It has been a slow February.
On Monday I wanted to get some cabosil to try, but Defender was kind of out of the way. I stopped at a couple of marinas along the way, neither panned out; it would have been quicker to have just bitten the bullet and made the trip to Defender.
From there I stopped at the house to get the glues that I had forgotten. Then it was on to Goodwill to get a smaller spoon for dishing out fillers. The spoon I have been using is like a small serving spoon or a very large soup spoon, shown here with the new sundae spoon. I picked the sundae spoon because it is small, like a teaspoon, but has a long handle which should make it easier to get to the bottom of the filler canisters. Gave 25 cts. Should help keep me from adding too much filler per batch.
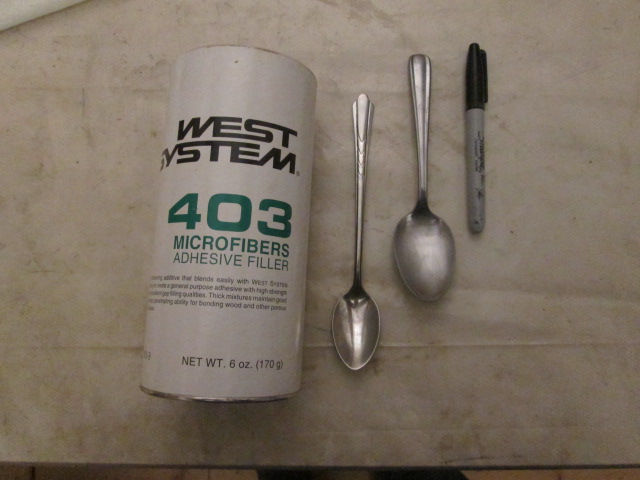
While there digging thru the spoon bin I found a good set of SS measuring cups, and a set of SS measuring spoons, just like mom’s old reliable ones. I prefer the SS over modern plastic because it doesn’t get scratched up and can’t melt. The long rectangular shaped spoons fit into herb and spice containers easier. I haven’t decided if I will include these in the trailer galley stuff because I won’t necessarily be doing the kind of cooking where careful measuring is called for, but the vintage nature of these appeals to me and I couldn’t pass them up for 99 cts each.
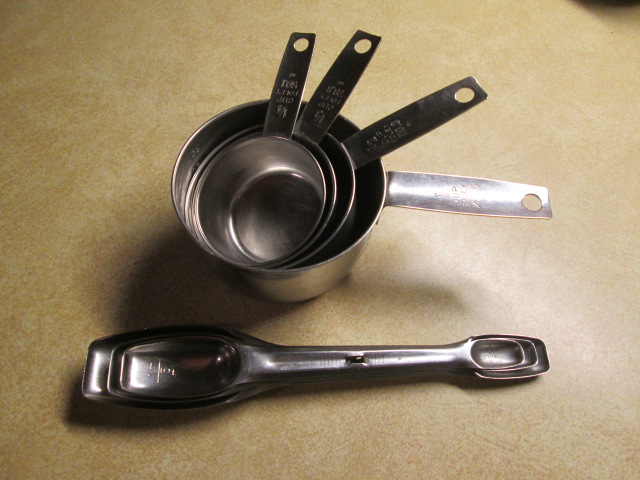
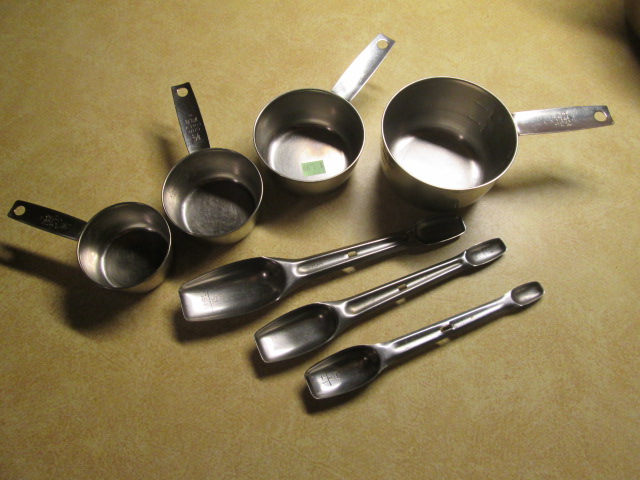
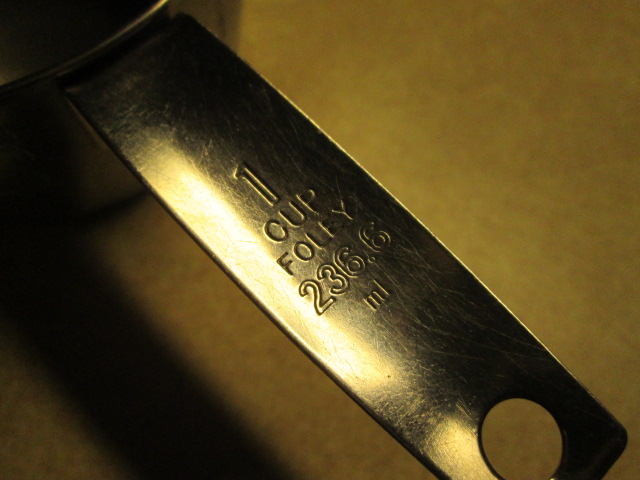
Got to Mecca and ended up chit-chatting with Karl. Didn’t even make it up to the loft before heading back home.
Wednesday was a tiring day at work and I went home and took a nap; a long nap.
Thursday I didn’t get anything of note done. Friday Yvette and I went out after work and bought a new dishwasher.
So that brings us to today. At midday it was still only 34 deg F in the loft, despite forecasts in the 50’s. Inside did eventually reach that with solar gain, but outside was still pretty chilly. I figured the 5 minute epoxy would be fast enough (turns out that it is actually 3 min, but I’ve been calling it 5 min for so long I don’t see any reason to change), so I mixed up a small batch with some of the 410 fairing filler and did a final round of touch-up on the street side under floor screw heads. Karl gave me a little bit of a hard time for “body working” under the floor, but my argument is that if I leave dips and voids that the under wrap of glass from the side skins doesn’t want to suck into, then there would be a potential weak point that water could take advantage of.
Once that was done I set about making a pair of caul style dogs that bolt to the middle pair of chassis mount holes under the rear of the galley floor. These will allow me to dog the hatch down tight against a pair of shims, locking it into the proper position and shape, and yet remove the draw latches so that I can glass under their location all in one go with the side walls. I ripped these from a scrap of pine barn board, about 7/8 inch thick rough on one side. The extra spacer accounts for the length of bolt that I was able to scrounge. I left the longer piece of wood a little long leaving room for wedge shims to tighten them up. The hook or tab for the wedge shim matches the angle of the bottom of the hatch (the “bumper”).
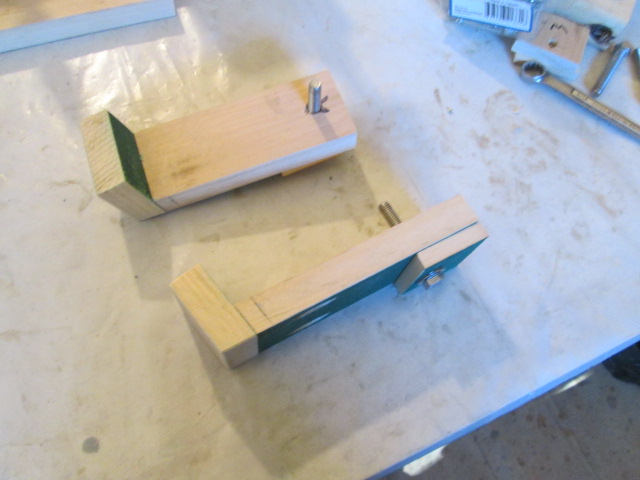
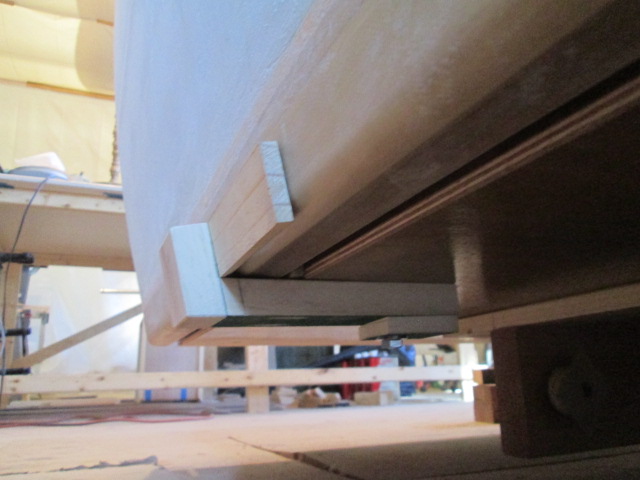
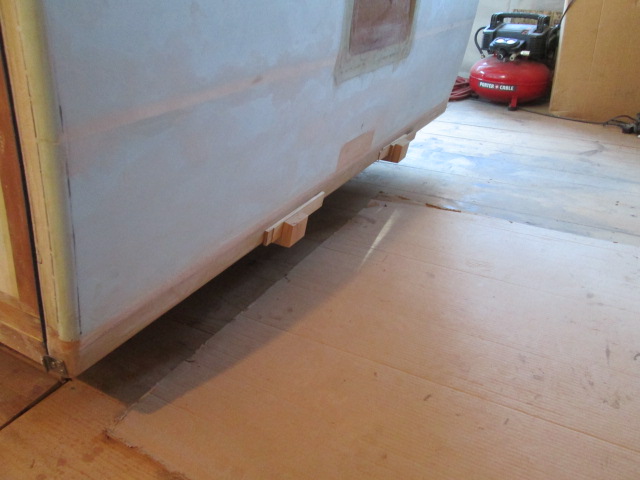
Next I wanted to mark guide lines along the front, roof and hatch to help line up the fiberglass overlaps and seams. I used some more of the barn board to make this marking guide. It squares off of the side wall and glides along as I hold a sharpie in one of the notches cut with the utility knife. I did a quick round over/bevel on all of the sharp edges so that it would glide over the foam more easily and not dig in.
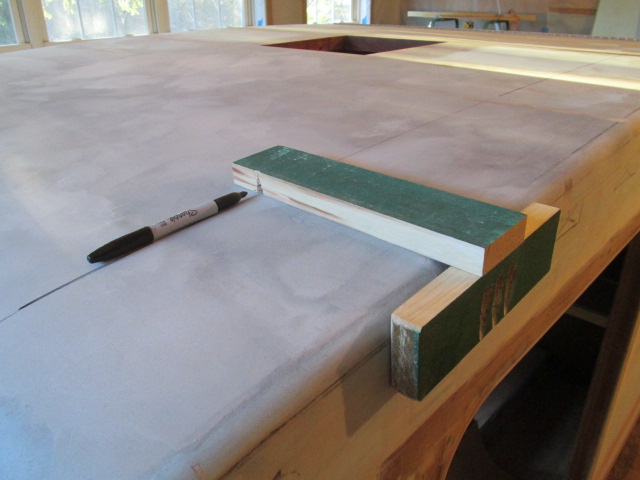
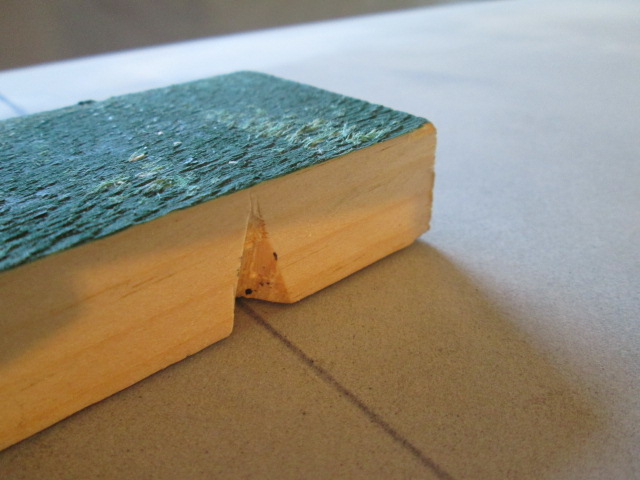
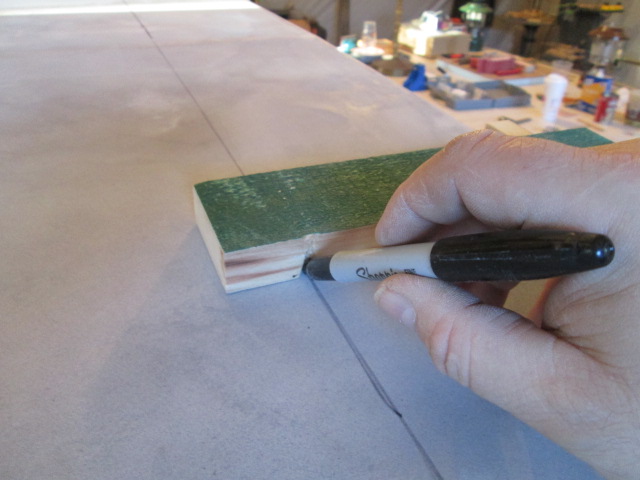

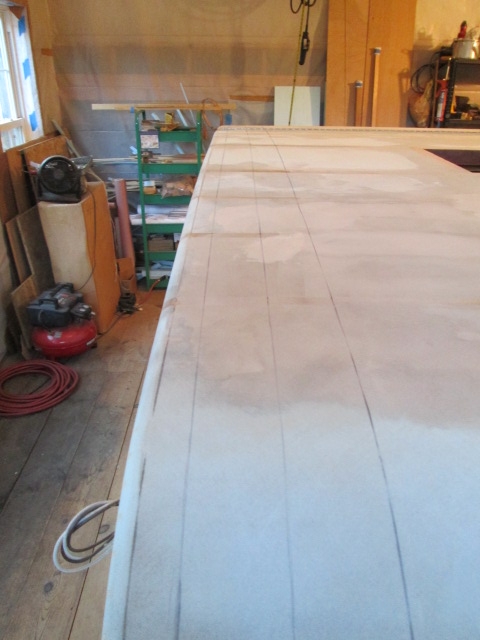
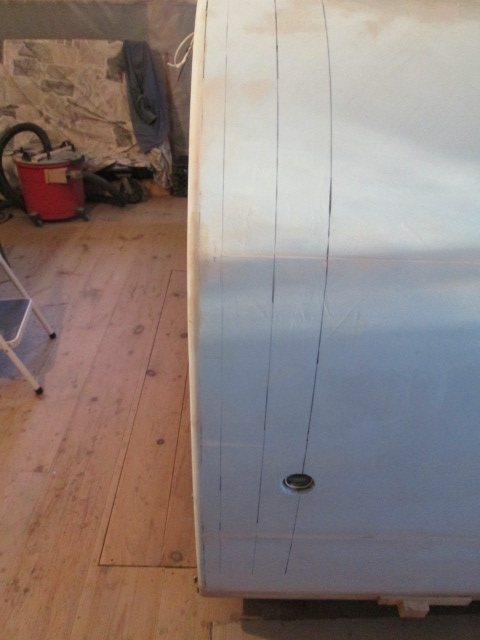
We’ll come back to this in a second.
Next I masked off the hatch hinge. I had already glassed under it and on to the adjacent sides a bit, but I still don’t want to slop epoxy onto it.
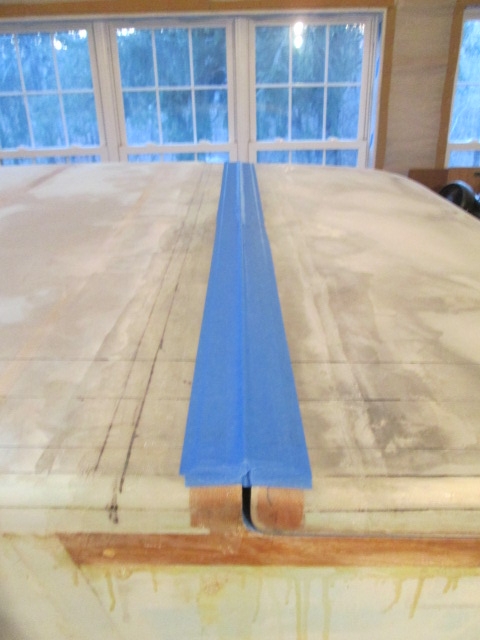
Back to the marking tool, I suddenly realized that I had screwed up, but “caught it in the audit”. I had hooked the measuring tape under the edge of the floor, strung it out and wrapped it up onto the roof at the crown of the big arc. I took 4 inches off for the under wrap and marked the roof at the 60 inch mark. Well, 64 inches is the width of the camper, not the width of the FG cloth. The cloth is only 60 inches wide. So I had to re-jigger it. By changing to a 3 inch under wrap I was able to reuse the second line, abandoning the inner most line on the roof, and made a new line between that and the outermost line. Even though I will layup the sides and roof separately, the idea I’m going with is to stagger the plies so that the first side ply ends where the first roof ply will end, which will in turn over lap the second side ply. The second roof ply will overlap all others. By doing it this way the total ply count at the seam will only be three, max, not four, so it should be easier to fair. By having the 2nd ply of each layup be the longer one it leaves only one rough edge, not two, and if I use the plastic peel ply trick it should make a nice transition with less sanding. Here is the corrected layout with about 1-1/2 inches of overlap per line; 3 inches total.
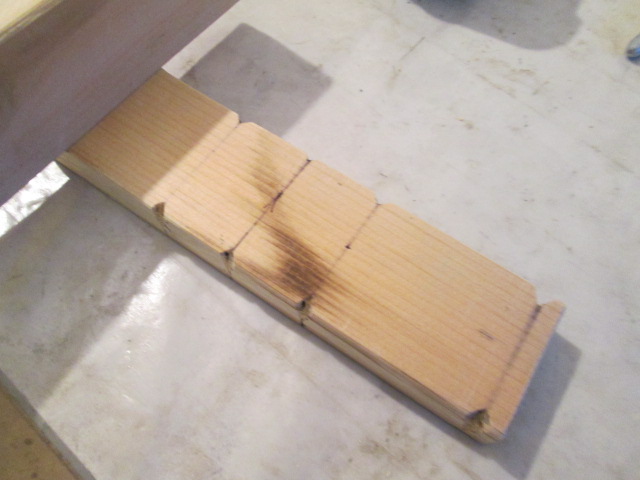
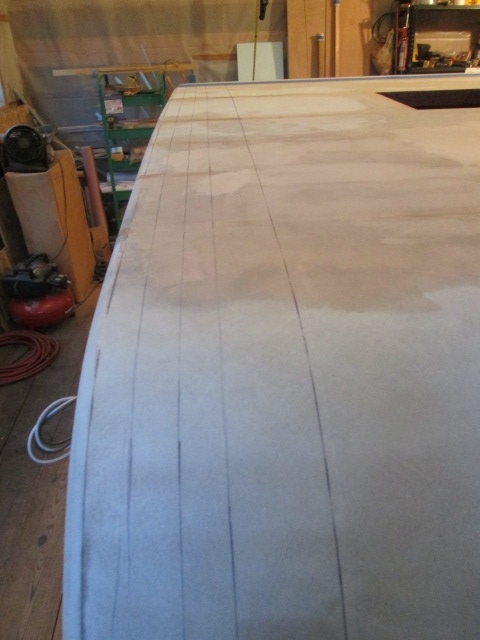
One last little detail, after removing the draw latch tabs from the ends of the hatch “bumper” I stuck the sharpie tip in each hole and gave it a little twist. The little bit of black ink surrounding the holes will make it easier to locate them when it comes time to drill thru the cured glass. You may also notice that I used a slightly thicker shim to increase the seal gap a little making it easier to get the steak knife in there to cut the hatch away later.
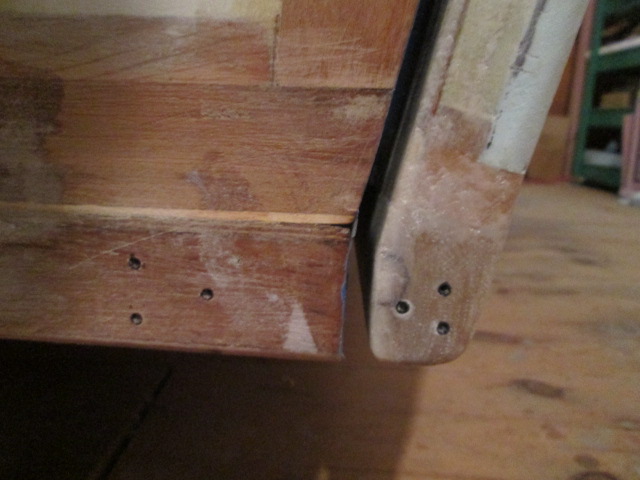
Next move will be figuring out how I want to wrap the front locker bump out. I’m thinking I will start there with a single ply, since the locker is pine and the area around it will be armored up with aluminum rock guard.
Tomorrow doesn’t look good for doing a major layup. The weather might be okay, but in the morning I will help my BIL press some bearings into the trailing arms of their commuter car. I might have enough time to prep cloth for the front, and then we have an early evening dinner reservation to celebrate mom’s recent B-day. I’m looking forward to that (num-num-num).