flip18436572 wrote:alffink wrote:
I just have the rigid foam sheets attached to the floor, which has been coated with asphalt slurry, .
How does the rigid foam stay connected to the trailer? Do you have pictures of you trailer in the process of the build? I know that glue does not hold forever, and it seems to fail in the changing winter temperatures of Iowa. Thanks.
I used pretty much the same method as Al Fink during my 2006 build. In Aug 2008 I finally 'plumbed' my TD for the PetCool A/C, & took the following pic of the underside. The TD at that time had been pulled more'n 6K miles over all kinds of roads'n trails, paved, unpaved, & muddy potholes, in every kind of weather. You can see that the foam insulation is still nearly pristine. As of today, & another 4K+ miles, it still looks the same. The A/C plumbing has actually picked up more 'dirt' than the trailer chassis or the bottom of the floor. I also did like Al says, cut the foam to be a 'press fit' on the still 'sticky' ashpalt coating, then I went a step further & cut small 'batten's from 3/4" square stock & stapled them to the 2X2' floor framing. Nothing has moved yet -
Underside of TD in Aug '08 after 6K miles
Underside of floor undercoated & insulated -
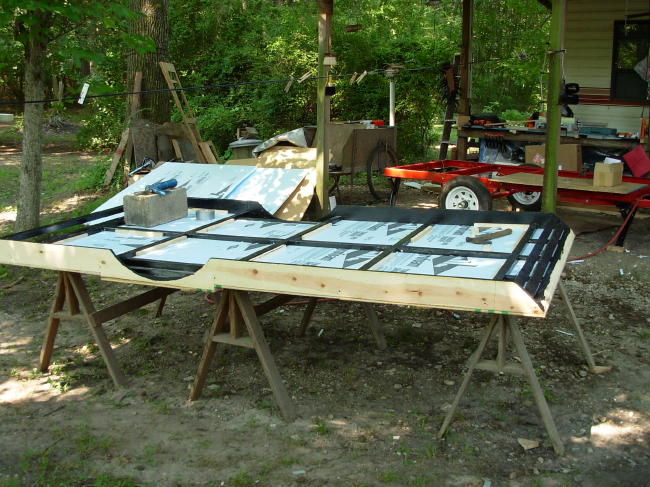