Yeah, I know most folks want to build (hatch included) as light as possible. I don't think the hatch is any place to skimp on strength. It cost me a little more but I bought a sheet of 3/4" cabinet grade birch plywood to cut my hatch ribs from. Those ribs are 11-plies with the grain in each ply running perpendicular to the next. That's a lot of strength to resist twisting, warping, & splitting. I also used 6 ribs rather than 4. Those 2 extra ribs added maybe 3 or 4 # of weight to the hatch but I couldn't estimate the extra strength. The cross pieces for hinge attachment (both on the hatch & the TD roof frame) are solid 1x3" (actual dimensions) oak. I made my ribs approx 1.5" in depth (height) & they're notched to fit the cross piece at the top (as is the oak cross piece). I cut the 1.5x1.5" bottom cross piece from clear spruce & it also is notched (dadoed??) to accept the rib ends. Also placed spacers between each rib at midway point between top & bottom. All joints are screwed & glued with appropriate support pieces placed to accept the 'T' bolt locking mechanism, & the surface mounted tail, turn, brake lights. My hatch is approx 51" from top to bottom thru the curve, & was covered with 2 layers of 1/8" luan (bent cross ways, with the grain). Had to add approx 3" piece at bottom but that area contains the hardware supports so it was no problem. Since I was using 4x10' 0.40" aluminum skin I had to do a little creative 'joinery' near the bottom of the hatch but that worked well & has not been a problem either with leakage or strength.
Dry fitting the rough cut ribs -
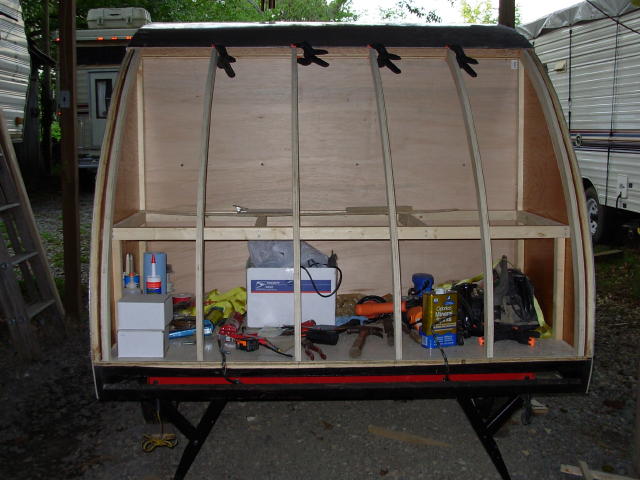
Hatch frame fitted, glued & screwed; supported at correct attitude & waiting for glue to dry -
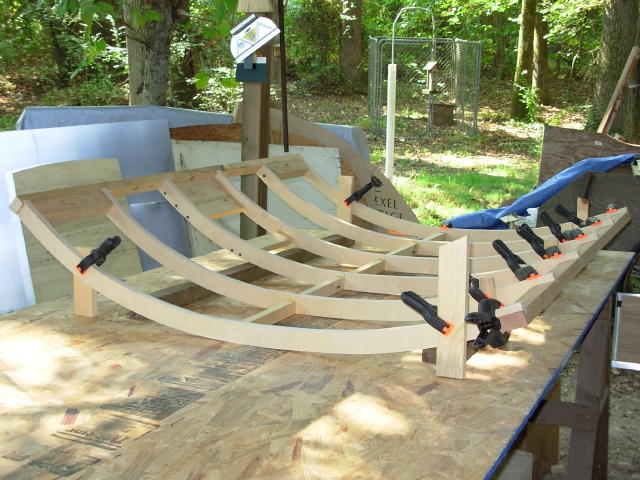
'Finished' ribs & final 'dry fit' after glue & screw -
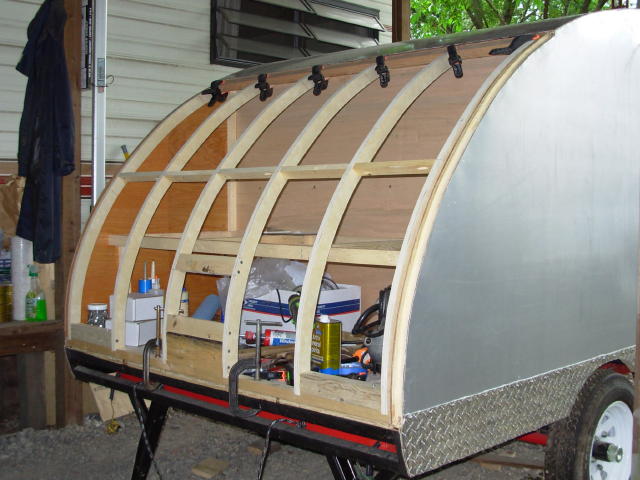
Ready for aluminum skin, trim, hardware, etc. -
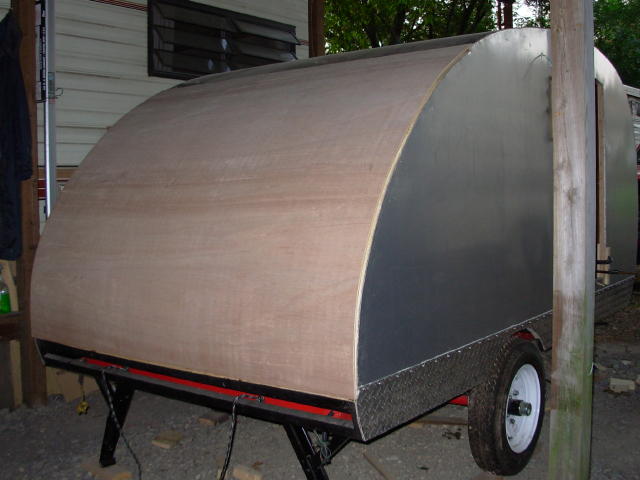
One shot of the rig ready to roll -
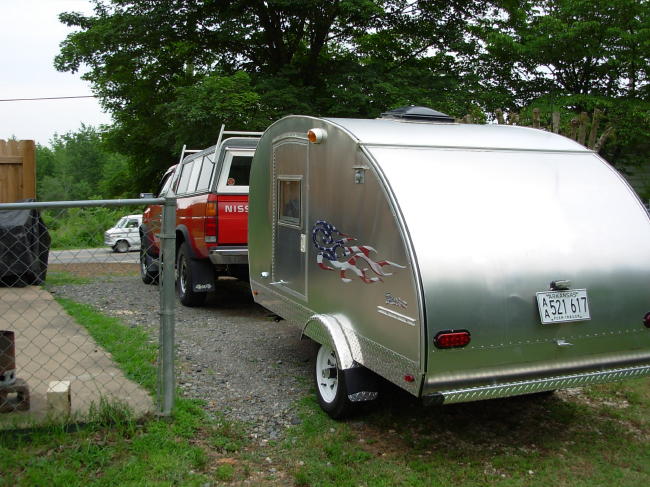
Oh yeah, I had enough of the birch ply left for the 2 counter shelves, the folding table attached, & the side table-
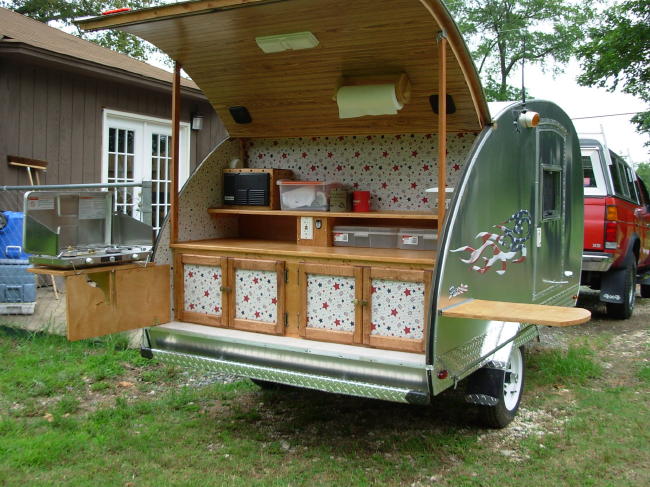