Kind of took it easy today; only 5 hrs on the build.
Started by fitting the corner blocks for the door surrounds in the second wall. The blocks didn't come out all exactly the same so I took care to chisel out the dado's just a whisker here and there. I also made sure to take from the inboard side so as not to affect the squareness of the opening.
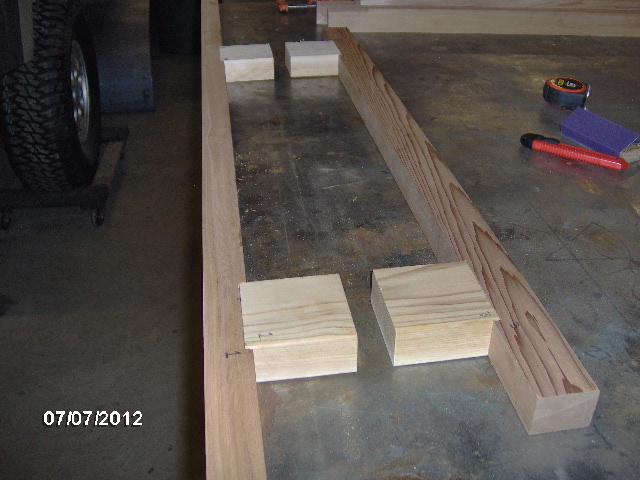
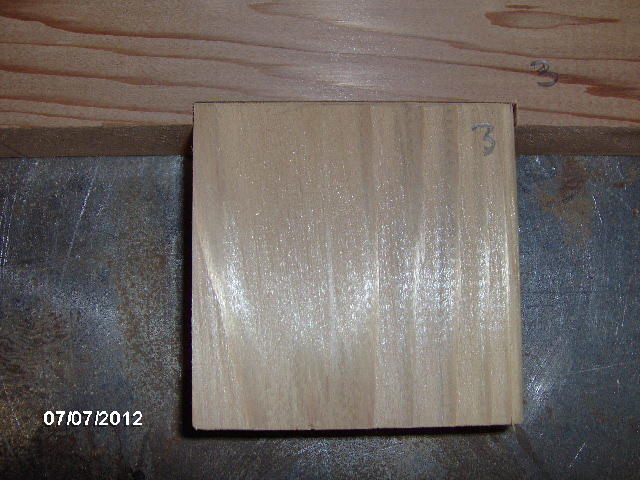
So here comes another confession. I thought I had made the first door surround nice and square, but later realized that I had measured the diagonals from the top ends of the header, which extend past the actual opening...it was easier by myself to just hook the tape over the top corner to measure. Problem was that I had not checked to see that the header ran past the door opening by the same amount at each end, and it didn't. The opening ended up about 1/8 inch out from bottom to top. I will build the door to fit the surround and no one will ever notice. It will be our little secret.
So on this wall I also trimmed the door header so that the distance from the corner block dado to the end of the header was exactly the same at each end.
After making some fine adjustments to the rabbets in the jambs (so that they all snuggled up to the corner blocks well), and dry fitting the rest of the door surround, I decided to lay the first wall on top to double check that the location of the galley under counter drawer glide blocking (which will also set the location of the bulkhead blocking) was identical. After moving the cardboard from in front of the standing parts (to protect against shop grinder and welding splatter, and incidental bumping), pulling the first wall frame down, flipping it, and locating it on top...
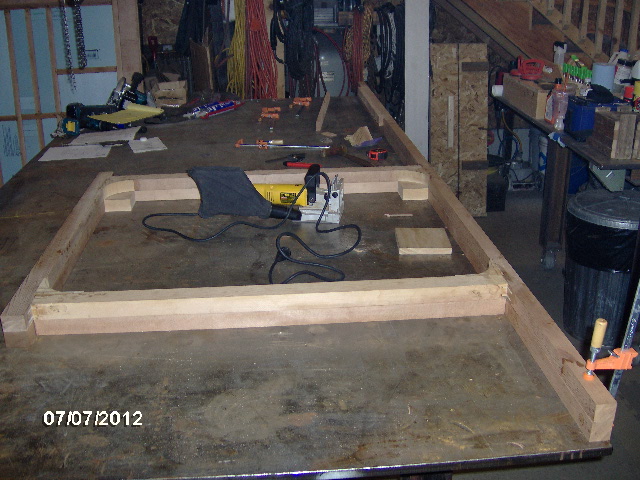
...I found that I had already made a pencil line on the second wall sill when I had laid them out together. Doh! Good photo op, though.
Then I broke out the biscuit slot cutter/jointer and started cutting slots, as before. Cut down the corner block to jamb biscuits, as before.
Then came the glue up. First I glued the corner blocks into the header and sill, then I started to glue the jambs into the lower corner blocks and sill. Uh oh. No slots in the sill for the jambs! Quick, quick, what to do? The biscuit cutter was still sitting right there, but it would no longer fit where it needed to go with the corner block in the way. Pull the corner blocks out quickly before the glue takes? That could create more problems and would be a mess. Glue it together and rely on the biscuits between the blocks and sill, and between the blocks and jambs to tie it all together? Sounds okay, but then the blocks are structural (Damn GPW, I'm doomed).
Do something! Glue it...
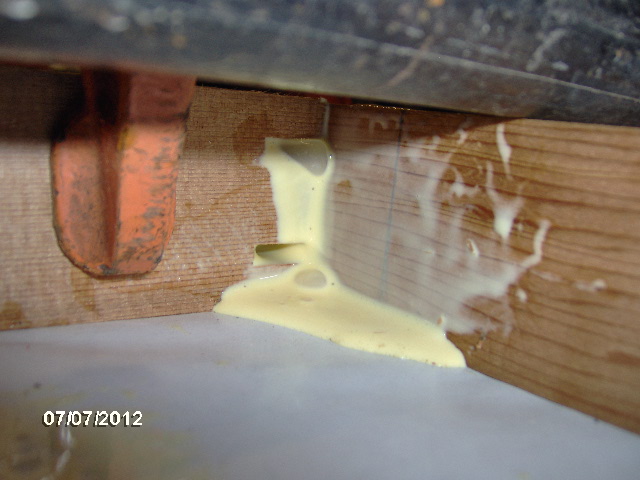

And screw it...
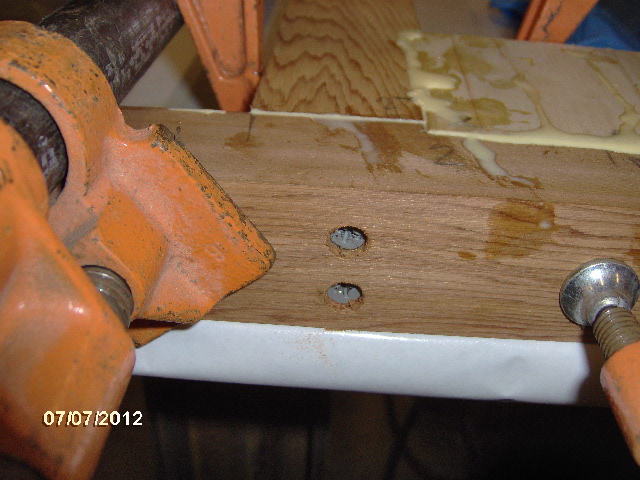
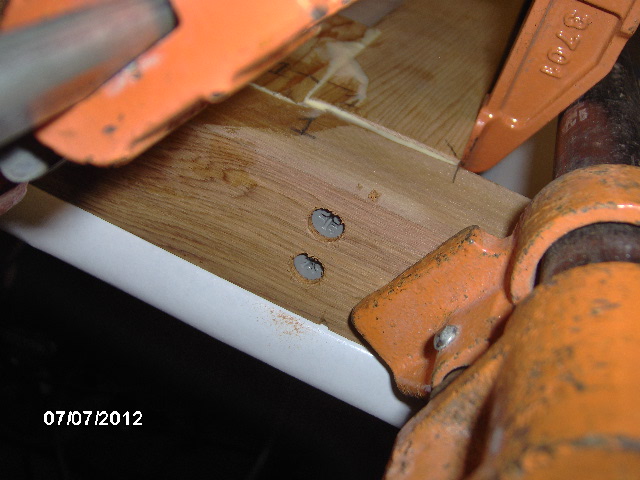
using coated deck screws. The countersinking drill driver was already in the drill, whew.
Followed up with the galley glide blocking and here she is.
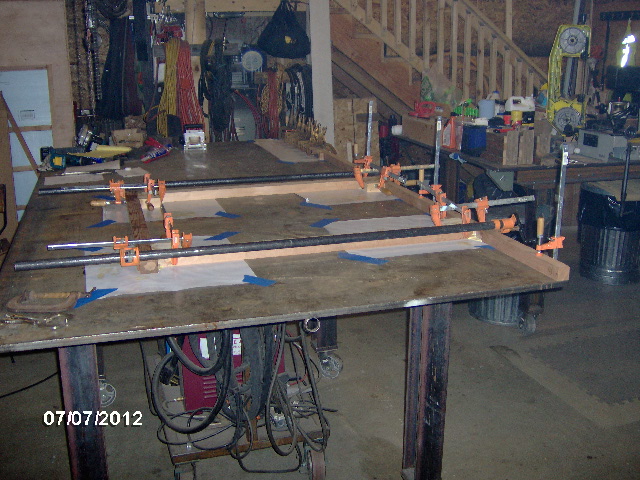
Notice that I used the freezer paper this time and took the time to tape it to the table. That worked out so much better. Didn't have to chase it around, didn't stick to anything and move unexpectedly, and didn't bunch up and pinch into the joint. Win, win. If it solves the discoloration issue with the cedar, then I have got it licked (never know when I might want to use some of that cedar for something that is not getting buried.
Some more detail shots.
The header to jamb joints.
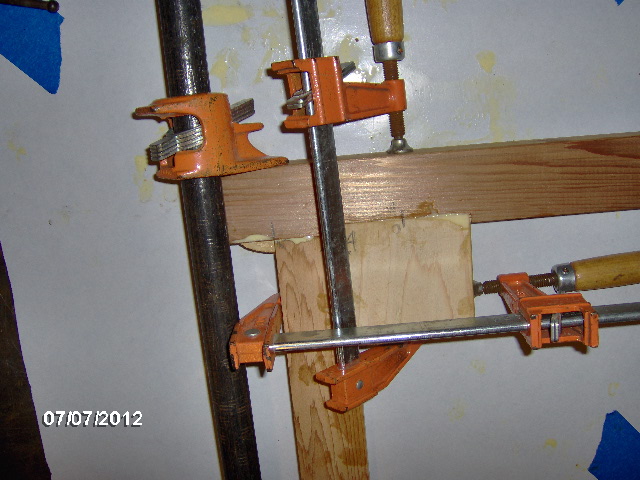
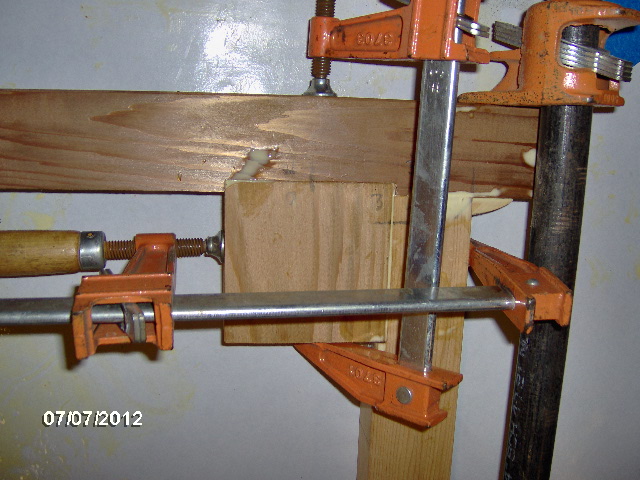
The jamb to sill joints.
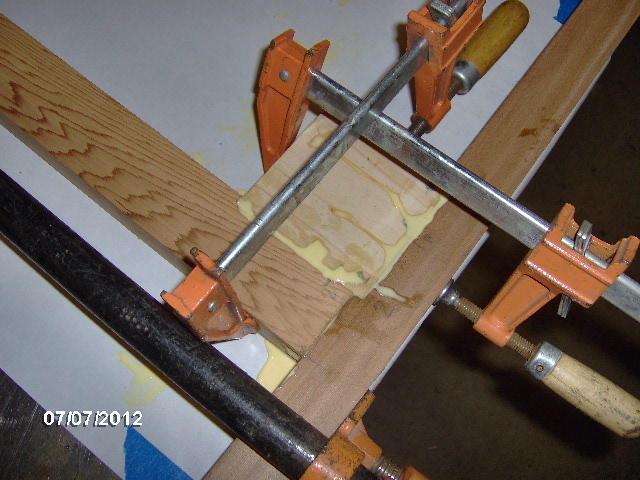
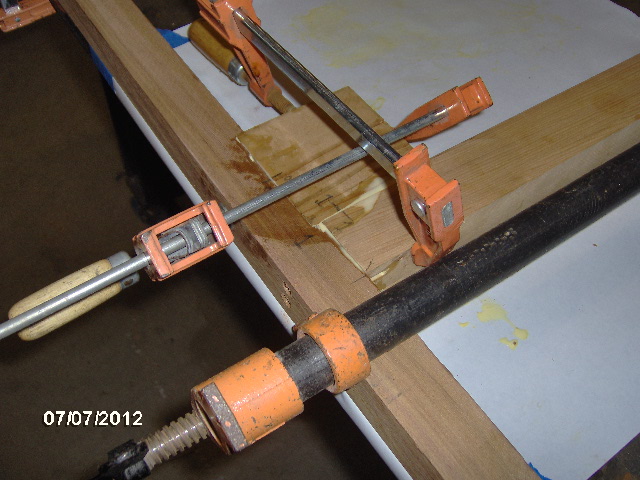
And the under counter glide blocking.
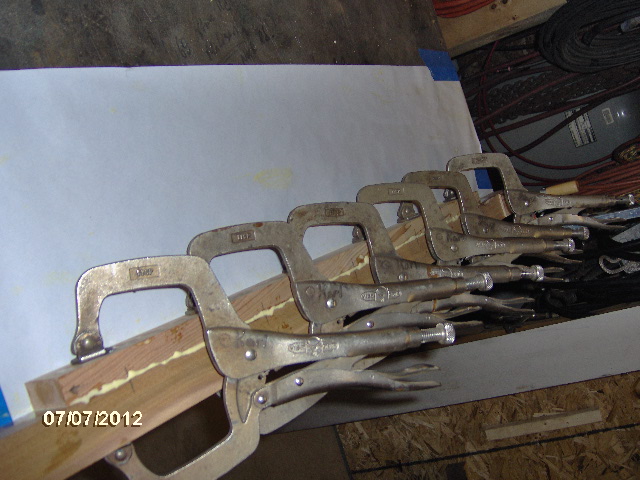
Right now I am only planning to have glides on the curb side where the cooler goes, but it just makes sense to put them in both sides now in case I decide I want to upgrade later.
Before starting the glue up I had thought and Karl had commented that maybe I should work on something else for now and do the glue up later, since it would then be tying up the bench. It was humid, I was in a daze and couldn't really think ahead to well. I knew I wanted to glue up the foam blanks for the walls, and the doors need to be built soon (but need to be fit to the walls so the corner blocks in the wall frames need to be radiused and I'd rather do that with the top bearing bit that I ordered last night). Screw it, just glue it.
Karl and Kris were in the shop welding and grinding on the chip drier project (making noise, dust and smoke), I guess making up for the holiday off, so I had been wearing a dust respirator and hearing protection even after having completed cutting the biscuits slots (...well, almost completed

).
Decided to get some fresh air by using the trailer frame as a bench to cut the piece of 1-1/2 thk x 2x8 ft foam that will extend the larger 4x8 sheets to 4x10.
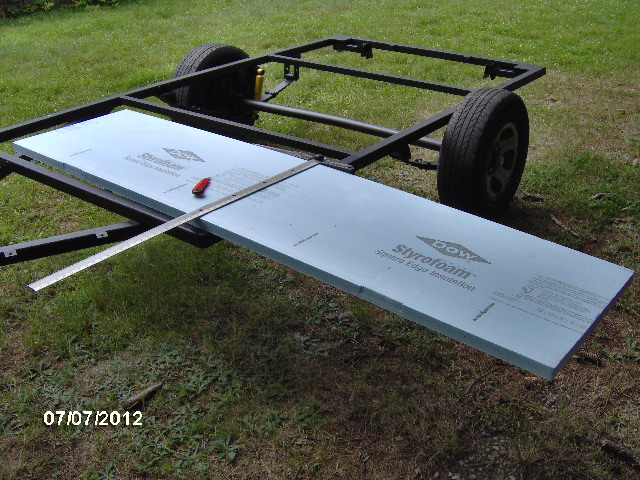
Then it started to rain a little. When I went back in I was still struggling with what to do next. I know, I know, there are so many things that need doing. The under galley dividers are small and I could prep and glue those on the left over corner of the bench, but I have not dimensioned those yet so I might screw them up (now it occurs to me that the skins would have told me what the dimensions needed to be...).
I ended up clearing off the opposite corner of the bench and finished radiusing the first wall door corner blocks using the multi-step router process using the bottom bearing bit.
Here are some pics showing the radiused sanding block I mentioned. It was made by stapling sand paper to the drop piece of the corner block that was rough cut off using the jigsaw.
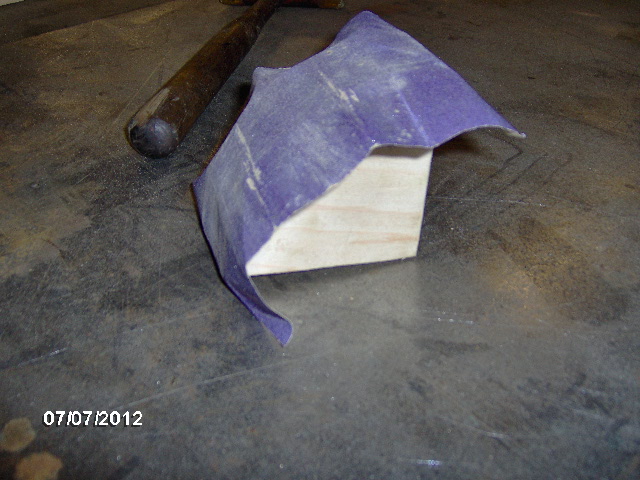
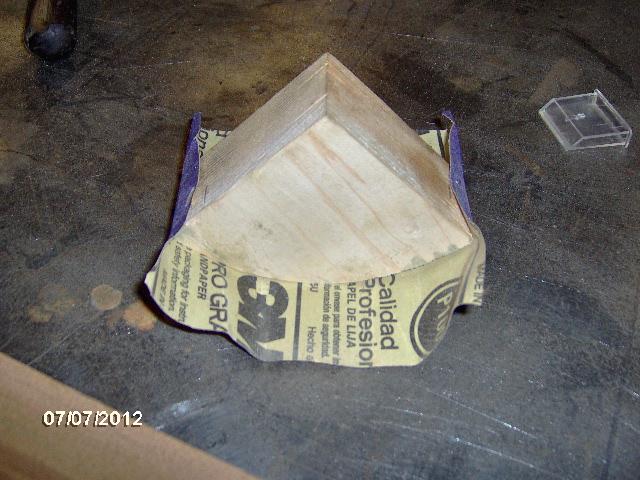
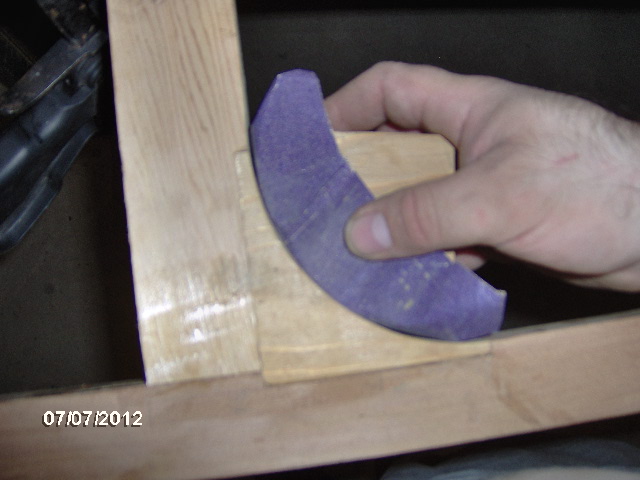
Shortly after those pic's I replaced the sand paper with a narrower strip which made it easier to hold.
And that pretty much did it for the day. Cleaned up after myself. Here is a parting shot showing the under side of the floor, the unskinned side of the galley bulkhead, and the first wall frame standing against Dave's big band saw at the end of the shop under the stairs.
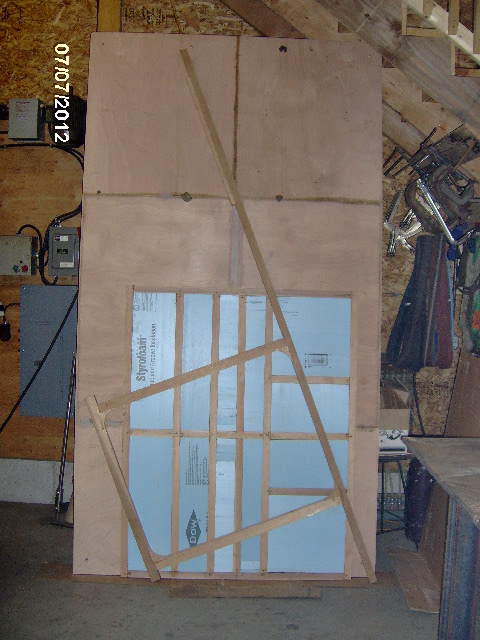
Tomorrow is another day. On the agenda is unclamping and cleaning up the second wall frame glue up; bonding the wall foam blanks with GG; prepping the door frames for glue up, and maybe even gluing up a door.
Stay tuned.
Oh yeah, Rocky the kitten goes to the vet for his healthy kitten check up and comes home with us on next Saturday. It should be exciting and entertaining all at the same time.