Page 1 of 2
Cutting channels & notches in Foam ?

Posted:
Thu Sep 22, 2016 1:22 pm
by rustytoolss
I'm sure what I need to know is in the Foamie section...somewhere. Buy maybe someone can give me a link to where I can see how channels (for interior wood supports/or foam) are cut into the foam. And what type of tools are needed. Or need to be built. There are places that I will need to cut in compete shallow squares also.
Re: Cutting channels & notches in Foam ?

Posted:
Thu Sep 22, 2016 2:20 pm
by KCStudly
The two best methods are a router or a hot wire knife, with the router being the most accurate by far.
Disadvantage to the router is the mess that it creates if you don't have a good vacuum setup.
Disadvantages to the hot wire knife is temperature and tension control; too much temp and not enough tension = sloppy cuts. Wrong travel speed can result in melt outs. Some people seem to have the knack, such as the guy who used gravity techniques (sorry, can't remember who that was at the moment). Also, the vapors should be avoided.
Re: Cutting channels & notches in Foam ?

Posted:
Thu Sep 22, 2016 3:27 pm
by yrock87
It should also be noted that the expanding agent in most XPS foams contain synthetic hormones (estrogen). Disturbing the foam (like when you cut or route it out) allows the residual agent in the foam to be absorbed into the body. Small amounts are generally not a concern, but women and small children can be very susceptible to reactions to these agents.
My baby daughter was several weeks home from the NICU when I went through the foam cutting part of my build. I took precautions such as stripping outer-layers off in the garage and showering immediately before interacting with my daughter.
Re: Cutting channels & notches in Foam ?

Posted:
Thu Sep 22, 2016 3:54 pm
by rustytoolss
Since I have not yet started my build. What about just gluing wood support directly to the foam without cutting a channel (in the interior) ? Would this create a problem ? or lower structural strength ?
Re: Cutting channels & notches in Foam ?

Posted:
Thu Sep 22, 2016 4:36 pm
by Pmullen503
rustytoolss wrote:Since I have not yet started my build. What about just gluing wood support directly to the foam without cutting a channel (in the interior) ? Would this create a problem ? or lower structural strength ?
It depends on how much force, the direction of the force (up and down or away from the surface) and how much area the wood piece is glued to the foam.
Routing a channel in the foam and then covering the support with canvas or fiberglass will be the strongest. The channel will provide mechanical support in addition to the glue. If the area is large enough for the force, you could just glue the piece to the foam or canvas. Remember that when gluing to foam that even if the glue bond is strong, the foam underneath the joint can separate. Increasing the area and/or routing a channel will increase the strength of the joint. If the force involved is not trivial, it makes sense to build a test piece or copy successful examples involving similar forces.
I had to add supports for significant weight after my foamie was built. I used the type of drywall anchor that looks like a big plastic screw right through the canvas into the foam. Then I screwed my wood supports to those. That adds a lot of strength and the pieces are still removable.
Re: Cutting channels & notches in Foam ?

Posted:
Thu Sep 22, 2016 5:21 pm
by yrock87
if you know you will have high loads, the other thing you can do is the hybrid approach, maybe KCstudly can chime in on this. My roof was 1/8 ply sandwiched over 1 inch foam. I went with a minimal framing approach.. I only have 3 total roof spars and it is plenty strong. the ply allows for a high surface area bond and the foam and ply together are stronger than either alone.
Re: Cutting channels & notches in Foam ?

Posted:
Fri Sep 23, 2016 7:19 am
by KCStudly
Chiming in, aye. My thoughts always seem to go back to the old "outer fibers" mantra. The strength of the skin, be it canvas or plywood, comes from it being the unbroken fibers in the outer most fibers in the panel member (be they inside or outside of the camper). When a load tending to bend or deflect the panel occurs, those outer fibers try to stretch or compress, depending on which side of the wall they are on. Now most materials (all?) are stronger in compression than they are in tension so we are mostly concerned with the strength of the outer most fibers in tension. This is where the canvas/fiberglass/plywood excels, it is really strong in tension compared to the foam. The foam isn't all that strong except when we consider it in large areas. In other words, if I poke it, dent it, or snap it in a line it won't take a lot of force to fail, but if I spread that force out (using canvas, FG or plywood) over a larger area the numbers go up dramatically.
Not that it was proposed, but what you really don't want to do is apply the stick framing to the surface of the foam and then try to skin over the irregular surface. For one the "sheet goods" are far easier to apply "in the flat"; you will have trouble getting it to lay into and stick in the inside corners. But the bigger reason is that you have now interrupted all of those fibers that no longer have a straight line of tension. Essentially you will have created a stretchy spring. So if you plan to surface mount sticks, do it after the skinning. For an afterthought addition such as a kids bunk, or internal support for a roof rack, this is a decent compromise, but for my sense of aesthetics and design I wouldn't plan it this way from the start.
Again, maybe the loads are small enough, and the structure strong enough to get away with just about any configuration, but why not optimize every aspect with good design practice? Done right you can have a litter structure that is as strong, or one that weighs the same and is stronger.
Here's another way of looking at it. Which do you think is stronger, if I glue the head of a bolt onto a flat surface and then pull and pry on the threaded end of the bolt, or if I run the bolt thru a "plate" with a washer under its head and then pull on it. The glued on bolt is only as strong as the glue joint and the fibers immediately surrounding the joint and is less capable of handling lateral forces (side leverage), whereas the thru bolt distributes the load over a much larger area of the wall, taking advantage of the unity of construction as well as having more lateral support. Embedding the stick members in the foam behind the skin is essentially the same as thru bolting with a washer.
Also, from an appearance and comfort level (i.e. not bumping into edges or sleeping up against a lump) I like smooth walls better.
Pays yer money and makes yer choice.
Re: Cutting channels & notches in Foam ?

Posted:
Sun Dec 04, 2016 8:57 pm
by rustytoolss
KCStudly wrote:Chiming in, aye. My thoughts always seem to go back to the old "outer fibers" mantra. The strength of the skin, be it canvas or plywood, comes from it being the unbroken fibers in the outer most fibers in the panel member (be they inside or outside of the camper). When a load tending to bend or deflect the panel occurs, those outer fibers try to stretch or compress, depending on which side of the wall they are on. Now most materials (all?) are stronger in compression than they are in tension so we are mostly concerned with the strength of the outer most fibers in tension. This is where the canvas/fiberglass/plywood excels, it is really strong in tension compared to the foam. The foam isn't all that strong except when we consider it in large areas. In other words, if I poke it, dent it, or snap it in a line it won't take a lot of force to fail, but if I spread that force out (using canvas, FG or plywood) over a larger area the numbers go up dramatically.
Not that it was proposed, but what you really don't want to do is apply the stick framing to the surface of the foam and then try to skin over the irregular surface. For one the "sheet goods" are far easier to apply "in the flat"; you will have trouble getting it to lay into and stick in the inside corners. But the bigger reason is that you have now interrupted all of those fibers that no longer have a straight line of tension. Essentially you will have created a stretchy spring. So if you plan to surface mount sticks, do it after the skinning. For an afterthought addition such as a kids bunk, or internal support for a roof rack, this is a decent compromise, but for my sense of aesthetics and design I wouldn't plan it this way from the start.
Again, maybe the loads are small enough, and the structure strong enough to get away with just about any configuration, but why not optimize every aspect with good design practice? Done right you can have a litter structure that is as strong, or one that weighs the same and is stronger.
Here's another way of looking at it. Which do you think is stronger, if I glue the head of a bolt onto a flat surface and then pull and pry on the threaded end of the bolt, or if I run the bolt thru a "plate" with a washer under its head and then pull on it. The glued on bolt is only as strong as the glue joint and the fibers immediately surrounding the joint and is less capable of handling lateral forces (side leverage), whereas the thru bolt distributes the load over a much larger area of the wall, taking advantage of the unity of construction as well as having more lateral support. Embedding the stick members in the foam behind the skin is essentially the same as thru bolting with a washer.
Also, from an appearance and comfort level (i.e. not bumping into edges or sleeping up against a lump) I like smooth walls better.
Pays yer money and makes yer choice.
I'm getting to the point of my Foamie project that I really need to think about, How I'm going to attach cabinets, shelves etc to my foam walls . (I have not yet installed the walls). But I want to plan out the places to notch the foam for wood (2x2s) supports. Can you post some pictures of what you consider to be good ways to go about this, or maybe list a link that shows what I should do.

Re: Cutting channels & notches in Foam ?

Posted:
Sun Dec 04, 2016 10:17 pm
by ghcoe
Re: Cutting channels & notches in Foam ?

Posted:
Mon Dec 05, 2016 12:10 pm
by KCStudly
I don't have enough time at the moment to pull specific links to the areas of my build (link in signature line), but essentially I used a minimal 2x2 wall sill and door frame with 1-1/2 thk foam butt glued; then I pocketed from either the inside or outside for 3/4 (1x) blocks only where I knew I would need a screw (except for at the bulkhead and fender locations where I used full height 1x4's). For most of these I used std 3-1/2 x 3-1/2 square pine 1x block and a router template held in place with temporary drywall screws, fired up the shop vac with its hose taped to the router and used a guide collar on the base plate. Then I cut the corners square with a steak knife and glued the blocks in "in the flat" under gravity clamps using GG. Then I put the inner skin on.
The trick is doing enough planning to figure out where all of the blocking needs to go. This is where having a detailed scale drawing and/or CAD model really helps; but you still need to plan (Got coat hooks? Dome lights? Light switch plates? Pillow lights? Cabinet face frames, running lights, galley light, fenders, porch lights, door keepers (that hold your doors open), wrap around rock guards, side table mounting rails, etc.)
Re: Cutting channels & notches in Foam ?

Posted:
Mon Dec 05, 2016 12:22 pm
by rustytoolss
Do you line the notches with canvas (making them somewhat wider) for extra strength ? I would doubt it, but just asking.
Re: Cutting channels & notches in Foam ?

Posted:
Mon Dec 05, 2016 3:18 pm
by KCStudly
I made mine a very snug fit wherever possible and relied on the expanding glue to do the rest, where not so good. (Not sure I under stand the question thou...)
Re: Cutting channels & notches in Foam ?

Posted:
Tue Dec 06, 2016 6:36 am
by GPW
QUOTE: “ The trick is doing enough planning to figure out where all of the blocking needs to go. “ ... Sage advice !!!

Plan Ahead ...
Our preference for notching is makng small wires, bent to the shape of the cut and inset into a scrap of wood .... controlled by a Variac , or model train transformer ...
Re: Cutting channels & notches in Foam ?

Posted:
Wed Dec 07, 2016 6:53 pm
by rowerwet
I have my galley shelf supported by 1/4" plywood strips that run from the shelf to the floor. Since plywood would buckle like this, I anchored it to the foam with PLpremium construction adhesive.
I used the bit holder extension on my drill to bore a row of holes every 4 inches or so.
Each hole is an inch deep or so.
Then jammed the nozzle of the PLp tube all the way into the hole.
As I pumped PLpremium into the hole , I let the nozzle push out of the hole.
The plywood was glued to the foam and held in place with coarse thread drywall screws.
PLp is a poly adhesive that swells as it cures, each hole packed with PLp becomes an anchor locked into the foam.
I used this for the galley opening frame as well.
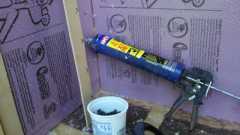
Re: Cutting channels & notches in Foam ?

Posted:
Thu Dec 08, 2016 12:22 am
by Andrew Herrick
rustytoolss wrote:Do you line the notches with canvas (making them somewhat wider) for extra strength ? I would doubt it, but just asking.
Do you mean line the routed channels with canvas?
I was under the impression that Gorilla glue (or other foam-safe polyurethane glues) would encapsulated the surface of the foam and protect it from localized damage, which I assume the purpose of the canvas would be ... if I'm on the right track, then it seems gorilla glue would be far faster?