Okay, yesterday I milled out the bolt openings in the door latch plates.
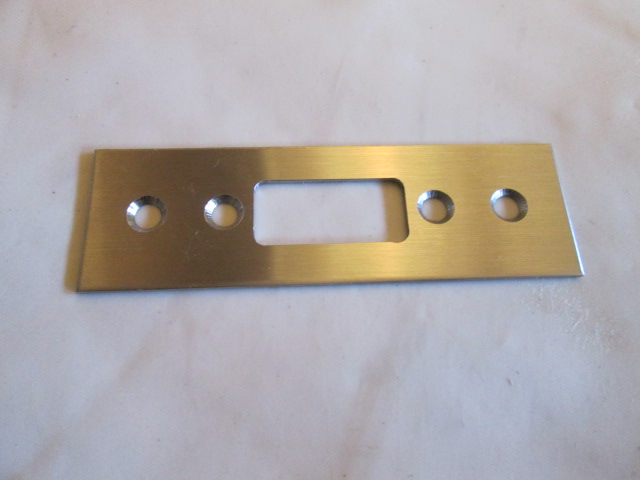
If you look closely at the above pic you can see a little snipe in the lower right corner. In making the several laps around the cut using the small 3/16 diameter cutter and just taking a few thou each turn, I accidentally turned the handle on the mill the wrong way… but the good news was that after taking this pic, in a dry fit with the latch I found that it wanted a little more clearance with the bolt, so I put it back in the mill and shaved that edge back and trued it back up.
Here’s another dry fit to the latch after cleaning the edges of the opening up a bit…
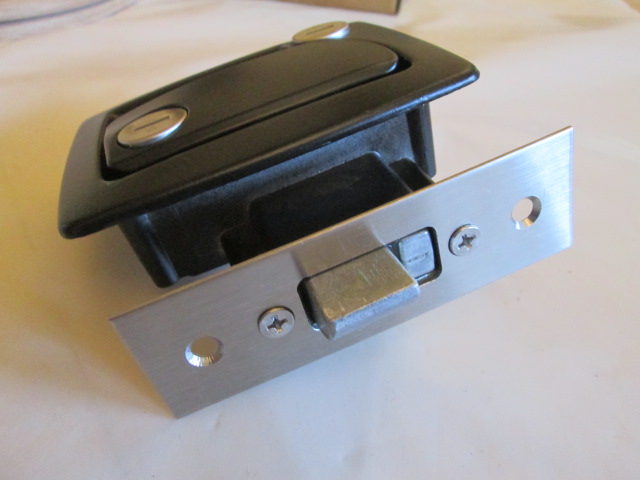
…and a quick mock up with the door. I would much prefer to recess the latch plate in a mortise, but I hadn’t allowed for that when I fit the latch and it would take more time (…Tony Latham’s advice to get camping ringing in my head…). I’ll leave that for another time and the 5/ct incomplete category; I can come back and change it later.
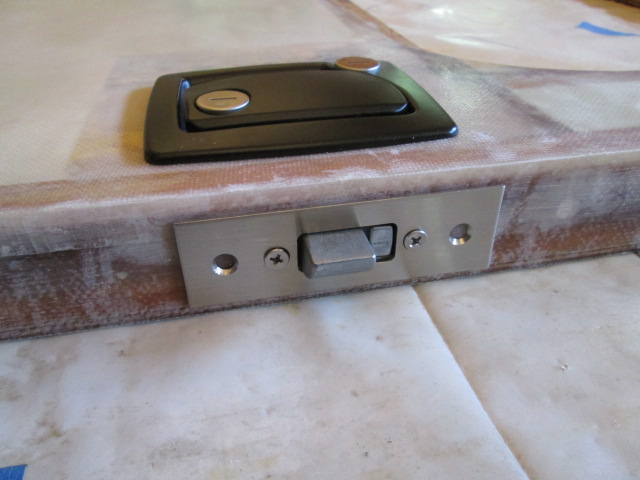
Qty (2) req.’d
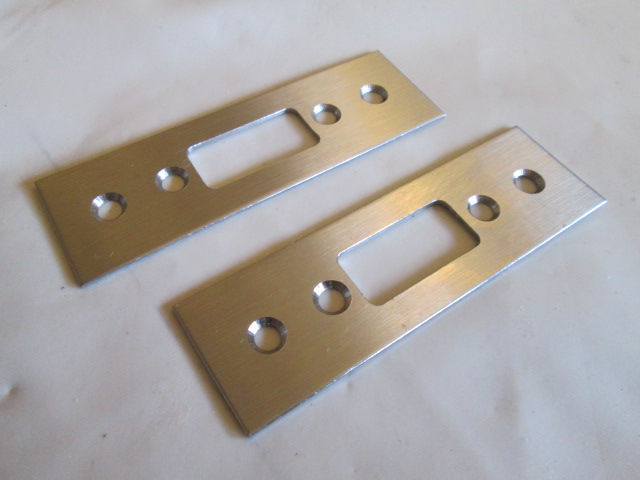
I also drilled and countersunk the screw holes in the strike plate blanks, but on the second one I got a little carried away and ran the countersink too deep; so today I roughed out two more. I did two more because it was different stock; although it is all .060 No. 2 brushed, sometimes the finish can be slightly different from different manufacturers and/or different lots. Plus this way we have one to screw up when working thru programing the mill. Shown here again with the jig, the SS comes brushed on both sides but with a plastic film on the “good” side to help protect against scratches in handling and fab.
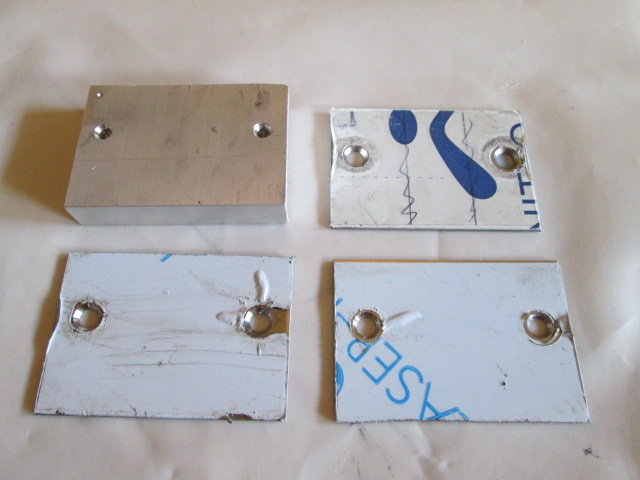
The newer strike plate blanks were just saw cut so I left them a little large to make sure that the profile milling has something to clean up. On the shear cuts we hadn’t thought to do that, but they have a nice clean edge anyway. (Karl wasn’t around and I have not been checked out on running the generator or shear, and it wasn’t worth the trip to work to use the smaller shear there, so I just cut them out of a drop strip on the big Marvel saw.) Here is one being test fit to the jig.
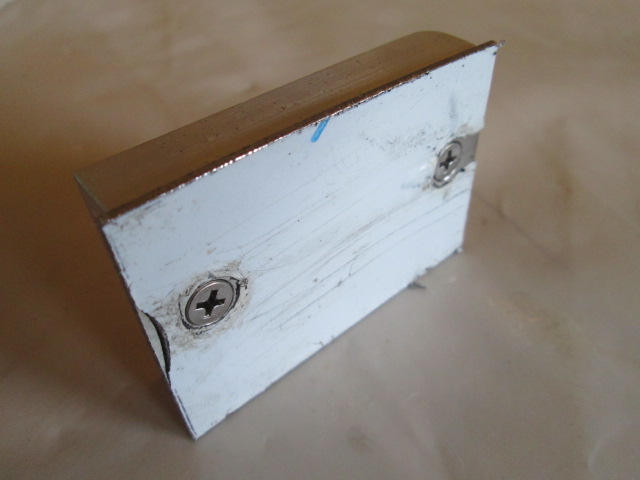
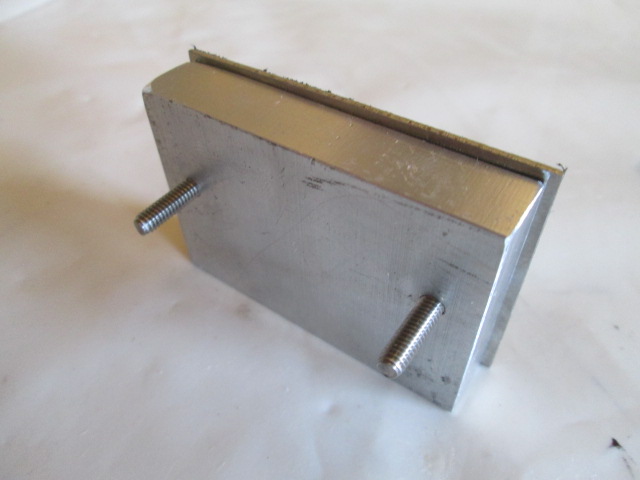
Still waiting for time on the CNC mill, I was looking for things that need to be done before filling the FG weave and getting back into bodywork (hot and humid and not looking forward to suiting up). Remember the T-nut inserts for the front shovel and axe mounts? The ones that I filled with wadded up stretch wrap and glassed over? Looks kind of like this (the fuzzy white spots next to the black line on the left).
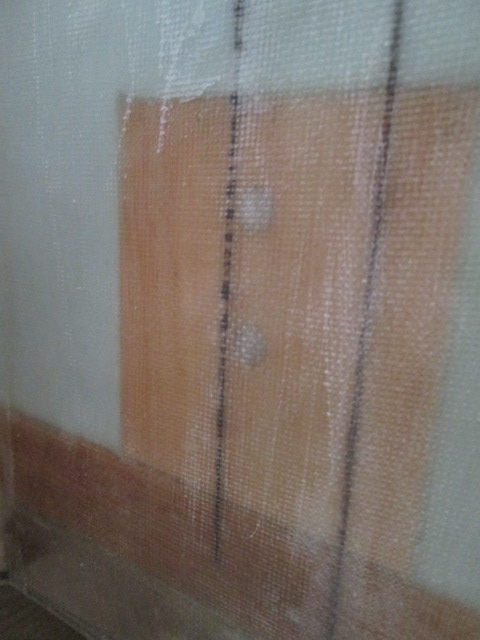
Time to drill those out before they get lost. I started with a small drill bit and just eyeballed the center, then stepped up to a little bigger bit. From there I used the utility knife kind of like a deburring tool gradually trimming the edge of the glass out until it met the edge of the hole in the wood blocking (being careful not to cut away the epoxy saturating the wood). Then I used a small pair of needle nosed pliers to twist and pluck the stretch wrap out of the hole, and cleaned up the edge with a little twist of fine sandpaper; shown using one of the mount bolts to verify that the threads were still clean.
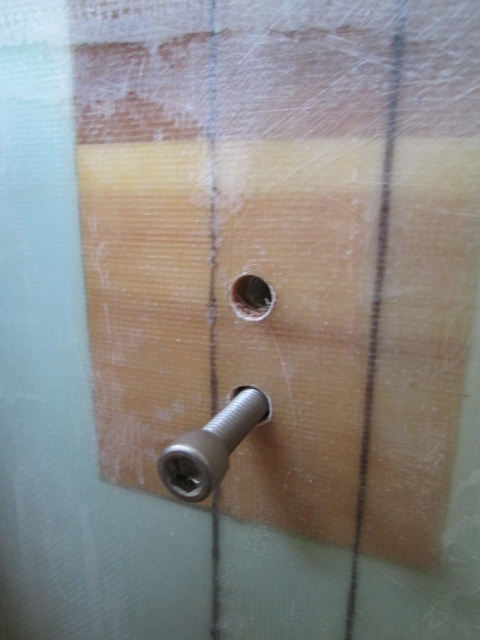
Still avoiding epoxy work and PPE, back to the door latch hardware, I used the screw shearing feature on my wire stripping pliers to trim the latch screws from 1-1/4 long to 1-1/8. This gave the pliers a pretty good workout shearing SS screws, but they are a nice quality Klein set so they did a good job of it. Also note that when I went to get the remaining screws needed I found that they had them in the oval heads, so I got enough to do all eight (plus some shorter FH’s for the latch plate screws).
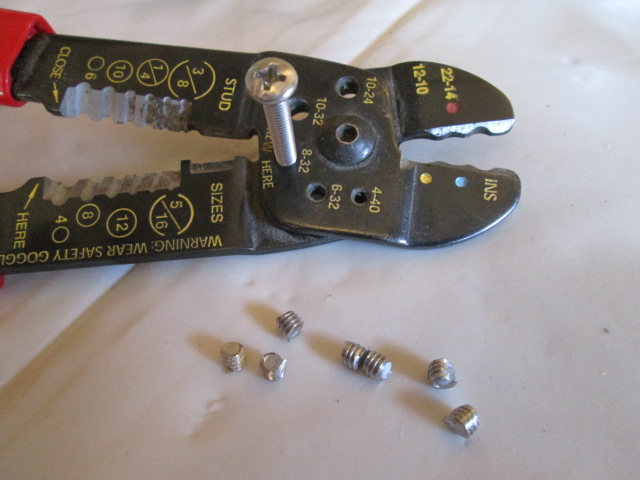
By turning the screws in until the tips were just flush with the back of the pliers I got nice consistent results.
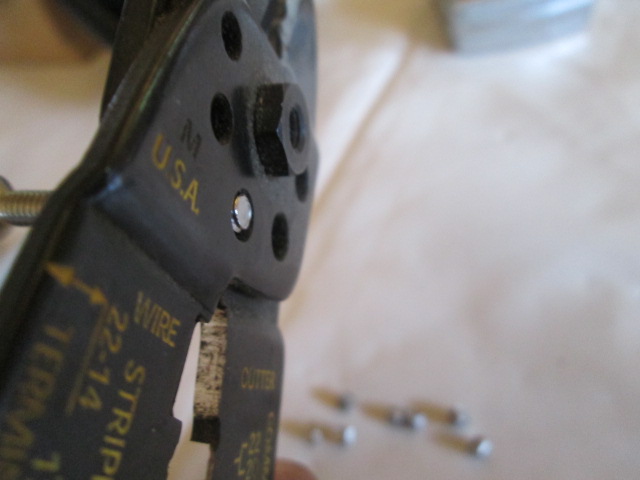
Careful inspection of the sheared tips was needed because any rolled or deformed thread here would wipe out the soft thread in the white metal of the latch casting. Here is the jagged edge of a screw, followed by one that has been filed smooth using that little ultra-fine file I got at the tractor swap.
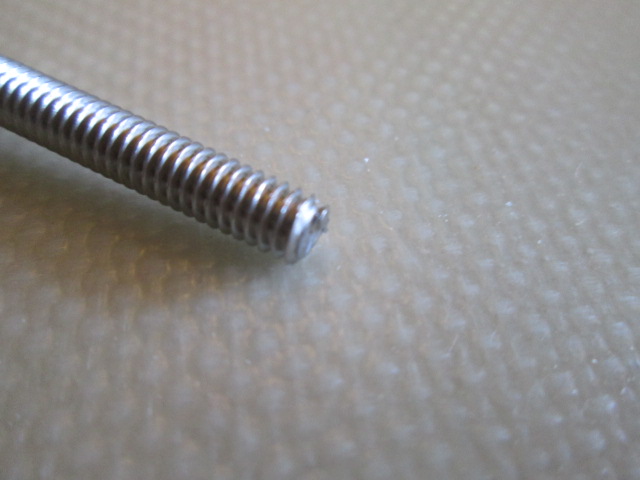
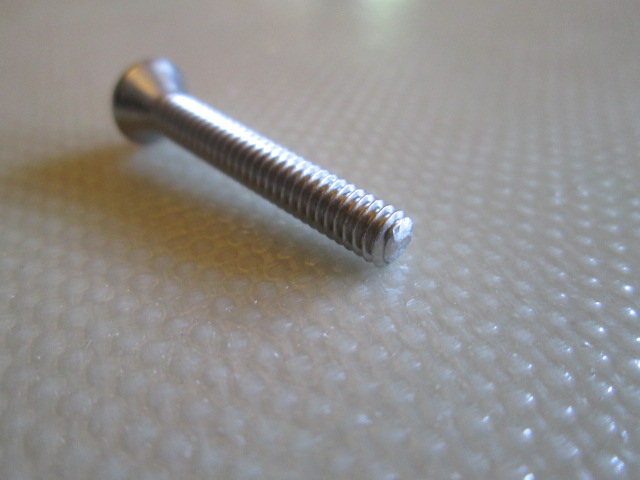
Details matter.
Finally, I fit the latch plates and latches, drilled and set wood screws to locate the latch plates, and assembled the inner latch paddles to the doors (just a dry run for now).
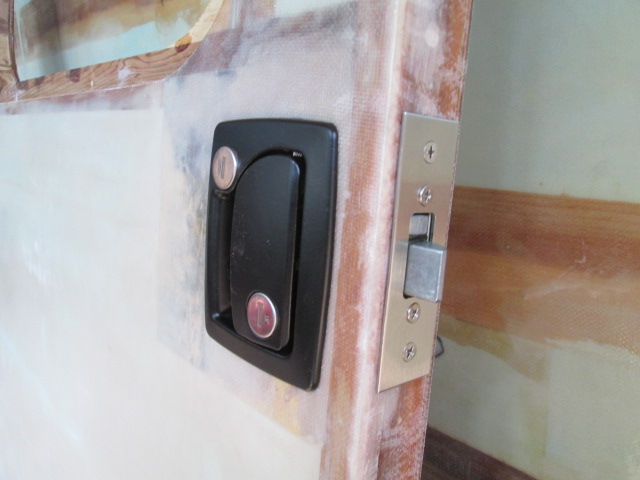
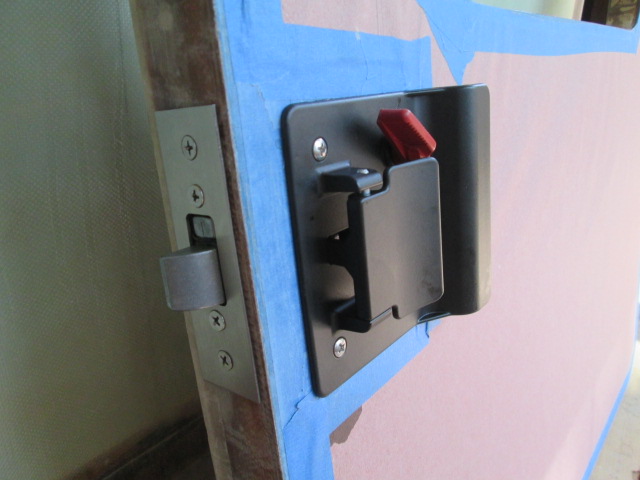
Here’s the same shot with the deadbolt extended.
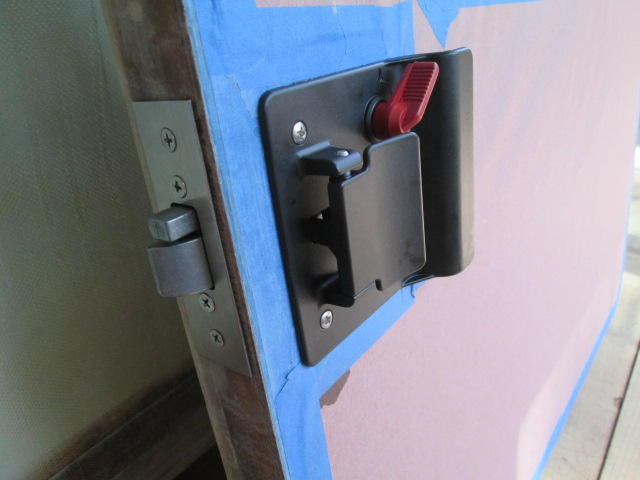
That felt good to get behind me, the whole issue with the short screws and ugly OEM latch plates. I may still mortise these in, but for now I’m happy with them.
I need to figure out what I will need for sheet aluminum for the TB lid, rock guards and fenders, and get that on order. I’m running out of things to do to avoid bodywork!