Let’s get caught up.
Monday I pulled the weights and what naught from the first of the curb side wall interior blocking glue ups.
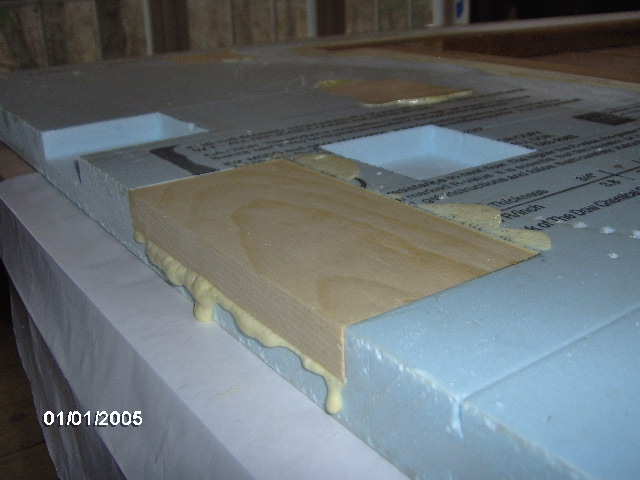
Then I cleaned that up with the small Surform grater and the small hard block with 100 grit paper.
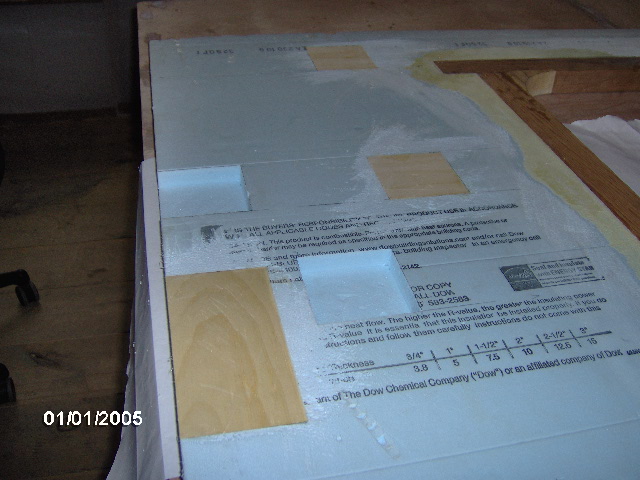
Did another round of glue ups, sometimes jumping ahead to leave room for the weights where the blocks were close together.
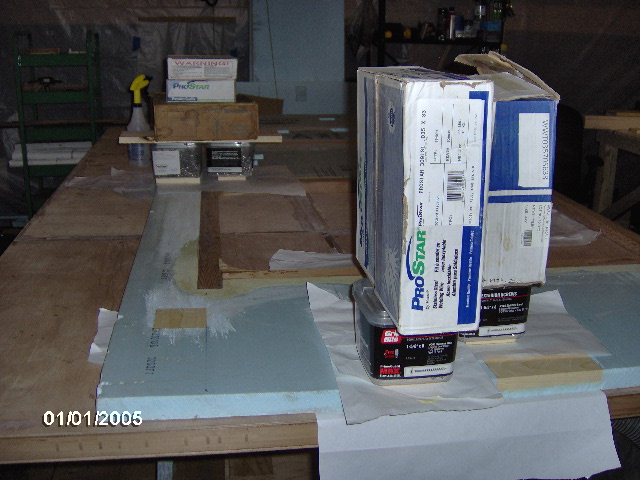
To recap, I used the spritzy water bottle to damp the wood blocks, wiping excess off with a paper shop towel. Made sure that the end grain was damp (it takes a bit more). Made sure that the recesses were dust free. Applied a bead of GG (about 1/8 inch) around four sides, and in an X through the middle of each recess. Used the fake credit card as a spreader wearing vinyl gloves to smear it into a thin layer on the bottom and four side walls. Push the block down in, damp side down, now paying attention to put the grain horizontal to the floor (seems less likely to split due to load that way). Top with plastic side of freezer paper down, add an equal size block to concentrate the weight, a tub of SS screws because they fit the block well, then a box of welding wire spool because it weighs enough to keep the GG from pushing the recessed block up. I have found that this schedule combats the hydraulic effect of the GG fairly well. Now that I am mostly done with these standard 1 x 4 x 4 nominal (3/4 x 3-1/2 x 3-1/2 actual) blocks I have found that my developed technique has gotten them to stay down in the holes about the same amount as I had set the router depth over the 3/4 inch desired depth. So knowing what I know now I would probably either set the depth truer, or use a slightly larger block for the spacer so that they don’t hold the recessed blocks down in the hole. No worry. Just a quick few passes with the hand sanding block and everything is fairly fair.
On this 2-fer in the galley I used a wider 1x6 plank for the weighted block and my drinking water supply and finish nailer (in case) for the weight, and it held the recessed blocks nice and flush.
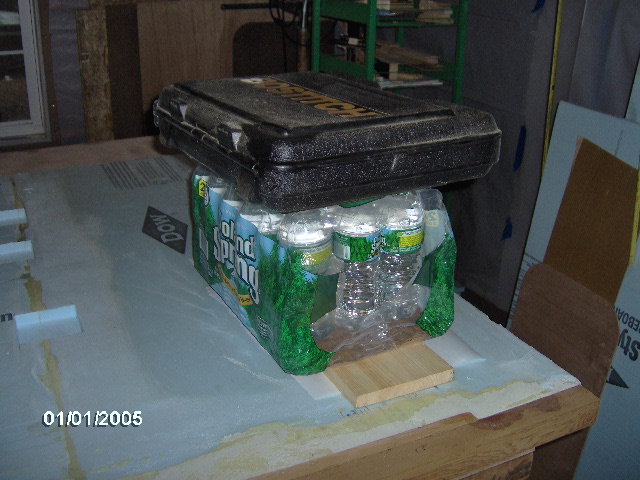
On Wednesday I pulled the weights and paper off and found that the front block had been pushed out forward due to the open side of the recess not constraining it; about 1/8 inch.
If you look closely at the previous pic you can see the expanded line of GG at the back of the block (on left seam in pic) and the corresponding unevenness between the block and the front edge of the blue foam (on right side of pic).
What I have found is that the consistency (or lack thereof) of the environment has a big effect on the performance of the GG. On moderate days where I left my glue bottles in the car it reacted much less than on colder days when I brought it in to work with me to keep it from freezing. Same thing when I was leaving the heat on in the loft overnight vs. bringing the glue home with me and shutting the heat down. Even the moisture that I put into the wood and how long I leave it sit, what the conditions are in the shop, whether I set the block damp side up or damp side down while I am prepping before actually setting the block in the recess can all have an effect on how the GG behaves. I don’t have any concern at all about the strength or integrity of the joints (they all kicked off eventually); it is more an issue of consistency, accuracy of placement, and amount of glue squeeze out so as to minimize the amount of clean up and maximize the fit. The more stable you can keep the environmental conditions the better.
Here it is after fairing the face of the wall.
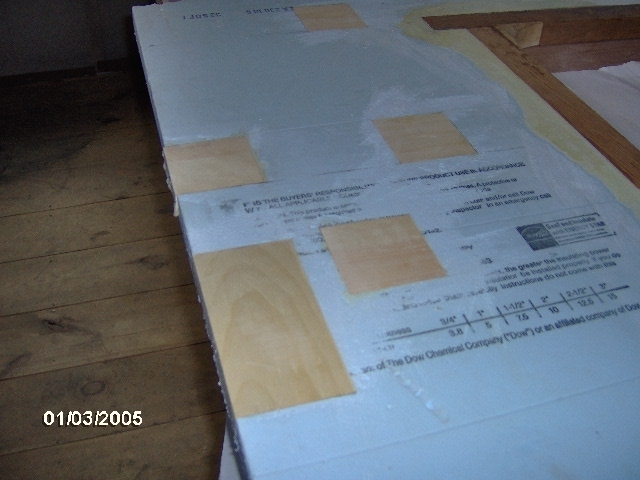
Here I have used the belt sander to fair the block back to the front edge of the wall. Glad I left plenty of margin around the screw location.
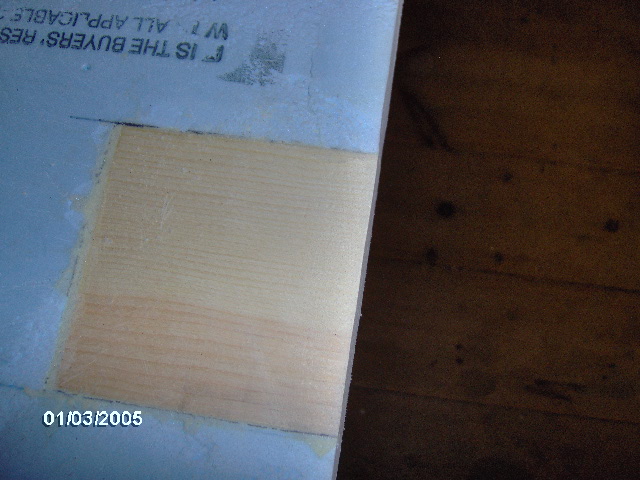
Here are the ones in the galley from under the water bottles; not bad.
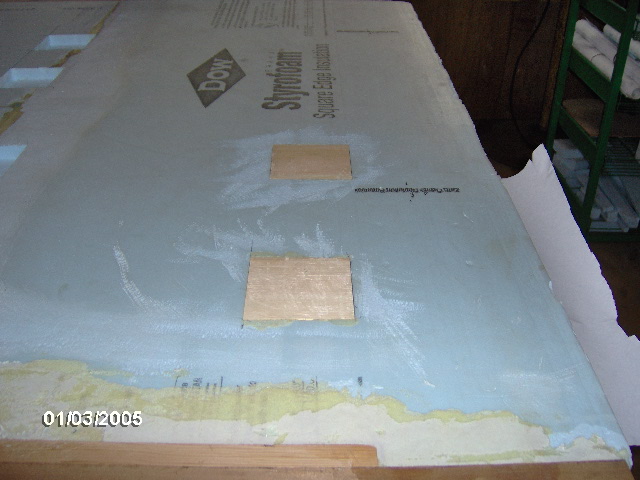
Note that I put freezer paper under the wall to protect the floor from any glue that might sneak through the seams or factory score lines in the foam. It did happen, so I am glad I took this extra precaution.
In the mean time I have been working to get my laminated galley wall edge pieces into a useable state. In order to be able to clamp the edges into the jig, maintain clearance with the clamps, and get the side of the edge above the jig blocks, I had to space the edge piece up off of the jig board and use spacers between the clamps and the part, as shown here.
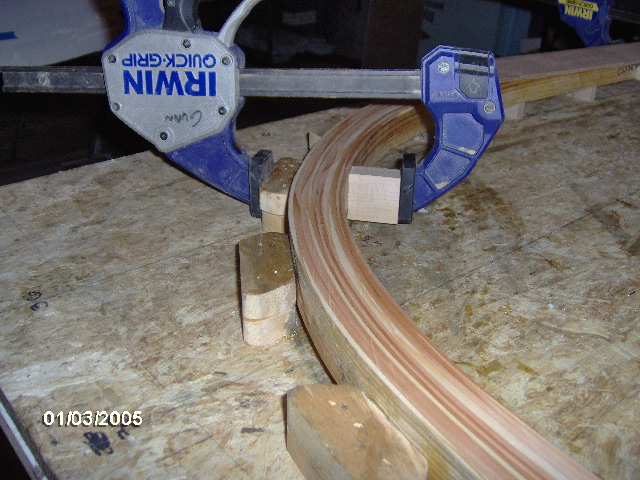
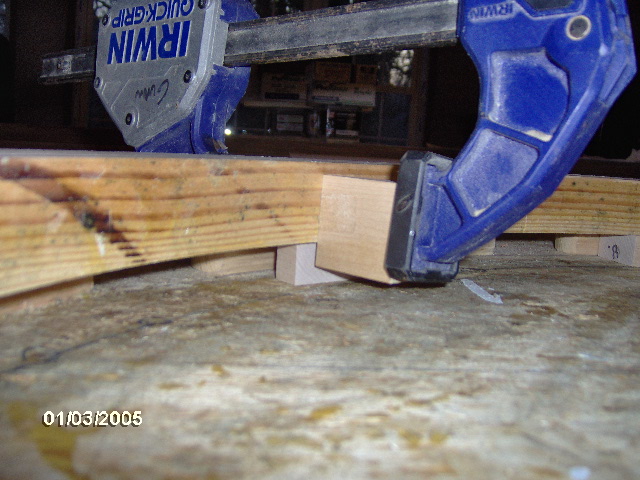
And here you can see why I needed to make the clearance, so that the rough ply skin lays flat on the laminated part and the clamps don’t get in the way of gluing them on flat.
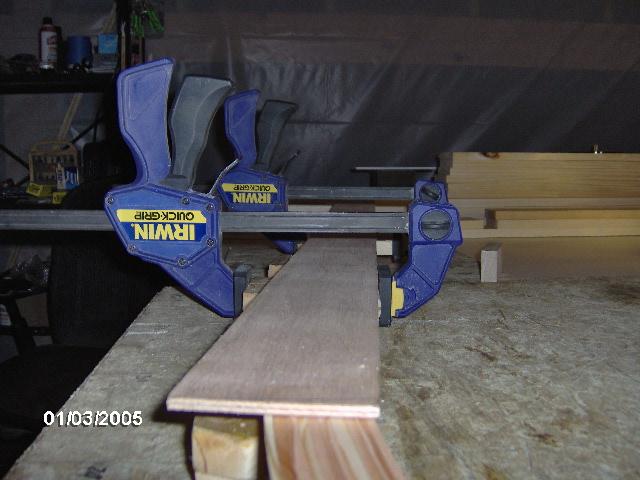
And a rough layout of the ply skins on the wall edging.
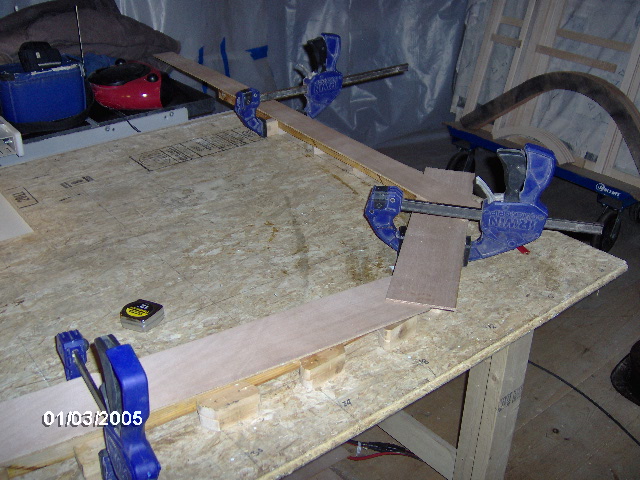
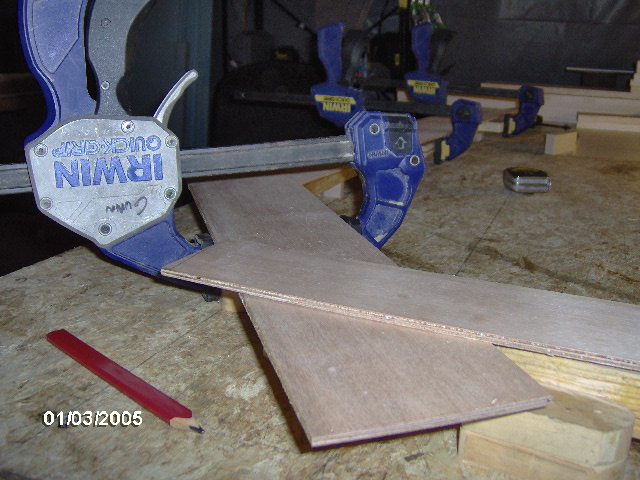
As it stands right now, I am considering this to be the piece for the curb side wall because I would rather have the ply spacer be on the inside off the wall, rather than on the outside where it will get routed out for the hatch seal. But I might change my mind on that before it is done.
One thing I learned is that the jig will only work for one side as is. If I want the ply spacer skin to go on the opposite hand for the street side wall the jig will need to be inverted. Maybe I will end up putting the curb side ply on the inside, and the street side ply on the outside. Does it really matter? I plan to seal and paint the edge any way.
I think we are into Thursday now. Back to the wall cores: I removed the weights, trimmed the excess GG, and hand sanded a bit to get closer to fair. These are the blocks for the cabinets at the back of the cabin over our feet.
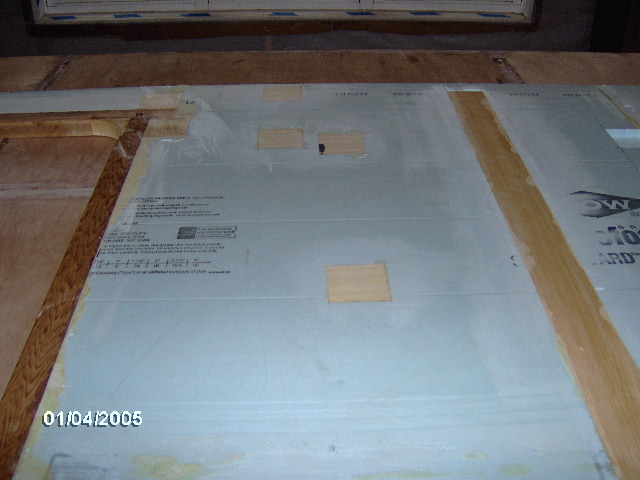
Same thing from the top looking down. The dark spot is marking dye from the lumber yard.
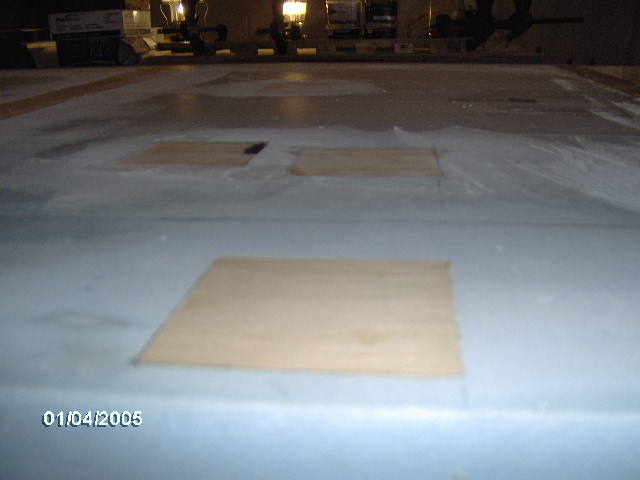
Got the last of the previously cut recesses filled, the ones in the galley.
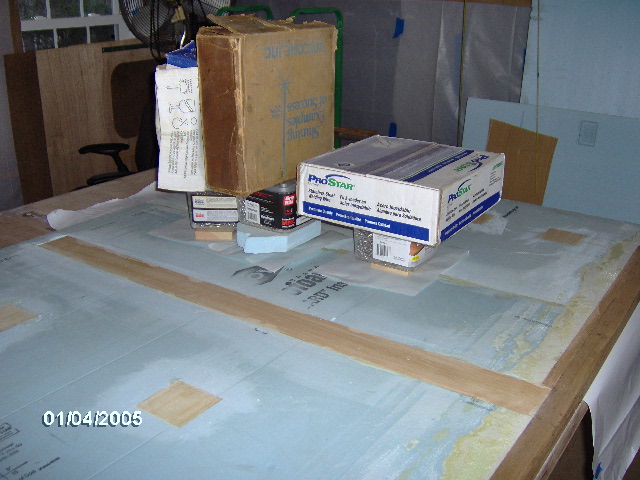
So what’s left for blocking? I have the hatch struts worked out in the model but, at this point had not translated those into useful dimensions. The fender mounting locations are planned out, but I want to verify those with a test fit of the fenders before committing to the cuts. I think I am going to put some cleats on the outsides to attach wing tables to, but I may want these to be lower than the galley counter, so I want to check that with a final ride height further along in the build. I thought about putting something in for my thermometer/hygrometer, but I think I will just use double backed tape for that instead of screws.
Had rain on top of snow with flurries later in the day (flurries didn’t show up in the pic).
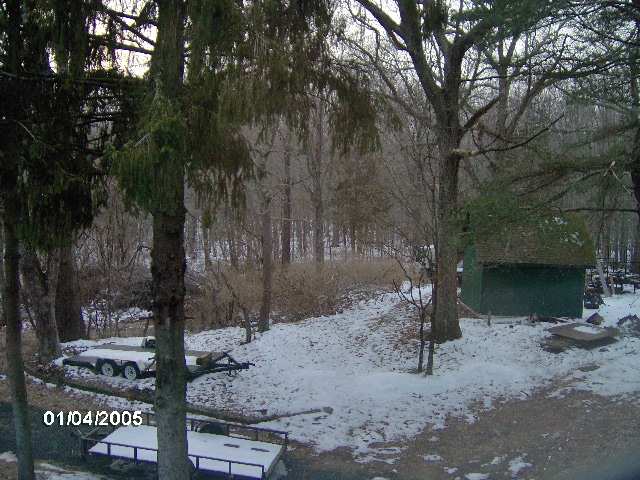
Set up the router to make half laps in the mitered scab pieces of 5mm ply that will get laminated onto the side of the galley wall edges. This is just a scrap piece of 5mm luan underlay used for setup.
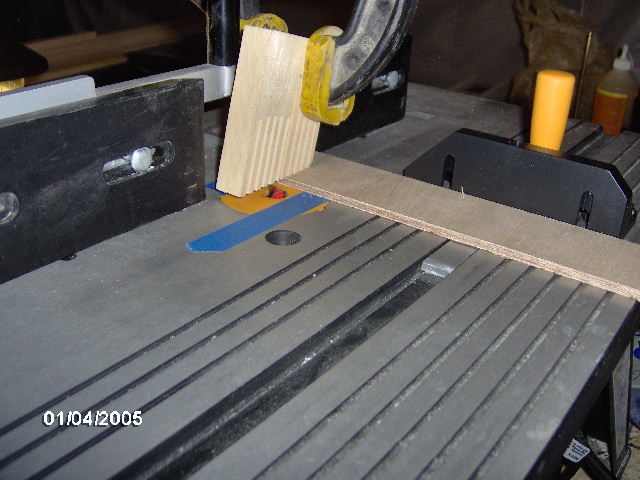
Friday I stayed after work and added the hatch strut block locations onto the wall drawing, and printed that out on the big plotter. Also made another copy of the wall edge profile, although I will probably use the outline from the CNC profile templates and fit the edge pieces to these to determine where to trim them.
That brings us to today, Saturday. I started by mitering the scab pieces of okoume and making the lap joints. Here is a shot of the dry fit.
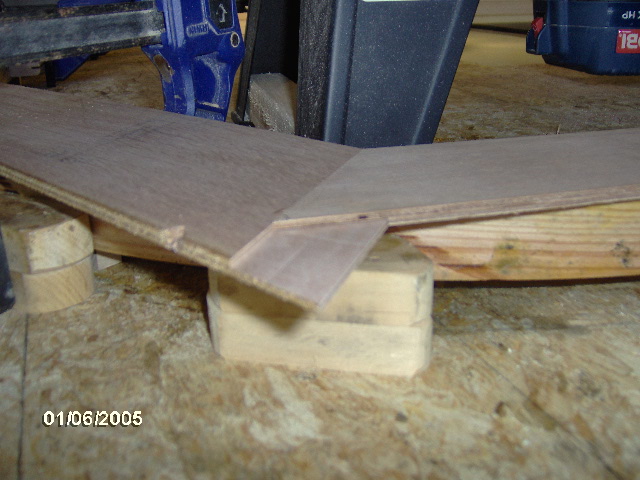
And here it is after gluing; sticking a couple of countersunk drywall screws thru the okoume into edge piece to pin them into location; adding a couple of scraps of the freezer paper over the miter joints; then screwing some random pine boards down over the whole length to clamp the skins down seriously.
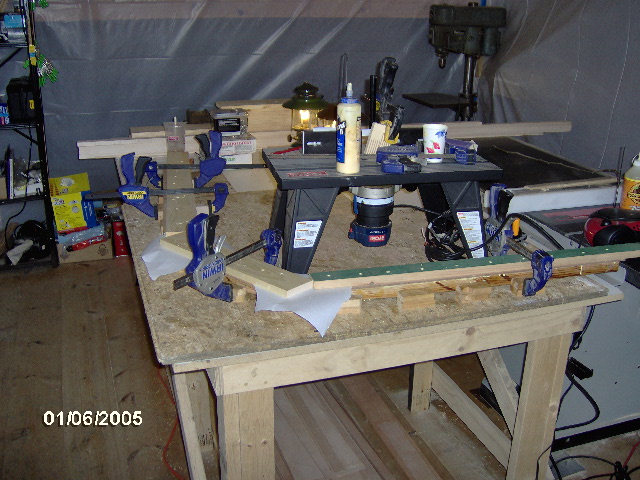
The clamping boards gave really even glue squeeze out.
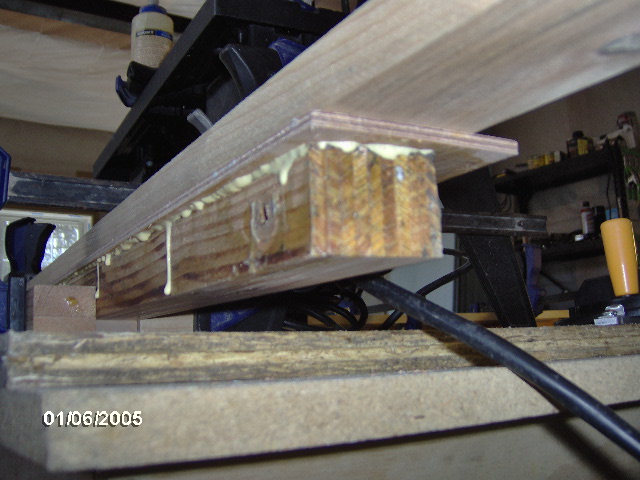
I only put glue in the lap joints where they sat over the edge piece, so that’s why, although a little blurry, you can see a little separation and no glue on the excess in the foreground of this next pic. Not to worry, the critical section under the wood plank clamp is good and tight.
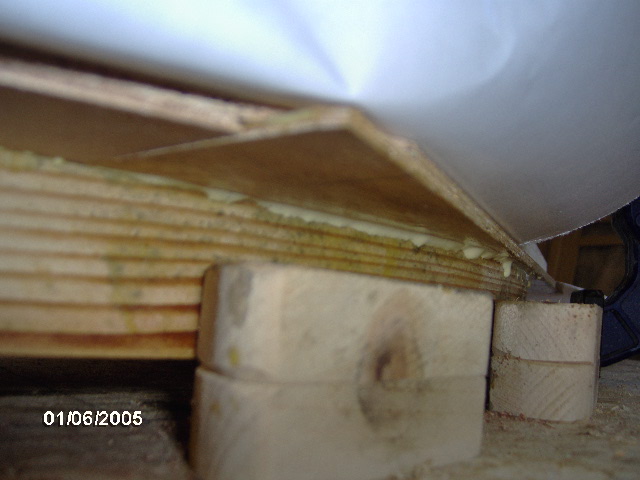
Here’s a better look at the pine I used as a clamp. Screws were placed every 4 to 6 inches or so.
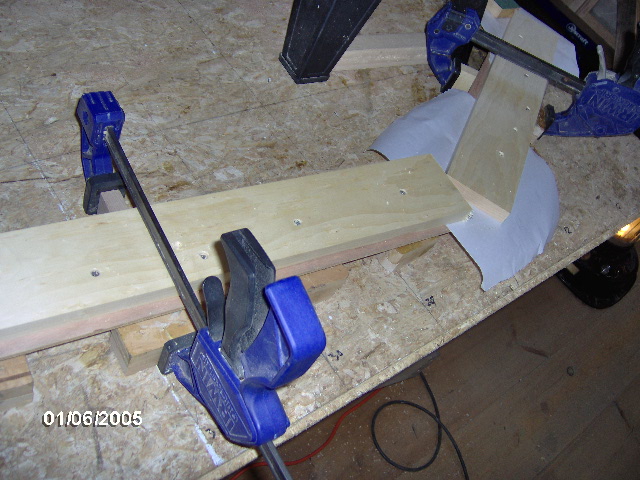
Then I moved back to the curb side wall, pulled the weights from the “last” of the blocks, trimmed, knocked down, and sanded to fair them out.
Next I set the CNC profiles up, got them into their exact positions, and traced out the outline with a black sharpie. Same deal as before, moving the center section around to get all of the big radius in the main part of the roof.
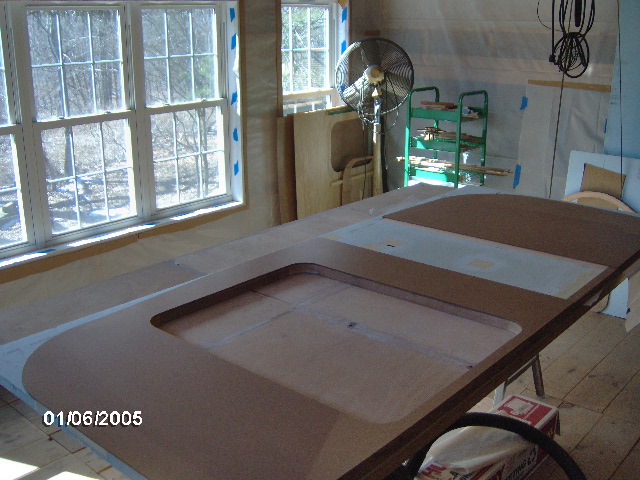
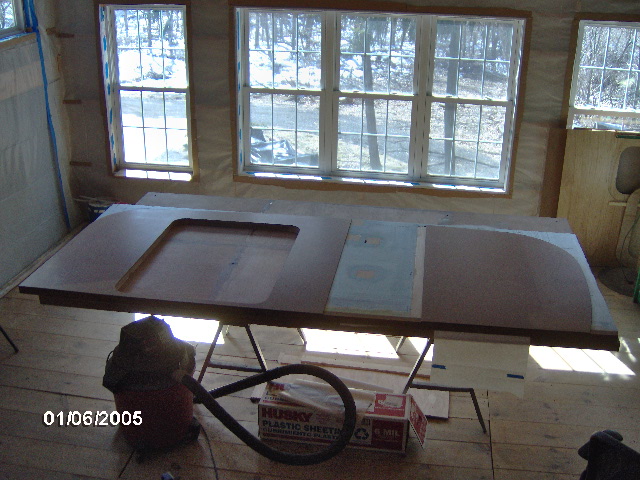
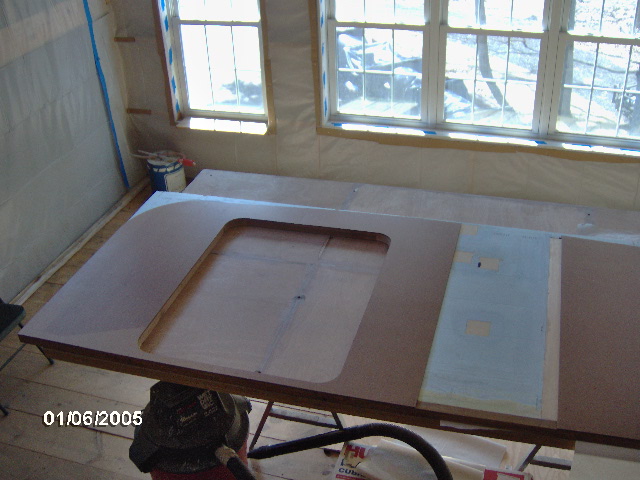
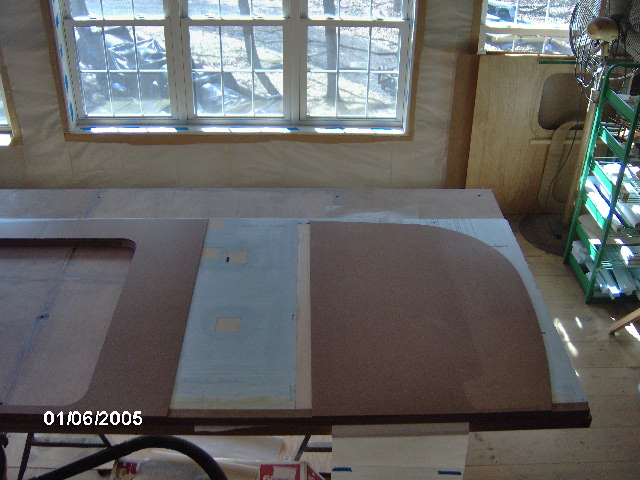
This is looking from the front along the top of the wall (top to left of pic, floor to right).
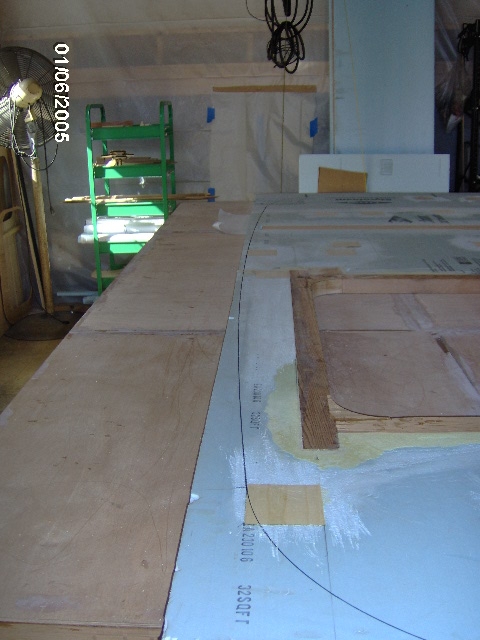
Here is the galley hatch section (shown with the floor to the left, the back to the lower right, and the top to the upper right).
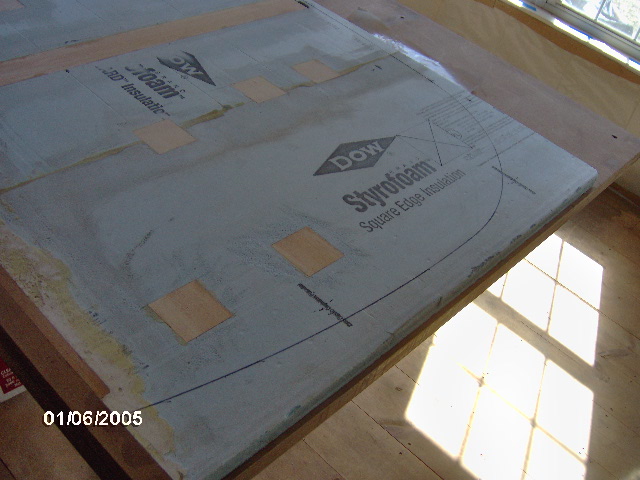
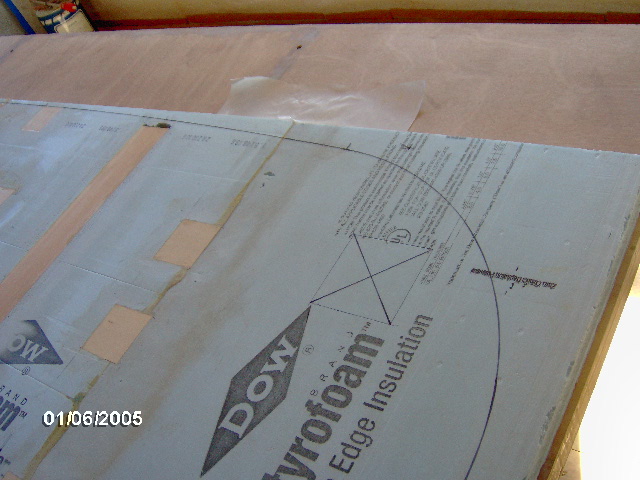
In the above pics, also note the larger square marked off for the tentative hatch strut blocking location. I’m not sure I want to commit to this location just yet based on the advice that having the struts anchor way out on the unsupported part of the wall can sometimes result in the struts bowing the walls out and affecting how the hatch fits when it is closed. I’m going to take another run at the design and figure out where the blocks would be if I were to keep the struts more in line with the hatch when opened. Then I can try either location, and if one doesn’t work out, the other will be there as a fall back. Still haven’t given up on the linear actuators, either. Note also that the layout (the big X) is for a bigger 3/4 x 5 x 5 block, and I will use some of the left over Red Grandis from the hatch ribs instead of the 1 x 4 pine that I have been using for the lower stress applications I have been using elsewhere.
From there I flipped the wall over and routed out the recess for the porch light blocking, shown here upside down with the top of the wall at the bottom of the pic.
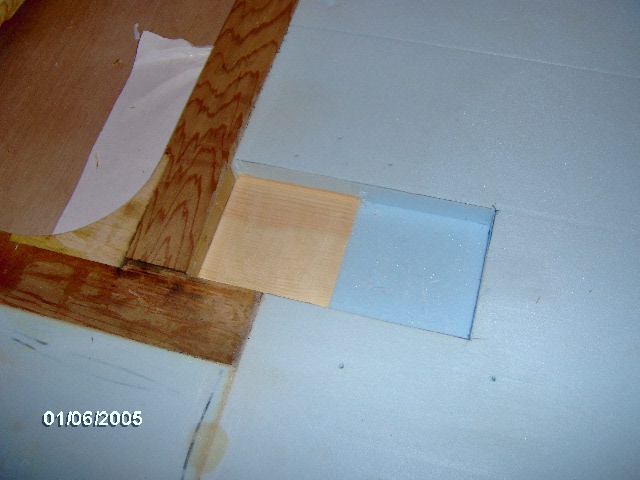
Then, after a little fitting, I glued that in and loaded on the freezer paper, weight spreader block, and weights.
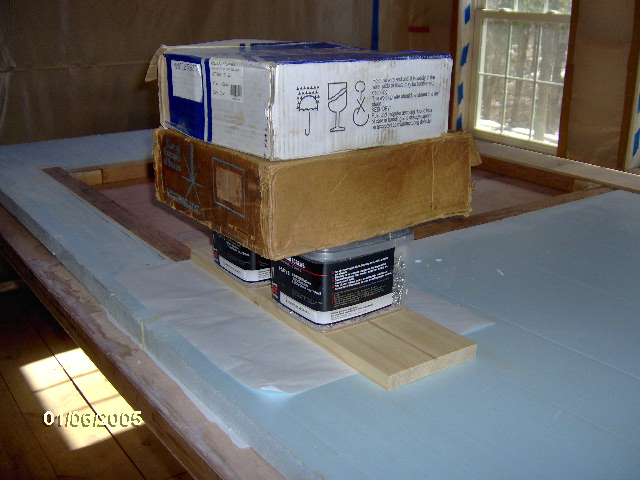
When I arrived at the shop at midday the outside temp was about 41F and the loft was only 39 or so. With the sun coming in it only took a couple of hours before I started shutting off the lanterns and heaters with the temp at about 55F (nice and comfortable for me wearing an over shirt and keeping moving.
Home early to clean up and get ready to take mom out and celebrate her B-day dinner (we had postponed from her actual B-day for various reasons). I had a wonderful osso bucco over risotto that I could not finish; mom had veal Marsala over pasta with a side of the asparagus and Parmesan risotto; Bill had the seafood shepherd’s pie (one of my favorites); and Yvette had the Italian salmon special with sauteed greens, sun dried tomatoes, etc. piled on top, the risotto on the side.
It's starting to feel like the "good ole days" of TPCE where I am putting in the time and getting things done. I’ll put a few more hours in on the build tomorrow.