Yahoo! When I went to download Saturdays photos, Friday's lost pic's miraculously appeared! Yippee!
So this may get a little disjointed as I will attempt to retell the story with pic's, plus I took new photos to fill in the blanks, so they might seem a little out of order. Not to mention that I completed the dado and rabbeting of the wall door frames today, so those will be in order of task done.
Karl had jumped in and rough trimmed the floor bottom skins using his cordless Makita panel saw. So when I was ready to trim the top skins he jumped in again. This time he went around and traced a reference line equal to the thickness of a carpenters pencil. He indicated that having the line would give him more confidence to hold the line and less concern about accidentally under cutting the floor proper.
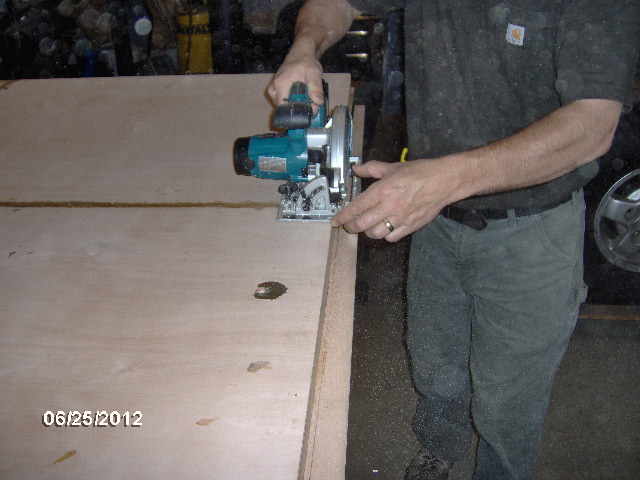
Sawdust, ya think?
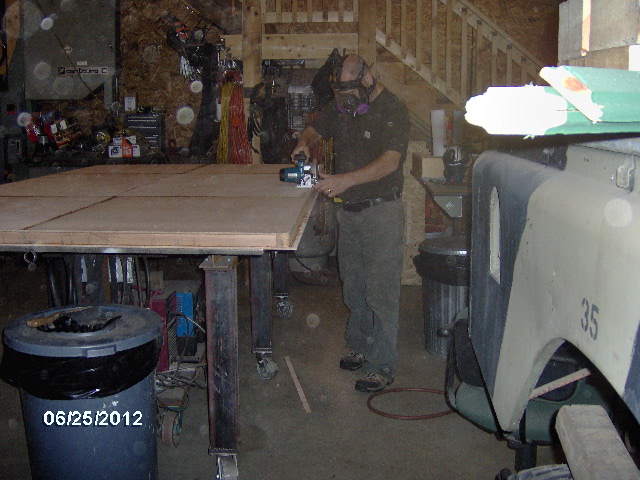
Note Karl's full face safety shield/respirator. He learned long ago that metal work is bad for you. PPE, just wear it!
Here's a closer look at the pencil mark. Again, the top skin is down so that the saw blade cuts up into the presentation side; less splintering that way.
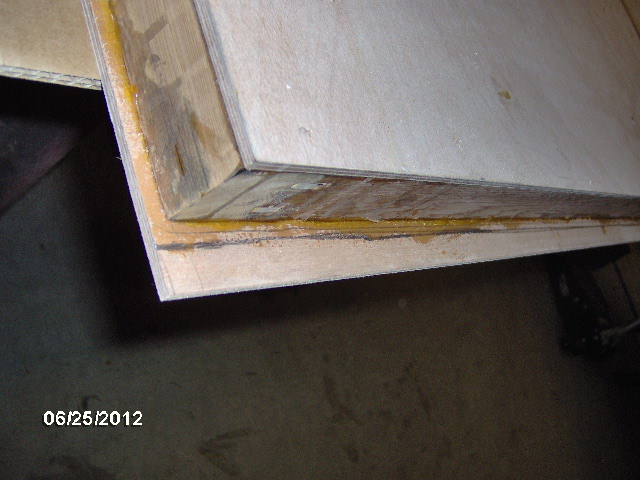
Okay, here is the floor with the top skin rough cut and flipped up.
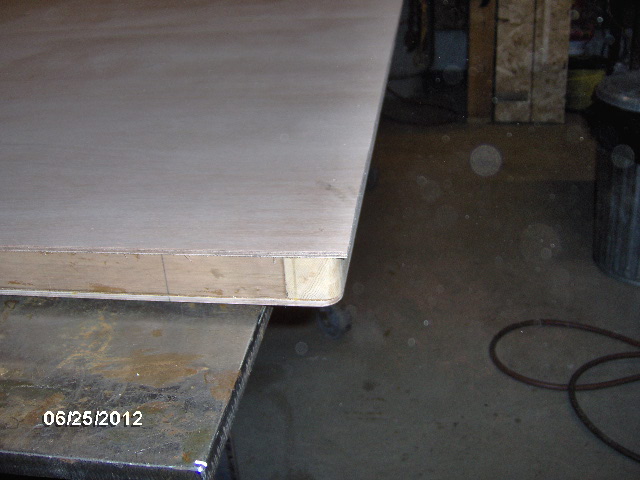
And a longer shot. I think it's time to clean the camera lens.
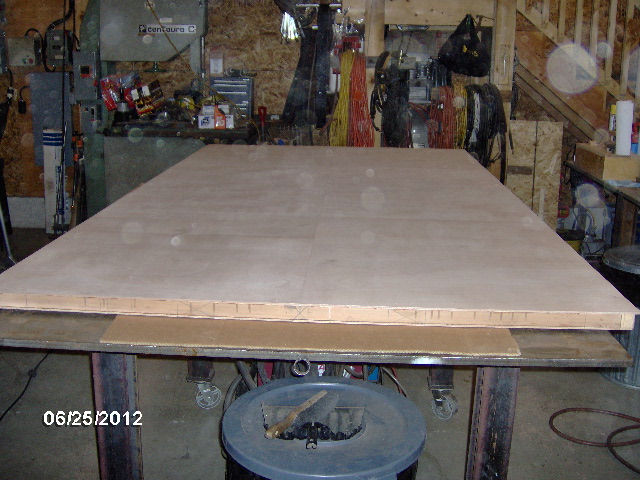
Next I routered the top floor skin flush to the outside of the floor frame (no pic).
Here's that nasty scarf lap on the bottom middle after I carved and chiseled away the loose flaps.

And here's a couple of close ups after sanding the roughness away.
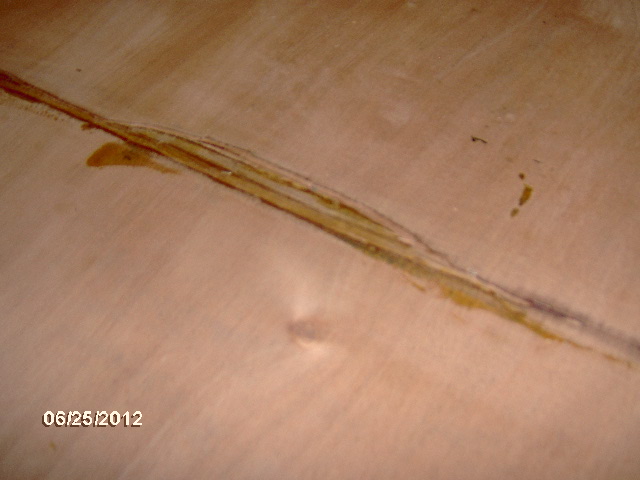
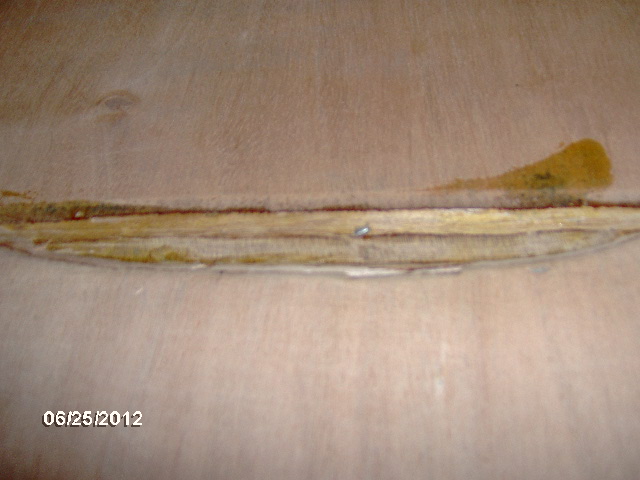

Bondo (polyester body filler).
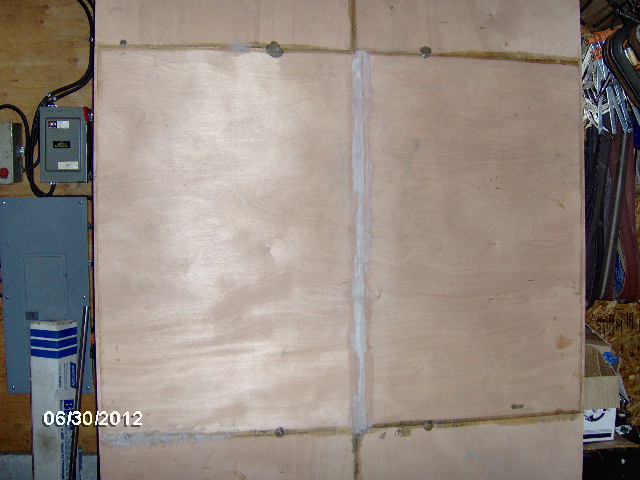
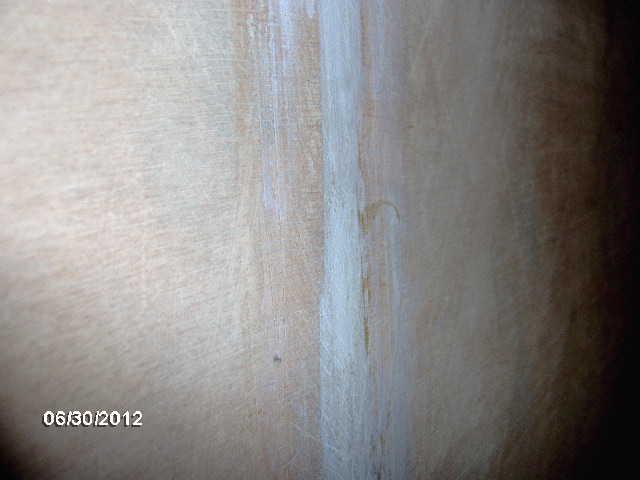
The dark rings around the mounting holes were caused by the wood glue dripping down through from the top skin and reacting with the steel table top. Should have put plastic down. I have also noticed that the cedar gets a blue haze or dye look when it reacts with the salt in my sweat (...not that I sweat much, not).
Here is the start of the galley bulkhead inner frame work (had a dry fit pic of the whole assembly somewhere, guess some pics are still missing).
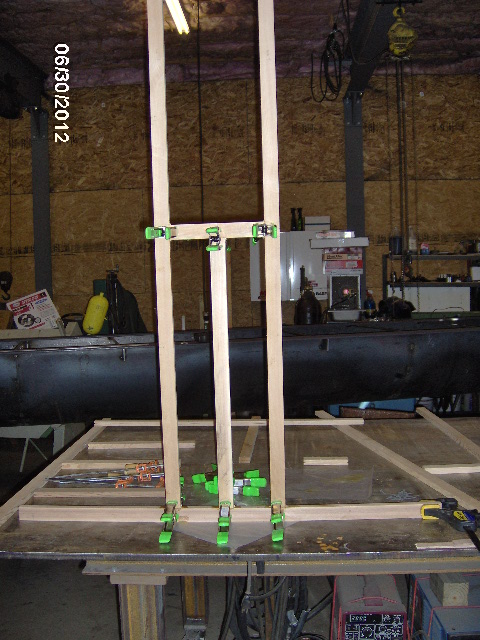
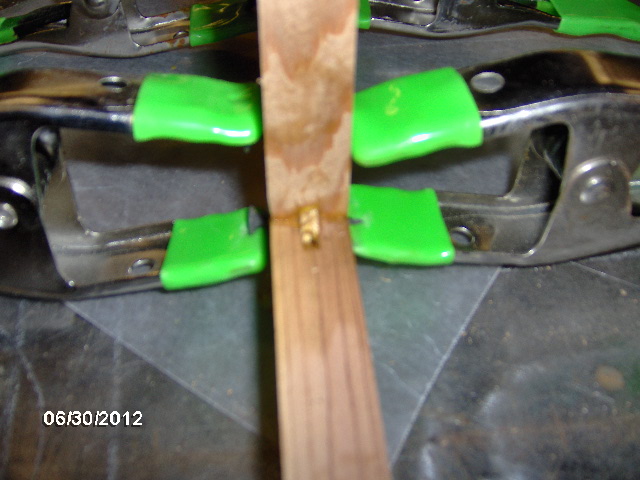
Using my drywall screw and spring clamp method, rather than long pipe clamps, meant that it could not lay flat on the table. Fortunately everything was cut very square so with the biscuits it was self aligning. If you look closely you can see that I used a single drywall screw sticking out both sides of the hole, rather than trying to drill multiple holes, or trying to screw two screws into each side of the same hole.
While the glue was setting up I got some more pics of the door corner block dado's. Here are the long rails, or sill plates, that go at the bottom of the walls (standing up in a corner of the shop with some unrelated drip molding).
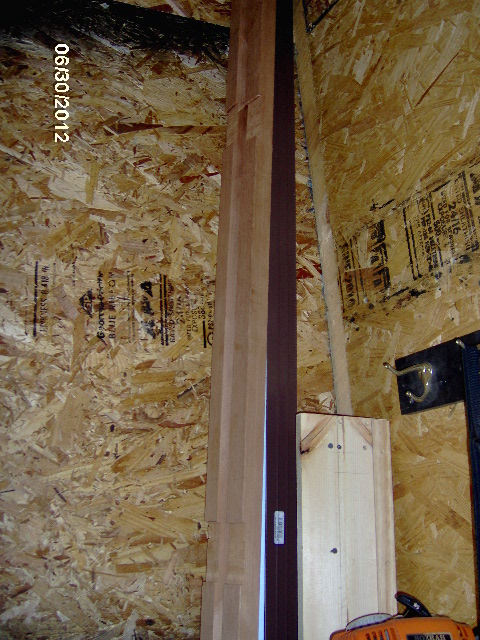
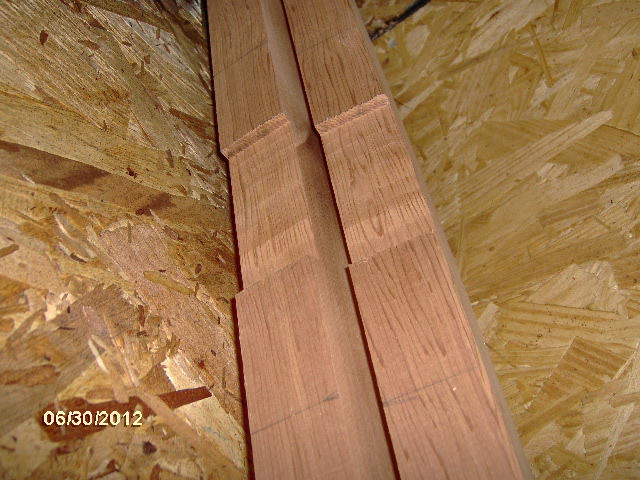
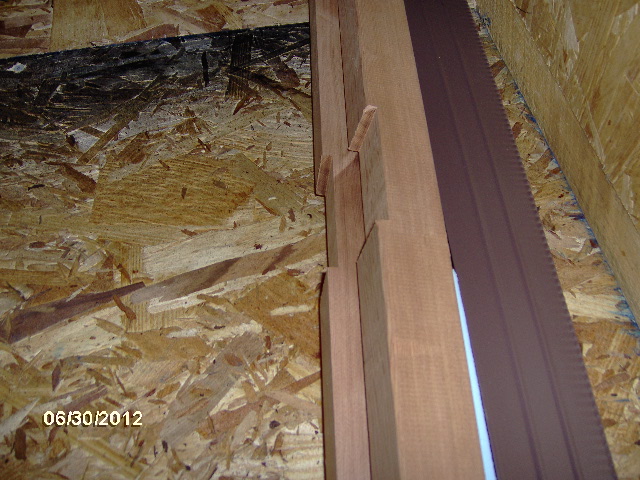
Here are the door headers (with dado's) and the door jambs (with rabbets).
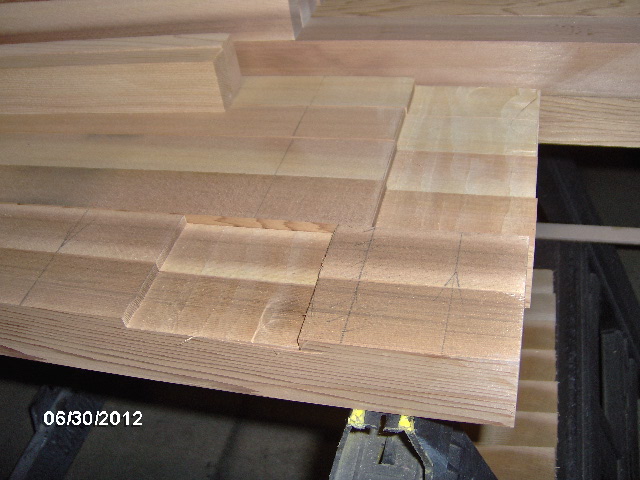
The door surround frame is a little beefier stock at 1-1/2 x 2 inch actual, giving plenty of meat to support hinge and latch hardware.
Here are the door corner blocks.
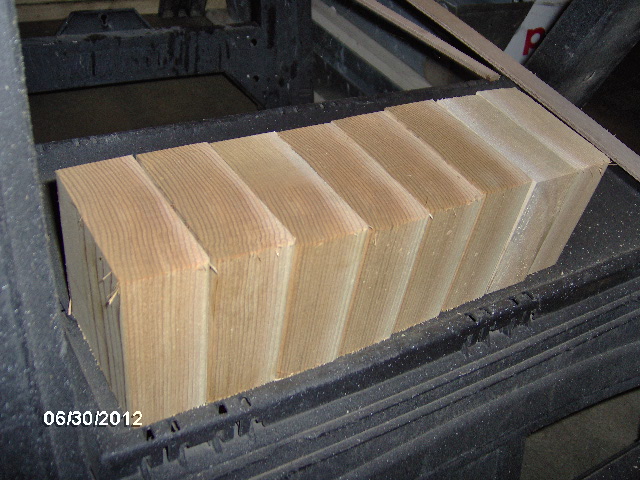
Ben's table saw is a joy to use! (echo, echo, echo...)
Okay, here's the set-up for rabbeting the door jambs. The quick square is clamped on to guide the router shoe. The door headers are clamped to the table on the right hand side to provide something the same height and support the far side of the router shoe, and I used the utility knife to score the edges of the cut to minimize chip out.
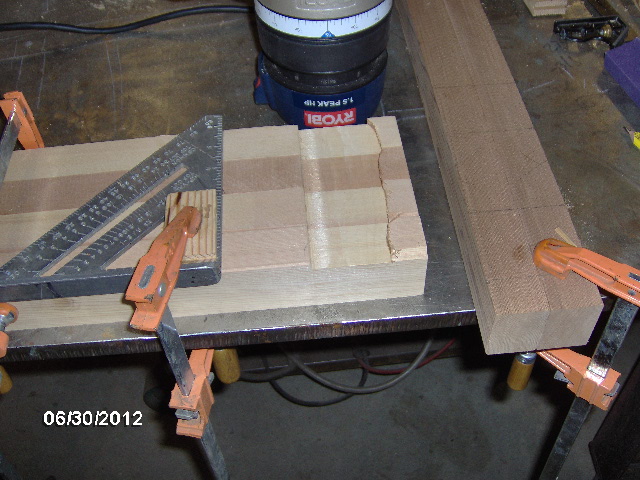
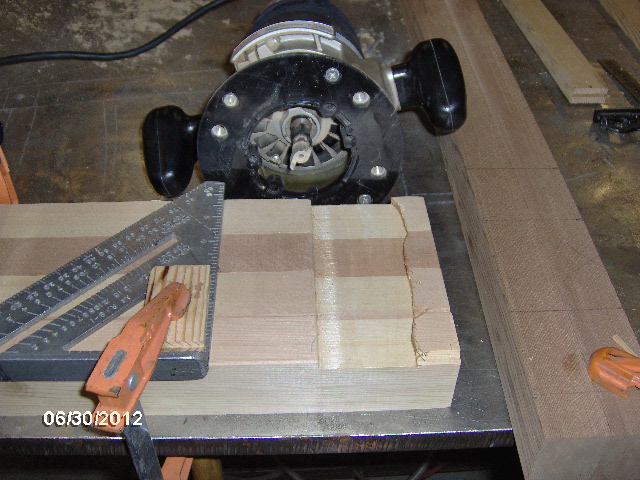
I found that the cedar cuts so easy that I could make the 1/4 deep cut in one pass, no need to make a shallower first cut.

Since the cut was wider than the offset of the router shoe, I would stop short of completing the cut and add this little 1/4 inch spacer (taped down so that the wind from the router didn't blow it away on approach), allowing the router to bridge the gap without falling into the hole and making a big gouge (not gonna show you how I learned that).
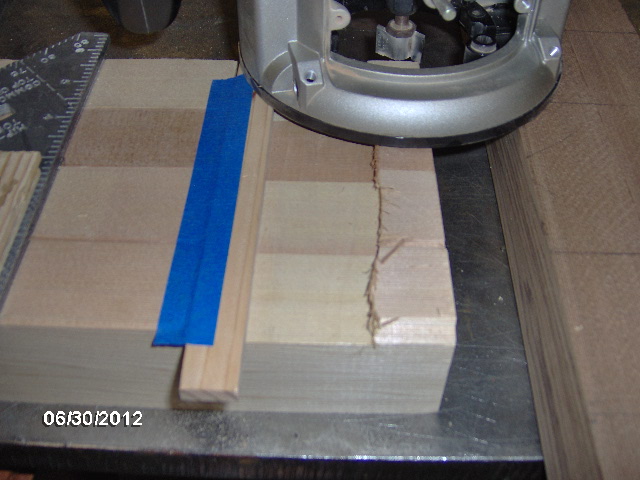
And here is the result.
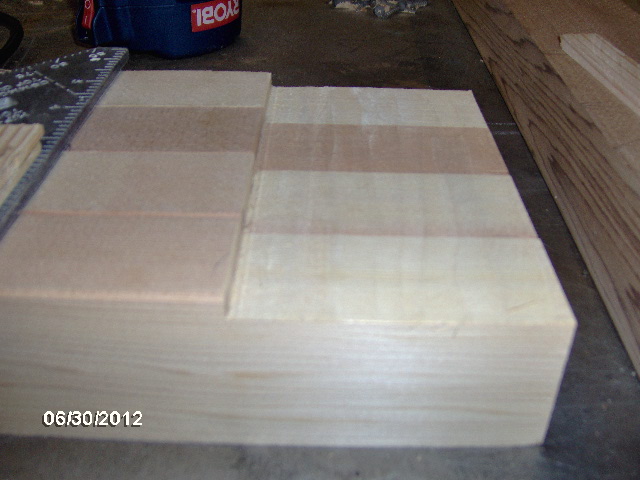
My cheap utility knife broke. The little nub that the blade hooks onto broke clean off of the thumb slider mechanism. Karl had one just like it, so I was able to continue (the long reach blade makes cutting foam possible, and makes it easy to reach in to cut biscuits sticking out, but that leverage is probably what broke it). I'll get another on my way to Mecca today.
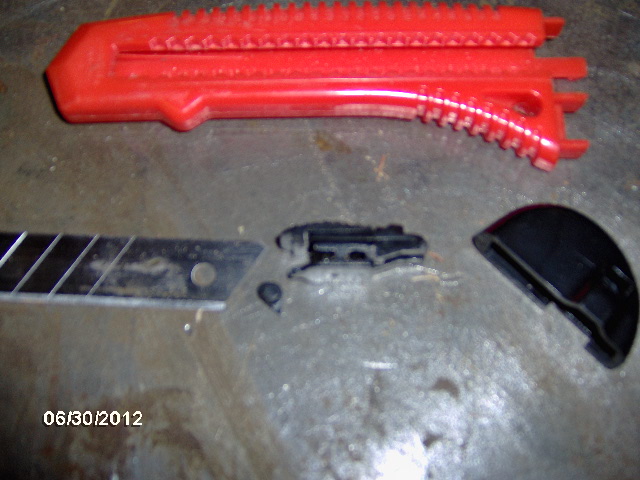
There was sawdust involved.
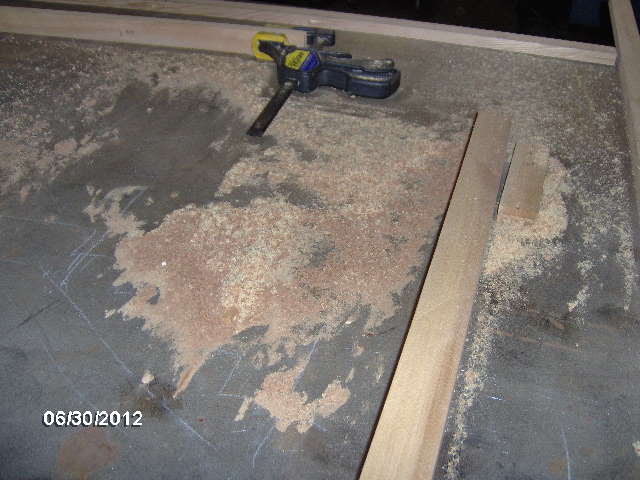
Back to the bulkhead framework. Now it can lay on the bench and hang off for the clamps.
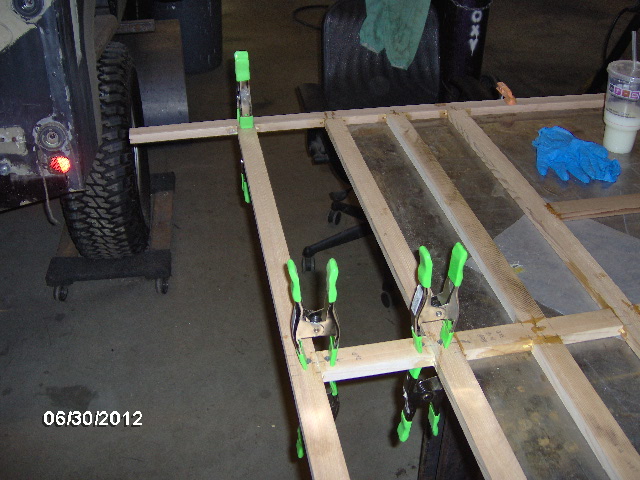
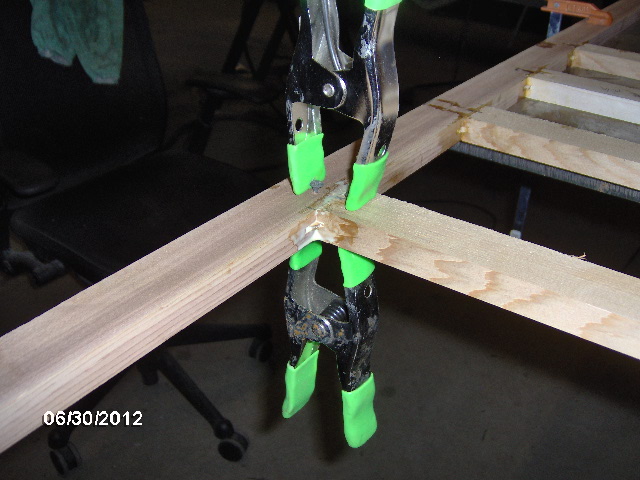
My overconfidence in being able to do the scarfing well led me to decide to make all of the bulkhead skin panels the same size; not planning for the seams to land on the planned xmbrs or studs. I wished I had thought that out a bit more and landed the seams on frame. I decided that, similar to the floor, I wanted to add more frame members for the panel butt joints to land on, so it appears that there is a lot more wood in there than you would think is needed. Ripped the added extra bits from the big hunk of drop cedar using Ben's table saw (that thing is sooooo sweet to use). Rest assured, the frame is super light weight.
The top header and bottom sill are the longest parts. The side stiles cap all of the xmbrs. Here are those dry fit pictures out of order. In the first pic the bottom is nearest.
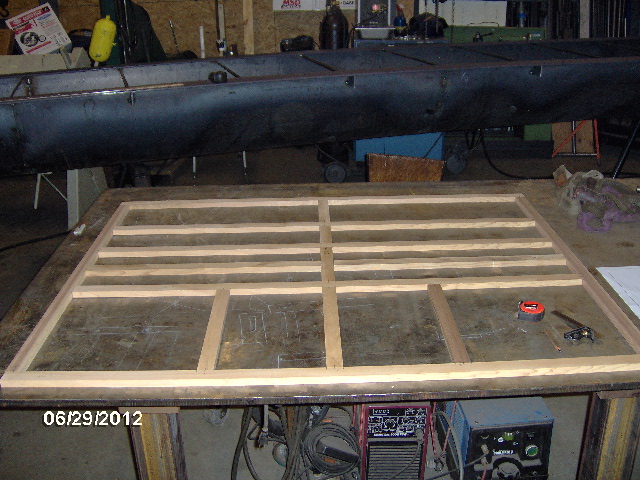
In this overview the bottom is to the left.
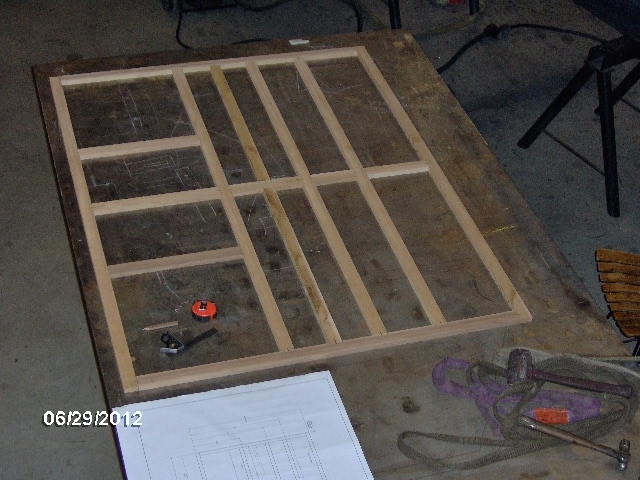
The members running through the centers, the 'X', were added to support the panel seams. The two cripples in the lower section give the under counter dividers something to screw into. The lowest xmbr is for the counter support, and the uppers are for the galley shelves and inside cabinets.
So, like I said, I started gluing biscuits in the middle and worked my way out to one side. Then I kept adding xmbrs and center blocks until they were all in place and I could add the other side. When I test fit the other side the extra center piece (the one that I cut, not Rover Mike) was just a hair longer than the rest. Since that main part of the frame was still setting up, and trying to trim the long piece would upset the glue up, I chose to chisel a pinch of material from the mating area on the side stile.
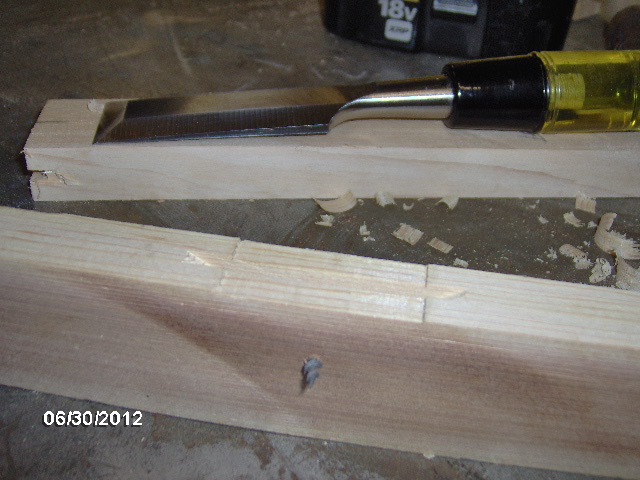
Fit like a glove. Also note that I avoid setting the chisel on the steel table, so as to reduce the risk of dulling it.
The new biscuit slot gluer works a treat, is quicker, saves on glue and squeeze out. Just do it.
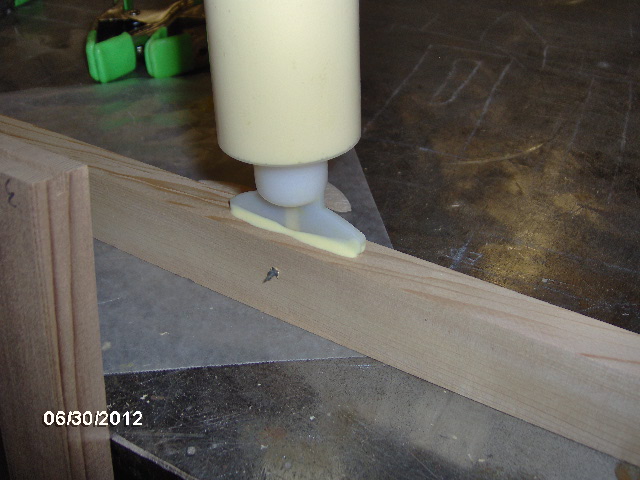
During periods of waiting for the next stage of glue up, I started cutting out foam. The 3/4 thk x 2 x 8 ft foam is thankfully 3/4 thk. It came as tongue and groove with a round tongue and groove. I started by using Karl's "utility knife" to trim off the rounded tongue.

Here is the finished bulkhead sub frame. You can also see the progress made on rough cutting the foam filler panels.
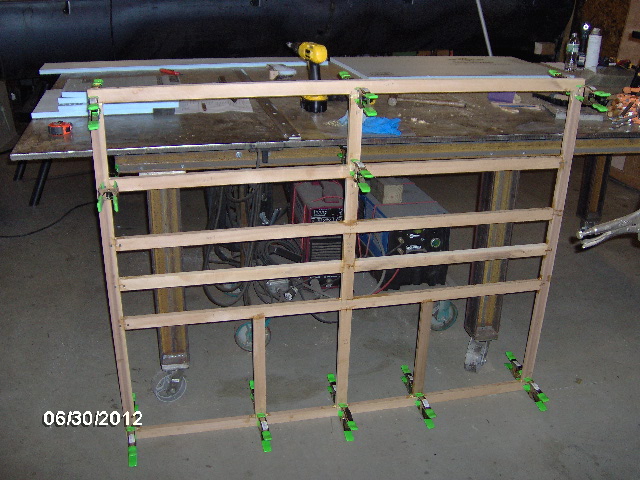
Wife came by to visit the kittens and snapped this cameo of me about to adjust my glasses (filler pic 'cuz my posts are too short as it is). Did I mention that it was humid again today?
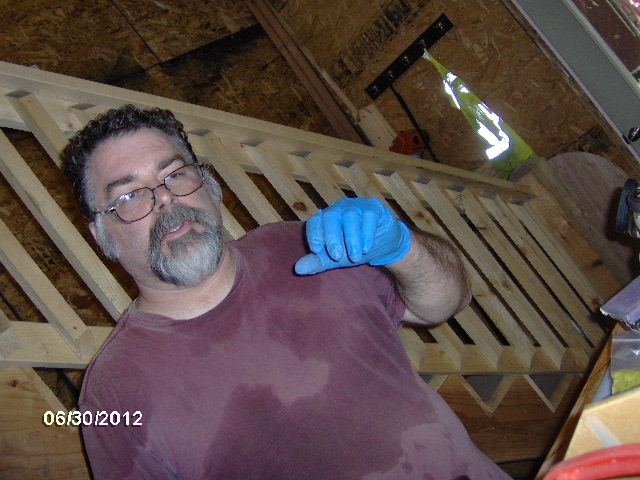
When I got to the end of the sheet the last piece was just about right to fill in one of the voids, except it had the groove in it. Having never used Gorilla Glue (GG) I decided that this was a good place to experiment, so I fished the cut off tongue out of the trash and glued it into the groove using painter's tape to clamp it.
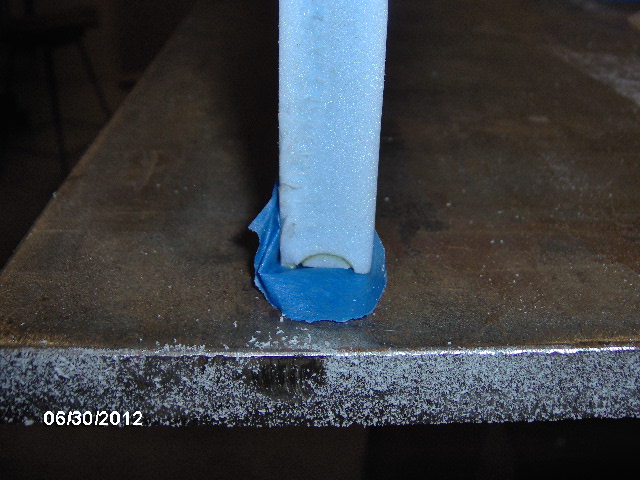
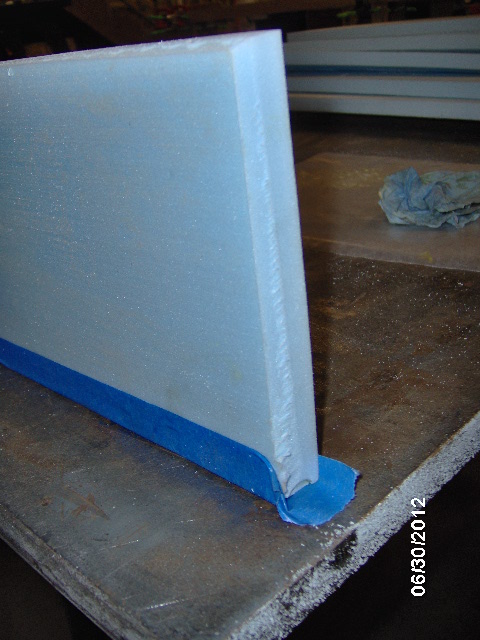

Worked really well.
I clamped the long sanding board that I made for leveling the floor foam to the bench and ran the foam panels over it a few strokes at a time to get the fit close, then fine tuned with my smaller block.
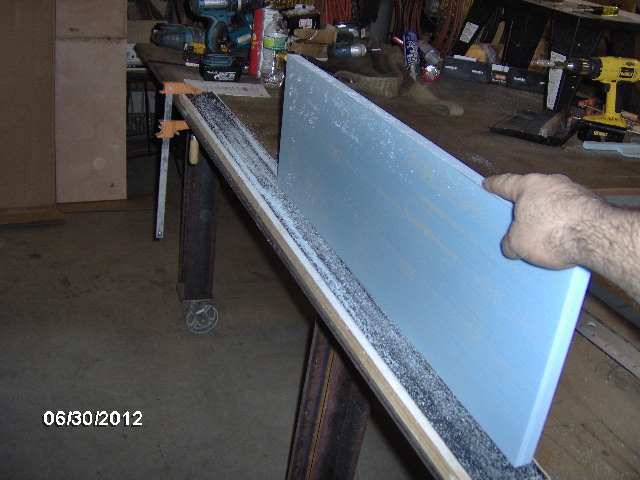
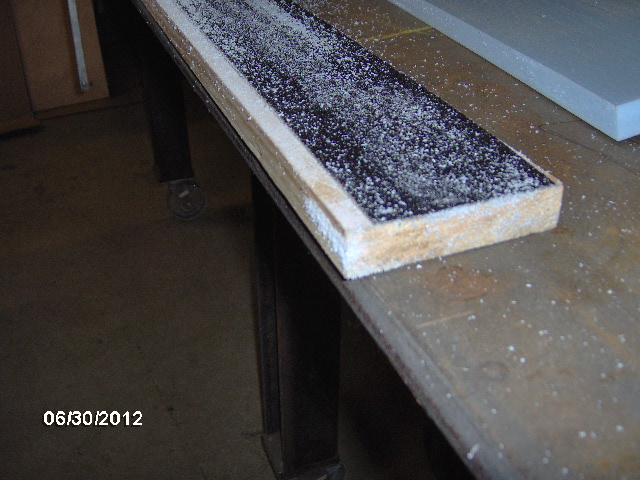
Foam fit exceptionally well using this method. Also note that I used a few smaller slivers to fill in the narrower slots, rather than resorting to using a second sheet of foam.
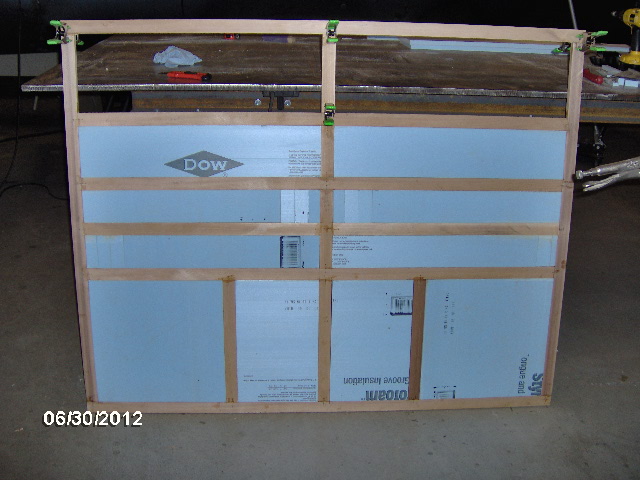
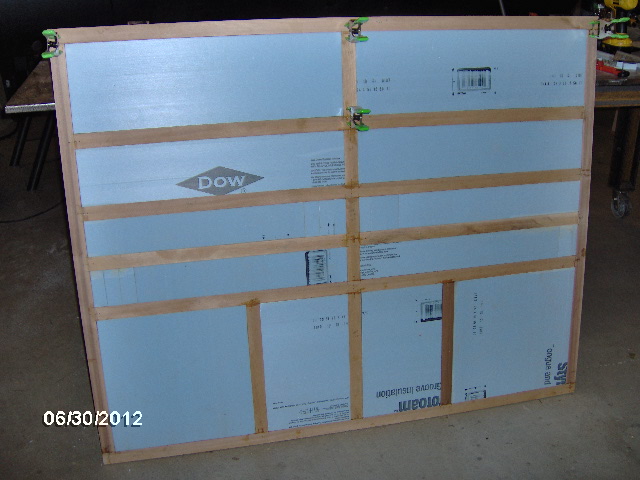
The camera makes it look curved, but it came out surprisingly square (within 1/32 on diagonals) without having to force anything.
At this point the whole assembly could easily be moved around and couldn't weigh 10 lbs (although I did not weigh it... it was feather light).
Here's what was left of the foam sheet. Pretty great yield.
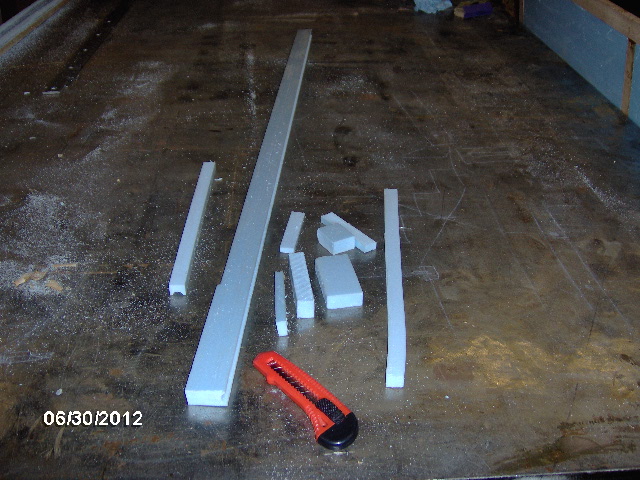
The 3/4 thick foam cut with just two passes of the razor knife; long drawing slices with the blade extended out and at a very shallow angle.
Here I have used the same technique as on the floor and have set guide nails for the panel alignment using a string to find straight centerlines.
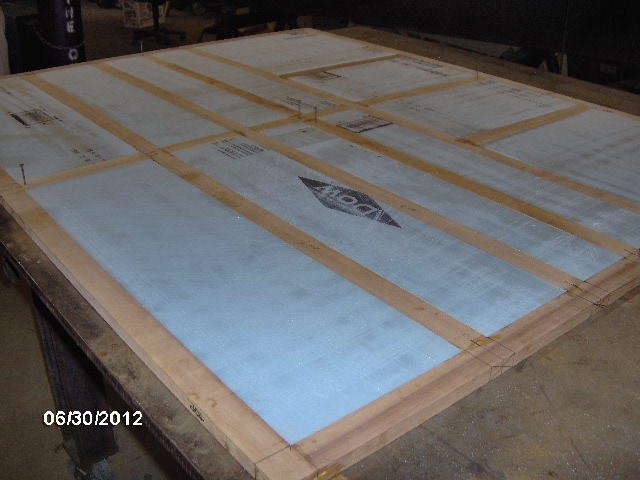
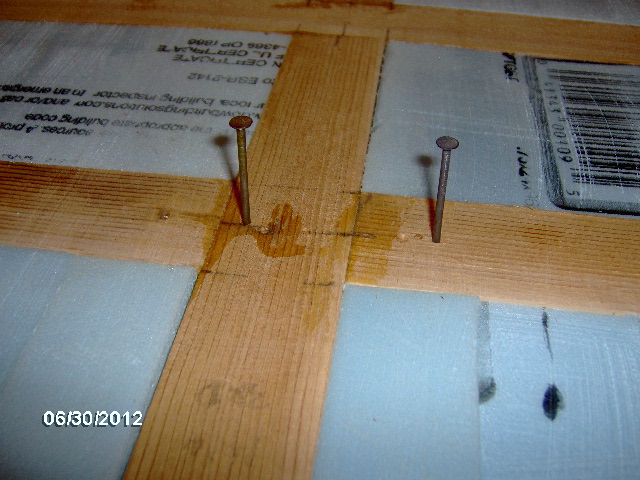
Also have already scratched up the surface of the foam using the sanding block.
Shop-vac is the right tool to use for cleaning up foam dust.
Here are some of those recovered pic's showing some more details on the door corner block dado's and rabbets. Scoring the edges of the cuts to prevent chip out.
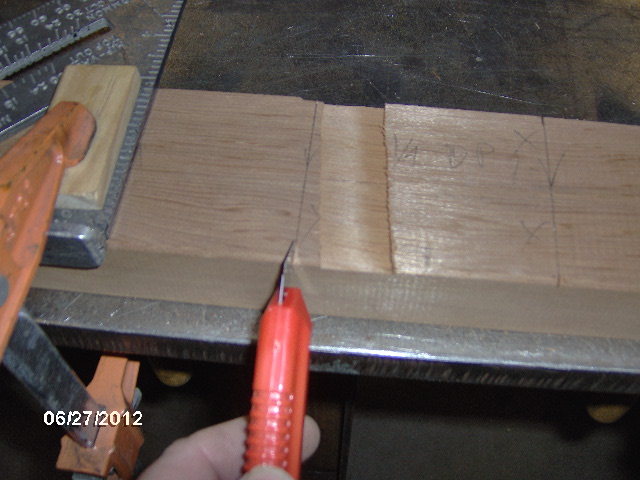
At first I thought I would need to make a couple of passes, so these are shallower than the previous pic's.

Intermediate spacer helps bridge the gap.
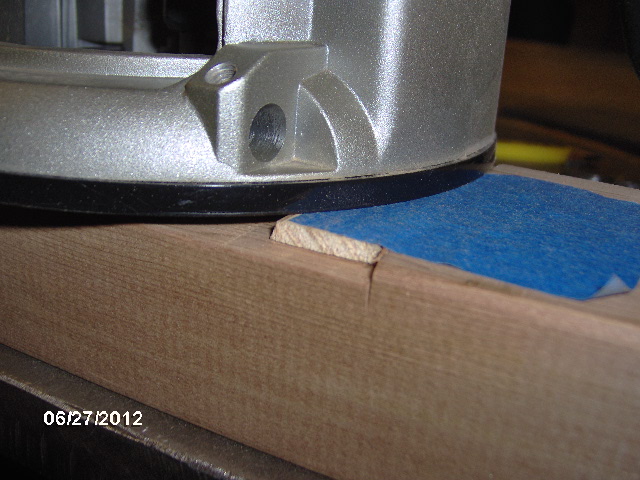
This is either the door surround headers or the wall sill plates.
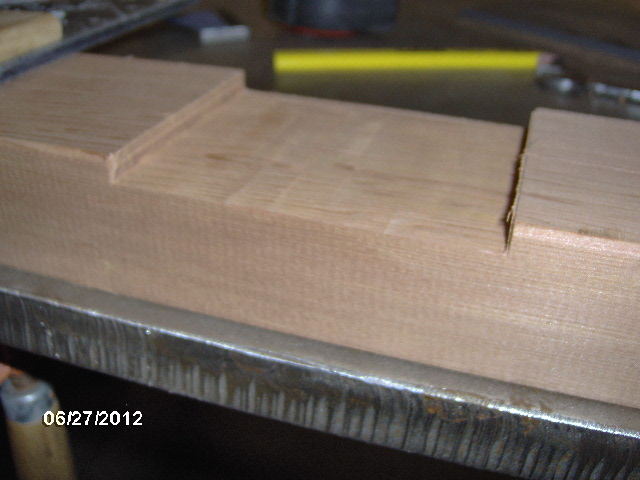
This might help explain the whole dado, rabbet, door corner block thing better; a couple of shots of the plans (macro setting on camera seems to be working better now).
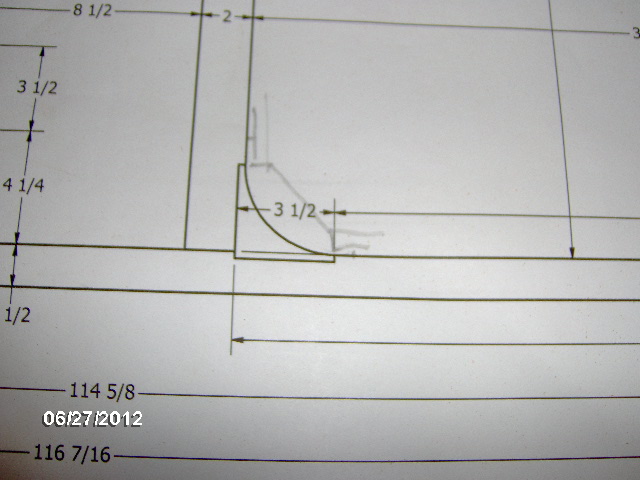
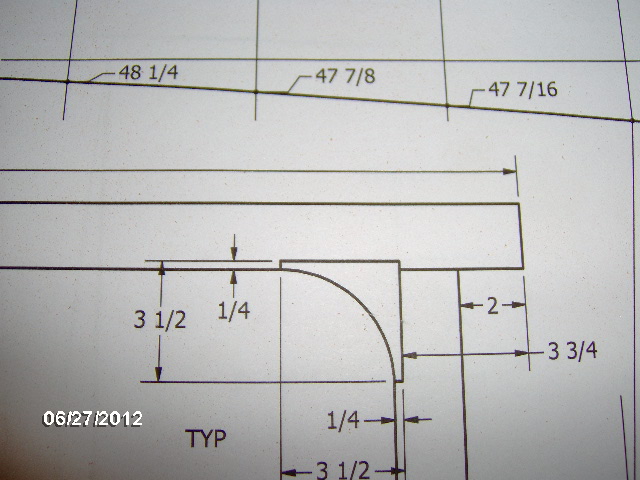
That brings us to today, Sunday.
Started out by doing the masking thing to the bulkhead inner skin panels.

Laid down some plastic drop "cloth" to protect the bulkhead from staining and contamination from the steel bench. Also keeps glue off of the bench.
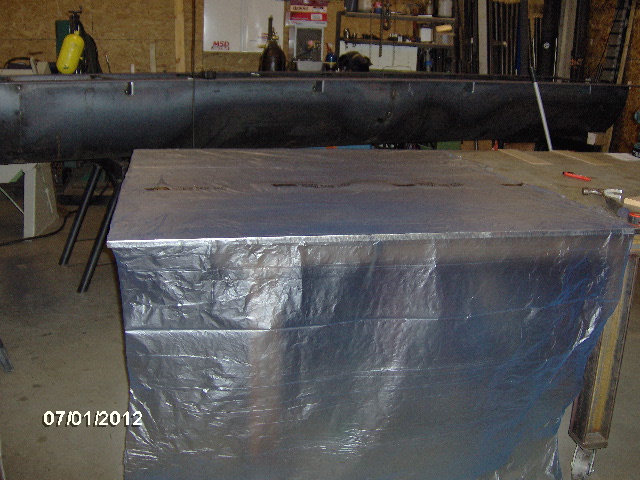
Got everything ready and laid out, then applied the 30NF adhesive.
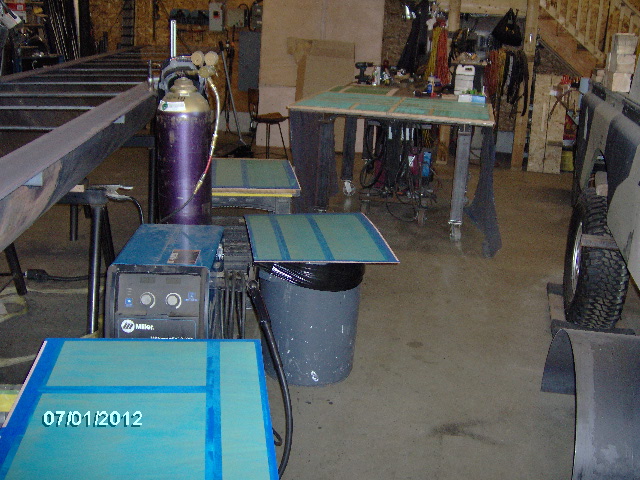
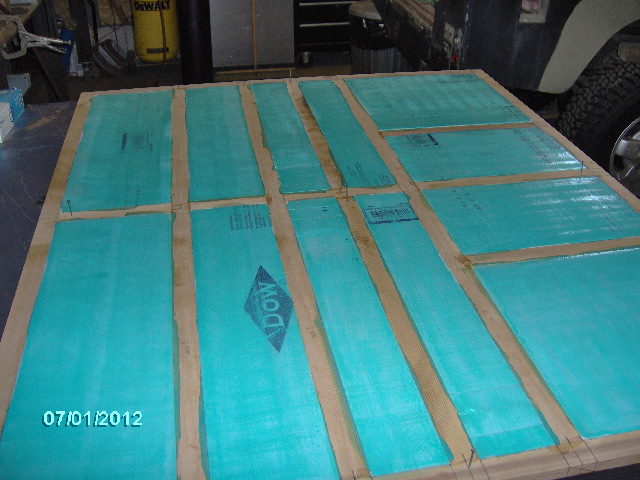
Peeled the tape off of the backside where the wood glue will go.
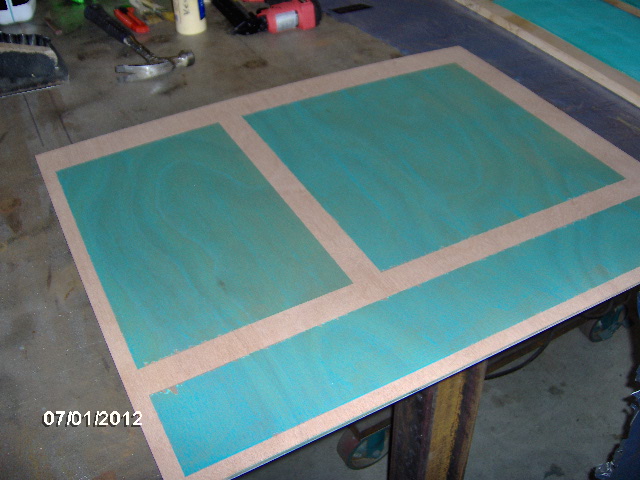
Waiting for the adhesive to dry on the foam it was time to check on the kitties. Wood pile makes a great 'Kitty Condo'. High above any predators in a good defensive position.
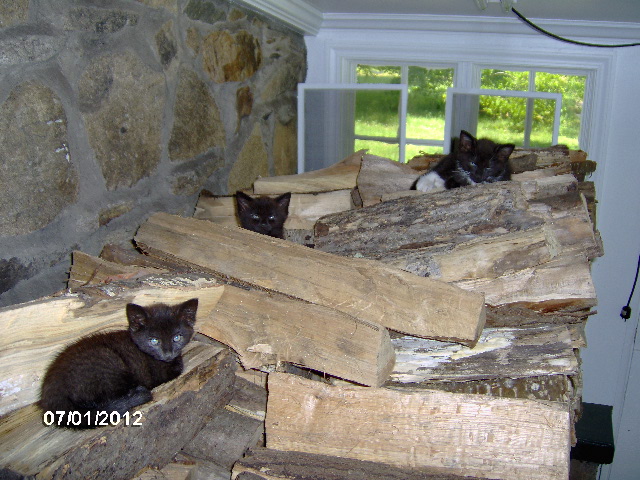
At first they would climb in to the nooks and crannies of the pile and nest inside, but now they have found the top of the pile and seem to like it there better.
I've been calling this little guy 'Sport'.
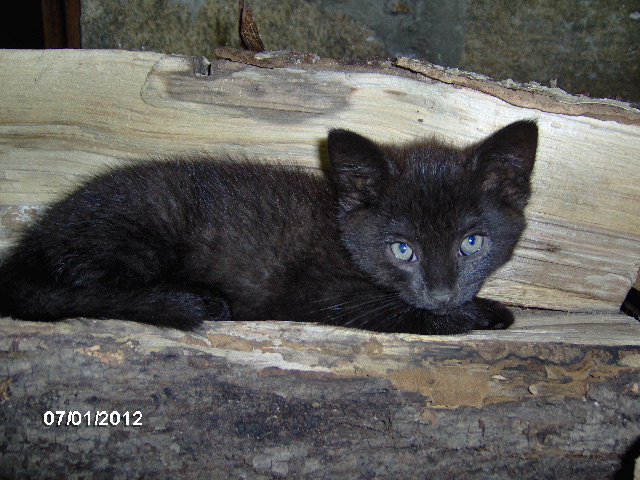
This is Rocky. Yvette and I have pretty much decided that we will be taking him home with us when they are 9 weeks and have finished their run of med's. Rocky has three little white hairs over the corner of his right eye and a few little stray white hairs on his forearms.
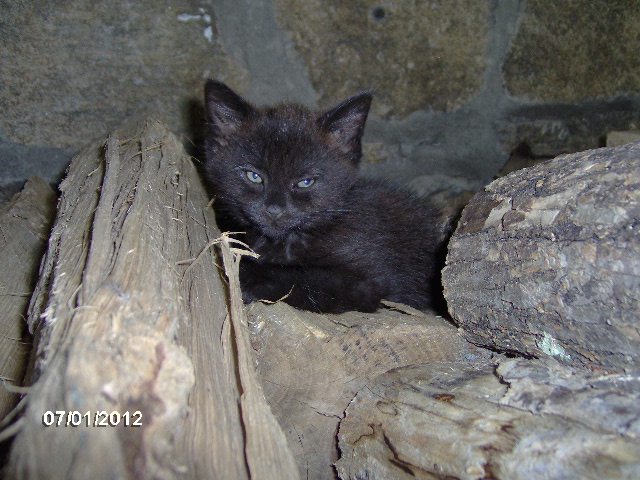
This is 'The Girl' with white boots, bib and belly. Chris and Karl will likely be keeping her.
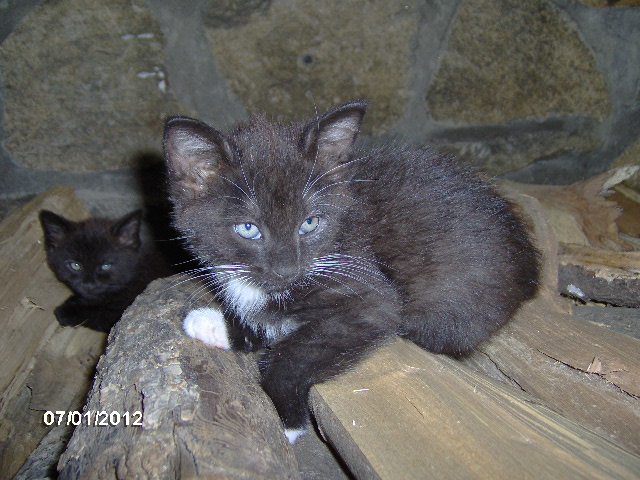
That's Rocky in the background.
The Girl, not too happy about the camera flash waking her up.
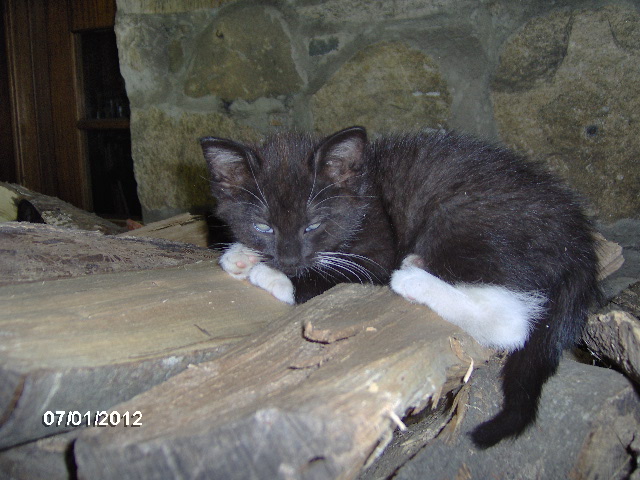
Kind of a big pile for these little kitties to be rough housing an top of.
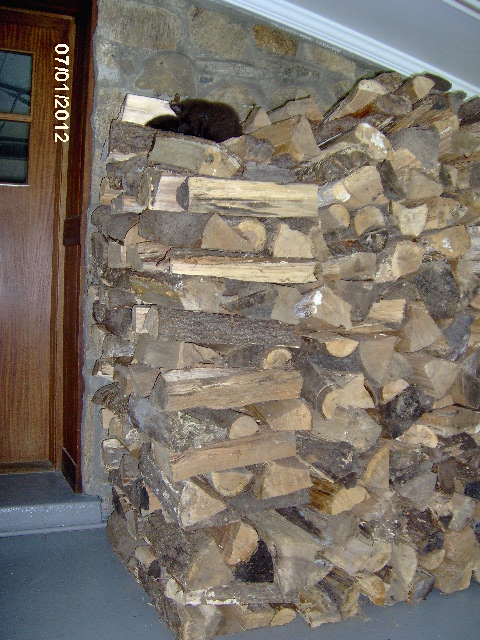
Rocky being adorable.
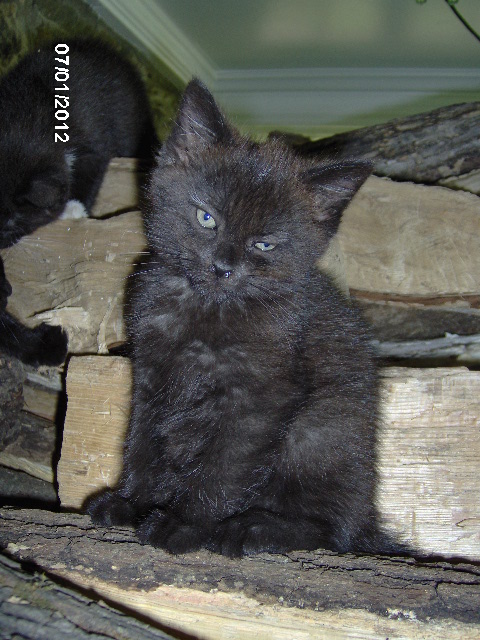
Family photo.
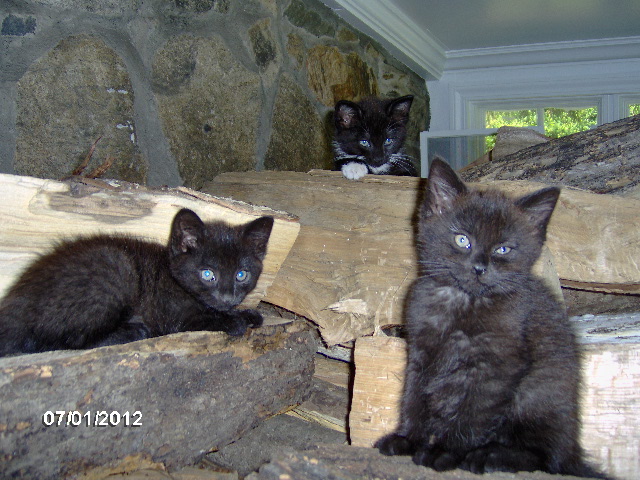
The pictures do not do justice to just how entertaining it is to watch kittens being kittens.
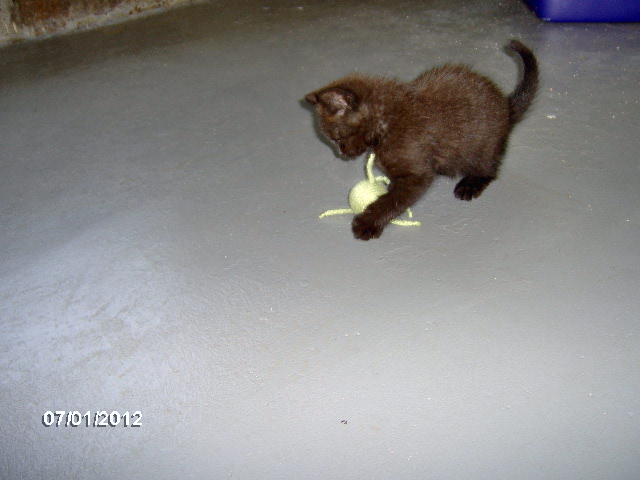
Okay, back to work.
Here is a piece of scrap luan that I cut out a 3-1/2 x 3-1/2 square to act as a router template for gouging out the wall foam where each of the cabinet mounting blocks will be set in.
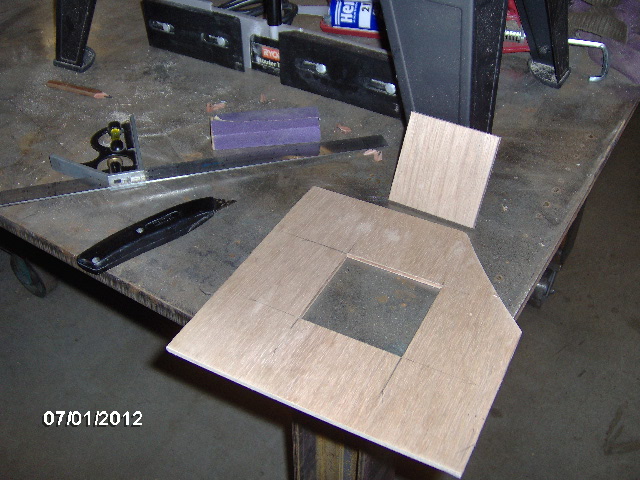
Just used a sturdy utility knife and metal straight edge to score it out. Touched it with the small 100 grit sanding block to remove any loose splinters.
Once the adhesive had dried on the bulkhead parts I started in gluing the frame and masked areas of the panel backs, then using the slat stickers to help align the panels against the alignment nails prior to sticking a brad in to lock it in place. Since I was working alone there aren't any pictures, but the process was the same as for the floor.
The bulkhead was the perfect size to allow me to clamp the bottom and both sides right to the edge of the bench. Along the top will be hidden by the inside cabinets so I used the brad nailer to fix that edge and down about half way along the upper middle seam. The rest was just weighted down to cure. I had originally thought that I would flip the extra plastic up over the skins before adding the weights, but some of the glue squeeze out dripped down the plastic, so I didn't do that. I just used scraps of cardboard to protect the skins from the grunge of the weights.
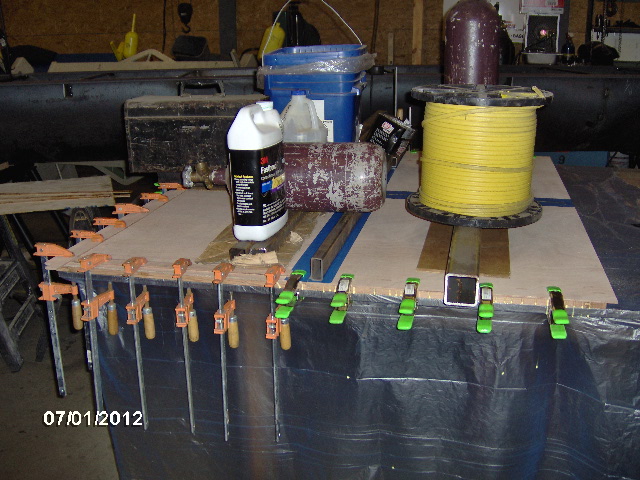
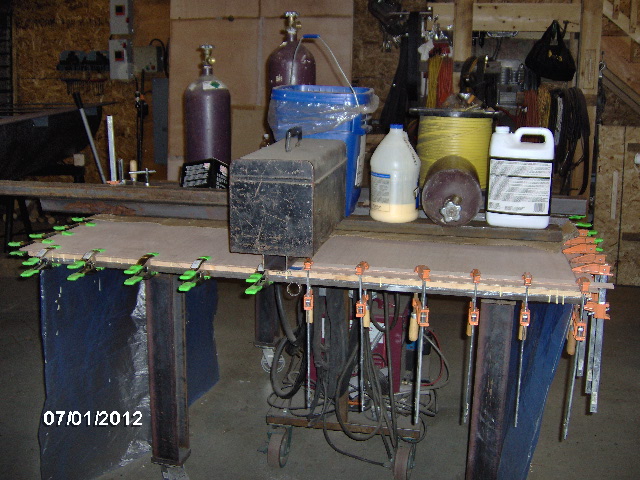
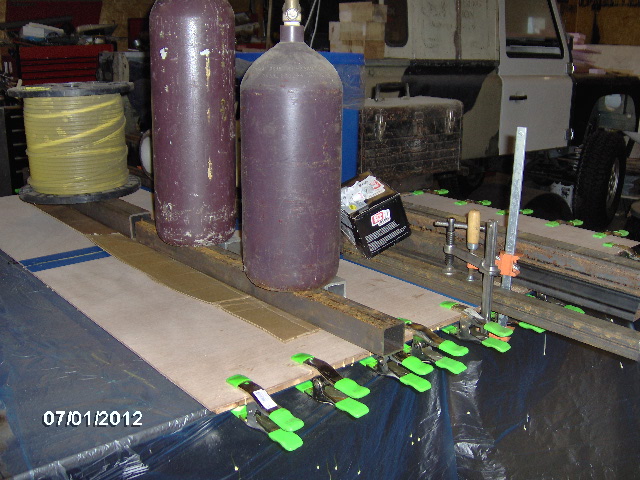
Whew. Now we're all caught up.