My plan was to build the walls first: outer layer, "framing/studs" and the inner skin. I would leave exactly a 1x2 width between the inner wall and studs so that I could 1) install the sidewalls, 2) put the headliner in, 3) sandwich the headliner with 1x2's and 4) put the outer skin over the entire thing. This would make certain that the structure was square and there would be no gaps on the inside between the walls and the headliner. I would have room in the space between the headliner and the outer skin for wiring. Also, when I put the top skin on, I wouldn't have to be accurate...just get it to overhang the sides and trim it flush.
Here is a "Visi-joe" diagram showing my basic intention. I have a detailed diagram in Sketchup, but this was quick to put together using MS Paint. It is not to scale but hopefully you get the idea.
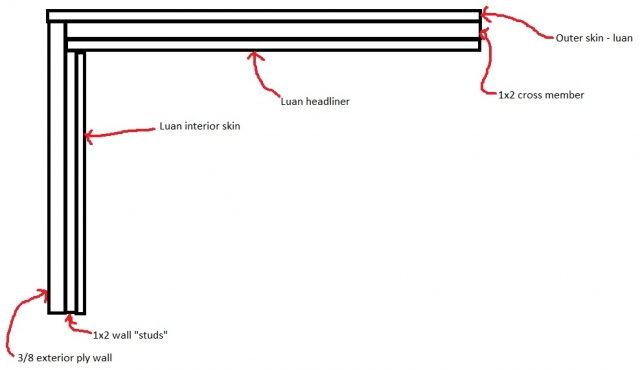
In order to get the curved 1x2 surface, I tried to "finger" the board. This idea failed miserably.
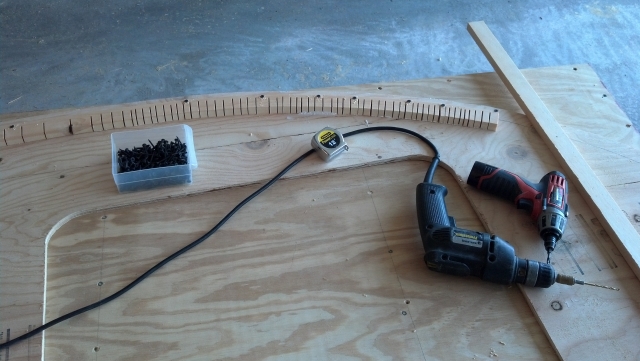
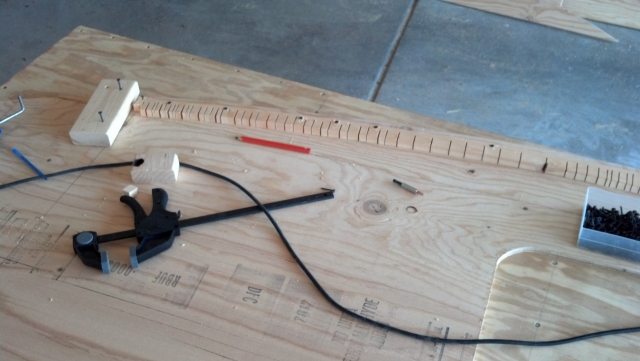
Instead, I decided to frame up the vertical studs, put the inner skin on, then "fill" the gaps with custom cut/curved pieces of 1x2. This worked well.
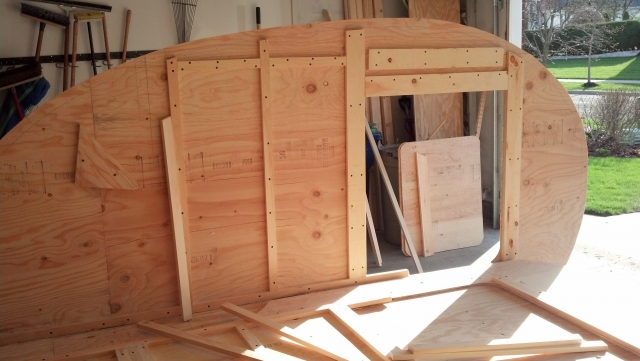
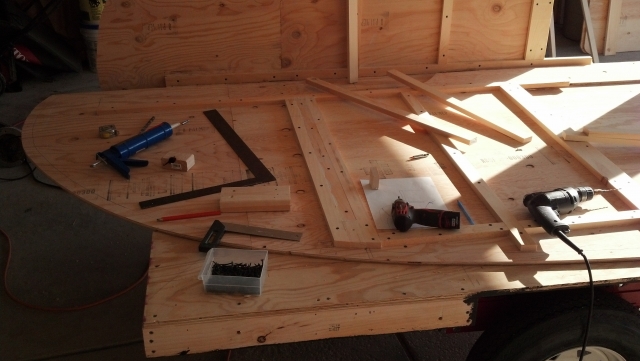
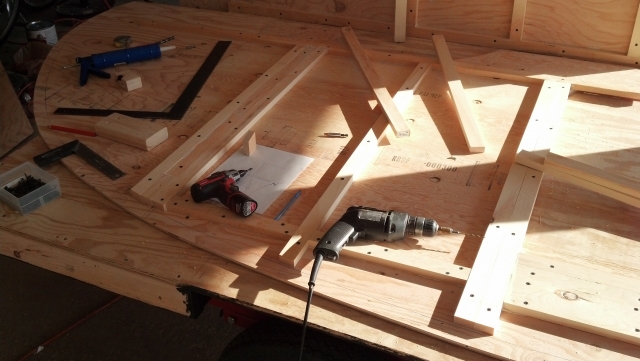