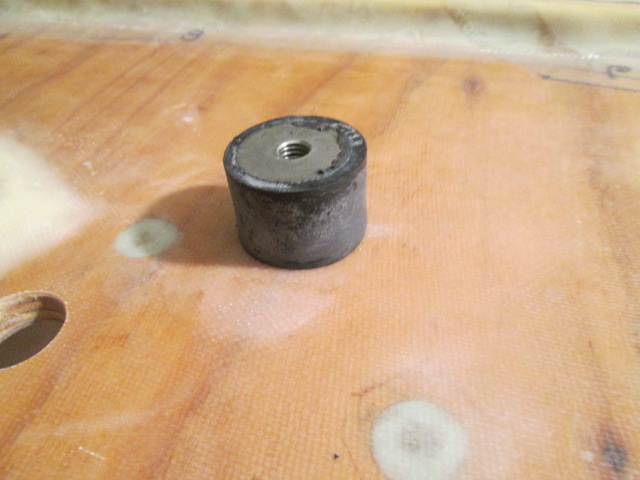
Wash, rinse and repeat three more times and we have rubber mounts all ready to go. I’ll take them back off to paint, but for now it is nice to have the box standing on its own four feet!
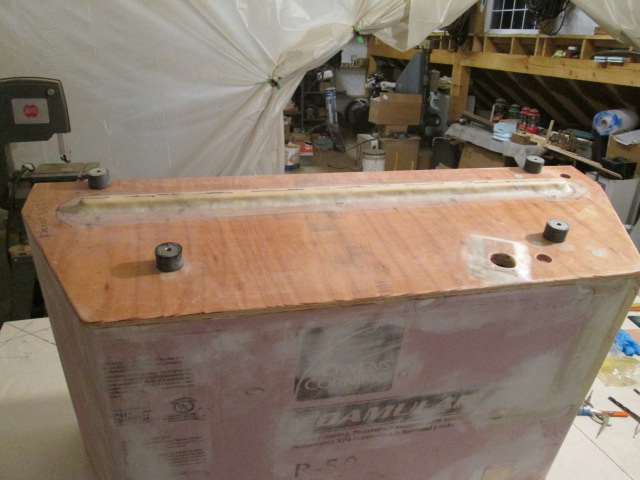
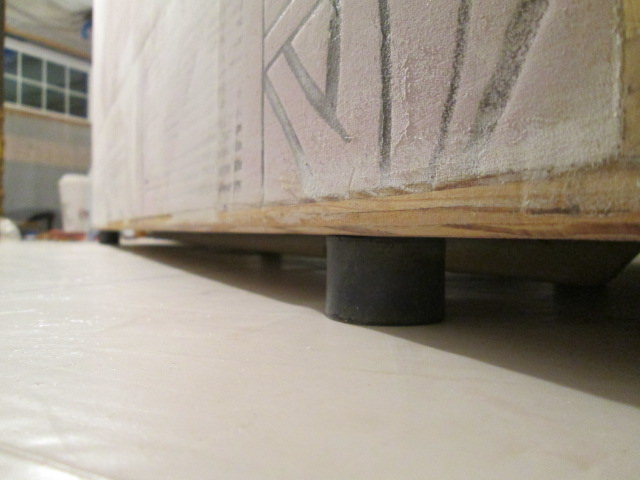
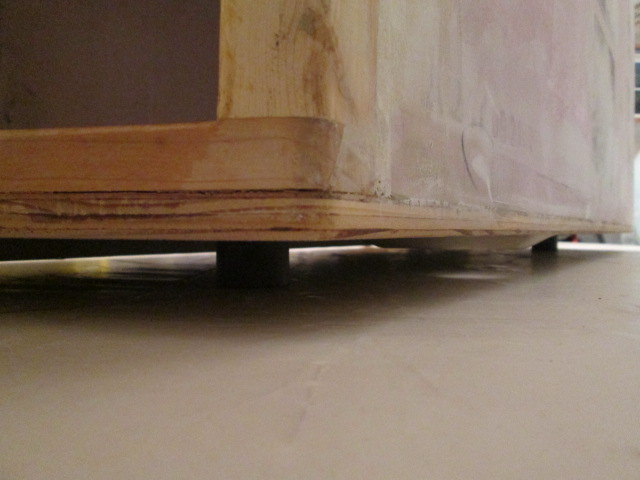
I like how easy it was to trim the bottom glass on the TB using the relatively crisp corner as a guide, so I think I will glass the rim and back next, then use the hard surface of the cured back as a guide for the round over bit bearing and radius the rear corners of the box for the front/side layup to wrap onto the back easier. That’s the plan for tomorrow.