angib wrote:That wheel is going to be free to flop about, isn't it? Two brackets spaced a few inches apart, with rubber inside them, aren't going to keep the wheel pointing straight ahead. Previously those brackets were several feet apart.
Assemble it all and bolt it to something rigid (doesn't have to be the frame) and see how easy it now is to move the wheel sideways.
Here is a better pix of the assembly:
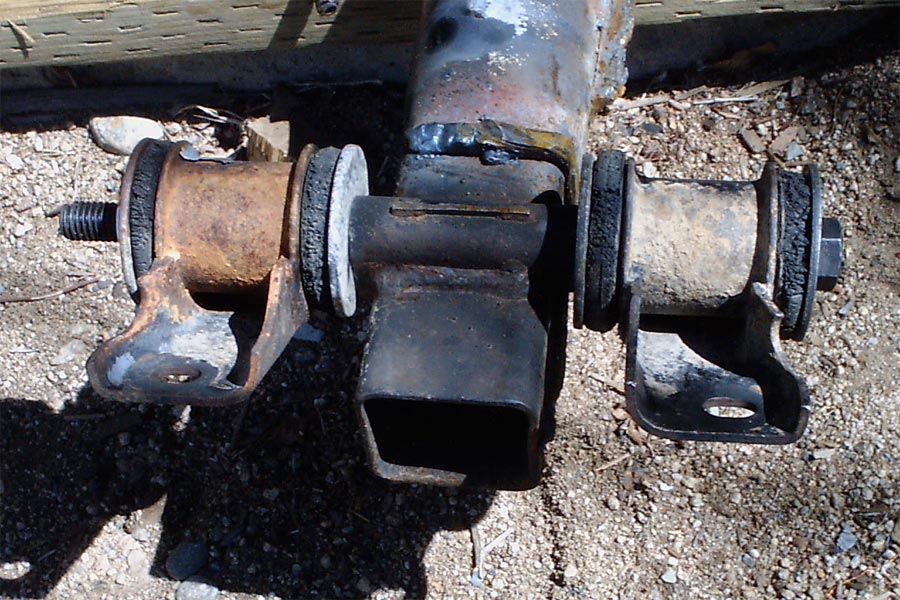
- avll27.jpg (138.43 KiB) Viewed 1424 times
The only thing that you can't see in the assembly is the steel sleeve bushings inside the rubber sleeve. This is what they look like:

- vw.JPG (78.56 KiB) Viewed 1424 times
When I increased the bore to accommodate the larger 1/2 IN hinge pin, all the holes that I reamed had a snug fit. The largest clearance in the system was the metal pass-through sleeve that is welded to the swing arm. I didn't have to ream it since there was enough clearance to accommodate the larger 1/2IN bolt. So by using a slightly larger bolt, I've actually reduced freeplay by chance. Futhermore, as the nut is tightened, everything goes into compression (except bolt of course) and the rubber bushings have a shoulder that keeps everything nice and snug. If I tighten the nut too tight, the assembly will not rotate in the swing arm sleeve without a lot of force to overcome the friction that the rubber shoulder on the bushing is applying. This is a very clever system and that's why the engineers at VW used it. I'll probably experiment with nut torque to get a snug fit on everything, sort of a Goldilocks setting, then drill the bolt and pin a castlenut on so I don't have to worry about the nut vibrating off. I can feel no movement on the bench and I'm confident there will be no unacceptable slop when it's mounted. But of course, I'll check. Thanks for your comments. This helps me rethink the system and makes me sure that I didn't miss anything. Andy