Mel, there's a huge gain in using a heavier cloth - 6oz is really just for sheathing to help with epoxy's inherent brittleness. It's really a 'starting point' or a 'bare minimum', there are plenty of heavier and more structural options. I have some bits of a heavy structural cloth (Dynel) that I use for 'hard points' in a layup. Dynel is a trade name, but it's like 'Kleenex' - it's a heavy cloth that combines both 90 degree and bias roving stitched together. I use it most often in lieu of butt blocks for assembling long hull and deck planks from 8' ply sheets. The down side is that it takes a lot more epoxy to wet out so, while it's a low profile and low weight option, it's definitely a more expensive way to go. I burned through about $40 worth of epoxy today and the only actual cloth I got down was about 15sq ft of 6oz...the rest was fillets, sealing ply, etc.
One option might be to use something like a 12" Dynel tape around the rockers of the trailer and maybe up the front wall. If you put it on before the 6 oz sheathing, the finish will be continuous. Anything that penetrates that layup would probably punch through plywood anyway. What you need is up to you, so maybe try laying up some cloth on a piece of foam and see if it's what you like - you can go with a heavier 90 deg cloth (called roving) or a structural cloth like Dynel, or Carbon/Kevlar, etc. It's all about what you need and what your budget looks like.
I'll grab some pics of the stuff tomorrow.
I'm kicking around the idea of allowing for one of those rotating boat racks you see on slide-in campers - a bushing secured with Dynel could be a quick and easy way to build for it, whether or not I actually use it. I'm starting to layout the side panels so now's the time...
______________________________________________________________________________________
Some reference pics I thought might be handy:
This is the resin I use most. It's runny so it wets out really well but it can suck up a lot of filler - good thing filler is cheap !
That amount of resin was about $150.
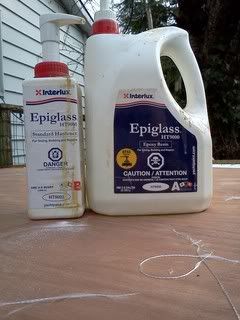
This is cabosil, a structural filler. This is a fibrous powder that makes the strongest epoxy adhesive you can come up with. It can be combined with other fillers to customize your adhesive, but should be added first since it takes a fair bit of resin to wet it. Those clumps are from the rough 'hooked' ends of the fibers that do the job, once it's stirred in it blends smooth. If you are using a lot of it, wear a dust mask as it's an irritant and you'll be sneezing for sure. This pot was about $7.
Microballoons are tiny glass bubbles that break when they're sanded, which makes them an excellent fairing compound. Being mostly air, the compound is lightweight and easy to sand. The texture is identical to flour. Again, about $7 for that pot.
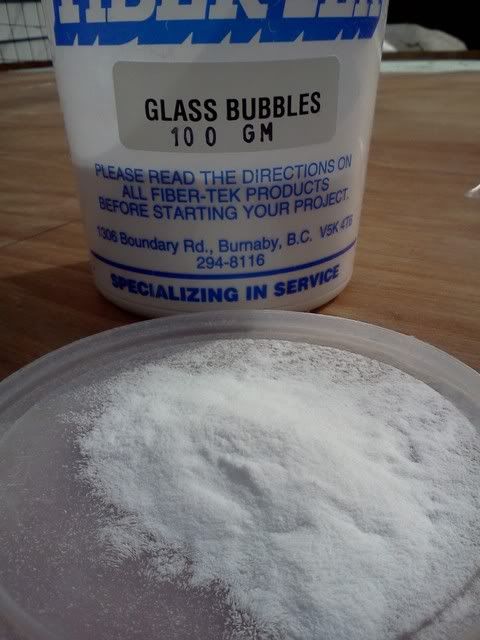
I assume everyone knows this stuff but if not, here's a neat trick for cutting cloth square:
With a 90degree cloth, you can usually pick or pull out one of the threads to give you a clear line to cut the piece off: just cut along that line and your cut edge will always be square to both sides.
