On Monday I made it out to Mecca but didn’t get thing one done. Nothing. Didn’t lift a finger. Instead Karl and I commiserated about our respective days.
Last night I reconfigured the stretcher to full width using the remnant of Tyvek that Karl donated. There was just enough left on the 10 ft roll for me to true up the edge and cut about 8 inches off to get the required width of the cabin.
I used the same long poplar 1x2 as the tack strip for the fixed end, but backed it up with a cedar 2x2 held fast with a dry wall screw at each end. (The 1x2 had flexed some at the front and I didn’t want to fill the 2x2 with holes, but it was long enough and sturdy enough to double up the 1x2.)
Rather than cut the Tyvek to a specific length, I folded the tag end back on itself and used packing tape to form a pocket at the length I needed for the hatch. This gives me options to adjust the length if need be.
Here’s the stretcher clamped to some spacers up at the hatch hinge. The stretcher is folded back up on itself here. Note that the fixed end of the stretcher is up at the hinge so that when it pulls it will pull the lower hatch foam down into the bumper. You can also see the pocket or loop in the Tyvek with aluminum square tube slipped in. (At first I thought I would be using the tourniquet clamps again, so needed something longer than the cabin is wide; all out of lumber so grabbed the aluminum out of Karl’s rack. Turns out I can catch the quick clamps on the bottom of the bumper so did not need the tourniquets.)
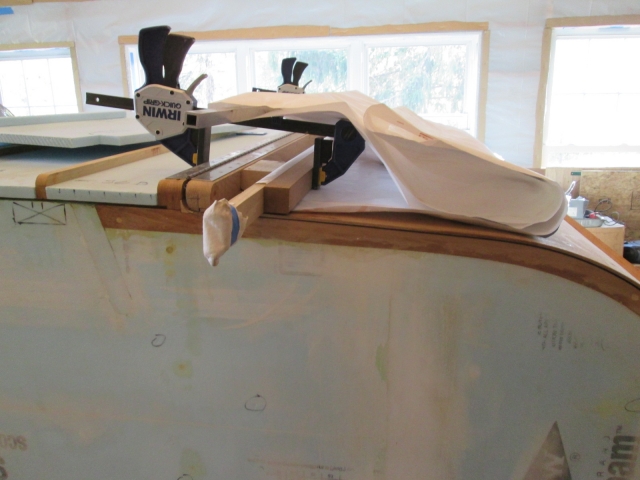
The 2x3 spacers provide clearance for the wire bung donut on the hatch skin.
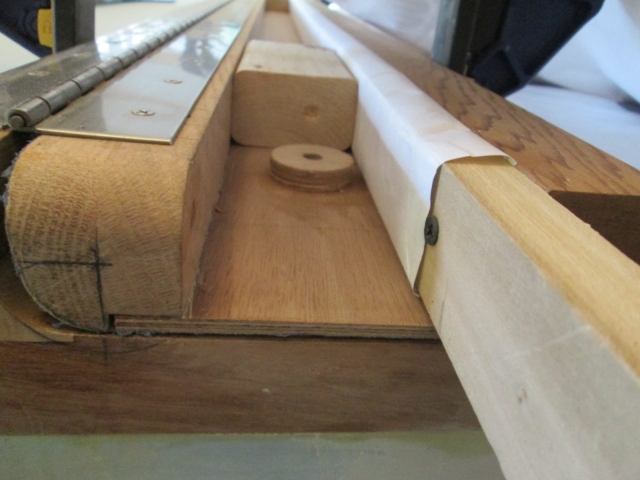
In order to keep the Tyvek even and avoid point load punctures, wherever there is a bump or transition, such as the two small blocks for the galley light screws or the hatch handle blocking, I added temporary fillers/spacers. At the galley light blocking it was just a long strip of Red Grandis laid on top of the blocks.
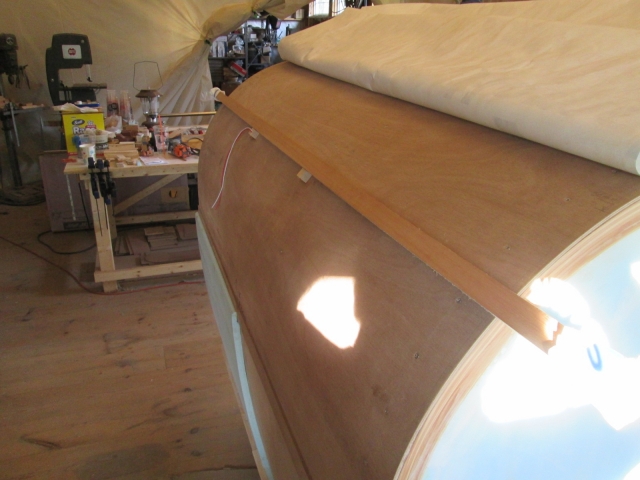
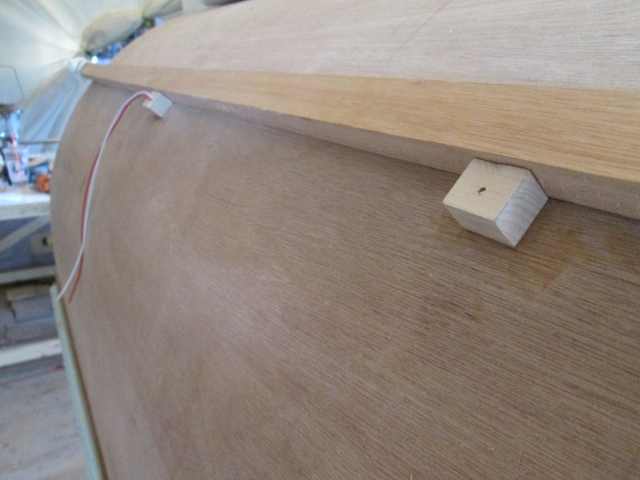
For the hatch handle blocking I taped a couple of lengths of 1 inch foam onto the lower end of the existing first layer of foam on the left…
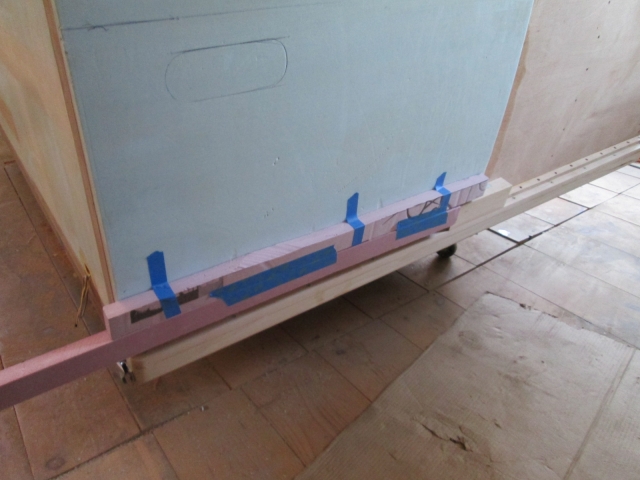
… with corresponding pieces taped to the right hand panel to be glued.
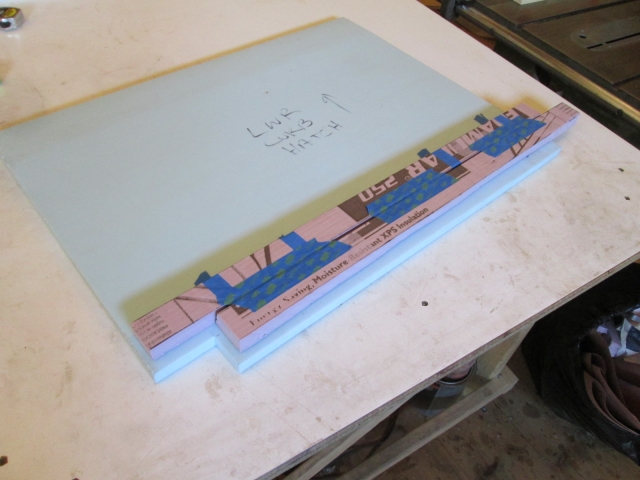
During a dry run I found that the pocket in the Tyvek around the aluminum tried to pull tight into a triangle shape (as predictable), whereas when stapled and rolled on to a wooden beam it would pull from one side only. This triangle tension was enough to shift the footing of the clamps, so I gave the aluminum tube a wrap, clamped a few spring clamps on to keep it from unravelling, and did another dry run; better.
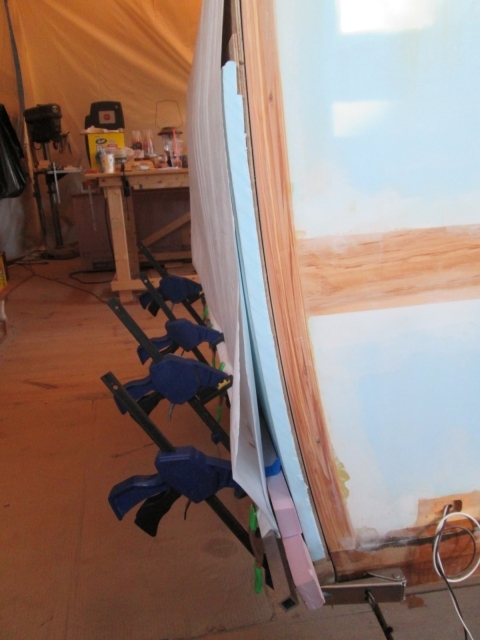
Finally, here’s another look at the top while tensioned. Note that I swapped to screw clamps so that I would have more quick clamps for along the bumper.
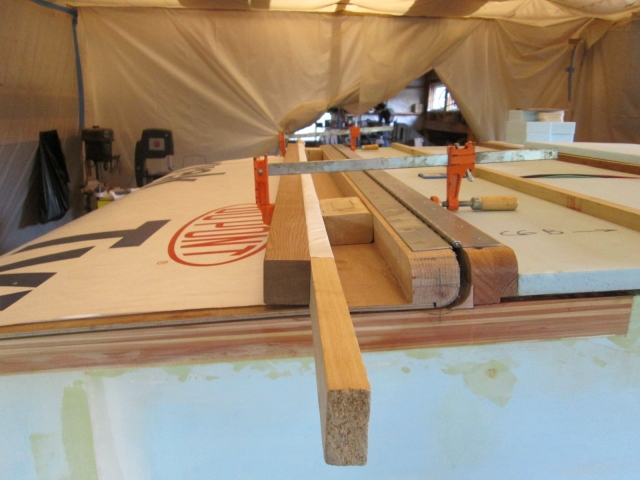
Tonight (Thursday) I went ahead and glued (PL300) the center filler strip of foam at the front of the cabin, just using tape to hold it down.
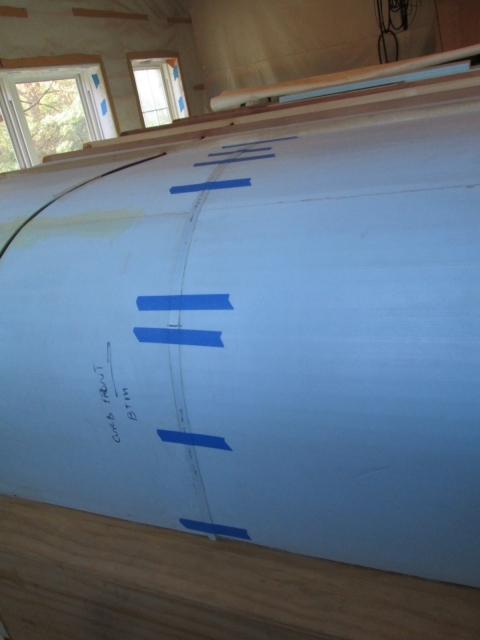
Back at the lower end of the hatch I decided to put the center strip in first, since the right side lower foam panel will want to be pushed into the handle blocking I figured it would work better this way. Since the tape doesn’t like to pull at a 90 deg angle, I had the first opportunity to use bamboo skewers to pin the piece in place.
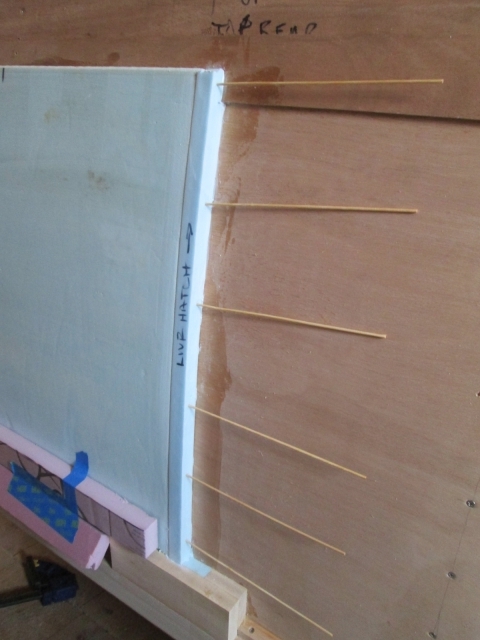
A couple of strips of 3/4 inch foam taped to the edge of the hatch gave me the reference I needed to transfer the profile needed for the clearance light blisters. Using 5 mm ply for the hot wire templates.
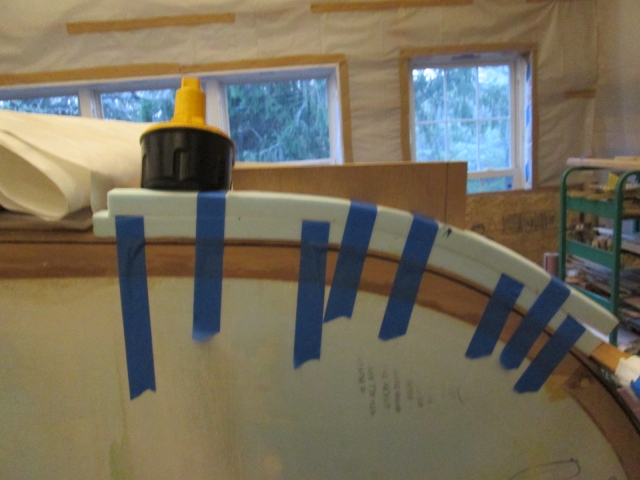
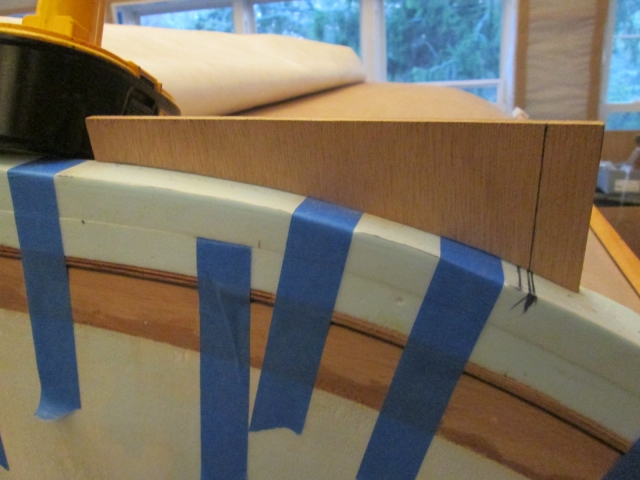
Shown upside down on the bench is one of the clearance light blister foam blanks, the blocking plate, and the two cutter templates. I cut them on the band saw and fine-tuned them with the sanding block to match both the hatch profile and each other.
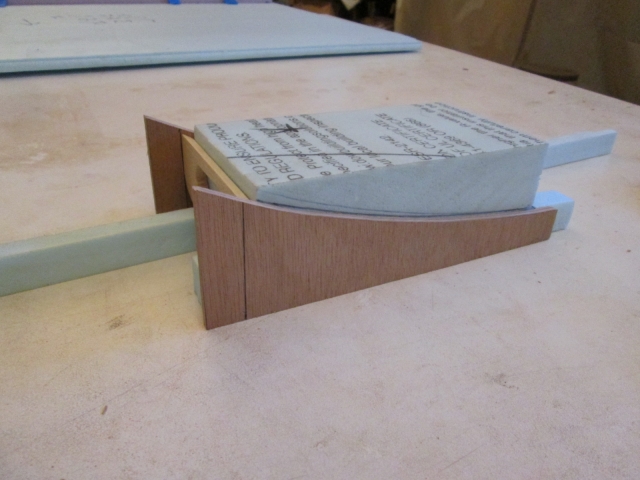
So just a couple of hours each night, but progress all the same.