Test fitting the lower actuator brackets with the washers found that they fit very well.
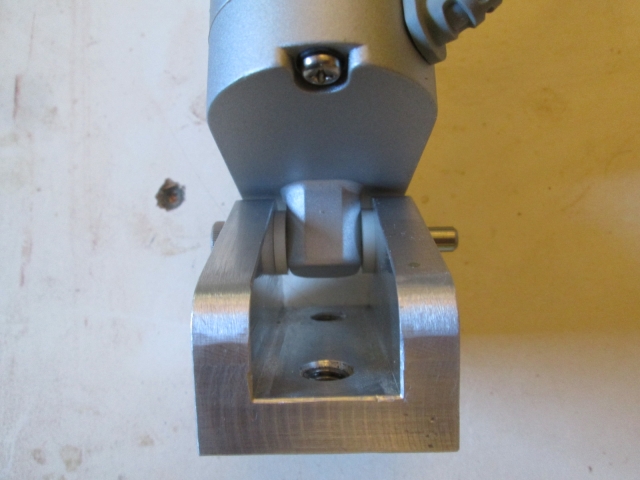
I made the upper washers a little smaller to better match the tips of the upper brackets, which made them a little close to the size of the chamfer in the rod hole. I might remake these with a conical seat to match the rod hole, or maybe a semicircular shape to match the diameter of the rod… or I might just leave them and see how they do, keeping an eye on them in use.
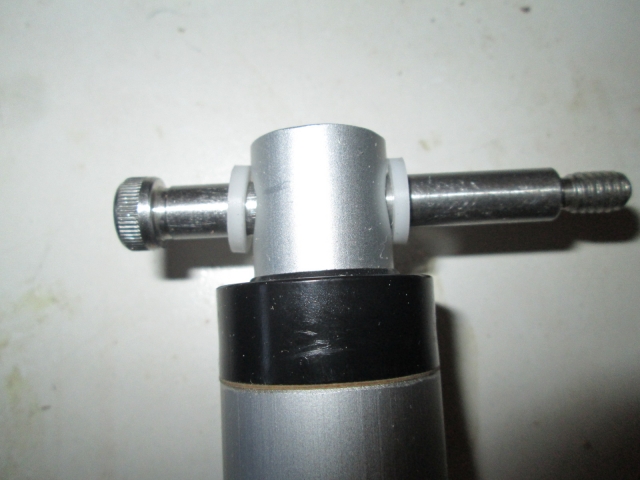
This next picture was kind of tight (big squirrel in a relatively small cage

). I cut a gauge stick that measured off the distance from the inside of the galley wall to the outside of the lower actuator brackets. This made it much easier for me to hold the bracket hard into position with one hand. By letting it hang from the actuator, swinging it hard against the bulkhead and gauge stick at the same time I was able to hold the bracket exactly in position, and plumb, while running the drill thru the guide bushing using the other hand. No slipping around.
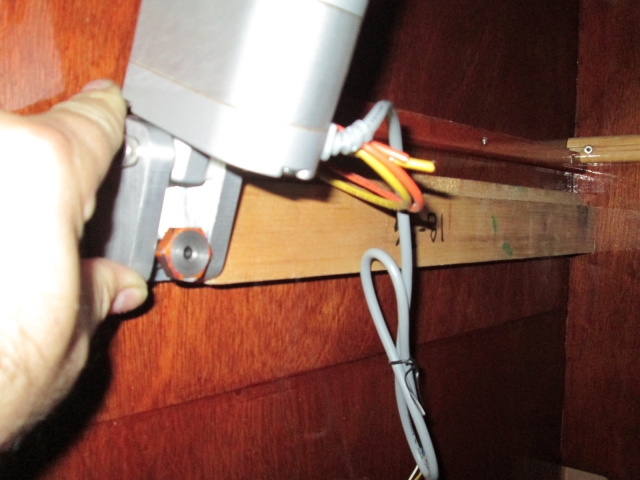
Once the pilot hole was drilled thru (with Karl’s help holding a backing block on the inside to prevent splintering) I stepped up the drill size and opened the hole up to 5/16 inch, matching the bolt size. The oak blocking was plenty hard enough to keep the subsequent drill sizes from wandering.
With the bracket separated from the actuator, Karl ran the lower mounting bolt thru from the cabin side; I repositioned the gauge stick to square the bracket back up, repositioned the drill guide to the upper hole, and drilled the upper pilot hole. Wash, rinse, repeat, and you get two mounted brackets.
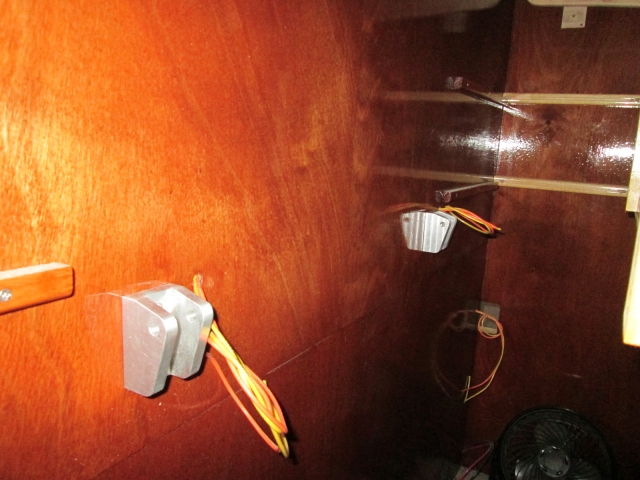
I haven’t made the washer plates yet (wanted to make sure the drilling went accurately first) so we just used some temporary wooden plates for now (drilled right thru them in place at the same time).
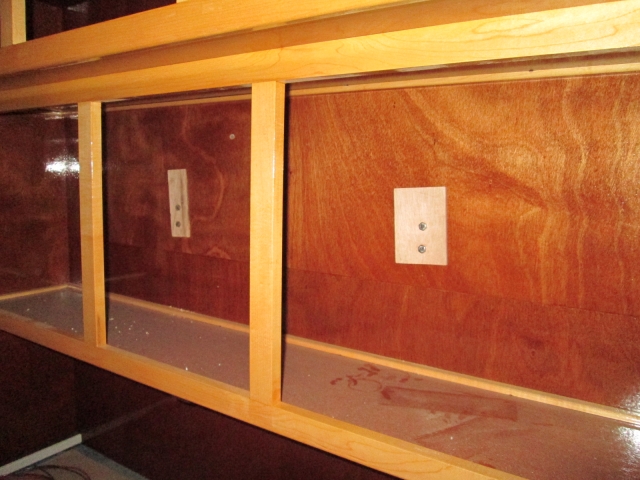
The finished washer plates will be much smaller (similar to the foot print of the brackets), in the same material as the switch plates.
Here is a test fit of one of the actuator assemblies.

With that settled I could get back to fitting the hatch skin; this time the lower section. I took the temporary 2x4 cleat off the lower edge of the upper skin. No surprise that there was a ripple in it. The middle areas between the ribs were trying to spring back.

To help dry fit the lower skin and hold it tight to the bottom of the ribs, just to start for a look-see, I used a couple of scraps of the 5mm ply as shims to space a temporary cleat and get it clamped to the lower hatch spar.
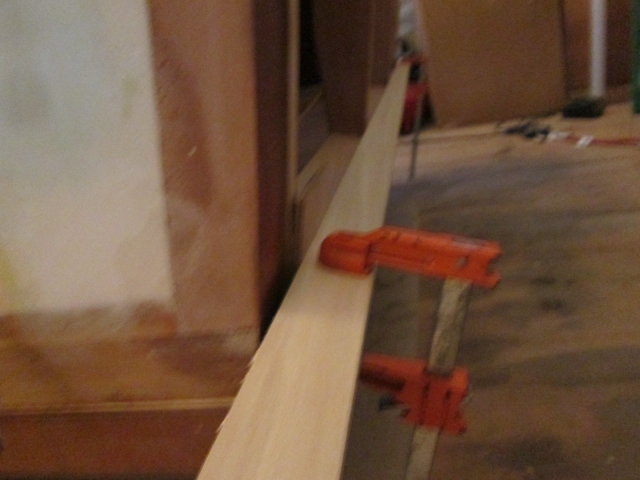
Tucked under the shims I added a sliver of the wax paper box chipboard so that the cleat wouldn’t be too tight.
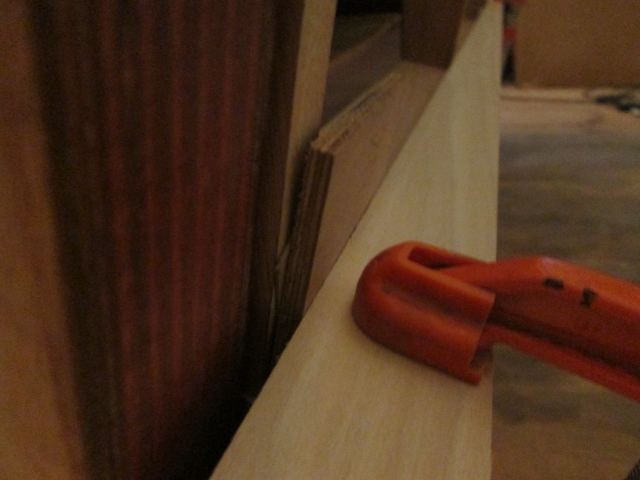
Once clamped I was able to remove the shims and slip the lower skin into place. Here you can see the overlap, excess that will become the backer strip for the panel splice.
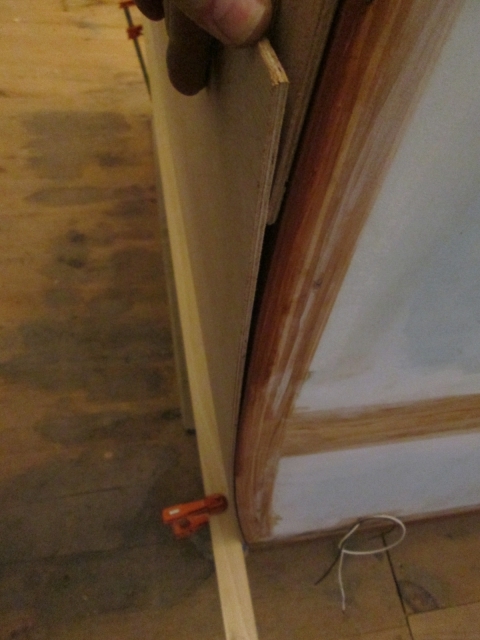
Still a little iffy about how to fit this accurately simultaneously at both the top bottom (maybe have Karl close me in and scribe a line to match mark the edge?), so I decided to sleep on it and come back rested tomorrow.
Train kept a rollin’.