Well I’ve been burning the candle at both ends and have kind of lost track of the days.
Wish I could sleep like my Muggie (Maggie).
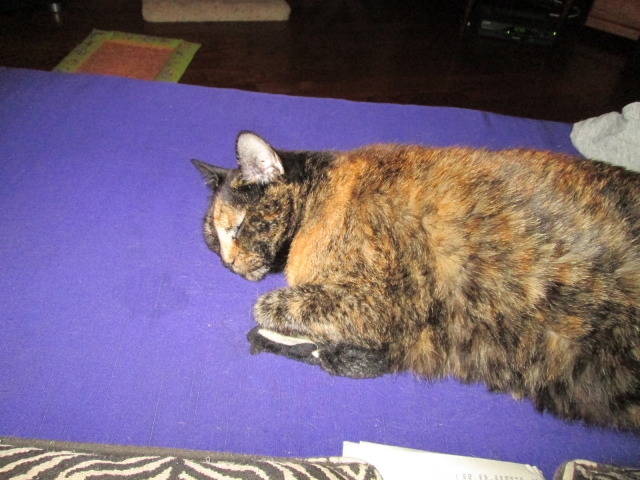
Note the road kill skunk toy (cat nip long since depleted) under her arm… and the dark spot on the hassock where she drooled previously.
Last of the bulkhead skin regluing (Hodder method), King of Clamps.
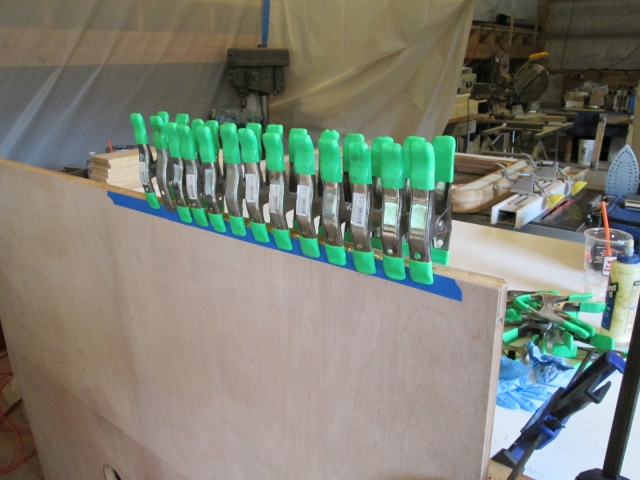
I am pretty sure that I have decided to screw the side walls into the bulkhead from the outside in thru the bulkhead blocking, rather than have Kregg pockets showing thru the back of the bulkhead wall. This means that I will have to fill the foam where the screws go and apply the canvas after. Won’t have to fuss with the extra canvas during erection, at the compromise of applying the canvas in the vertical (but GPW makes that look easy, so…).
However, for the joint between the bulkhead and floor I don’t really want to screw up from the bottom of the floor and risk the sealing issues that might present themselves. So I decided to have Kregg pocket screw holes along the bottom rear of the bulkhead down into the floor.
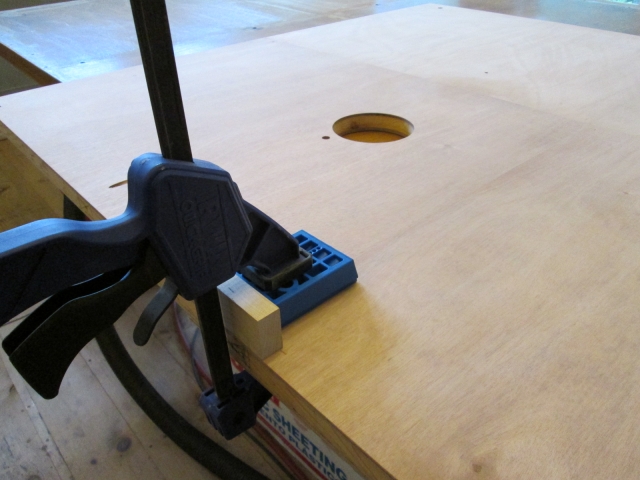
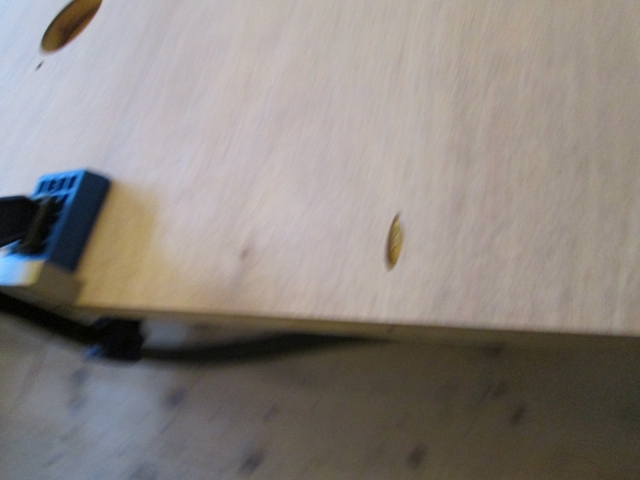
Three holes, one through each vertical member in the field of the bulkhead frame. At least one of these will be hidden by the under cabinet divider for the cooler bay; maybe a second if I decide to add the other divider. If not, this and the middle one can be filled with a plug and stained to try and hide them. They are at the bottom under the counter, so will not be obvious either way.
Then I stained the rear face of the bulkhead. The colors are not true in the pics. In the flash they look orange, and without they look more brown, but w/o the flash you can see the grain better.
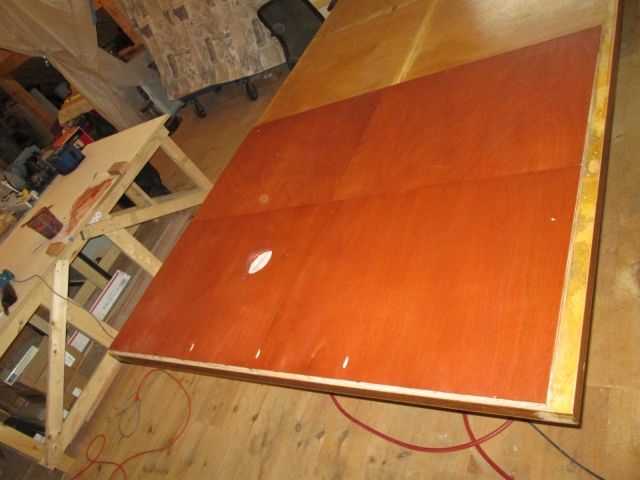
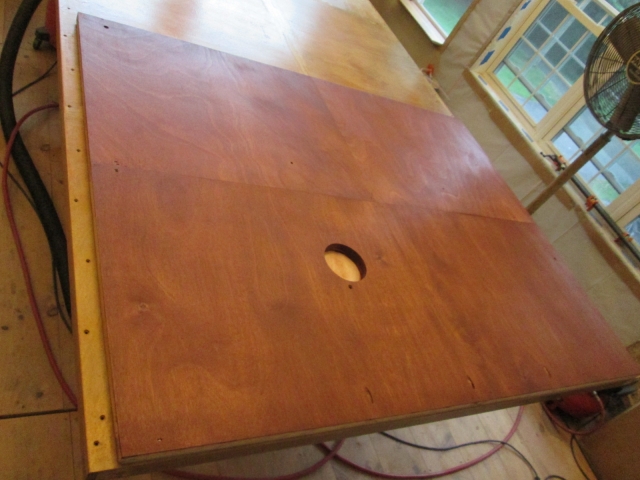
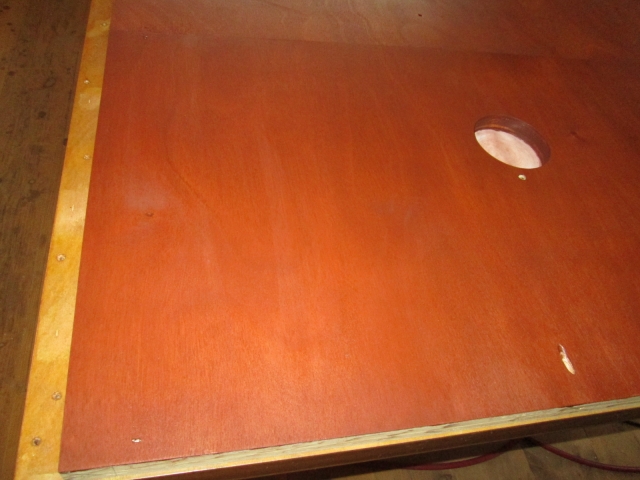
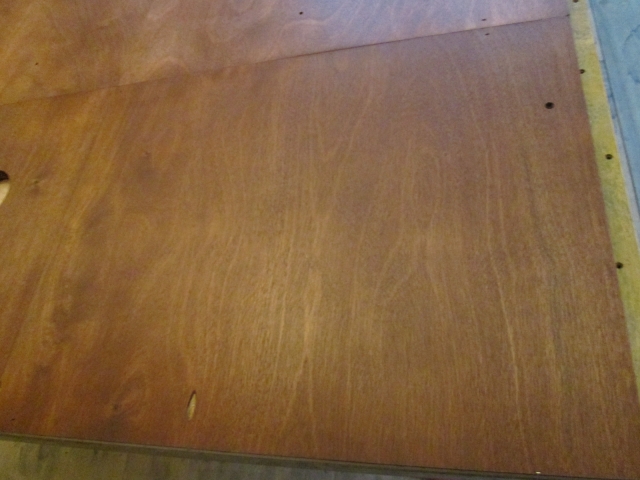
The upper two panels were naturally a lighter color than the lower two; more pink and paler, whereas the lower two were darker, more brown. So the stain ended up lighter on top (lower right in pic).
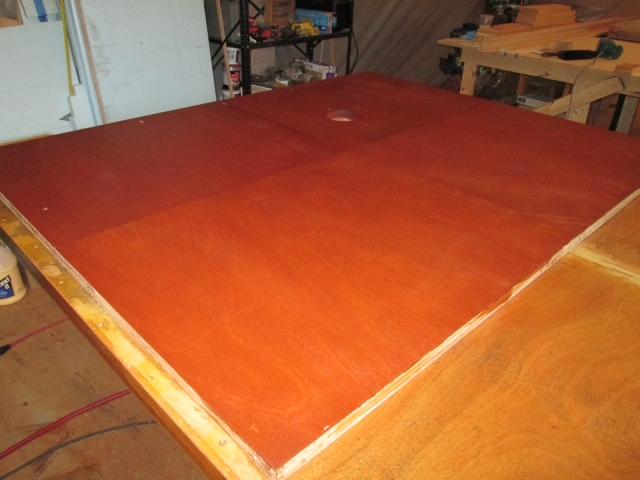
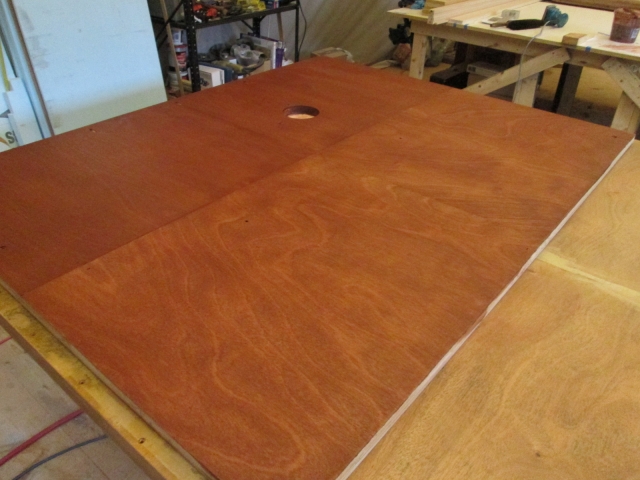
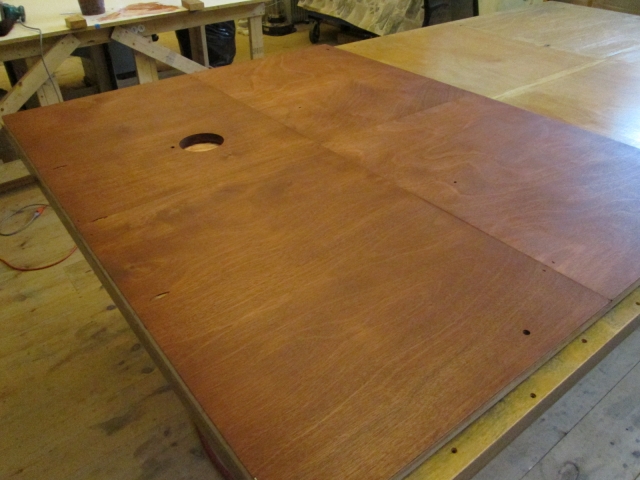
So I rubbed some more stain on just the top and made it a bit more even.

Still lighter on top (to left in this pic).
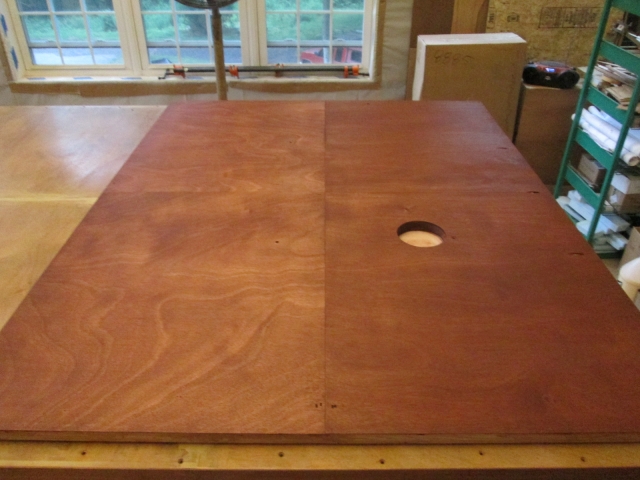
In the vertical in natural light it doesn’t look too bad. With the parting line slightly above the counter top level it might look like a back splash, or be hidden in the shadow of the upper shelves.
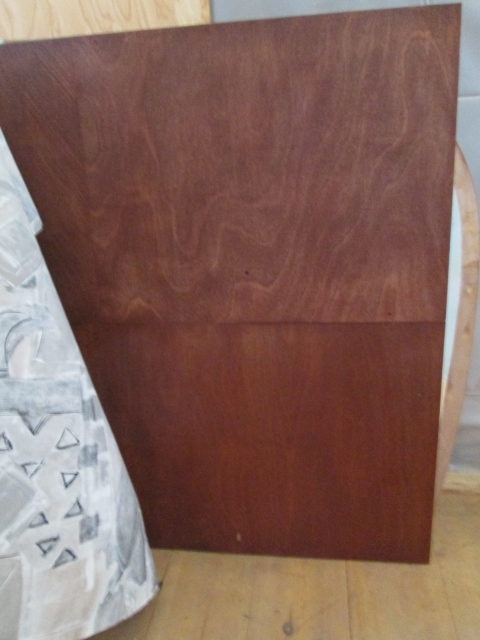
That must have been the 3 hrs I put in on Friday. On Saturday I spent a bunch of time sanding the underside of the floor where the canvas will get glued under, and along the edges.
I was a little surprised that the last coat of TB2 (sealing the rounded over bottom edge) seemed to peel up easily from the previous layers. All future overcoats will get a scuff coat first. Spent quite a bit of time scuffing off the flaky layer and re applying another full coat on the radius.
Once that was done I managed to flip the floor over by myself, tho had to struggle a bit when it wanted to crash into the fan.
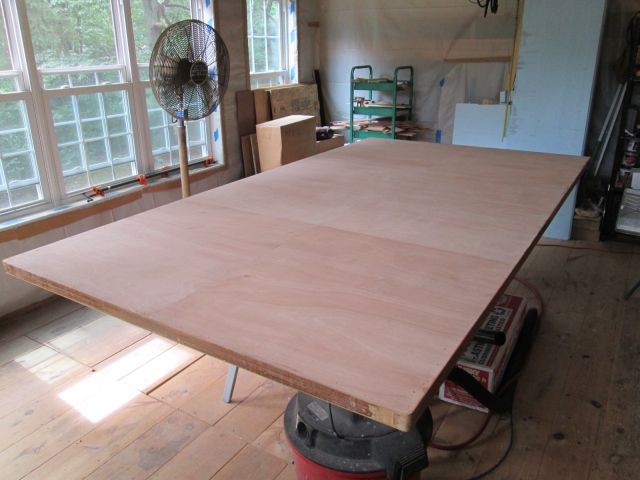
Spent a bunch of time commiserating with Karl, casually hand sanding with 220 grit and the small block and discussing the options for a hard edge along the rear of the galley floor. Then, after he beat feet back to the comfort of his air conditioned house, I ran the RO sander with 320 grit.
Next I masked off the line under the bulkhead (.94 tape on 1.125 wide bulkhead) and under the walls (1.5 tape on about 1.875 thick walls).
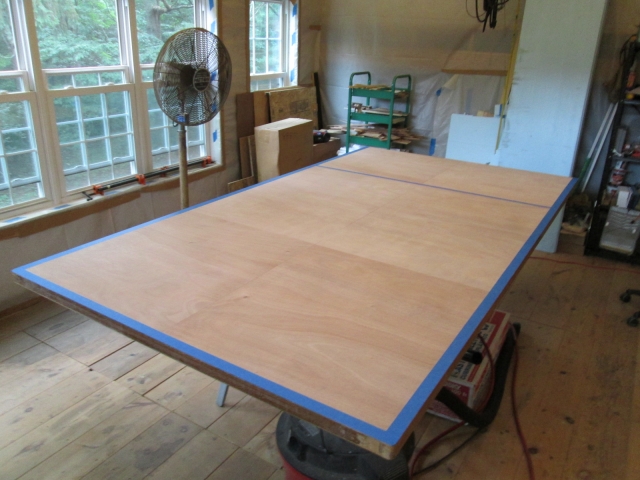
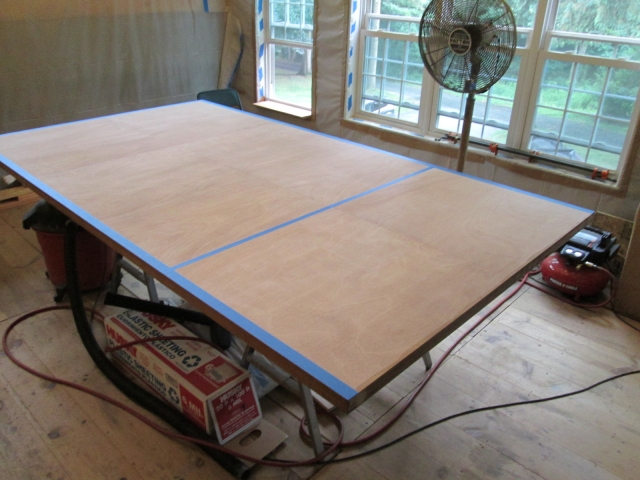
This will ensure that the stain runs all the way under the walls, but will leave plenty of raw wood for the construction adhesive to grab.
Next I rubbed on the stain (the first pic is a pretty good color rendering).
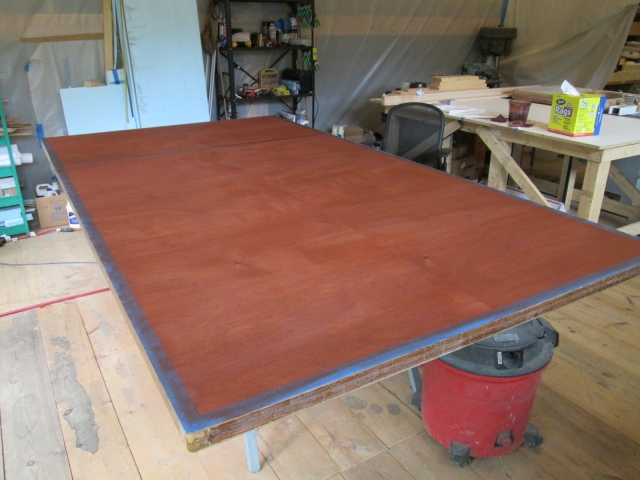
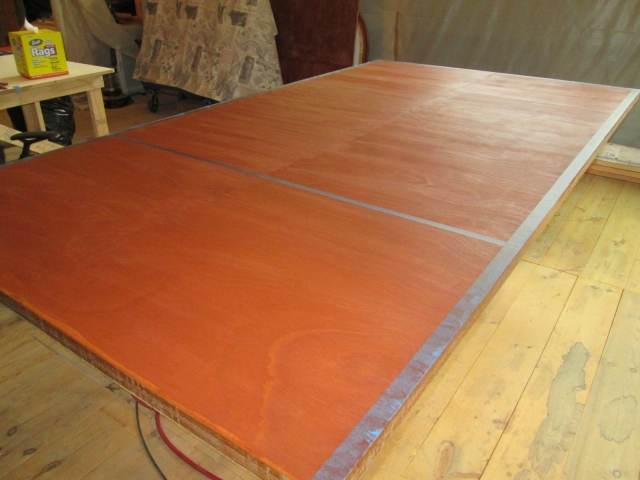
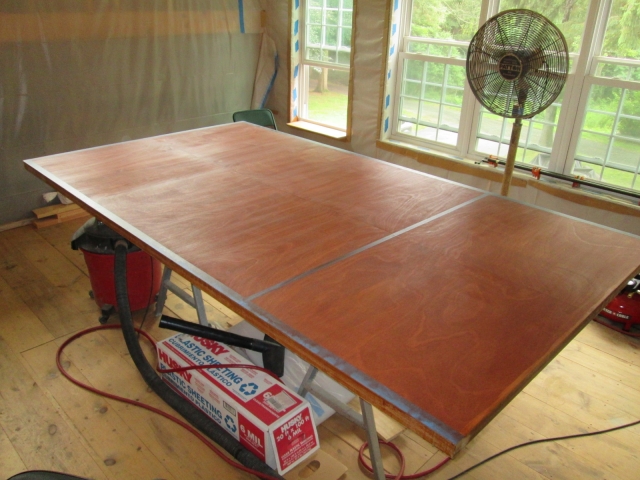
Rubbed on it some more to get the color even, and then some more to remove any excess stain.
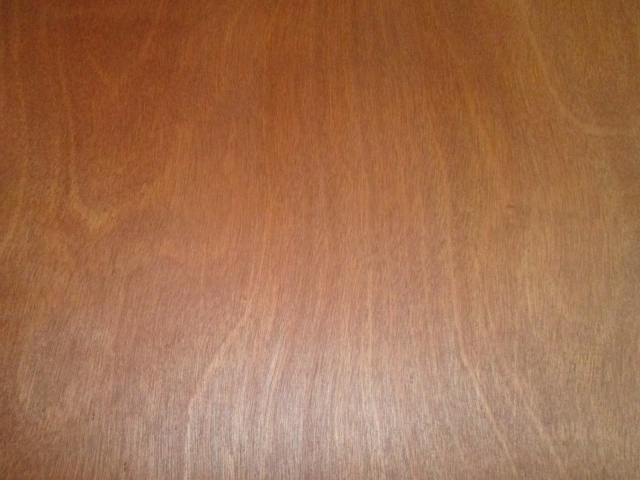
And removed the masking tape.
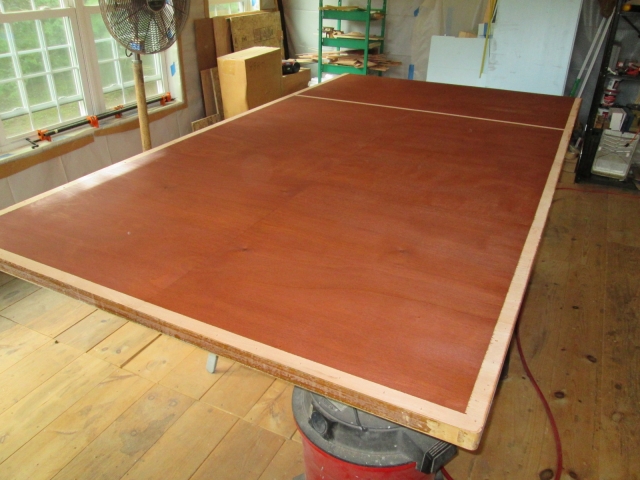
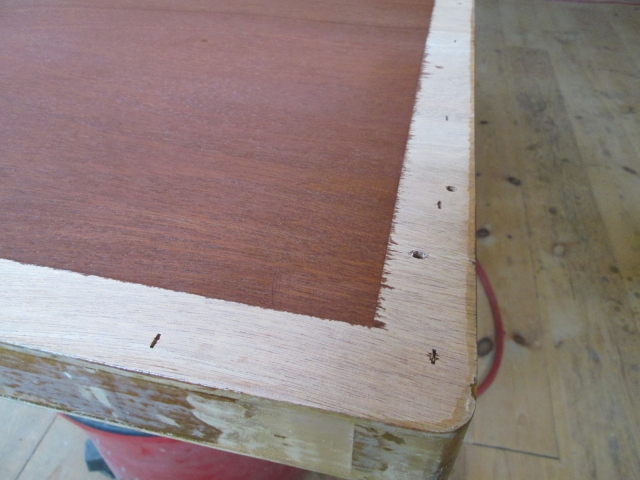
I wanted a hard aluminum edge on the rear corner of the galley floor to keep plastic totes or whatever from wearing away at the edge of the plywood top skin. However, I had not designed this in and had not allowed for the thickness of this in my seal arrangement.
I didn’t want it to sit proud of the top surface (at least not by much) because I didn’t want things to hang up on it when sliding out; and I had not allowed for any additional thickness between the rear of the floor and the hatch seal. It would have been nice to use a 2x2x1/8 thk aluminum angle shape, but the floor is only 1-7/8 thk (plus a skotch) and the 3/16 ply deck only overlaps the rear subframe 2x by 1-1/2 inch; wouldn’t want to weaken the skin joint too much by routing it away. Thought about using the 2x2x1/8 and ripping it to 1/2x1-7/8, but that seemed complicated having to cut 1/8 inch off the back of the floor and notch the 1/2 inch top leg in from under the walls. Karl seems to be wanting me to wrap this up, so all of his suggestions lately have been that which cut corners (“sanding? Heck just slap the stain on… it will be hidden under the mattress… hard edge? How many times do you plan on using this thing anyway? It will be fine, just poly it.”) I think it is his state of mind after dealing with the nut cases on the high end bronze railing and the subsequent add on work that they have given him. His customers have no sense of reality of what quality really is because they just throw money at things. So long as the spec sheet says they are getting top quality materials and the architect sells them a concept on a print, they don’t really know what quality is. Don’t get me wrong, Karl does first rate work, but he can get frustrated by idiots just the same as you and me.
So after sleeping on it and browsing my options while standing at the metal rack at Ho-de-po this morning (Sunday), I decided to let in a 3/4 x 3/4 x 1/8 aluminum angle. That way I could use the rabbeting router bit on the rear edge of the floor without having to clear off the whole thing, and I could cut the relief in the top surface w/o cutting away all of the join between the top skin and the rear subframe member.
Here is the angle section for the hard edge.
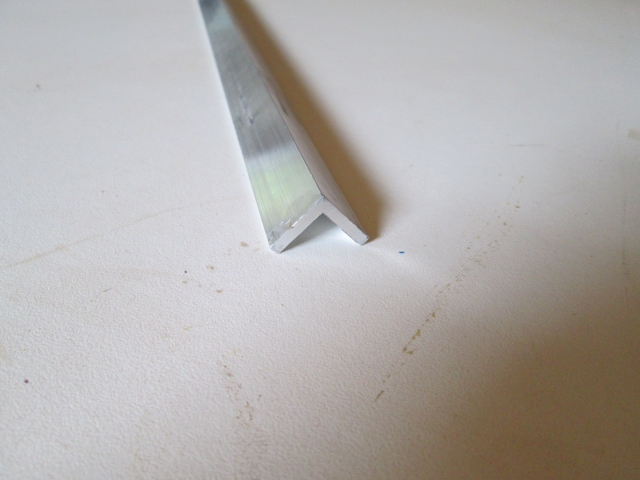
Here I have laid out the cut in pencil. The aluminum will extend under the walls by just a little, about 1/4 inch, will be flush to the rear of the floor, and just a tad above flush with the top surface of the floor.

Next I set the router up with the rabbeting bit. It is a 1-1/4 diameter cutter, 1/2 inch tall, and accepts bottom bearings of various diameters to set the amount of offset that the cutter will take. By using a 1 inch bearing along the rear of the floor I can chase a 1/8 inch deep cut however far down the rear edge of the floor I want merely by changing the depth of the router plunge setting.
In order to help support the router I clamped some 2x2’s onto the underside of the floor, used two shims equal the floor plys, and a 1x2 on edge to act as an outrigger supporting the overhanging portion of the router shoe.
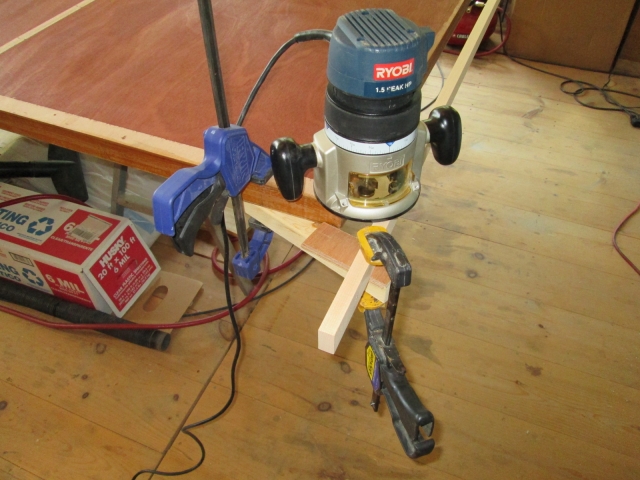
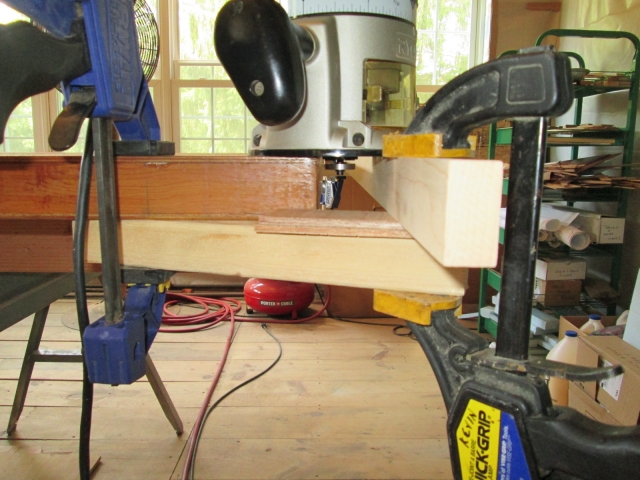
This made it ridiculously simple to run the router across the rear edge of the floor, taking an 1/8 of an inch per pass without having to worry about tipping the router. The stability also helped me concentrate on the start and end of the cut, minimizing the amount of hand chiseling that I would have to do to remove the cutter radius.
I made several passes until I was able to fine tune the final pass so that the top surface of the aluminum would be just a whisker above the finished floor. Here I have cut a small piece of the angle aluminum to use as a gauge to check fit. You can also see the score line that I made for the top cut (to follow) using the extruded aluminum straight edge.
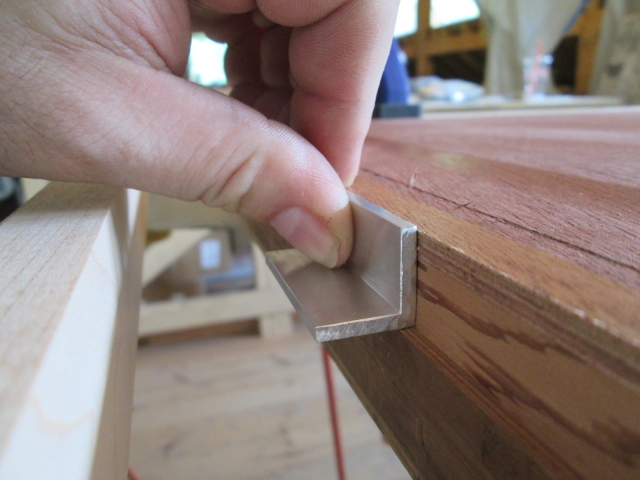
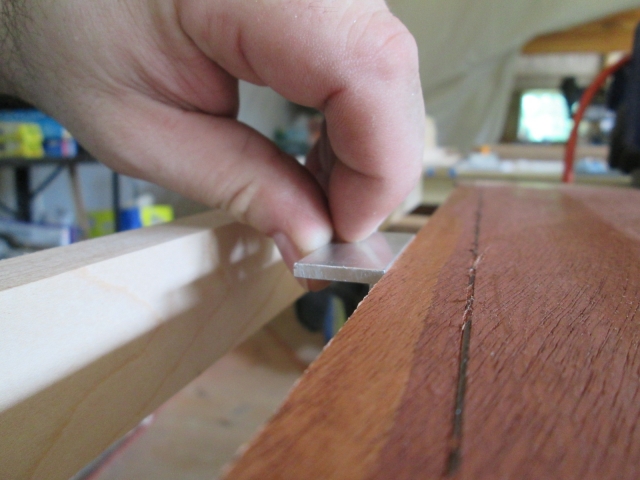
The lead in to the cut will have to be chiseled out by hand.
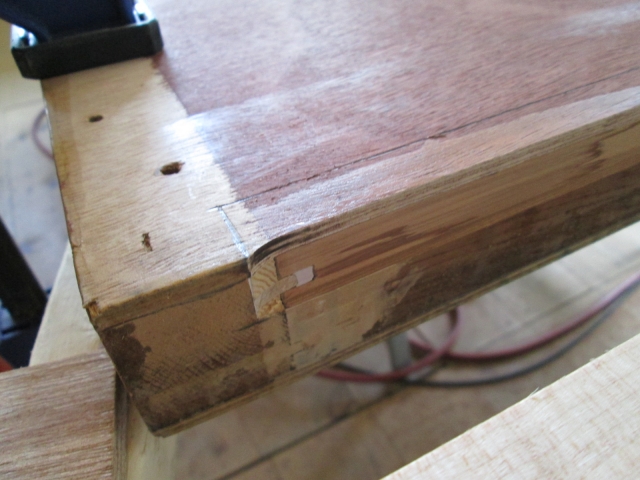
Next I moved the outrigger in a bit, set the straight edge to guide the top cut, and set the router up for the straight cutting bit. Here I have run the router into the top surface of the floor and cleared out a section to check my setup.
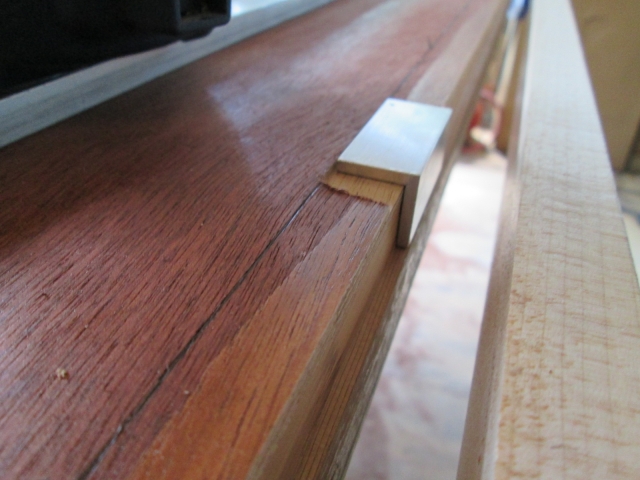
Looked pretty good so I went ahead and made the cut.
Fit nice and tight at the street side.
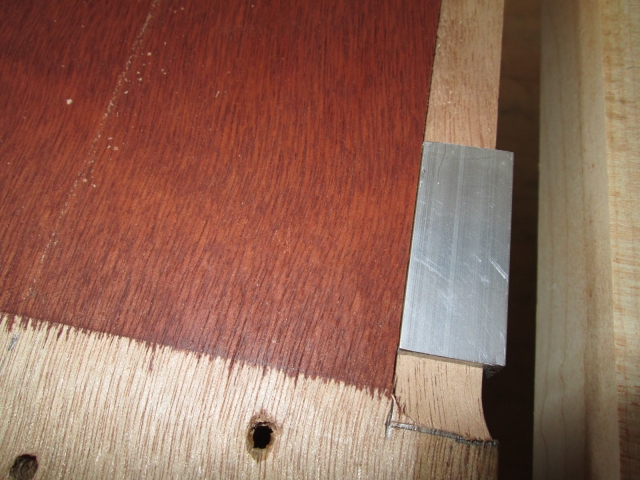
And nice and tight at the curb side.
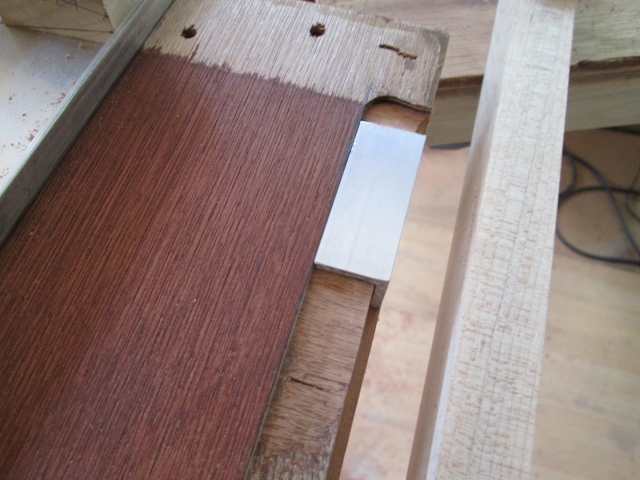
But in the middle there was a 1/16 plus overcut.
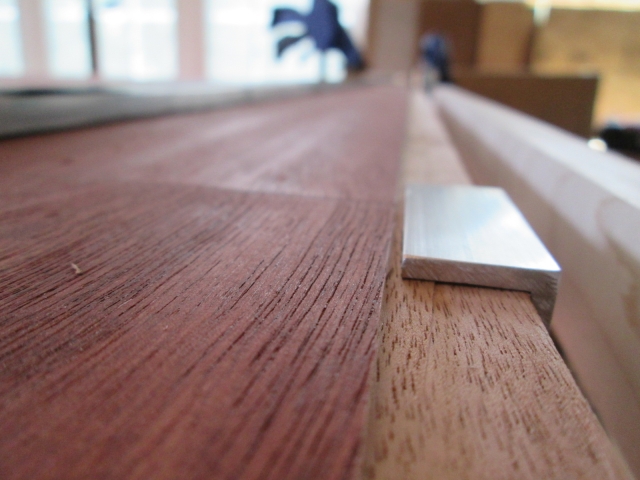
The straight edge guide must have bowed in the middle. Drat.
Not too bad, but not perfect. I can stain the cut edge and bed the trim in caulk. The trim will get counter sunk holes to accept flat head screws alternating in spacing along the top and rear edge. Might even have it powder coated, schmaybe.
Chiseled out the street side.
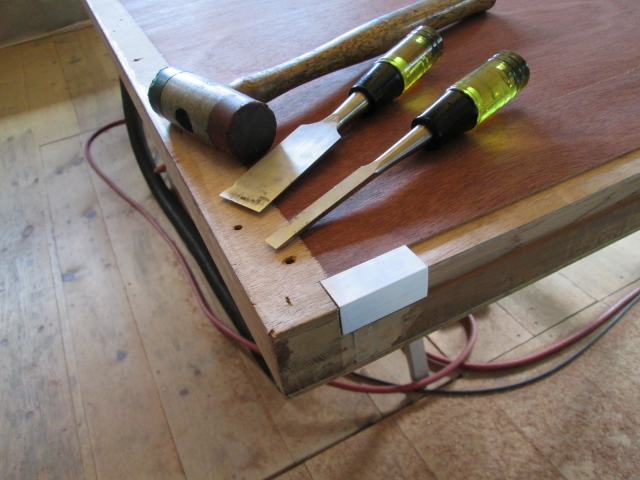
And the curb side.
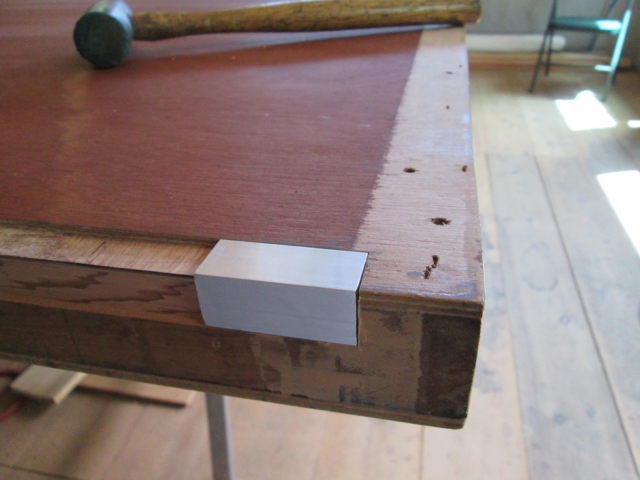
And cut the shape to fit.
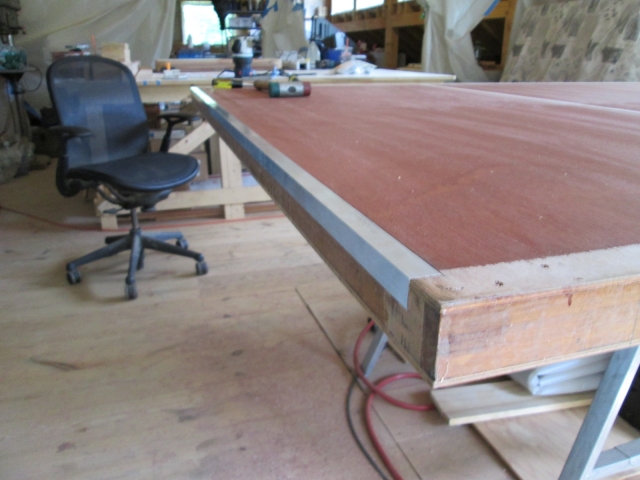
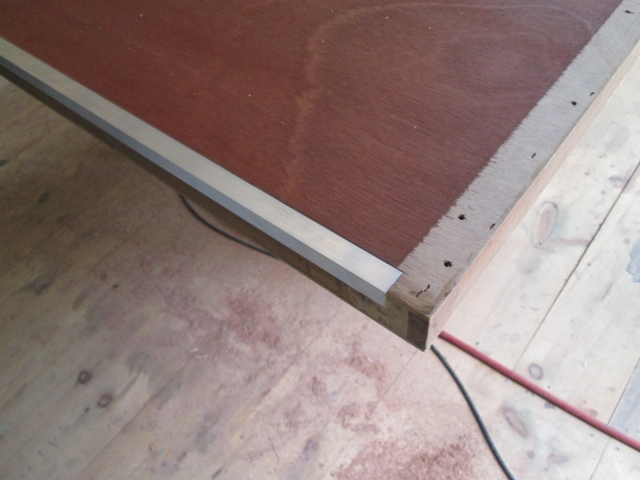
To help hide the little gap in the middle I masked off the fresh cut…
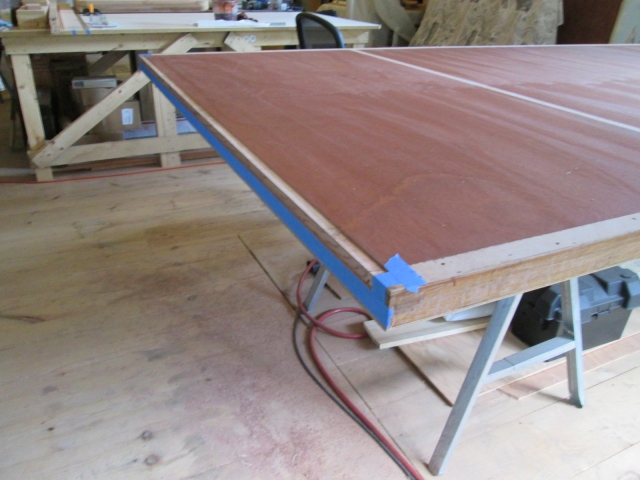
… and stained the exposed edges.
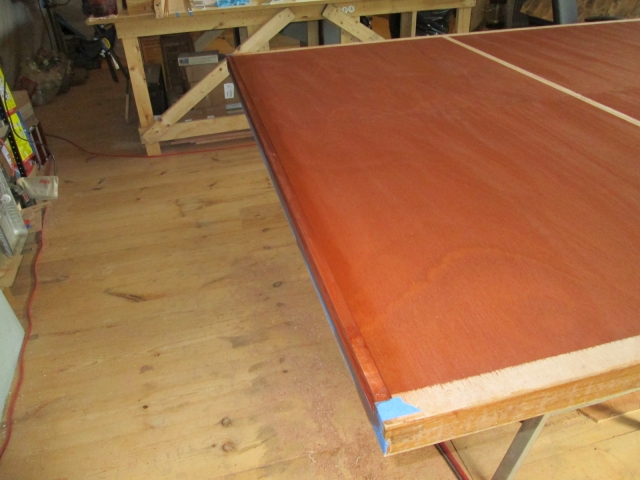
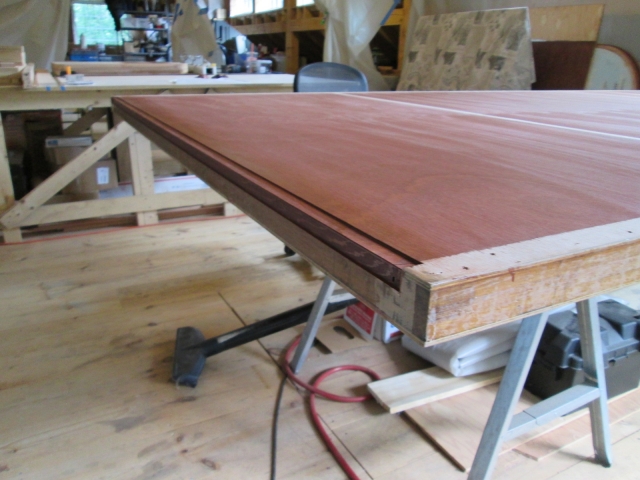
A couple more looks at the trim just dry fit.
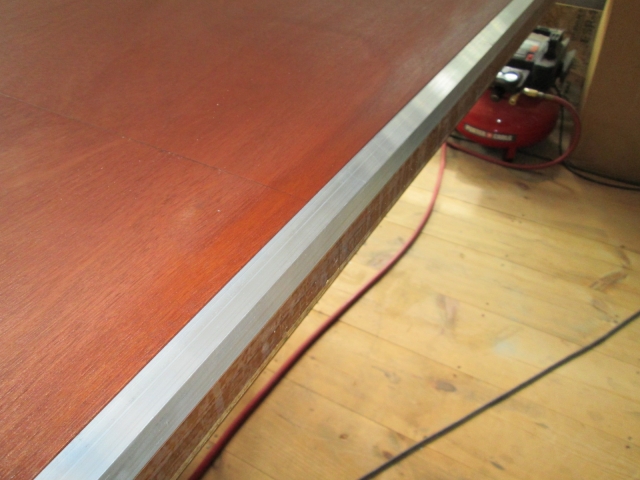

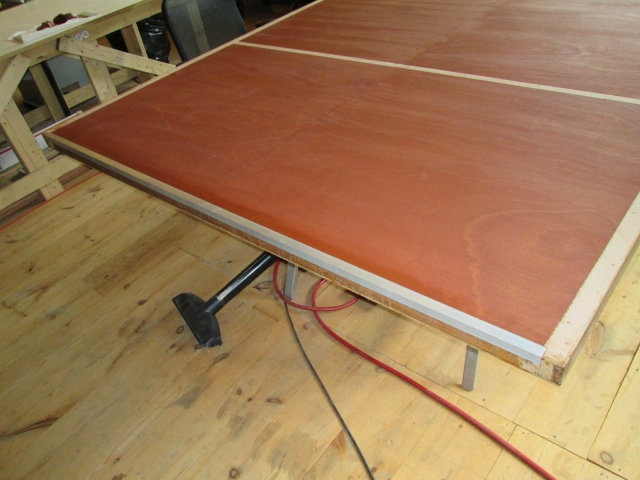
That was only about 3 hrs on Sunday, but the loft temp had got to 90 deg F and humidity was over 60/ct. I was drenched and fading fast so went for cold

and AC
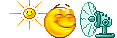
.